Kaizen for Business: Small Steps to Success
Success in business doesn’t always come from big gestures. Small, continuous improvements can make a difference. Kaizen, a Japanese concept, focuses on making small, incremental changes to achieve big results.
In this article, we’ll explore how Kaizen can benefit businesses of all sizes and how its principles can be applied to drive success in the real world. Let’s take a closer look at how small steps can lead to big achievements in the business world.
The Origins and Evolution of Kaizen
Kaizen originated in Japan as a business philosophy for continuous improvement. It has evolved over time to include various principles and practices to make work environments more efficient. Today, Kaizen is a global phenomenon, with organizations worldwide adopting its principles for operational excellence.
Kaizen has been applied successfully in industries such as manufacturing, healthcare, and services. Companies like Toyota and Ford Motor Company have used Kaizen to improve production processes and enhance efficiency. Service-oriented businesses have also embraced Kaizen to streamline workflows and achieve optimal resource utilization.
In comparison to other improvement frameworks like agile, lean IT, and Six Sigma, Kaizen stands out for its focus on employee engagement, waste elimination, and continuous improvement. Unlike other methodologies, Kaizen involves all employees and aims for sustainable improvements over time, making it a practical and effective framework for achieving long-term success.
Core Principles of Kaizen
Principle 1: Continuous Improvement
Organizations can improve by involving employees, promoting teamwork, and using tools like 5S, JIT, Kanban, the five whys, and value stream mapping. By encouraging all employees to find opportunities for improvement, organizations can create a culture of continuous improvement.
Maintaining a culture of continuous improvement involves embracing mistakes for growth, relying on employee feedback, and using the PDCA cycle for sustained improvements. Organizations can also minimize waste and boost efficiency by employing just-in-time inventory and lean production methods.
Kaizen principles can be applied to production, logistics, and customer service by focusing on waste elimination, good housekeeping, and standardization. By using the kaizen methodology and empowering people to make changes, organizations can improve various aspects of their operations.
Principle 2: Good Process, Good Results
Implementing good process in Kaizen leads to good results. It focuses on continuous improvement and increasing productivity. The core principles of Kaizen include empowering people, eliminating waste, and standardizing work. These principles highlight the importance of efficient equipment use, waste elimination, and quality control.
Principle 2: Good Process, Good Results is important in continuous improvement and organizational success. It enables companies to achieve waste elimination, good housekeeping, and standardization. By following this principle, companies can streamline and make their processes efficient, leading to improved productivity and overall success.
Principle 3: Go See for Yourself
The principle of “Go See for Yourself” in Kaizen aligns with the concept of continuous improvement by emphasizing the importance of firsthand observation and understanding of processes and operations. By physically going to the actual place of work, employees can identify inefficiencies, waste, and areas for improvement, contributing to the overall goal of making the work environment more efficient.
This firsthand observation allows for a deeper understanding of the work processes, enabling employees to make informed decisions and implement changes effectively.
Personally observing processes and operations in the context of Kaizen’s “Go See for Yourself” principle offers benefits such as the opportunity to identify and eliminate waste, improve quality, and enhance productivity. It also fosters better communication and collaboration among employees, as they work together to identify improvement opportunities and implement changes. Furthermore, it promotes a culture of ongoing learning and development, as employees are empowered to take ownership of their work environment and contribute to continuous improvement efforts.
The “Go See for Yourself” principle contributes to employee empowerment and engagement in the implementation of Kaizen by valuing their firsthand input and experiences. It encourages employees at all levels to actively participate in the improvement process and share their insights, ideas, and concerns. This involvement not only leads to better problem-solving and decision-making but also instills a sense of ownership and commitment to the continuous improvement efforts, ultimately creating a more engaged and empowered workforce.
Principle 4: Empowering Employees
Empowering employees is important when implementing Kaizen. It allows for more involvement and commitment from staff. This leads to valuable insights and suggestions for improvement, boosting productivity and efficiency. Strategies for empowering employees in Kaizen include open communication, involving them in decision-making, promoting ownership, and providing skill development. These practices align with the goal of continuous improvement, ensuring all employees are engaged in the process.
Empowered employees take initiative, collaborate effectively, and contribute to the ongoing success of the organization, leading to sustained progress and positive outcomes.
