The Kaizen Approach: Grow Little by Little
We often look for big leaps and instant success in our quest for personal or professional growth.
But what if the key to progress is taking small steps and making incremental improvements?
This approach is known as Kaizen. It is a Japanese philosophy that advocates for continuous, small changes leading to significant long-term development.
By focusing on gradual and sustainable progress, the Kaizen approach has proven to be an effective strategy for individuals and organizations looking to grow little by little.
Defining Kaizen: The Strategy for Incremental Improvements
The core principles of Kaizen aim to create a culture of continuous improvement within an organization. This involves all employees. Kaizen believes that every process can be improved. It encourages small, ongoing changes that can significantly improve over time. This promotes efficiency and productivity.
The PDCA Cycle consists of Plan, Do, Check, and Act. It serves as a structured model for executing Kaizen. This helps in systematically identifying opportunities for improvement, testing potential solutions, and evaluating results before implementing changes.
This approach brings a scientific and data-driven strategy to the improvement process. It ensures that changes are well-considered and effective. Implementing Kaizen can lead to increased employee engagement, streamlined processes, and a focus on quality.
However, there are also challenges such as resistance to change, the need for sustained commitment, and the risk of complacency after initial improvements.
Despite these challenges, Kaizen offers a valuable approach to continuous improvement in any organization.
How the Kaizen Philosophy Functions
The Kaizen philosophy promotes small improvements in an organization. It involves all employees and aims for continuous improvement. The principles include maintaining high standards, meticulous processes, and respecting the human factor. It also focuses on finding problems and creating solutions, and fostering a culture of continuous reflection and improvement. The PDCA (Plan-Do-Check-Act) cycle executes Kaizen by bringing a scientific approach to making improvements.
It involves planning changes, executing them, checking the results, and making them permanent. Kaizen helps organizations apply ongoing improvement systematically, leading to overall growth and development.
Exploring the Core Principles of Kaizen
Principle One: Eliminate Waste
Kaizen’s Principle One helps identify and eliminate waste in a work environment. It uses techniques like value-stream mapping to analyze the production process and find non-value-adding activities.
By eliminating activities that don’t add overall value, such as overproduction, defects, unnecessary transportation, and underutilized talent, a company can reduce waste and improve efficiency.
Examples of wasteful practices that Principle One can address include excessive inventory, waiting times between production steps, unnecessary employee motion, and overprocessing of products. For example, reducing inventory levels can free up working capital and reduce potential risks.
To continuously reduce waste, strategies like Gemba walks involve managers observing real-time operations to find inefficiencies. Visual controls, part of the 5S methodology, can help sustain improvements and prevent waste from happening again. This can include using color-coding and visual displays to make problems immediately apparent and prompt quick corrective action.
Principle Two: Standardize Tasks and Processes
Standardizing tasks and processes in a Kaizen framework means creating guidelines and best practices everyone follows. This helps work to be consistent and efficient, making it easier to find areas for improvement. For example, a manufacturing company may standardize the process for assembling a product to ensure high-quality production.
The benefits are numerous, enhancing productivity, quality, and safety. It can also lead to time and cost savings and better resource utilization.
Challenges may arise, like resistance to change from employees and difficulty enforcing standards. However, overcoming these challenges is essential for fostering an organization’s continuous improvement culture.
Principle Three: Foster a Culture of Continuous Improvement
An organization can create a culture of continuous improvement by involving employees at all levels. This means encouraging them to identify areas for improvement and implement their ideas. Clear goals, necessary resources, and training support these efforts.
Strategies like Kaizen events, regular team meetings, and performance tracking can help foster this culture. Potential obstacles may include resistance to change, lack of motivation, and insufficient support from leadership.
Open communication, incentives, and leading by example are essential to overcome these challenges. By addressing these challenges, organizations can create an environment where continuous improvement is ingrained in the company’s values and daily practices.
Principle Four: Maintain Order and Organization
Maintaining order and organization is important for the successful implementation of Kaizen. It helps employees easily identify areas for improvement and make changes effectively.
Strategies like 5S, which involves Sort, Set in order, Shine, Standardize, and Sustain, can be used to maintain order and organization in the workplace.
This ensures that the workplace is clean, organized, and efficient, supporting the principles of Kaizen. It also aligns with Kaizen’s goals by promoting continuous improvement and efficiency.
Well-organized processes make it easier to identify and address inefficiencies, leading to positive changes and improvements in the company’s operations.
These improvements ultimately enhance products, services, and overall business performance.
