Getting Started with Lean Management
Would you like to improve your business processes and make them more efficient? Lean management might be the solution for you.
Lean management focuses on eliminating waste and continuously improving to help your organization operate more effectively and deliver greater value to customers.
This article will explore the basics of lean management and give you the knowledge you need to start your lean journey.
Fundamentals of Lean Management
Lean management focuses on:
- Identifying value.
- Creating a continuous workflow.
- Developing a pull system.
- Visualizing workflow.
- Pursuing continuous improvement.
Value, from the customer’s perspective in lean management, means optimizing resources and providing a steady workflow based on customer demands. This approach aims to create value for the customer and eliminate waste through principles like identifying value, continuous workflow, pull systems, and visualizing workflow. These principles streamline processes and eliminate inefficiencies to achieve perfection.
The Origins and Evolution of Lean Management
Core Elements of Lean Management
Lean management focuses on understanding value and eliminating waste. The five core elements are central to this practice:
- Identifying value.
- Creating continuous workflow.
- Developing a pull system.
- Visualizing workflow.
- Focusing on continuous improvement
This approach helps companies optimize resources and better serve their customers, aligning with Lean principles.
By mapping the value stream and identifying waste, companies can pinpoint underutilized resources and areas for improvement. Pursuing perfection through continuous improvement is crucial in Lean management, aiming to maximize customer value while minimizing waste for long-term organizational success.
Understanding the 5 Key Principles of Lean Management
Defining Value from the Customer’s Perspective
In Lean Management, “value” means meeting customer needs and desires while minimizing waste. This involves creating products or services that solve a specific problem for the customer or provide a unique benefit that they find useful.
Lean Management focuses on understanding true customer demand and delivering products or services that align with these demands, rather than relying on guesswork or forecasts.
Organizations can define value by thoroughly understanding customer needs and preferences through direct engagement and observation. This can be achieved by gathering customer feedback through surveys, focus groups, and direct communication.
Data analytics tools can also be utilized to track customer behavior, understand purchasing patterns, and identify areas for improvement based on real customer demand.
To define value, organizations can use tools like customer relationship management (CRM) software, Net Promoter Score (NPS) surveys, online reviews, social media monitoring, and direct customer engagement channels. These tools enable organizations to gather, track, and analyze customer feedback to identify areas for improvement and ensure that products or services are aligned with true customer demands.
Mapping the Value Stream to Identify Waste
Mapping the value stream is a key step to identify waste in production. It involves creating a visual representation of the entire process, from receiving raw materials to delivering the product. This helps make waste more visible and easier to detect by identifying all steps and activities. Organizations can categorize different types of waste, like overproduction and waiting time, by tracking each step in the value stream. This involves process mapping, time observation, and data collection.
Challenges include resistance from employees and difficulties in data collection. Best practices for lean management include engaging employees, continuous communication, and regular review and improvement of processes.
Enabling a Steady and Continuous Workflow
Organizations can improve workflow by using lean management methodologies. This helps work move smoothly through different stages without interruptions or delays. Lean principles focus on optimizing resources and meeting customer demands. By identifying value, visualizing workflow, and making continuous improvements, companies can achieve a smooth and efficient workflow. Lean management has been successful in manufacturing, software development, startups, accounting, and healthcare.
It eliminates waste and improves operations. Proficiency in lean management skills is a valuable investment, making organizations flexible, customer-focused, and efficient.
Implementing a Pull System to Manage Flow
Implementing a pull system to manage flow within an organization involves several steps and considerations.
- First, the organization must identify the demand for its products or services to ensure that the pull system is driven by actual customer needs.
- Then, the organization must establish clear and effective communication channels to relay customer demand throughout the production or service delivery process.
- Furthermore, it’s important to continuously monitor and adjust inventory levels to prevent overproduction and limit excess in-process inventory.
Effectively integrating a pull system into existing processes and workflows requires careful analysis of the current state of operations.
This analysis should identify areas of waste and excess inventory that can be minimized through the implementation of a pull system.
By aligning the pull system with the organization’s existing processes, the goal is to create a smooth and efficient flow of work.
When implementing a pull system, organizations must be mindful of common challenges and pitfalls, such as inaccurate demand forecasting, resistance to change from employees, and inadequate inventory control.
To mitigate these challenges, organizations can invest in employee training and education to create a culture of continuous improvement.
Additionally, implementing robust inventory management and demand forecasting tools can help mitigate risks associated with inaccurate demand forecasting.
Pursuing Perfection through Continuous Improvement
Companies can pursue perfection through continuous improvement. They can do this by implementing Lean Management principles. This involves identifying value, creating a continuous workflow, developing a pull system, visualizing workflow, and striving for continuous improvement.
By integrating continuous improvement into daily operations, organizations can optimize resources and meet real customer demands. This includes addressing common types of waste, such as overproduction, defects, transportation, and waiting, and eliminating them.
Lean Management helps organizations identify and eliminate waste by visualizing workflow and implementing a pull system. This allows them to produce based on customer demand rather than stockpiling inventory.
Leveraging Lean Management Benefits
Lean management principles help organizations improve workflow and efficiency. By optimizing resources and aligning workflow with real customer demands, organizations can save time and money. This approach also boosts customer satisfaction, leading to increased revenue from referrals and repeat business in different industries.
By implementing lean management, organizations reduce waste and enhance overall performance. Programs like Lean Six Sigma Green Belt teach essential skills applicable in services, manufacturing, and general business roles. They cover various tools for lean management and ways to eliminate waste, improving efficiency.
