Getting Your Validation Process Approved Easily
Getting your validation process approved can be simple if you know the right approach. By following a few easy steps, you can streamline the process and improve your chances of getting the green light. Whether it’s for a project, proposal, or new initiative, understanding the key elements of the validation process is important.
In this article, we’ll explore practical tips and strategies to help you easily get your validation process approved.
Understanding Process Validation
What Process Validation Means
Process validation involves process design, process qualification, and ongoing process verification. It can be done before use (prospective validation), during use (concurrent validation), and after use (retrospective validation and revalidation).
Following rules and guidelines set by regulatory authorities, such as the USFDA and GHTF, is important for successful process validation. Good documentation practices are essential to provide evidence of controlled processes throughout the validation stages.
Documenting evidence of controlled processes and adhering to regulatory guidelines are crucial to successful process validation. For instance, software tools like SafetyCulture can assist by offering ready-to-use templates and digital storage for process validation evidence.
3 Main Parts of Process Validation
Designing the Process
Designing a validation process involves considering critical factors like process parameters and identifying potential failure modes. This includes conducting a risk assessment and using tools like Failure Mode and Effects Analysis (FMEA). It’s important to clearly define the validation protocol, set acceptance criteria, and conduct thorough testing to gather reliable data. Good documentation practices, recommended by USFDA and GHTF, are essential for demonstrating controlled processes.
A systematic approach helps companies create a validation process that mitigates risks and ensures product quality and reliability. Examples in the blog show how following these practices can lead to successful validation processes and compliance with regulations.
Checking the Process
Regular checks are important for ensuring that the validation process is working correctly. It’s best to check at the end of each stage and at the end of each project to make sure it meets the defined criteria.
When checking the process for validation, important things to look at are production output, error rates, customer feedback, and compliance with industry standards.
If you don’t do regular checks, there’s a risk of undetected errors or deviations, which can lead to non-compliance, product defects, and safety hazards. This could result in customer dissatisfaction, financial losses, and regulatory sanctions.
So, it’s really important to do regular and thorough checks to prevent these consequences.
Making Sure the Process Keeps Working
To make sure a designed process works well and keeps working well, you can do things like ongoing training, regular audits, and clear documentation. Regular checks and assessments can be done to make sure a validated process is reliable and consistent. This includes monitoring key process parameters, using statistical data analysis, and having a change control system to manage any changes.
Also, using a robust corrective and preventive action (CAPA) system and doing risk assessments can help address any potential issues and keep the process working properly. These strategies can help identify and manage risks, making sure the validation process approval stays effective and reliable.
4 Different Kinds of Process Validation
Validation Before Using
Before using any process, it’s important to go through the key steps involved in validation. The process validation involves three stages:
- Process design.
- Process qualification.
- Continued process verification.
Ensuring that the validation process is thorough and effective can be achieved by documenting evidence of controlled processes and using tools like SafetyCulture.
The potential consequences of not validating a process before using it include the risk of producing products that do not meet quality standards, leading to customer dissatisfaction and possible legal implications.
It’s crucial to follow the guidelines set by regulatory bodies such as the USFDA and GHTF to validate processes effectively and ensure product quality and safety.
Validation After Using
After the validation process, we can measure its effectiveness using real-time data and comparing it with established performance criteria. This includes monitoring the process output to make sure it consistently meets the predetermined specifications. Regular audits and reviews are conducted to identify any deviations and take corrective actions to maintain the process integrity.
Ongoing monitoring and periodic revalidation are crucial to ensure that the validated process continues to function as intended. This involves regular assessments to confirm that it still meets the predefined requirements and remains in control. Any changes to the process or equipment are also evaluated to determine their impact on validation.
Documentation of successful validation is required to demonstrate compliance with regulatory standards and ensure process reproducibility. This includes detailed records of process parameters, equipment calibration, and any deviations encountered during the validation process. By maintaining thorough documentation, organizations can provide evidence of a controlled and consistently performing process, ensuring product quality and safety.
Validation During Use
Validation during use ensures that a process is effective and safe. Factors like process consistency, potential failure points, and impact on product quality should be considered.
For instance, in the pharmaceutical industry, validating the manufacturing process for a new drug involves documenting steps, testing for variations, and ensuring the final product meets quality standards.
To measure effectiveness, regular quality control checks, real-time monitoring of critical process parameters, and analyzing performance data over time are important.
Similarly, in the food production industry, monitoring the effectiveness of a packaging process includes regularly checking seal integrity and conducting shelf-life studies for product quality and safety.
