Better Every Day: The Kaizen Way
Are you looking to make positive changes in your life? Do big, sweeping transformations feel overwhelming? Look no further than the kaizen way. This Japanese philosophy focuses on making small, continuous improvements every day. These lead to significant results over time. With a focus on consistent progress and a commitment to ongoing growth, the kaizen way offers a practical and sustainable approach to self-improvement.
Learn how this method can help you achieve your goals and cultivate a mindset of continuous improvement.
Unveiling Kaizen: A Path to Continuous Improvement
Kaizen philosophy focuses on continuous improvement through small, gradual changes. It involves all employees in identifying improvement opportunities to impact organizational transformation.
There are diverse Kaizen events like Point, Line, Plane, and Cube Kaizen, which provide a structured framework for targeted improvements. This ultimately contributes to the efficiency and quality of operations.
The pros of the Kaizen methodology include productivity improvement, standardized processes, and waste reduction. However, the cons may involve resistance to change and the need for significant culture shift.
Real-world examples demonstrate the effectiveness of Kaizen through success stories of companies achieving significant improvements in productivity and product quality.
The Tenets of Kaizen Philosophy
Principle 1: …,
The first principle of the Kaizen philosophy emphasizes the need for improvement. It recognizes that everything can be improved and simplified. This principle encourages individuals and organizations to adopt a mindset of ongoing, gradual improvement. Principle 1 creates an environment that fosters innovation, efficiency, and productivity.
For example, within a manufacturing setting, it might prompt employees to identify and address inefficiencies in a production line. This leads to streamlined processes and reduced waste. In an office environment, the principle could encourage workers to find new and improved methods for completing tasks, ultimately enhancing productivity and reducing errors.
Principle 2: …,
Kaizen Principle 2 emphasizes the focus on processes rather than individual tasks. This contributes to continuous improvement by evaluating and adjusting processes. Instead of just completing tasks, Kaizen encourages developing efficient processes for better performance and quality. Optimizing processes can lead to significant improvements in productivity and operational efficiency.
Principle 2 includes creating a standardized method, using the latest technology, maintaining a clean workspace, following work standards, and written procedures. Techniques like Standardized Work and Visual Factory exemplify this principle in Kaizen philosophy.
Implementing this principle involves conducting regular process review sessions, active employee participation, and periodic assessment of the workflow cycle. Effective implementation can drive visible improvements in output quality, productivity, customer satisfaction, and overall business performance.
Principle 3: …,
Principle 3 is really important in the Kaizen philosophy. It focuses on respecting the current process, practices, and individuals in the organization.
By recognizing everyone’s efforts, it creates a culture of constant improvement, learning, and growth. This is achieved by promoting ongoing education, training, and coaching, which leads to better problem-solving skills and increased employee engagement.
For example, when employees’ existing knowledge and deep understanding of a process are acknowledged, it not only appreciates their efforts but also encourages them to be open to new ways of doing tasks and finding opportunities for improvement.
Moreover, this level of respect creates a more collaborative and empowering work environment. It allows for successful implementation of the Kaizen philosophy and overall business excellence.
Principle 4: …,
Principle 4 of Kaizen is about standardization. This principle helps with continuous improvement by emphasizing the importance of having standard processes and procedures within an organization. Implementing Principle 4 ensures that operations are consistent, reliable, and efficient, which forms the basis for ongoing improvement. Standard procedures make it easier for businesses to identify deviations, waste, and areas for improvement.
Practical applications of this principle include creating detailed work instructions, optimizing workflow processes, and establishing standardized training programs. These applications aim to streamline operations, reduce errors, and identify opportunities for incremental improvements.
For example, a manufacturing company may use standardization to define best practices for equipment maintenance, leading to increased productivity and reduced downtime. Similarly, in a service-oriented business, standardizing customer service processes can lead to improved customer satisfaction and more efficient problem-solving.
Principle 5: …,
Principle 5 in the Kaizen philosophy is about respecting people and creating a culture of trust and cooperation.
This principle focuses on valuing team members’ ideas, promoting open communication, and fostering a supportive work environment.
Integrating Principle 5 into Kaizen methodology can create a positive atmosphere. This motivates employees to actively participate in continuous improvement.
When employees feel respected and valued, they are more likely to contribute innovative suggestions and take ownership of their work. This drives sustainable improvements.
For example, in manufacturing plants, respecting employees’ expertise has led to streamlined production processes and reduced waste.
In customer service industries, implementing Principle 5 has improved problem-solving and increased customer satisfaction through better communication.
