Kaizen Assessment: Measure and Learn
Kaizen means “change for the better” in Japanese. It’s a method for continuous improvement at work. A critical part of Kaizen is checking progress and learning from the results. This means measuring how well changes work and using that information to improve things.
In this article, we’ll discuss why Kaizen assessment is essential and how it can make organizations better in the long term.
Understanding Kaizen: An Overview
Kaizen’s philosophy is based on continuous improvement through small, ongoing positive changes. Instead of top-down or radical transformations, it focuses on cooperation, commitment, and gradual changes. The Plan-Do-Check-Act (PDCA) cycle is a critical tool for implementing the Kaizen methodology. It involves planning changes, carrying them out, checking the results, and then acting to standardize the new process.
Diverse forms of Kaizen applications exist, such as value stream mapping and Total Quality Management, in various industries and areas of business. The Kaizen 5S framework is another example of improving workplace efficiency and effectiveness. Other examples include Kaizen events, such as individual-point and group-oriented organizational improvements. All of these aim to foster continuous improvement and innovation.
Core Tenets of Kaizen Philosophy
Principle 1: Seiri, or Sort
The principle of Seiri, or Sort, in the Kaizen philosophy, is about getting rid of unnecessary items and organizing necessary ones. It means separating essential from non-essential items to save time and create more space. This principle can be used with sorting tools like red-tagging, cleaning, and removing clutter. Seiri helps eliminate waste and improve efficiency, contributing to continuous improvement in an organization.
In real-world applications, companies have used Seiri to reduce inventory, save costs, increase productivity, and improve workplace safety.
Principle 2: Seiton, or Systematize
The Seiton principle, or Systematize, is fundamental in the Kaizen philosophy. It focuses on organizing the workplace to support continuous improvement efforts.
By using Seiton, companies can efficiently arrange tools, equipment, and materials. This helps employees find what they need easily and reduces wasted time and effort.
The principle contributes to the overall goal of improving workplace efficiency. It creates a well-organized environment that promotes productivity and streamlines processes.
Practical examples of using Seiton in business include color-coding work areas, visual management boards to display workflow and inventory information, and establishing a clear labeling and storage system.
These examples show how Seiton can be applied effectively to ensure that everything in the workplace has its designated place, leading to a more efficient and productive work environment.
Principle 3: Seiso, or Shine
The principle of Seiso, or Shine, is fundamental in the 5S system in Kaizen. It focuses on cleanliness and orderliness to keep the workplace organized and clutter-free. This helps create a safer, more efficient work environment, crucial for successfully implementing Kaizen principles. Strategies for Seiso include regular cleaning schedules, visual management tools, and employee training to highlight the importance of workplace cleanliness.
Principle 4: Seiketsu, or Standardize
Seiketsu, also known as Standardize, is a principle in Kaizen philosophy. It is important for improving processes and reducing variation in work. This involves creating standardized work procedures and practices to ensure consistency and efficiency.
By implementing visual management tools, checklists, and standardized work instructions, organizations can maintain consistent practices and reduce the risk of errors or variations in output.
Seiketsu contributes to overall efficiency and quality improvement within an organization. It promotes a standardized work environment where employees can identify abnormalities and make necessary improvements.
This principle involves continuously refining standardized processes to ensure optimal efficiency and quality. For example, the use of standardized checklists and visual cues in a manufacturing setting can help employees identify and rectify defects, ultimately improving overall quality and productivity.
Principle 5: Shitsuke, or Sustain
The Kaizen methodology has a key principle called “Shitsuke,” or sustain. This principle focuses on ensuring that the improvements made last for a long time. To achieve this, organizations need to set up transparent systems and processes to keep track of the changes from Kaizen. This involves regular follow-up assessments, collecting data, and getting ongoing employee feedback to see how the improvements work.
Using visual controls, like graphs, charts, and performance boards, can help maintain the discipline needed to implement changes. These visual aids give real-time information on how improvements are progressing and keep employees involved and committed. Also, creating a culture of ongoing improvement within the organization is crucial to sustaining Kaizen initiatives.
This can be done by giving regular training and education on Kaizen principles, forming cross-functional Kaizen teams, and acknowledging and rewarding employees for their contributions to the improvement process.
