How to Analyze Problems: A Kid’s Guide
Have you ever faced a problem that seemed impossible to solve? You’re not alone! Learning how to analyze problems can help you find solutions, no matter how tricky the situation may seem.
In this kid’s guide, we’ll explore practical strategies for breaking down problems and finding creative solutions. By using these simple techniques, you’ll be able to tackle any problem that comes your way.
So, let’s dive in and discover the power of problem-solving!
Understanding the Ishikawa Fishbone Diagram
Steps to Create an Ishikawa Diagram
Creating an Ishikawa Diagram involves a systematic approach.
- First, identify the specific problem to be addressed and display it at the head of the fishbone.
- Then, brainstorm and note possible causes that contribute to the problem on the appropriate branches of the fishbone.
- Categorize these causes into specific groups, such as people, process, technology, or environment, providing clarity and order to the analysis.
- Finally, carefully consider and organize the components of the Ishikawa Diagram, including the fish head, bones, causes, sub-causes, and arrows, to ensure the visual representation is easy to comprehend and analyze.
Following these steps will help the team execute a thorough problem analysis using the Ishikawa Diagram.
Identifying Potential Causes
Identifying potential causes using the Ishikawa Fishbone Diagram involves several key steps.
- Start by defining the problem.
- Then, identify major categories or factors related to the problem.
- Lastly, drill down further to potential root causes within each category.
This approach helps visualize and organize potential causes, making it easier to analyze and address the underlying issues efficiently.
Another technique, the ‘5 Whys,’ involves repeatedly asking “why” to delve into the deeper layers of potential causes until the fundamental root cause of the problem is identified. This technique encourages critical thinking and helps uncover hidden or overlooked causes, ultimately leading to more comprehensive and effective solutions.
Additionally, using an Affinity Diagram offers benefits. It allows for grouping and organizing large amounts of information, ideas, and potential causes into categories, helping to identify common themes or patterns. This method enhances collaboration and understanding among different stakeholders, leading to a more thorough and holistic analysis of potential causes and contributing factors to the problem at hand.
Breakdown of the Pareto Principle
Creating a Pareto Chart
The Pareto Chart is a helpful tool for analyzing and solving problems. To create one, start by clearly defining the problem and gathering relevant data. Then, categorize the data into groups to find the root causes. After that, organize the data in descending order to highlight the most important factors.
A Pareto Chart is used to focus on the factors that contribute to most of the problem. By identifying the most significant factors, professionals can prioritize where to focus their efforts for the best solution. This allows for allocating resources where they are most needed, leading to improved outcomes.
The significance of the Pareto Principle in quality management lies in its ability to help identify and address the most important factors over the less important ones. By focusing on the critical factors, quality management processes can be streamlined and resources can be allocated more efficiently for maximum impact. This principle has proven to be a valuable tool across various industries for driving intelligent growth and productivity.
Interpreting a Pareto Chart
A Pareto Chart is a useful visual tool for identifying and prioritizing significant factors. It shows the “80/20 rule,” where 80% of effects come from 20% of factors. This helps determine where to prioritize efforts for maximum impact. The chart includes vertical bars for each factor’s impact and a cumulative percentage line to focus on significant factors.
For example, in sales management, a Pareto chart can identify the top 20% of products generating 80% of revenue, aiding sales prioritization. Its interpretation is crucial for problem-solving, encouraging a data-driven approach to address influential components.
Exploring the ‘5 Whys’ Technique
Executing the ‘5 Whys’ Process
The process for executing the “5 Whys” technique involves these steps:
- Identifying a problem or situation that needs analysis.
- Asking “why” the problem occurred.
- Analyzing the answer to the first “why” question to determine the root cause.
- Repeating the question-asking process five times to get to the deeper cause of the problem.
- Using the information to implement effective solutions and prevent the reoccurrence of the issue.
The “5 Whys” technique can be applied to identify the root cause of a problem through a systematic process of asking “why” multiple times until the underlying issue is fully exposed. By digging deeper into the initial responses, teams can uncover the true root cause and develop more effective solutions. For example, in a manufacturing setting, a “5 Whys” analysis may reveal that a machine’s malfunction is due to inadequate maintenance rather than a mechanical issue. This insight enables teams to fix the underlying issue to prevent future breakdowns instead of just resolving the immediate problem.