These examples show how Principle 5 has been successfully applied in real-world Kaizen initiatives. They demonstrate its positive impact on achieving continuous improvement goals.
Principle 6: …,
Principle 6 of the Kaizen philosophy is about standardizing and streamlining processes. It’s all about keeping up the improvements made through previous principles. This principle is a big part of the idea of always getting better in Kaizen. It makes sure that improvements stick around and get even better.
For example, in a factory, Principle 6 means making and following standard work instructions for a job. This keeps the improved way of doing things going, so productivity and quality stay high. In a service industry, Principle 6 could mean making checklists or standard ways to do tasks. This keeps the improvements in customer service or how things run sticking around. When processes are standardized, organizations can hold onto and build on the improvements they’ve made using Kaizen.
Principle 7: …,
Principle 7 of the Kaizen philosophy focuses on communication for continuous improvement. It encourages open and honest dialogue among everyone in the organization. This includes employees, managers, and executives. By doing this, the principle aims to identify areas for improvement and promote innovative solutions.
Practical examples of implementing Principle 7 include team meetings, suggestion boxes, and regular performance reviews. Effective communication allows for insights, suggestions, and feedback from all levels of the organization.
However, there may be challenges in implementing Principle 7. These could include resistance to change, lack of trust in the organization, and poor communication skills among employees and management. Overcoming these challenges requires commitment from leadership to create a culture that values open communication and the exchange of ideas.
Principle 8: …,
Principle 8 of the Kaizen philosophy focuses on understanding and retaining knowledge. Having access to a wealth of knowledge is important for continuous improvement. Kaizen encourages employees to take ownership and maintain knowledge to benefit the organization. This principle contributes significantly to continuous improvement by promoting a culture of learning and information sharing.
When employees are knowledgeable and continuously informed, they can make better decisions, identify improvement opportunities, and implement changes effectively.
Practical applications of Principle 8 in real-world Kaizen initiatives include implementing knowledge management systems, providing training and development opportunities, and encouraging mentorship programs. These initiatives ensure that employees have the tools and resources needed to gain and retain knowledge, supporting Kaizen’s foundation of continuous improvement.
Principle 9: …,
Principle 9 in Kaizen says to make decisions slowly by consensus, consider all options thoroughly, and then implement the decision quickly. This principle is important because it ensures that decisions are evaluated and supported by all team members before implementation, leading to effective changes.
It contributes to continuous improvement in the Kaizen methodology by fostering a decision-making process that involves all employees, leading to increased commitment and a sense of ownership.
By empowering employees to participate in the decision-making process, Principle 9 creates a culture of collaboration and accountability, ultimately driving continuous improvement.
Organizations can implement Principle 9 effectively in their Kaizen initiatives by creating an environment that encourages open discussions and feedback. This inclusive approach to decision-making encourages continuous improvement and ensures that changes are implemented effectively.
Principle 10: …,
Principle 10 in the Kaizen philosophy is about quality control. It focuses on maintaining high quality in processes and products for customer satisfaction and long-term success. This principle supports continuous improvement by promoting excellence and the pursuit of perfection. By following quality control measures, companies can find and fix defects, errors, or inefficiencies in their operations, leading to better products, services, and customer experiences.
Real-world examples of Principle 10 in Kaizen include using quality control checks in manufacturing to catch and fix defects before products reach the market. Service industries also apply this principle by setting high quality standards to measure and improve customer service for long-term growth and loyalty. In the end, Principle 10 highlights the importance of quality as a main driver of continuous improvement and excellence in the Kaizen approach.
Implementing the Kaizen Strategy
Setting Goals with Kaizen
Setting goals with Kaizen is about making specific targets for continuous improvement. These targets should line up with the principle of small, ongoing positive changes.
For example, a company might aim to reduce production line defects by 10% within six months or improve customer satisfaction ratings by one point quarterly. These clear targets promote incremental improvement.
To integrate continuous improvement into the goal-setting process with Kaizen, companies can create a culture of constant evaluation and adjustment. This could include quarterly performance reviews to assess progress toward set goals and encourage teams to engage in continuous reflection and feedback sessions. This ensures that employees have the chance to make suggestions for incremental improvement.
To make sure that Kaizen goals are sustainable and achievable, companies can use strategies like regularly scheduled performance reviews, employee feedback systems, and process evaluation. This helps to create a culture of accountability and continuous improvement, and gives employees opportunities to contribute to the goal-setting process.
Additionally, organizations can include Kaizen events in their yearly plans to promote short-term, targeted improvement initiatives.