Implementing the Kaizen Methodology
Plan-Do-Check-Act Cycle: A Framework for Improvement
The Plan-Do-Check-Act cycle is part of the Kaizen methodology. It helps organizations improve continually. The cycle involves planning a change, testing it on a small scale, analyzing the effects, and standardizing successful changes. This cycle is important for assessing the impact of changes and is a vital tool for driving improvement. By repeating the cycle, the Kaizen methodology can be successfully implemented.
The cycle helps teams plan, test small changes, and rigorously evaluate each one before deciding on standardization. This leads to sustained improvement and a continuous enhancement culture within the organization.
Diverse Forms of Kaizen Applications
Single-Point Kaizen
Single-Point Kaizen is about making small, gradual improvements by focusing on one specific aspect of a process. It’s different from bigger approaches to Kaizen that look at the whole system.
With Single-Point Kaizen, organizations can make manageable changes without needing big overhauls. These changes can lead to better efficiency, less waste, and higher quality.
Organizations can use tools like value stream mapping and Total Quality Management to find and prioritize areas for improvement. These tools help visualize and analyze specific processes. Then, organizations can prioritize areas based on their potential impact, feasibility, and available resources.
Kaizen Blitz for Rapid Changes
A Kaizen Blitz is a method for making fast changes in a workplace. It involves short-term projects that last 3-5 days. A team from different departments works intensely to find and fix specific areas for improvement.
For a successful Kaizen Blitz, there should be clear goals, team empowerment, data-driven decisions, and well-planned action to implement changes.
Unlike traditional Kaizen, which focuses on gradual improvements, Kaizen Blitz is all about speed and instant changes. It helps organizations quickly solve important problems and see real results quickly. It’s a great tool for continuous improvement in a fast-paced environment.
Kaizen Teian: The Suggestion System
Kaizen Teian, the suggestion system, is part of the Kaizen methodology. It encourages employees to share their ideas for improving the organization.
This system supports ongoing improvement by creating a culture of continuous improvement and innovation. Employees can identify areas for improvement and offer practical solutions, promoting collaboration and engagement.
To implement Kaizen Teian, it is important to create a comfortable environment for sharing ideas. Employees also need proper training on how to submit suggestions. Establishing a transparent process for reviewing and implementing changes is crucial.
Recognizing and rewarding employees for their contributions can motivate them to participate in the suggestion system. By integrating Kaizen Teian into the organizational culture, companies can use their employees’ collective intelligence to drive ongoing improvements.
The 5S System in Kaizen
First S: Sort (Seiri)
The First S in the 5S System of Kaizen is Sort (Seiri). Its purpose is to eliminate unnecessary items from the workplace, creating a well-organized and efficient environment.
By sorting through items and removing non-essential ones, it reduces clutter, improves workflow, and increases productivity. This contributes to the overall goal of continual improvement by creating a more focused and streamlined work environment.
Implementing the First S: Sort (Seiri) principle involves:
- Identifying necessary and unnecessary items.
- Removing unnecessary items.
- Organizing the remaining items.
- Setting standards for maintaining an organized workplace
This process helps achieve the goals of Kaizen by promoting workplace efficiency, safety, and discipline.
Second S: Set in Order (Seiton)
Set in Order (Seiton) in the context of Kaizen means organizing and arranging items in the workplace to boost efficiency and productivity. This involves giving specific places for tools, materials, and equipment and using clear visual indicators for item placement. Seiton contributes to Kaizen’s goals by creating an organized work environment that reduces waste and motion and enhances safety. Examples include designated storage areas, labeling and color-coding inventory, and ergonomic workstations.
An organized workspace improves operations, boosts morale, makes inventory monitoring easier, and increases productivity and customer satisfaction.
Third S: Shine (Seiso)
The “Shine (Seiso)” principle is very important in the 5S system in Kaizen. It focuses on cleanliness and proactive maintenance to make the workplace organized, visually appealing, and efficient. This leads to improved safety, less waste, and higher productivity.
To implement “Shine (Seiso),” specific practices include regular cleaning of workstations, equipment, and tools and creating and following maintenance schedules to prevent breakdowns and defects.
