Benefits of the Toyota Production System
The Toyota Production System (TPS) changed how manufacturing companies work. It made them more efficient, reduced waste, and improved quality. Developed by Toyota Motor Corporation, TPS focuses on continuous improvement and respect for people. This creates a culture of employee empowerment and innovation. TPS has set a global example for businesses, showing the benefits of lean manufacturing and just-in-time production.
Knowing the advantages of TPS can help organizations improve their operations and provide more value to customers.
Core Tenets of the Toyota Production System
Lean Manufacturing Principles
Lean Manufacturing Principles are a core part of the Toyota Production System. They focus on eliminating waste, improving efficiency, and making continuous progress.
Kiichiro Toyoda developed the Just-in-Time concept, which aims to reduce excess inventory and streamline production processes to minimize waste.
Additionally, the Jidoka principle, initially introduced by Sakichi Toyoda for automated looms, focuses on building machines capable of making judgments to eliminate defective products and wasteful practices. This enhances efficiency by eliminating the need for human intervention to identify and address issues, allowing for seamless production processes.
Sustaining Kaizen initiatives within the Toyota Production System involves consistently applying the “Toyota Way,” a philosophy that encourages all employees to improve continuously and solve problems.
Toyota has achieved sustained success and competitiveness in the automotive industry by implementing and evolving Lean Manufacturing Principles.
Just-In-Time Production Methodology
The Just-In-Time Production Methodology focuses on eliminating waste and achieving efficiency. It’s based on the Toyota Production System and aims to reduce excess inventory, processing steps, and defective products. The goal is to create ideal conditions for production, where machines, facilities, and people work together to add value without generating waste.
This approach helps reduce waste, increase efficiency, and rapidly improve productivity and work efficiency. It achieves this by eliminating waste between operations, lines, and processes.
Implementing Just-In-Time in manufacturing has challenges. It requires well-coordinated operations and can be disrupted by unforeseen events like supply chain disruptions. It also demands discipline and commitment from all employees for successful implementation and sustenance.
The Role of Kaizen in Continuous Improvement
Implementing Kaizen in Daily Operations
Kaizen principles can be easily added to everyday operational processes. This can be done by creating a culture of continuous improvement, involving employees, and promoting open communication. Regular training on Kaizen principles helps employees understand and embrace the concept of continuous improvement.
Monitoring and evaluating processes, making necessary adjustments, and recognizing and rewarding employees for their contributions are important for sustaining and improving Kaizen initiatives in daily operations. Employees are vital in implementing and sustaining Kaizen. They can drive continuous improvement by participating in decision-making processes, improving projects, and accessing necessary resources and support. The Toyota Production System is a practical example of how Kaizen can be implemented and sustained in daily operations, benefiting not only Toyota but also being adopted globally by other companies.
Strategies for Sustaining Kaizen Initiatives
Maintaining and sustaining Kaizen initiatives in an organization involves several effective strategies:
- Create a culture of continuous learning and improvement.
- Encourage open communication among team members.
- Provide regular training and resources for employees to develop their problem-solving skills.
Leaders can ensure that continuous improvement efforts remain a priority by:
- Setting clear expectations.
- Aligning improvement goals with the organization’s overall objectives.
- Recognizing and rewarding employees for their contributions to the Kaizen process.
Successful examples of sustaining Kaizen initiatives can be seen in the manufacturing, healthcare, and technology industries. Companies in these sectors have used Kaizen principles to streamline production, optimize patient care, and enhance product development, leading to increased efficiency, higher quality, and greater customer satisfaction.
Enhancing Efficiency With the Jidoka Principle
Automating Quality Control Checks
Automating quality control checks in a manufacturing or production environment offers several benefits. By implementing automation, companies can improve the accuracy and speed of quality control processes, reducing errors and defects.
Additionally, automation can enhance the efficiency of production operations by streamlining the inspection process and eliminating manual tasks, ultimately resulting in cost savings and increased productivity. However, there may be challenges in implementing automated quality control checks, such as the initial cost of acquiring and deploying the necessary technology and potential employee resistance. These challenges can be addressed through thorough cost-benefit analysis to demonstrate automation’s long-term value and provide adequate training and support to ensure a smooth transition.
Empowering Employees to Address Production Issues
Strategies to empower employees to take ownership and address production issues in the organization include:
- Providing regular training opportunities on problem-solving and continuous improvement.
- Establishing a system of rewards and recognition for employees who identify and address production issues.
- Creating a culture of open communication and transparency where employees are encouraged to speak up about production challenges.
Leadership can create a culture of continuous improvement and problem-solving among employees by:
- Leading by example.
- Demonstrating problem-solving skills.
- Encouraging employees to share their ideas and suggestions for improvement.
- Providing regular feedback and support to employees.
- Creating a safe environment for employees to experiment and make mistakes without fear of retribution.
Tools and resources that can be provided to employees to identify and address production issues in real time include:
- Access to real-time production data and analytics.
- The use of visual management tools such as kanban boards.
- Implementation of digital quality control systems that enable employees to track and monitor production processes in real time.
Impacts of the Toyota Production System on the Industry
Industry Adoption and Adaptation of TPS Principles
Industries have adopted and adapted TPS principles to improve their production processes, focusing on eliminating waste and promoting efficiency. Strategies such as implementing the Just-in-Time concept and making continuous improvements have been effective in integrating TPS principles into different industry settings.
However, industries have also faced challenges in implementing TPS principles, such as excess inventory, extraneous processing steps, and defective products, among other instances, which intertwine to create more waste. To address these challenges, companies have worked towards daily improvements and better thinking to achieve the ideal conditions for making things, where machines, facilities, and people work together to add value without generating any waste. The Toyota spirit of monozukuri, also known as the “Toyota Way,” has been adopted by companies in Japan within the automotive industry and in production activities worldwide.
The TPS has evolved into a world-renowned production system, and even today, all Toyota production divisions are improving TPS day and night to ensure its continued evolution.
Comparative Analysis of TPS and Six Sigma Approaches
Integrating Six Sigma Methods with TPS for Maximum Efficiency
Six Sigma methods and the Toyota Production System can work together to improve manufacturing efficiency. TPS focuses on eliminating waste, while Six Sigma reduces defects and variations. By combining them, companies can continuously improve and reduce waste, leading to increased efficiency. Key strategies for aligning Six Sigma with TPS include continuous quality improvement, standardizing work processes, and reducing variability in production.
TPS aims to eliminate waste, while Six Sigma focuses on statistical approaches and defect reduction. Both emphasize process improvement and standardization but use different methodologies and tools. Integrating them helps optimize manufacturing and improve efficiency.
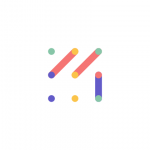
Vizologi is a revolutionary AI-generated business strategy tool that offers its users access to advanced features to create and refine start-up ideas quickly.
It generates limitless business ideas, gains insights on markets and competitors, and automates business plan creation.