Principle Five: Practice Self-discipline
Incorporating self-discipline into Kaizen means consistently following continuous improvement principles. It involves eliminating waste and making small positive changes. For individuals, self-discipline means taking personal responsibility for finding improvement opportunities and seeing them through. This may involve creating and sticking to an action plan, even when faced with challenges.
Self-discipline is crucial in maintaining Kaizen principles. It helps individuals stay focused on their improvement goals, overcome obstacles, and be accountable for their progress. Organizations can support employees in developing self-discipline by providing training and resources to cultivate good habits, stay motivated, and persist in their improvement efforts.
Creating a culture that values and recognizes self-discipline reinforces its importance in continuous improvement.
The PDCA (Plan-Do-Check-Act) Cycle: A Model for Kaizen Execution
The PDCA (Plan-Do-Check-Act) cycle is a model for executing Kaizen. It provides a systematic approach to making continuous improvements. The cycle ensures that changes are thoroughly planned, executed, and evaluated before implementation.
The key components of the PDCA cycle – planning, doing, checking, and acting – align with the principles of Kaizen. They emphasize the need to analyze current processes, develop incremental improvements, test those improvements, and then implement them if proven successful.
The systematic and iterative nature of the PDCA cycle reflects the core concept of Kaizen. This concept is centered around making ongoing, positive changes that contribute to overall organizational improvement.
The Just-in-Time Inventory System and Kaizen
The Just-in-Time Inventory System cuts waste and uses inventory efficiently. It promotes continuous improvement by spotting inefficiencies and areas for improvement.
Benefits of implementing Kaizen for inventory management include less waste, better efficiency, improved quality control, and higher employee engagement. Challenges like resistance to change, extensive training, and potential disruptions may arise during implementation.
Real-world applications of Kaizen in inventory management include Gemba walks, 5S workplace organization, and visual management tools like Kanban boards. These tools help identify improvement opportunities, monitor inventory levels, and make sustainable changes in the inventory system.
Kaizen’s 5S Framework: A Systematic Blueprint
Sort (Seiri): Clearing the Work Area
Sorting (Seiri) is a crucial part of the Kaizen philosophy. Its main goal is to get rid of unnecessary items in the work area and only keep essential tools and materials. This helps create a more organized and efficient workspace. Sort (Seiri) is a key part of the 5S framework, which focuses on maintaining order and organization. It involves categorizing items, removing unnecessary ones, and assigning a place for everything to ensure easy retrieval.
Practices include regular cleaning, marking locations, and establishing clear guidelines for what should be kept in the workspace. These principles and practices effectively help implement Sort (Seiri) in the workplace, fostering a culture of continuous improvement and prioritization of efficiency and productivity.
Set in Order (Seiton): Organizing the Work Area
“Set in Order (Seiton)” organizes the work area. It helps streamline processes, reduce waste, and increase efficiency. Assigning a specific place for each tool or supply reduces time spent searching. This increases productivity. Implementing “Set in Order (Seiton)” as part of the 5S Framework improves safety and accessibility to tools and materials and creates a cleaner work environment.
It fosters a culture of continuous improvement within an organization by instilling discipline, encouraging ownership of workspaces, and promoting pride and responsibility. This encourages employees to identify areas for improvement, find solutions collaboratively, and contribute to the organization’s success.
Shine (Seiso): Cleaning the Work Area
Shine (Seiso) helps maintain order and organization in the work area. It focuses on cleanliness and visual management. Regular cleaning and maintenance ensure everything is in its rightful place and easily accessible. This creates a more efficient work environment.
Integrating Shine (Seiso) into the 5S Framework is significant. It ensures that cleanliness and maintenance become part of the workplace culture. This makes it an essential part of a company’s standard processes.
Practicing Shine (Seiso) aligns with the principle of fostering a culture of continuous improvement in the workplace. It instills the mindset that everything, including the cleanliness and organization of work areas, can be improved. This contributes to an overall culture of ongoing positive changes and supports the Kaizen philosophy of continuous improvement.
Standardize (Seiketsu): Standardizing Procedures
Companies can standardize procedures and tasks by creating detailed work instructions and visual aids, like flowcharts. This helps employees understand how to complete tasks correctly. Training sessions and regular audits ensure that standardized procedures are consistently followed. Leaders should monitor and support employees to maintain standards. Ongoing training and communication through team meetings and visual displays help employees understand and adhere to standardized procedures.
Involving employees in developing standardized procedures increases their commitment to following the standards, creating a collaborative work environment aligned with the Kaizen approach.
