The Four Rules of Toyota’s Car Building Secrets
Toyota has four rules for building cars. These rules are the foundation of its success and have helped Toyota become one of the most respected car manufacturers. In this article, we’ll look at the four secrets behind Toyota’s car-building process and how they have helped the company maintain its reputation for quality and innovation.
Origins of Toyota’s Manufacturing Philosophy
Toyota’s manufacturing philosophy originated from the Toyota Production System (TPS). The TPS aimed to gain a competitive advantage by achieving high quality, low cost, and Just-In-Time delivery in world markets. Its focus was eliminating waste, overburden, and unevenness, creating standardization for safe operations, ensuring consistent quality, and pursuing continuous improvement.
This philosophy also involved conducting experiments and creating a community of scientists within the organization. Toyota’s manufacturing philosophy has significantly impacted the global car manufacturing industry, leading to its worldwide adoption. Toyota’s four basic rules include specifying work processes, standardizing connections between workers, designing pathways for products and services, and using scientific methods to make improvements.
These principles have played a crucial role in shaping the global car manufacturing industry, setting a standard for manufacturing systems’ design and operation.
Overview of TPS
The Toyota Production System has four rules:
- Specifying work processes.
- Standardizing connections between workers.
- Designing pathways for products and services.
- Using scientific methods to make improvements
These rules help create a community of scientists and enable the establishment of hypotheses when defining specifications and testing them.
Additionally, the principles of Jidoka, Just-in-Time, Heijunka, and All or None contribute to the TPS by:
- Eliminating waste, overburden, and unevenness
- Creating standardization for safe operations and consistent quality
- Focusing on continuous improvement
The TPS rules also impact supplier management and global car manufacturing by establishing clear supplier-customer relationships and specific pathways for goods and services. This aims to improve communication and make potential improvements at the lowest possible organizational level, resulting in more efficient and effective operations for suppliers and improved quality for global car manufacturing.
What Are the Four Rules of Toyota Production System?
Rule 1: Jidoka (Autonomation) – Empowering Machines and Operators
Jidoka, or autonomation, has a rich historical development. It dates back to the roots of the Toyota Production System. Spear and Bowen (1999) exemplify TPS as a system that drives people at all levels to get involved in experiments and learn from empirical data. This results in the creation of a community of scientists who set up all operations as experiments and follow four rules to do that.
Implementing Jidoka involves empowering operators to understand their work processes clearly, standardizing connections between workers, designing product and service pathways, and improving methods using scientific approaches.
For example, Toyota marks the floor length for each work area in tenths and creates a clear supplier-customer relationship, with a direct connection established between each supplier-customer. This ensures that products and services flow to a specific person or machine rather than just the next available person or machine.
Improvements follow the scientific method at the lowest possible organizational level. The key principles and effects of Jidoka (Autonomation) are improved production efficiency, minimized overburden, and smooth flow through standardized work and methodical improvements.
Historical Development of Jidoka
Jidoka has a rich history within the Toyota Production System. It has evolved and been influenced by historical developments in manufacturing processes, shaping the system’s philosophy and success.
Jidoka now encompasses specifying work processes, standardizing connections between workers, designing product and service pathways, and using scientific methods for improvement. These developments aim to ensure high quality, low cost, and Just-In-Time delivery.
These historical developments have profoundly impacted the implementation of Jidoka in manufacturing processes and led to the establishment of a community of scientists within the organization.
Toyota has fully embraced these principles in its daily operations, treating all processes as experiments. This approach involves everyone at all levels in experiments, driving organizational learning and contributing significantly to the success of the Toyota Production System.
Real-World Implementation
Toyota’s Manufacturing Philosophy streamlines operations and reduces waste in real-world production settings. By following TPS rules, organizations have overcome challenges of overburden, waste, and unevenness while achieving standardization for safe operations and consistent quality.
This implementation has successfully driven people at all levels to get involved in experiments and prompt organizational learning. Challenges have included difficulties connecting people, defining clear supplier-customer relationships, and constructing efficient production lines that ensure smooth flow and timely delivery.