Sustaining Kaizen Initiatives
To make sure that Kaizen principles are integrated into daily operations and sustained, organizations can:
- Implement regular training and workshops to keep employees engaged in the Kaizen process.
- Create clear communication channels for feedback and suggestions from all levels of the organization.
- Recognize and celebrate small improvements and successes to maintain motivation.
Challenges in maintaining Kaizen momentum include resistance to change, complacency, and sustaining employee engagement. To address these, organizations can:
- Foster a culture of open-mindedness and flexibility to encourage change and continuous improvement.
- Provide incentives for active participation in Kaizen initiatives and establish a monitoring system for accountability.
To cultivate a culture of continuous improvement and a Kaizen mindset, organizations should:
- Promote collaboration, teamwork, and innovation.
- Create an environment that values learning and growth.
- Empower employees to take initiative and provide necessary resources and support for improvement.
- Establish a culture of transparency and trust to foster ownership and commitment to Kaizen.
The Kaizen Process Cycle: PDCA
The Kaizen Process Cycle has key stages outlined in the PDCA model: Plan, Do, Check, and Act.
In the “Plan” phase, organizations set objectives and processes for improvement. In the “Do” phase, they implement planned processes and test solutions on a small scale. The “Check” phase involves monitoring and evaluating results to ensure they align with the set objectives. Finally, in the “Act” phase, companies summarize experiences and identify further improvement opportunities based on data and results from the “Check” phase.
The PDCA model supports the continuous improvement philosophy of Kaizen by providing a structured approach to resolve issues. It encourages employees to engage in problem-solving and innovation, fostering a culture of continuous improvement.
Organizations can implement the PDCA model into everyday processes to foster a mindset of continuous improvement. By regularly applying the PDCA cycle, companies can address inefficiencies, streamline processes, and enhance productivity. This approach encourages employees to assess their work, identify areas for improvement, and participate in positive changes.
Diverse Kaizen Events and Their Impact
Point Kaizen: Immediate Action
Point Kaizen is a quick way to make big improvements. It focuses on making small changes that add up over time.
Unlike Line Kaizen and Plane Kaizen, Point Kaizen zooms in on one specific part of a process. This could be a bottleneck or an area that’s not working well.
To use Point Kaizen, start by identifying the specific problem. Then figure out what’s causing it. After that, test small solutions and see what works best. Finally, put those solutions in place to make things better.
For example, a manufacturing company might use Point Kaizen to fix a broken machine that’s slowing down production. They’d look at the machine closely, pinpoint the problem, and make small tweaks to improve efficiency right away.
Line Kaizen: Process Alignment
Line Kaizen is an approach that helps align processes within an organization. It focuses on improvement on the shop floor or specific work areas. By encouraging employee participation and standardizing processes, Line Kaizen can lead to the removal of inefficiencies and waste, ultimately optimizing workflow.
This can be achieved through methods such as value stream mapping, 5S organization, visual management, and other lean techniques. Line Kaizen facilitates continuous improvement in an organization by actively involving frontline workers in identifying and implementing incremental improvements in their work areas.
This results in increased efficiency, reduced lead times, and improved product quality. Through aligning processes and fostering continuous improvement, organizations can streamline their operations, optimize resource utilization, and achieve sustainable growth.
Plane Kaizen: Cross-departmental Improvements
The Plane Kaizen approach involves making improvements across different departments by creating a unified vision and shared goals. Teamwork and collective effort are emphasized to foster collaboration and communication. Regular cross-functional team meetings are established to discuss project updates, identify challenges, and share best practices. This open dialogue helps break down silos and work towards a common objective.
Organizations can measure the impact of these improvements by setting clear KPIs (Key Performance Indicators) that are shared and monitored across departments. This ensures that outcomes align with the organization’s overall objectives and allows for transparent reporting and analysis of progress.
In addition, tools like process mapping and value stream analysis can provide insights into the flow of work and identify areas for improvement, helping to gauge the effectiveness of cross-departmental initiatives.
Cube Kaizen: Organizational Transformation
Cube Kaizen focuses on continuous improvement in all areas, involving all employees to eliminate waste and redundancies. It encourages standardized programs and processes for ongoing positive changes, ensuring continual improvement in the workplace.
The key principles are based on systematic and standard processes, facilitating organizational improvement through various approaches such as Point Kaizen, System Kaizen, and Line Kaizen. These approaches emphasize productivity improvement and a humanized approach to workers.
Challenges of implementing Cube Kaizen include the need for a cultural shift and overcoming resistance to change. However, the benefits include improved efficiency, reduced waste, increased employee engagement, and enhanced customer satisfaction through continuous improvement.
