Approaches to Toyota Production System
The Toyota Production System (TPS) is a famous manufacturing method. Businesses worldwide have studied and copied it. TPS has changed how companies work on making things.
In this article, we’ll look at the different TPS approaches and how they have made it successful in manufacturing. Whether you own a business, manage one, or are just interested in manufacturing, knowing TPS principles can give you useful ideas for making production smoother.
Objectives of the Toyota Production System
The Toyota Production System focuses on continuous improvement. It does this by streamlining processes and eliminating waste. This is achieved through just-in-time production and problem-solving principles. For example, their supply chain reduces waiting times and overproduction.
Respect for humanity is central to the Toyota Production System. This involves valuing and taking care of employees. It also prioritizes safety, well-being, and professional development in the work environment. In practice, this means promoting open communication and empowering employees to contribute to process improvement.
The system also prioritizes the development and empowerment of personnel and partners. This is done by emphasizing training, skill-building, and autonomy. Toyota invests in the skills and expertise of its employees and builds strong relationships with suppliers and partners.
Historical Background of the Toyota Production System
The Toyota Production System started after World War 2. At that time, it was hard to find replacements for broken machinery. High labor costs and a small market made things even more challenging. TPS focused on reducing waste and improving efficiency, which was very important in this situation.
Eiji Toyoda and Taiichi Ohno, two important people at Toyota, made big contributions to TPS. They worked together to shape its main ideas and goals. They also focused on mass customization, also known as “lean production,” which ensured that every vehicle met high-quality standards and customer needs. They set up a process that pulled products through the pipeline continuously, avoiding waste from overproduction, waiting, and over processing.
Core Tenets of the Toyota Production System
Pursuit of Continuous Improvement (Kaizen)
Kaizen is a Japanese concept for continuous improvement. It’s closely tied to the Toyota Production System. The focus is on reducing waste, increasing efficiency, and optimizing processes. Small changes can lead to big improvements over time.
In the workplace, Kaizen encourages workers to suggest and make improvements. This boosts productivity and problem-solving skills. It’s a team effort to achieve the best results.
Kaizen in the TPS involves everyone at every level. It empowers people to refine and enhance operations. This ensures that everyone feels a sense of ownership and contributes to better systems and practices.
Upholding Respect for Humanity in the Workplace
A workplace can create a respectful environment by focusing on employees’ well-being. This includes open communication, feedback channels, and continuous improvement.
Providing training opportunities, recognizing individual contributions, and promoting a safe work environment are important. These strategies can prevent overburdening and make work more meaningful, following the Toyota Production System principles.
Moreover, these approaches can reduce waste, improve efficiency, and contribute to the organization’s success.
Creating Efficient Processes for Optimal Results
Organizations can achieve optimal results by focusing on principles such as just-in-time production, continuous improvement, and problem-solving. They should also emphasize respecting people and eliminating waste to minimize inconsistencies and overburdens.
One key strategy for ensuring efficiency is to implement concepts like Jidoka and Just-In-Time. These enable the efficient production of products at the pace of customer demand while meeting high-quality standards.
These principles can be adapted and applied to different industries to achieve maximum efficiency. This involves identifying and eliminating waste, conserving resources, and fostering a culture of continuous improvement and problem-solving.
By doing so, organizations can create meaningful work, ease burdens for workers, and effectively utilize resources to achieve optimal results.
Empowering and Developing Personnel and Partners
Toyota empowers its staff and partners to continuously improve and work efficiently. They prioritize the well-being of their workforce and give them the skills and tools they need. This helps them meet high-quality standards and customer requirements.
Toyota uses strategies like Jidoka and Just-In-Time to create an environment where workers can be highly efficient. They also focus on eliminating waste and overburden to make work easier for their employees. This approach supports the development of their staff and partners within the Toyota Production System framework, emphasizing respect for humanity in the workplace.
Institutional Learning through Problem-Solving
Problem-solving is an important part of the Toyota Production System. It helps employees learn and develop critical thinking skills by addressing and solving challenges at their core. This continuous improvement approach allows teams to find and fix inefficiencies in real-time, improving processes and productivity. By involving employees and partners in decision-making, it enhances their skills and fosters a culture of continuous learning and growth.
This not only boosts efficiency and performance but also creates a collaborative problem-solving mindset, contributing to overall success.
Essential Elements of Workplace Management
Workplace management in a successful company involves eliminating waste, inconsistency, and overburden in manufacturing and logistics. It also focuses on just-in-time production, continuous improvement, and problem-solving.
The Toyota Production System emphasizes respect for humanity in the workplace. It aims to make work easier and less burdensome for workers and create meaningful work.
This management system promotes continuous improvement and efficient processes by applying the concepts of Jidoka and Just-In-Time. This allows for efficient production at the pace of customer demand, ensuring high-quality standards and meeting individual customer requirements.
Key Terminology in the Toyota Production System
The Toyota Production System has four core principles:
- Just-in-time production.
- Continuous improvement.
- Respect for people.
- Problem-solving
These principles help in achieving operational excellence by identifying and eliminating waste, inconsistency, and overburden in manufacturing and logistics.
Organizations can use these principles to improve efficiency, reduce costs, and deliver high-quality products to meet customer demand.
TPS also promotes respect for humanity in the workplace through the concept of Jidoka. This empowers workers to stop the production line in case of quality issues, creating a sense of responsibility and engagement among employees. This fosters higher employee satisfaction and productivity, as it allows for meaningful work and opportunities for skill development.
Key terminology in the Toyota Production System includes Jidoka, Just-In-Time, and waste elimination. These terms are vital in creating efficient processes. For example, just-in-time production minimizes inventory costs and reduces the risk of overproduction by manufacturing products based on customer demand. Waste elimination focuses on identifying and eliminating non-value-added activities, leading to resource optimization and enhanced productivity.
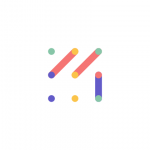
Vizologi is a revolutionary AI-generated business strategy tool that offers its users access to advanced features to create and refine start-up ideas quickly.
It generates limitless business ideas, gains insights on markets and competitors, and automates business plan creation.