However, the benefits of improving work processes, standardizing connections between workers, designing pathways for products and services, and using scientific methods to make improvements have revolutionized global car manufacturing and supplier management. For instance, specifying work processes has enabled workers to understand the sequences of their activities, and standardizing connections has facilitated clear supplier-customer relationships and resistance-free production.
Rule 2: Just-in-Time – The Right Parts at the Right Time
Toyota’s production system revolves around getting the right parts at the right time. This means materials and parts are available when needed and in the right quantity.
The Kanban System is an example of this principle in action. It regulates material flow through visual cues, like cards or signals, to ensure supplies are replenished as needed without overstocking.
Principles of Just-in-Time
The principles of Just-in-Time focus on eliminating waste, overburden, and unevenness. They also aim to create standardization and continuous improvement in the production process.
Implementing Just-in-Time in manufacturing ensures efficient production. This is achieved by eliminating waste, improving quality, and reducing production times through shorter fabrication and assembly sequences. The Kanban system further enhances this principle by providing a visual signaling system to regulate the flow of materials and maintain production consistency. This application ensures that materials and components are replenished precisely when needed, aligning with Just-in-Time principles and contributing to efficient production.
The four rules of the Toyota Production System have significantly impacted global car manufacturing. They have improved work processes, standardized connections between workers, designed pathways for products, and used scientific methods for improvements. This framework has allowed manufacturers to streamline operations, reduce waste, and increase productivity. These rules contribute to higher efficiency in car assembly lines, reducing manufacturing costs and improving the overall quality and reliability of vehicles worldwide.
Kanban System Application
The Kanban system contributes to the principle of Just-in-Time in the Toyota Production System. It ensures that work tasks are completed as needed and in a continuous flow. This helps prevent overproduction and reduces lead times, aligning with the TPS objective of minimizing waste.
In Toyota’s manufacturing processes, the Kanban system manages inventory levels and signals when more parts need to be produced. This helps maintain a balanced flow of work and resources, ensuring a smooth and efficient production process.
The Kanban system also aligns with the principles of Heijunka and leveling workload. It visually represents work orders and schedules production based on customer demand, allowing for better workload distribution and production line balancing within Toyota’s operations.
Rule 3: Heijunka – Leveling Workload
Heijunka, also known as leveling workload, has a big impact on production efficiency. It evens out the natural ups and downs in production rates, keeping a steady workflow. This reduces waste, overburden, and unevenness. Implementing Heijunka in manufacturing makes the production line smoother and more balanced, reducing the risk of bottlenecks and overproduction. It also helps with scheduling and resource allocation, improving overall productivity and reducing costs.
Heijunka is important in the Toyota Production System because it aligns production with customer demand, reduces inventory and lead times, and improves quality and flexibility. Heijunka creates a stable and predictable production environment by spreading work out evenly over time, enabling continuous improvement and process optimization.
Effects on Production Efficiency
Implementing the Heijunka principle affects production efficiency in Toyota’s manufacturing process by creating a predictable and level production schedule, which allows for a more stable and efficient workflow. This proactive approach helps to minimize waste and overburden, resulting in smoother and more consistent production operations.
Applying the Kanban System within the Toyota Production System significantly impacts production efficiency by enabling a clear and visual signaling system for inventory control and demand management. This method ensures that materials are replenished only when they are needed, reducing excess inventory and streamlining the production process.
Additionally, the ‘All or None’ principle in Toyota’s decision-making process impacts production efficiency by encouraging a yes/no approach to sending requests and receiving responses. This leads to clear and precise supplier-customer relationships and minimizes ambiguity and delays in operations.
Deep Dive into Rule 4: All or None
Understanding the ‘All or None’ Principle
The ‘All or None’ principle is important to Toyota’s manufacturing philosophy. It helps workers understand the complete set of activities for a task, including the sequence, timing, and desired outcome.
For example, Toyota marks the floor length for each work area in tenths so that any timing deviation can be quickly identified. This principle impacts decision-making at Toyota by creating direct supplier-customer relationships and clear connections between individuals. It also has practical implications for the TPS rules, particularly in constructing the production line where goods and services flow to a specific person or machine. This principle is crucial in global car manufacturing, highlighting the importance of a particular pathway for products and services, reflecting Toyota’s streamlined approach for optimal efficiency.