Sustain (Shitsuke): Upholding Changes Made
Organizations can maintain and support changes with the Kaizen philosophy by involving employees at all levels. This involves creating a culture of continuous improvement and regularly engaging employees. One strategy is using Kaizen events following a PDCA cycle to ensure long-term improvement. These events bring a scientific approach and develop a culture of ongoing improvement.
Self-discipline is essential in upholding Kaizen changes, as employees are expected to follow standardized work and actively participate. This ensures consistent application of changes and deeply ingrains the Kaizen philosophy in the organization’s culture.
Assessing the Benefits and Challenges of Kaizen
Improved Efficiency and Reduced Wastage
The organization implemented Kaizen to improve efficiency and reduce wastage.
Employees at all levels were involved in this continuous improvement process.
Specific changes were made to standardize tasks and processes, with a focus on eliminating waste and improving efficiency.
Clear standards and expectations were set for each task.
Bottlenecks and inefficiencies in the workflow were identified and eliminated.
The organization fostered a culture of continuous improvement, encouraging employees to contribute ideas and solutions.
Regular training and support were provided to keep the workforce’s skills current and relevant.
This approach successfully reduced wastage and increased efficiency in the organization.
Enhanced Employee Morale and Engagement
Kaizen empowers employees to improve their workplace. It involves actively involving employees at all levels to identify areas for improvement. This approach enhances employee morale and engagement by creating a sense of ownership and involvement. It can lead to increased job satisfaction and commitment. Implementing Kaizen requires commitment and sustained effort, and the benefits may take time.
Organizations must use tools like PDCA cycles, standardized work, and Kaizen events to succeed. These methods enable employees to identify, plan, and implement improvements, fostering a culture of continuous improvement.
Potential for Overemphasis on Incremental Change
Focusing on small changes in a company may cause them to miss out on bigger, transformative improvements. It could lead to satisfaction with small changes and a lack of pursuit of more significant advancements. Emphasizing only small enhancements could make it harder for the organization to adapt to big shifts in the market, making it less competitive and resistant to change.
A solely incremental approach could cause organizations to miss out on opportunities for growth and innovation. This is why some companies, like Toyota, have successfully used Kaizen alongside other approaches to keep growing and innovating.
Risk of Implementation Fatigue
Continuous improvement can contribute to implementation fatigue. The need for ongoing change can lead to exhaustion and decreased employee morale. Resistance from team members can also occur due to the frequency of changes. Organizations can establish clear communication and a supportive work culture to prevent implementation fatigue. Providing training and resources to employees is crucial for their readiness and confidence in the improvement process.
Allowing for breaks between improvement cycles can help prevent burnout and maintain focus on progress.
Kaizen in Action: Real-World Applications
Real-world applications of Kaizen can be seen in various industries: manufacturing, healthcare, education, and technology. In manufacturing, companies use Kaizen to make small but impactful changes to their production processes, resulting in increased efficiency and reduced waste. In healthcare, Kaizen is applied to continuously improve patient care and safety by identifying and implementing improvements in workflow and processes.
Companies like Toyota involve employees at all levels and encourage suggestions for improvements, creating a culture of ongoing improvement. This has significantly improved quality, productivity, and employee morale. Other organizations use Kaizen events to kick-start improvement efforts and achieve targeted goals through the PDCA cycle.
Challenges and barriers in applying Kaizen include resistance to change, lack of employee engagement, and the need for sustained leadership commitment. Organizations may also struggle with effectively measuring the impact of Kaizen initiatives and ensuring that improvements are sustained over time. Overcoming these challenges requires a dedicated effort and a commitment to continuous improvement at all levels of the organization.
Essential Tools and Techniques for Kaizen Implementation
Kaizen is based on the idea that everything can be improved. It focuses on making small changes, reducing waste, standardizing work, and involving all employees in the process. These principles aim to create a culture of continuous improvement within an organization.
The PDCA (Plan-Do-Check-Act) Cycle is a systematic approach to Kaizen. It involves planning the improvement, implementing the plan, checking the results, and acting on those results. This cycle ensures that changes are made structured and effectively, leading to sustainable positive outcomes.
The 5S Framework, which stands for Sort, Set in Order, Shine, Standardize, and Sustain, provides a structured blueprint for Kaizen implementation. It focuses on organizing the work environment, maintaining cleanliness, and standardizing procedures. This framework creates a visual workplace and sets the stage for ongoing improvement.
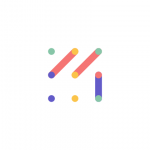
Vizologi is a revolutionary AI-generated business strategy tool that offers its users access to advanced features to create and refine start-up ideas quickly.
It generates limitless business ideas, gains insights on markets and competitors, and automates business plan creation.