Mitigating Common Lean Management Implementation Challenges
One common challenge when implementing Lean Management principles is resistance to change. Employees and management may hesitate to adopt new processes, especially if they have been successful with traditional methods. Lack of leadership support is another challenge. Management needs to be fully committed to the Lean principles for successful implementation.
Organizations may struggle with sustaining the continuous improvement aspect of Lean Management. It requires ongoing effort and dedication.
To mitigate these challenges, organizations can focus on creating a culture of continuous improvement. They can provide training and education on Lean principles and demonstrate the benefits of Lean Management through real-world examples. Leadership buy-in is essential, so executives should be actively involved in promoting and leading the Lean initiatives. Moreover, organizations should establish clear goals and metrics to measure progress and celebrate successes.
Strategies and best practices for overcoming resistance and driving sustained adoption of Lean Management principles include effective communication to clearly explain the reasons behind the change. Involving employees in the process to gain their buy-in and recognizing and rewarding employees who actively contribute to Lean initiatives is important. It is also essential to empower employees to make suggestions and implement improvements, ensuring that Lean Management becomes a part of the organization’s culture.
Insightful Examples of Lean Management in Practice
Lean Management in Software Development
Lean management principles can be easily applied in software development. This involves identifying customer value, improving workflow, creating a pull system based on customer demand, visualizing workflow, and seeking continuous improvement.
By aligning development processes with real customer demands, lean management can optimize resources, reduce waste, and create a more efficient and customer-focused software development lifecycle.
Challenges and opportunities in implementing lean management in software development include resistance to change, rigid organizational structures, and the need for a cultural shift towards customer value. Opportunities for lean management in software development include improved customer focus, faster response to customer requirements, and increased flexibility to adapt to changing market conditions.
Lean management techniques, like Kanban, can be used for more efficient project management in software development. This involves visualizing workflow, limiting work in progress, and enhancing the team’s ability to adapt to changing priorities and customer needs in a more agile and efficient manner.
Utilizing Kanban for Effective Project Management
Kanban is a popular approach in Lean management. It’s great for making project management more effective. By visualizing workflow and limiting work in progress, it helps teams optimize their workflow, find and remove bottlenecks, and increase productivity.
The key principles and practices of Kanban that make it useful for project management include:
- Visualizing work
- Setting work-in-progress limits
- Managing flow
- Making process policies clear
- Using feedback loops to improve performance constantly
By following these principles, teams can:
- Make their progress more transparent
- Identify areas for improvement
- React better to changing project needs
Teams can improve their project management using Kanban by:
- Regularly reviewing their Kanban board
- Incrementally updating and improving their processes
- Using metrics to monitor and measure their performance
By taking these steps, teams can create a culture of continuous improvement, resulting in more efficient project management and successful project outcomes.
Adapting Lean Principles in the Startup Ecosystem
Lean principles can help startups meet their unique needs and challenges. This involves focusing on creating value for the customer, optimizing resources, and maintaining a steady workflow based on real customer demands.
Startups can implement lean management principles effectively by identifying value, creating a continuous workflow, developing a pull system, visualizing workflow, and continuous improvement to achieve sustainable growth.
However, integrating lean principles into startup operations may face obstacles such as resistance to change, lack of resources, and limited experience with lean management principles. But, doing so also offers the opportunity to improve customer focus, increase flexibility, and respond faster to customer requirements.
Lean Management Transformations in Healthcare
Implementing lean management in healthcare has challenges like staff resistance to change, lack of leadership support, and difficulties in changing processes. But it also offers opportunities like improved patient care, cost reduction, and operational efficiencies.
Lean management can streamline administrative processes, reduce wait times, and enhance the patient experience in healthcare settings. Successful case studies have shown improvements in patient flow, reduced infections, and increased staff satisfaction.
Involving frontline staff in the process and focusing on continuous improvement are vital. Adapting lean management to the unique challenges of healthcare is crucial.
Applying Lean Thinking to Financial Processes
Lean management principles can help make financial processes better.
Here’s how:
- Identify value.
- Keep the workflow going smoothly.
- Develop a pull system.
By understanding the value stream and seeing the workflow, organizations can find and fix waste and inefficiencies in financial processes.
This can lead to better effectiveness, efficiency, and cost reduction.
It can also cut down on over-processing, lower inventory, and reduce transportation and wait times.
Implementing Lean Thinking can also create steady workflow based on actual customer needs, making financial processes more customer-focused, flexible, and quicker to meet customer requirements.
Lean Management Inquiries and Clarifications
Lean Management involves identifying value, optimizing workflow, establishing a pull system, visualizing workflow, and embracing continuous improvement. Companies can use these principles to streamline processes, cut waste, and deliver value to customers.
Implementing Lean Management helps companies overcome challenges through continuous improvement. By focusing on reducing waste, businesses can refine processes and address efficiency, resource allocation, and customer satisfaction issues.
Examples of Lean Management in different industries include lean manufacturing, lean software development, Lean Six Sigma, lean startup methodologies, and value-based healthcare. These applications show that Lean Management is adaptable and can improve productivity and customer satisfaction in various business fields.
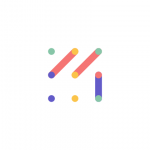
Vizologi is a revolutionary AI-generated business strategy tool that offers its users access to advanced features to create and refine start-up ideas quickly.
It generates limitless business ideas, gains insights on markets and competitors, and automates business plan creation.