Join Our Lean Management Training Today!
Ready to take your business to the next level? Consider Lean Management training. Our program offers practical strategies for streamlining processes and improving efficiency. You’ll learn to identify and eliminate unnecessary steps in your workflow, leading to increased productivity and cost savings. Join us today and start reaping the benefits of lean management!
Benefits of Lean Management for Professionals
Managers and Team Leaders
Managers and team leaders can benefit from using lean management principles. They help understand operational processes and find ways to streamline and reduce waste. This leads to continuous improvement, better performance, and less waste.
Effective techniques for managers include value stream mapping, 5S, Kaizen events, and standard work development. These focus on cutting out non-value-added activities, standardizing work, and encouraging continuous improvement.
To improve their lean management skills, managers should participate in Lean Six Sigma tools and methodologies, value stream mapping, waste reduction strategies, and creating a culture of operational excellence. They should also focus on personalized toolkits and critical management principles for Lean operating systems.
Process Improvement Specialists
Process improvement specialists find areas in a company’s processes that need improvement. They do this by analyzing and evaluating current workflows. They look for bottlenecks, unnecessary steps, and inefficiencies. They also gather data on key performance indicators, customer feedback, and employee input to find specific areas for enhancement.
To make processes more efficient, they use techniques like Lean Six Sigma, developing standard operating procedures, and encouraging continuous improvement within the organization. They also use methods like Value Stream Mapping, Kaizen events, and Gemba walks to find and eliminate waste while optimizing workflow. They use a variety of tools such as statistical process control charts, Pareto analysis, and root cause analysis to identify performance issues and develop improvement initiatives.
Their goal is to make meaningful changes and sustain efficiency gains within the organization.
Operational and Quality Managers
Operational and quality managers use lean management principles for continuous improvement. They implement Lean Six Sigma tools to reduce waste and analyze performance. Interactive learning methods, like group activities and role-playing, are used in training programs to enhance employee engagement and practical understanding of lean principles.
Purdue University offers an online certification course on Lean Principles. The course focuses on critical concepts and management principles related to Lean operating systems deployment. It provides targeted content and engagement opportunities for students. The program also offers an official certificate in Lean Principles along with 3.5 Continuing Education Units upon completion.
Learning Objectives and Skills Gained
Key Lean Management Principles and Practices
Lean management principles and practices have many benefits for managers and team leaders. They help improve efficiency and productivity. Concepts like value stream mapping and standardized work help identify and remove unnecessary activities, making processes more efficient. Tools such as Kanban boards and Gemba walks help measure and analyze performance, leading to continuous improvement. Applying these methods can lead to organizational excellence and sustainable success for teams.
Techniques for Streamlining Processes
Lean management is about streamlining processes in an organization. One technique is value stream mapping, which identifies wasteful steps in a process. Another is 5S, which promotes workplace organization. Kaizen events allow teams to make immediate changes. Implementing lean management principles enhances process efficiency. Eliminating waste, optimizing resources, and improving quality lead to smoother workflows.
Tools like key performance indicators (KPIs) measure performance and track progress over time. By using these tools, companies can achieve significant gains in operational effectiveness.
Tools for Measuring and Analyzing Performance
Performance measurement in a professional setting involves using various tools. These tools include balanced scorecards, KPI dashboards, and benchmarking. They help assess and evaluate different aspects of an organization’s operations.
These tools help in identifying areas for improvement and streamlining processes. They provide comprehensive data on quality, productivity, customer satisfaction, and financial performance.
For example, businesses regularly measure and analyze key performance indicators like customer retention rates, production cycle times, defect rates, and labor productivity. This helps them gain insights into their operational efficiency and effectiveness.
By using these tools, organizations can make informed decisions, set achievable performance targets, and effectively monitor their progress towards continuous improvement and waste reduction.
Training Schedule and Participation Requirements
Dates and Duration of the Training Program
The Lean Management training program from Purdue University lasts eight weeks. It requires about four to five hours per week.
The program aims to develop leaders in Lean Six Sigma implementation and achieving exceptional results. It offers industry-specific tracks and expert instructors.
The training is 100% online and led by instructors. This allows for flexible learning schedules. Specific dates for the program are not provided.
The program focuses on personalized toolkits for Lean methodologies and critical management principles. It does not have rigid, predetermined session dates.
Expected Weekly Time Investment for Participants
The Lean Management program requires a time commitment of about four to five hours per week for eight weeks.
Participants should plan to dedicate this time to engaging with the material, including video lectures, readings, quizzes, and interactive discussions.
They are also encouraged to apply Lean principles and tools in their professional environments, contributing to process optimization and skill development.
By investing this time each week, participants can expect to gain a deeper understanding of Lean principles and methodologies, and develop expertise to drive lasting change and improvement within their industries.
Key Modules and Workshop Sessions
The Lean Management training program covers a variety of topics, including Lean Six Sigma tools and methodologies, Lean operating systems deployment, and specialized industry tracks.
Participants will engage in interactive learning methods, such as group activities and role-playing, to gain practical examples and hands-on experience in Lean principles.
The program aims to develop leaders who can drive continuous improvement and reduce waste in organizational processes, regardless of their industry or role. After completion, managers, team leaders, process improvement specialists, and operational and quality managers will have skills to implement Lean methodologies, improve organizational performance, and achieve exceptional results.
This comprehensive approach ensures that participants acquire practical knowledge and tools that they can immediately apply within their roles, leading to sustained improvements in company performance.
Interactive Learning Methods
Group Activities and Role-Playing
Group activities and role-playing help people understand and apply lean management principles. They provide hands-on learning experiences, where participants learn how to use lean methodologies in real-world situations. These activities help individuals develop skills like problem-solving, communication, teamwork, and decision-making, which are important for successful lean management.
By taking part in these activities, lean management professionals can gain a deeper understanding of lean principles and how to apply them in their organizations. This prepares them to tackle challenges and drive continuous improvement. The interactive nature of these activities creates a dynamic learning environment that promotes engagement and knowledge retention, making the training more effective. This approach ensures that professionals have the skills to lead successful lean initiatives and get real results in various industries and roles.
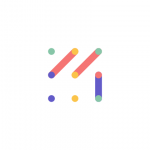
Vizologi is a revolutionary AI-generated business strategy tool that offers its users access to advanced features to create and refine start-up ideas quickly.
It generates limitless business ideas, gains insights on markets and competitors, and automates business plan creation.