Effectively using the “5 Whys” process necessitates a disciplined approach to problem solving and a commitment to root cause analysis. It’s important to involve multiple individuals from cross-functional teams to gather different perspectives and insights. Also, keeping the process simple and straightforward, without jumping to conclusions, is a critical factor in effectively leveraging the 5 Whys technique. Moreover, documentation of the “5 Whys” analysis to later track implementation of solutions and improvements is essential for driving impactful problem-solving efforts.
Example of Applying the ‘5 Whys’
One real-life example of using the ‘5 Whys’ technique is when a customer complains about a product defect on an online retail platform. The company can use the ‘5 Whys’ method to find the root cause of the defect and prevent it from happening again.
The steps for applying the ‘5 Whys’ technique involve defining the issue, asking “why” the problem occurred, and then asking “why” again after each answer until the root cause is identified. This helps in taking corrective actions.
The potential outcomes of using the ‘5 Whys’ to analyze a specific issue are many. It helps in not only solving the immediate problem but also preventing it from happening again. It can also improve understanding of processes, product development, and customer service, leading to better quality and efficiency.
Plotting Data on a Scatter Diagram
Properly plotting data on a scatter diagram involves identifying two variables and plotting them as a set of individual points. The horizontal axis represents one variable, while the vertical axis represents the other.
For example, in marketing, one might plot advertising spending on the horizontal axis and revenue on the vertical axis. By doing this, one can examine the patterns and relationships between the two variables.
There are key steps to follow when creating a scatter diagram. First, collect and organize the data before plotting. Second, label the variables clearly on the axes for easy interpretation. Third, plot each data point accurately to form a pattern that can then be analyzed.
Analyzing and interpreting patterns within scatter diagrams is important. Look for trends or clusters of points on the diagram, which would indicate relationships or potential correlations between the variables. For instance, a positive trend in the data points would suggest that the two variables are directly proportional.
Interpreting these relationships can provide valuable insights for problem solving and decision making, such as targeting the most effective marketing strategies or understanding production costs and output.
Analyzing Patterns in Scatter Diagrams
When analyzing patterns in scatter diagrams, follow these steps:
- First, identify and plot the variable on the horizontal axis.
- Then, plot the dependent variable on the vertical axis.
- Use the scatter diagram to observe the relationship between the two variables.
Scatter diagrams are a useful tool for identifying potential relationships between variables. By examining the plotted points, you can look for patterns and trends that might suggest a correlation or link between the two variables.
There are common patterns observed in scatter diagrams:
- Positive correlation: an increase in one variable corresponds to an increase in the other.
- Negative correlation: an increase in one variable results in a decrease in the other.
- No correlation: no apparent link between the variables.
These patterns can provide valuable insight into the relationship between variables, allowing for informed decision making and problem solving.
Learning About Affinity Diagrams
Grouping Ideas in an Affinity Diagram
An Affinity Diagram is a tool that groups a large number of ideas or issues into their natural relationships. This is usually done through the collective effort of team members.
By encouraging participative decision making, the diagramming process can yield a considerable number of ideas in a relatively short period. The process, therefore, calls for group dynamics to be actively facilitated and coordinated to ensure its success.
Once the ideas are gathered, the key advantage of Affinity Diagrams becomes evident: the organization of the ideas into a cohesive framework, which can then be used to generate themes, countermeasures, and further investigation.
This structured approach to problem solving and brainstorming helps to ensure that ideas are not lost and that a robust understanding of the issues is achieved. This allows for greater depth and understanding of the problem-solving process, helping the organization to effectively address the issues at hand.
Utilizing Affinity Diagrams for Group Discussions
Affinity diagrams help groups discuss and generate ideas. Members can contribute and organize their thoughts visually, making it easier to identify themes and patterns. This method is structured and organized, allowing for a more thorough analysis of ideas and better decision-making. It’s also essential for organizing and categorizing ideas, which helps to identify common threads and relationships, making problem resolution clearer.
In short, affinity diagrams offer a practical and insightful way to navigate through complex problems concisely.
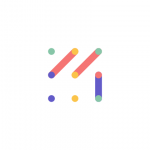
Vizologi is a revolutionary AI-generated business strategy tool that offers its users access to advanced features to create and refine start-up ideas quickly.
It generates limitless business ideas, gains insights on markets and competitors, and automates business plan creation.