Doing Validation Again
Validation should be repeated to ensure the manufacturing process meets quality standards. Companies can identify changes in processes, materials, or equipment that might affect product quality.
For example, in the pharmaceutical industry, a new raw material supplier may require revalidation for product safety.
The frequency of revalidation depends on the process nature. Critical processes might need more frequent revalidation.
Skipping revalidation poses a risk of producing low-quality products, leading to safety issues and recalls. Regulatory action and damaged reputation could follow.
Thus, repeating validation is crucial for maintaining manufacturing integrity and ensuring product quality.
Rules to Follow for Process Validation
Steps to Get Your Validation Approved
To get validation approval, you should follow specific steps. The FDA recommends:
- Performing process design
- Process qualification
- Continued process verification to ensure efficient validation approval.
Good documentation practices are crucial throughout these stages.
Ensuring evidence of controlled processes is thoroughly documented is imperative for approval.
It’s also essential to use tools like SafetyCulture to facilitate documentation and process validation.
With these steps and recommendations in place, you can ensure your validation process meets the necessary requirements for approval.
What the FDA Says You Should Do
The FDA has specific guidelines for process validation. These include three stages: process design, process qualification, and continued process verification. There are also four types of process validation: prospective, retrospective, concurrent, and revalidation.
Following these guidelines is crucial for good documentation practices and aligns with industry best practices. Failure to comply could lead to product quality issues, compliance violations, and potential safety hazards for consumers.
It’s important for companies to document controlled processes and validate production to ensure product quality and safety. Tools like SafetyCulture can help with documentation and validation, enabling companies to comply with FDA guidelines and industry standards.
Helpful Tips for Each Validation Stage
Tips for Designing the Process
When designing a validation process, it’s important to consider key factors. These include documenting evidence for controlled processes and aligning the process with regulatory guidelines.
The process design can greatly affect the validation outcome and effectiveness. Poorly designed processes may result in unreliable results and non-compliance with regulations.
To ensure successful validation, it’s important to thoroughly plan, clearly document process parameters, and closely align with regulatory guidelines.
Tools like SafetyCulture can help with effective documentation and validation, leading to successful outcomes.
Tips for Checking the Process
To ensure process checks are accurate and thorough, follow best practices:
- Implement good documentation practices.
- Adhere to regulatory guidelines (such as USFDA and GHTF).
- Use tools like SafetyCulture for documentation.
Maintain process validation effectiveness:
- Conduct the 3 stages of process validation: process design, process qualification, and continued process verification.
- Implement the 4 types of process validation: prospective, retrospective, concurrent, and revalidation.
Document evidence of controlled processes and provide validation examples. Avoid common pitfalls:
- Incomplete or inconsistent documentation.
- Lack of adherence to regulatory guidelines.
- Insufficient evidence of controlled processes.
By following best practices and avoiding common pitfalls, ensure rigorous and effective process validation.
Tips for Ongoing Process Checks
Ongoing process checks can be easily implemented. This involves setting clear and measurable performance criteria that match the process-specific requirements.
For example, in manufacturing, thresholds for temperature, pressure, or other critical variables can be set and regularly monitored. In healthcare, ongoing process checks could involve regular audits of patient care protocols, ensuring compliance with best practices. These checks also include internal audits and evaluations by external parties. Identifying potential issues during ongoing process checks can be done through proactive monitoring and surveillance systems. Automated sensors can detect anomalies triggering immediate corrective actions. Ongoing process checks can be integrated into a system of continuous improvement by analyzing trends and patterns over time to drive process enhancements. This ensures the process remains aligned with best practices and regulatory standards.
Real Examples of Process Validation
Process validation is seen in industries like pharmaceuticals, food and beverage, and manufacturing.
In pharmaceuticals, companies validate processes by thoroughly testing and documenting each production stage to ensure critical parameters are within specified limits.
In food and beverage, advanced monitoring and control systems maintain consistency and safety in the manufacturing process.
In manufacturing, automated testing and inspection processes ensure product quality and safety, reducing human error and increasing efficiency.
One challenge faced is the lack of standardized procedures, but companies adopt best practices and comply with regulatory requirements to overcome this.
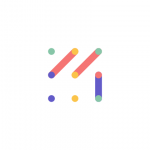
Vizologi is a revolutionary AI-generated business strategy tool that offers its users access to advanced features to create and refine start-up ideas quickly.
It generates limitless business ideas, gains insights on markets and competitors, and automates business plan creation.