The Big 4 Validation Types You Should Know
Validation ensures data and information accuracy, reliability, and worthiness. Understanding different validation types is crucial in today’s data-driven world. Whether in software development, data analysis, or quality assurance, knowing the big 4 validation types can significantly impact project success. Each type, from input validation to process validation, plays a critical role in maintaining data integrity and ensuring sound decision-making.
What Does It Mean to Make Sure Things Work Right?
There are 4 main types of validation to know when making sure things work right.
These include:
- Prospective validation
- Concurrent validation
- Retrospective validation
- Periodic revalidation
When manufacturers need to check that making stuff works right, they divide the production process into separate steps and analyze critical points in the manufacturing process, such as mixing times or temperature.
They also closely and intensively monitor all the manufacturing steps and critical points in at least the first three production-scale batches.
Then they assess the consistency of a process through trend analysis on test results and a close examination of all recorded process deviations and their relevant investigation reports.
Checking things can help in neat ways, enabling companies to catch errors and issues early in the process so they can be corrected before the final product is produced.
This helps ensure quality, consistency, and compliance with regulatory requirements in drug product development and manufacturing.
The Big 4 Types of Checks to Know
Getting Ready Before: Looking Forward Check
The “Getting Ready Before: Looking Forward Check” process has 4 key steps: prospective, concurrent, retrospective, and revalidation.
Prospective validation involves analyzing critical points when introducing new products and manufacturing processes. Concurrent validation requires intense monitoring of all manufacturing steps in the early production batches. Retrospective validation analyzes past production batches to assess process consistency for stable products. Revalidation checks if systems still operate as initially validated and if unintended changes have occurred.
To ensure tools and machines are in good condition, individuals can conduct thorough equipment and instrument qualification and validation. When designing the process, it’s important to ensure proper documentation practices, monitor process deviations, and conduct trend analyses on test results.
Looking Back: What Already Happened Check
- The previous work aimed to fully understand the process and monitor all manufacturing steps and critical points in the first three production-scale batches during normal production.
- Close and intensified monitoring of manufacturing steps and critical points, trend analysis on test results, and examination of all recorded process deviations were the main actions taken during the previous work.
- The outcomes included obtaining data-based computer systems or manual methods for retrospective validation and ensuring periodic revalidation to check for unintended changes affecting the process, system, or equipment.
Doing Checks While You Work
Effective checks when working should be done at different stages of validation to ensure everything functions correctly. The stages include prospective validation, retrospective validation, concurrent validation, and revalidation.
Prospective validation happens during the development stage. It involves dividing the production process into separate steps and analyzing potentially critical points in the manufacturing process.
Concurrent validation requires a full understanding of the process based on prospective work. It involves close and intensive monitoring of all the manufacturing steps and critical points during normal production.
Retrospective validation analyses accumulated results from past production batches manufactured under identical conditions to assess the consistency of a process.
Periodic revalidation offers the opportunity to check that the systems are still operating as originally validated and that no unintended changes have affected the process.
Continuously checking and ensuring that tools, machines, and programs are in good working condition is important to maintain the quality and safety of the products being developed and manufactured.
Checking Again: Making Sure It’s Still Right
Some methods for checking things to make sure they’re still right include prospective validation, concurrent validation, retrospective validation, and periodic revalidation. These methods involve different approaches to evaluating and confirming that the specific requirements for an intended use are met in product development and commercial production.
Regular checks to ensure things are still working correctly are important in the pharmaceutical industry. They provide assurance that the manufacturing processes are operating within defined parameters and that the end products consistently meet quality standards.
Incorporating a system for checking again into a process offers the benefit of ensuring compliance with regulatory requirements, maintaining product quality and safety, and identifying and addressing any potential issues or deviations in a timely manner.
This systematic approach to validation not only reduces the risk of product recalls and compliance issues but also enhances the overall efficiency and reliability of the manufacturing processes.
How Do You Check That Making Stuff Works Right?
Designing the Process: The First Stage
When designing the process for the first stage, there are important things to consider for validation. These include dividing the production process into separate steps and analyzing key points like mixing times or temperature. It’s also crucial to make sure that all the needs for the specified intended use are met.