How ‘Rule 4’ Impacts Toyota’s Decision-Making
The ‘All or None’ principle of Rule 4 significantly impacts Toyota’s decision-making process. It ensures that improvement follows the scientific method at every level of the organization. This principle enables the company to adopt a systematic approach to problem-solving and enhancement. It fosters a culture of innovation and learning within the organization.
For example, if a worker on the production line identifies an opportunity for improvement, they must follow the scientific method when developing and applying the proposed changes. This adherence to Rule 4 is evident in Toyota’s manufacturing and production processes. Every improvement initiative is guided by scientific principles, ensuring that each alteration is thoroughly evaluated and based on empirical evidence. This optimizes efficiency and quality control and aligns with the company’s operational strategy.
By adhering to Rule 4, Toyota systematically enhances its process for designing pathways for products and services. This contributes to its competitive advantage and world-renowned quality standards.
Rules Applied: TPS at Work
Examining Toyota’s Factories
Toyota’s factories use Jidoka, Just-in-Time, Heijunka, and the ‘All or None’ rule from the Toyota Production System.
Jidoka ensures product quality by stopping production when a defect is found. Just-in-Time reduces inventory and waste. Heijunka aims to level production by regularly making goods in small quantities.
Toyota applies the ‘All or None’ rule through lean manufacturing, where workers perform multiple tasks and no subpar products are accepted.
These rules impact efficiency and decision-making in the factories. TPS fosters accountability, encourages improvement, and promotes learning from mistakes. This creates a culture that values continuous improvement at all levels.
The TPS rules also affect supplier management and Toyota’s global manufacturing. By establishing clear customer-supplier relationships and specific product pathways, these rules streamline operations and build meaningful connections. This enables Toyota to maintain consistent quality throughout its global supply chain, contributing to the company’s success.
What Are the Four Rules of Toyota Production System?
Exploration of TPS’ Rules in Supplier Management
The rules of the Toyota Production System greatly impact supplier management. They ensure a clear supplier-customer relationship and establish a direct connection between each supplier and customer.
These rules influence supplier management by creating a specific pathway for products and services to flow through the production line. This ensures that goods and services flow to a specific person or machine.
Additionally, the rules provide a structured approach to improvement. They demand that any improvement follow the scientific method, be guided by a teacher, and occur at the lowest possible organizational level.
TPS principles can be applied in supplier management by having clear yes/no approaches to sending requests and receiving responses. It also involves establishing a specific sequence of activities for workers and standardizing the connections between workers.
Implementing TPS rules in supplier management has a global impact on car manufacturing. It promotes continuous improvement, establishes standardized operations for consistent quality, and eliminates waste, overburden, and unevenness, benefiting manufacturers worldwide.
Impact of TPS Rules on Global Car Manufacturing
The Toyota Production System rules have specific impacts on global car manufacturing. The TPS rules promote the elimination of waste, overburden, and unevenness, creating standardization for safe operations, consistent quality, and continuous improvement. These principles affect car production on a global scale by ensuring efficient production, reducing inventory levels, and maintaining a consistent workflow.
For instance, the principles of Jidoka, Just-in-Time, Heijunka, and All or None have been implemented in global car manufacturing to achieve high quality, low cost, and delivery efficiency. Real-world examples of TPS rules implemented in car production include specifying work processes, standardizing connections between workers, designing pathways for products and services, and using scientific methods to improve.
For instance, car manufacturers have implemented specific measures to ensure that work processes are clearly defined, supplier-customer relationships are established, production lines are constructed to ensure the flow of goods and services, and continuous improvement methods are employed. These implementations have improved productivity, reduced costs, and enhanced quality in car manufacturing.
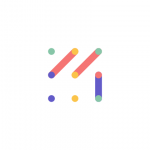
Vizologi is a revolutionary AI-generated business strategy tool that offers its users access to advanced features to create and refine start-up ideas quickly.
It generates limitless business ideas, gains insights on markets and competitors, and automates business plan creation.