The 5S System in Kaizen
Sort
The “Sort” phase in the 5S System of Kaizen is important for improving workplace organization and efficiency. It involves eliminating unnecessary items and materials from the work area to create a conducive environment for continuous improvement.
This phase helps workers create a productive and organized workspace, leading to streamlined processes and reduced waste, contributing to overall continuous improvement. It encourages employees to classify and discard unnecessary materials, tools, and equipment, resulting in easier access to essential items and decluttered working areas.
Effective execution involves the active involvement of all employees in the sorting process to assess the necessity of each item. Visual aids such as color-coding and signage can support the implementation of the “Sort” phase, and regular audits and reviews of the sorted work areas are crucial for maintaining order and maximizing the benefits of this phase in the context of the Kaizen methodology.
Set in Order
The “Set in Order” component of the 5S approach is important in implementing the Kaizen strategy. It helps create an organized, efficient workplace.
This involves arranging and identifying necessary items for regular work, reducing time wasted in searching for tools and supplies. “Set in Order” includes principles like assigning specific locations and markings for items, tools, and equipment, and standardizing procedures for employee compliance.
In Line Kaizen events, “Set in Order” helps achieve process alignment, streamline workflows, and reduce errors. This well-organized environment facilitates process standardization and a systematic approach to production activities.
This aligns with the core principles of Kaizen, emphasizing continuous improvement at all organizational levels for operational excellence.
Shine
Shine is a concept in the Kaizen philosophy. It focuses on cleanliness and organization in the workplace. Its goal is to maintain work areas at the highest level of cleanliness to ensure standard operations and eliminate defects.
Shine supports Kaizen’s principle of continuous improvement. It helps identify and address ongoing positive changes. By integrating Shine into their strategy, organizations can create an environment that promotes visual control and cleanliness. This makes it easier to spot abnormalities and opportunities for improvement.
Shine also contributes to creating a disciplined and standardized work culture, aligning with Kaizen’s objective of eliminating waste and redundancies. To effectively incorporate Shine, organizations can establish regular cleaning schedules, implement 5S practices, and provide training to employees on standard operating procedures and workplace organization techniques.
These approaches help maintain a clean, efficient, and safe work environment, which is crucial for the success of Kaizen principles.
Pros and Cons of the Kaizen Methodology
Implementing the Kaizen methodology has many advantages. It fosters a culture of continuous improvement, encouraging employees to streamline processes, eliminate waste, and increase productivity. This leads to a more efficient operation.
Kaizen also humanizes the workplace, improving employee satisfaction, engagement, and empowerment. It promotes standardized approaches, reducing errors and creating a safer working environment.
However, there are potential drawbacks to using the Kaizen methodology. It can be time-consuming and requires commitment from all levels of the organization. There may be resistance to change from employees accustomed to existing processes, and it may not be suitable for all business models.
Finally, Kaizen requires available leadership and management support to be most effective.
Kaizen in Action: Real-world Examples
Kaizen has been used in many industries and processes. In manufacturing, it has helped with production and waste reduction, saving money and increasing productivity.
But some organizations have had trouble with creating the right culture and mindset for Kaizen. Some people don’t like change and don’t want to keep improving.
To see how well Kaizen is working, companies use key performance indicators (KPIs) to track improvements in productivity, quality, and efficiency. They also look at employee feedback and engagement.
Despite the challenges, real-world examples show that Kaizen can help with continuous improvement and long-lasting growth.
The Historical Journey of Kaizen
The historical journey of Kaizen has key milestones. These have shaped the philosophy of continuous improvement. Kaizen began in Japanese quality circles. After World War II, it was further developed and spread in the USA under the Training Within Industry program. These events have influenced how Kaizen has evolved and been used in different industries and organizations. The historical context of Kaizen has been important in shaping its principles and strategies.
It emphasizes the significanceof small, ongoing positive changes for big improvements. Kaizen aims to get rid of waste and redundancies through standardized programs and processes. This aligns with its core principles. Kaizen also emphasizes involving all employees in a business, making the workplace more humanized. These historical influences continue to impact how Kaizen is practiced in different sectors. They have contributed to its significance as an approach to continuous improvement.
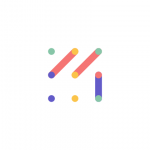
Vizologi is a revolutionary AI-generated business strategy tool that offers its users access to advanced features to create and refine start-up ideas quickly.
It generates limitless business ideas, gains insights on markets and competitors, and automates business plan creation.