To ensure that the process is designed to work well from the start, it’s important to meet the requirements for prospective validation. This means closely monitoring all manufacturing steps and key points, doing in-process testing, and thoroughly analyzing all recorded process deviations and investigation reports.
When qualifying the process for the first stage, it’s important to meet the requirements for concurrent validation. This involves fully understanding the process based on previous work, closely monitoring all manufacturing steps and key points in at least the first three production-scale batches, and inspecting systems to make sure they are still operating as originally validated with no unintended changes.
Qualifying the Process: The Second Stage
There are 4 main types of checks to consider during the qualifying process in the second stage: prospective validation, retrospective validation, concurrent validation, and revalidation. Each type plays a different role in ensuring that the process works correctly and consistently.
To check the production processes during the second stage, the company must closely monitor all steps and evaluate potential critical points. This involves testing elements such as temperature, mixing times, and in-process testing. Tools and machines must be evaluated to ensure they are operating properly. It’s important to check for unintended changes that could affect the process or equipment, and to ensure all systems are still operating as initially validated.
Examples of processes that should be validated at this stage include sterilization, aseptic filling, heat treating, plating, and plastic injection molding.
Always Watching: The Third Stage
Four validation types to be aware of in “Always Watching: The Third Stage” are:
- Prospective validation: This is done during the development stage to analyze critical points in the manufacturing process before introducing new products and manufacturing processes.
- Concurrent validation: This is carried out during normal production and involves close monitoring of all manufacturing steps and critical points, particularly in the first three production-scale batches.
- Retrospective validation: This involves analyzing accumulated results from past production batches to assess process consistency and stability of established products.
- Periodic revalidation: This offers the opportunity to verify that systems are still operating as initially validated and that no unintended changes have affected the process, system, or equipment.
By conducting these checks, companies can ensure that the production process is working as intended, meeting regulatory requirements, and maintaining good documentation practices. These checks ultimately help in validating pharmaceutical production processes and ensuring product quality and safety.
Keeping Stuff Clean: How to Check It’s Super Clean
To ensure that things are really clean, there are several key steps:
- Prospective validation during development
- Concurrent validation during production
- Retrospective validation to assess consistency
- Periodic revalidation to check systems
These validation types confirm that specific requirements for intended use are met. To verify tools and machines are working, one can:
- Understand the process based on prospective work
- Intensify monitoring of manufacturing steps and critical points
- Analyze results from past production batches
- Periodically check for unintended changes
Using these validation methods can benefit by:
- Maintaining quality control
- Meeting regulatory requirements
- Ensuring consistency
- Streamlining and automating with digital tools
Making Sure Tools and Machines Are Good to Go
Making Sure Laptops and Programs Work Well
When it comes to ensuring that laptops and programs work well, there are important checks that need to be considered.
Prospective validation during the development stage is necessary. This includes the division of the production process into separate steps and the analysis of potentially critical points in the manufacturing process.
Concurrent validation is crucial and is carried out during normal production. It requires a full understanding of the process based on prospective work. It also involves very close and intensified monitoring of all the manufacturing steps and critical points.
Retrospective validation is important for the analysis of accumulated results from past production batches manufactured under identical conditions to assess the consistency of a process. This helps in maintaining good working condition of laptops and programs over time.
Furthermore, periodic revalidation offers the opportunity to check that the systems are still operating as originally validated and that no unintended changes have affected the process, system, or piece of equipment and the end result.
All of these measures contribute to ensuring that laptops and programs work well and remain in good working condition.
Neat Ways That Checking Stuff Helps
Checking is important for making sure things work properly. It provides evidence that the requirements for a specific intended use are met. There are different stages involved, including process design, process qualification, and continued process verification. These are done through prospective validation, concurrent validation, retrospective validation, and periodic revalidation.
Checking also helps to keep tools and machines in good condition, ensuring they still operate as intended and thatno unintended changes have affected the process. This can prevent issues and ensure smooth and efficient manufacturing.
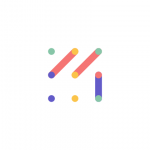
Vizologi is a revolutionary AI-generated business strategy tool that offers its users access to advanced features to create and refine start-up ideas quickly.
It generates limitless business ideas, gains insights on markets and competitors, and automates business plan creation.