“Shine (Seiso)” is part of the continual improvement philosophy in Kaizen. It promotes discipline, order, and attention to detail. It emphasizes that cleanliness and regular maintenance are ongoing habits contributing to the organization’s overall success.
Fourth S: Standardize (Seiketsu)
Standardization methods in the Kaizen methodology are part of the “Fourth S: Standardize (Seiketsu)”. These methods involve creating consistent processes and procedures for all members of an organization. This includes making detailed work instructions, checklists, and visual aids, and regularly reviewing and updating these standards. Standardization also involves training employees to follow the established procedures and sharing best practices among all team members.
Standardization is important for the success of continuous improvement efforts within an organization. It promotes consistency, reliability, and efficiency in operations. When processes and procedures are standardized, it becomes easier to identify variations, inefficiencies, and defects, which can be addressed through further improvement activities. Standardized work also provides a stable foundation for waste reduction, quality enhancement, and empowering employees to contribute to improving their work environment.
It also sets a benchmark for evaluating performance and measuring progress toward achieving the organization’s objectives.
Fifth S: Sustain (Shitsuke)
Sustain (Shitsuke) is crucial in Kaizen. It means ensuring that the small changes made continuously are maintained for a long time.
This can be done by regularly training and educating employees to ensure that new standards and processes are always followed. For example, in a manufacturing setting, regular audits and tools like color-coded floor markings and signs can help maintain efficiency and safety improvements.
Leadership also plays a role in keeping up with Kaizen’s improvements. It involves creating a culture of continually improving, where managers and supervisors actively support and recognize employees’ efforts. For instance, leaders can do Gemba walks to engage with frontline employees and help them improve.
Employee engagement is another important part of maintaining Kaizen improvements. Organizations can do this by involving employees in the process, encouraging them to give feedback, and recognizing and rewarding their contributions. For example, they can use suggestion programs or idea boards for employees to share improvement ideas and be recognized for them.
By using these strategies and techniques, organizations can ensure that the improvements made through Kaizen are not only maintained but also improved over time.
Evaluating Kaizen: Pros and Cons
Benefit of Continual Improvements
Continual improvements in the context of Kaizen methodology offer several benefits to organizations. Companies can significantly improve processes, products, and services by making small, ongoing positive changes. These improvements can increase efficiency, reduce waste, and higher quality output.
Additionally, continual improvement contributes to the overall success of Kaizen implementation by fostering a culture of cooperation and commitment among employees. It encourages everyone in the organization to actively participate in identifying and implementing improvements, resulting in a more engaged and empowered workforce.
Furthermore, organizations can leverage continual improvements to drive positive change and growth using tools like value stream mapping and Total Quality Management. These methodologies enable companies to identify areas for improvement and implement changes systematically, leading to sustainable growth and continuous development.
Cultural Change as a Challenge
Implementing the Kaizen methodology can be challenging. Organizations may resist cultural change. Employees who are used to traditional top-down transformations may be skeptical and reluctant. Cultural change can also lead to resistance from middle management, lack of employee buy-in, and fear of the unknown.
To address these challenges, organizations can focus on providing extensive training and support to employees at all levels. Creating a culture of collaboration and open communication is vital. Demonstrating the benefits of Kaizen through success stories and practical examples can also gain the support needed for a successful transition.
By integrating Kaizen into the organizational culture, sustainable improvements can be achieved in various industries and business areas.
Kaizen in Action: Real-world Successes
Implementing Kaizen principles has led to significant improvements for various organizations. For instance, a manufacturing company used Kaizen to reduce waste and boost productivity. Kaizen’s strategies streamlined workflows in healthcare, leading to better patient care and shorter wait times. These examples show how versatile and practical Kaizen is across different industries.
Organizations have successfully used the Kaizen approach by fostering a culture of continuous improvement and empowering employees to identify opportunities. Regular events and workshops engage employees in making small, incremental changes that collectively enhance processes, quality, and overall performance.
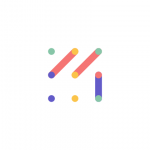
Vizologi is a revolutionary AI-generated business strategy tool that offers its users access to advanced features to create and refine start-up ideas quickly.
It generates limitless business ideas, gains insights on markets and competitors, and automates business plan creation.