Principle 5: Visual Management
Visual management is very important in the context of Kaizen. It helps communicate information, track progress, and identify issues in the workplace.
Using tools like color-coded boards, charts, and graphs, employees can easily see project status, productivity levels, and problem areas. This supports transparency and empowers people to make informed decisions and take immediate actions.
In continuous improvement, visual management enhances communication and workflow. Tools like Andon systems signal when an issue arises, and Kanban cards monitor work in progress. Visual cues help identify bottlenecks, standardize work processes, and maintain production flow.
Visual management also promotes good housekeeping and standardization, aligning with Kaizen’s principles for waste elimination and creating an efficient work environment.
Implementing Kaizen: The PDCA Cycle
Phase 1: Plan
Phase 1 of the Kaizen process involves specific goals like waste elimination, good housekeeping, and standardization. The organization should align the planning phase with Kaizen’s principles by empowering employees and encouraging continuous improvement. Strategies and tools used in the planning phase include value stream mapping, 5S, the five whys, and follow-up events. These methods help in identifying solutions and making the work environment more efficient, based on the Kaizen philosophy.
Phase 2: Do
During “Phase 2: Do” of the PDCA Cycle, the focus is on implementing the improvement plan. This involves carrying out the agreed-upon changes, collecting relevant data, and closely monitoring the process for any issues. By taking action in this phase, the organization can observe the changes and make adjustments as needed.
Implementing “Phase 2: Do” aligns with Kaizen principles, emphasizing continuous improvement and involving employees in making necessary changes. It empowers employees to take ownership of improvements and contributes to enhancing productivity and efficiency.
Tactical tools like the Five Whys and Kanban Boards are essential in “Phase 2: Do” of Kaizen implementation. The Five Whys technique helps identify the root cause of a problem, while Kanban Boards promote workflow efficiency and identify potential bottlenecks. Both tools support the successful implementation of improvement initiatives during the “Do” phase of the PDCA Cycle.
Phase 3: Check
Phase 3: Check includes different methods to measure how well the changes in the kaizen process are working. It involves looking at key performance indicators, gathering data on the improved processes, and comparing it to the initial benchmarks. Using tools like control charts and histograms, organizations can see if they’ve made the improvements they wanted.
During Phase 3: Check, methods like value stream mapping and follow-up events are used to check how things are going with the changes made in the implementation phase. Value stream mapping helps visualize the whole process and find places where more improvements can be made. Follow-up events make sure the changes keep working over time and that any problems are dealt with quickly.
Phase 3: Check helps the continuous improvement process in Kaizen keep going. By regularly checking on the progress and impact of the improvements, organizations can find more ways to make things better and make sure that continuous improvement stays a big part of their business. This helps create a culture of always getting better and changing within the organization.
Phase 4: Act
To make sure that the improvements identified in Phase 4 are implemented well, Kaizen business principles focus on involving employees, empowering them, and using tools like the PDCA cycle and just-in-time inventory strategy. Involving all employees in the improvement process and giving them the necessary training and resources helps organizations ensure that the changes are effectively carried out.
Standardization and good housekeeping practices can also be used to maintain the improvements over time.
To make sure that the changes made in Phase 4 last over time, organizations can use strategies like follow-up events and employee feedback mechanisms. By continuously monitoring and adjusting processes based on feedback, the organization can ensure the changes last. Embracing mistakes as opportunities for growth is also an important Kaizen principle that helps the improvements last.
To monitor and evaluate the impact of the changes made in Phase 4, the organization can use tools like value stream mapping, the five whys, and follow-up events. These strategies help identify the root causes of problems and continuously evaluate the impact of the changes. Measuring key performance indicators and involving employees in the monitoring process helps the organization effectively evaluate the impact of the changes made in Phase 4.
Kaizen’s Tactical Tools
Tool 1: The Five Whys
The Five Whys tool helps find the root cause of a problem. It does this by asking “why” multiple times. For instance, if a machine in a factory stops working, asking why it stopped leads to asking why a specific part failed, and so on, until the root cause is found.
To use the Five Whys for continuous improvement, follow key steps. These include asking “why” multiple times to understand the deeper reasons for a problem, involving all employees, and taking action on the root causes. For example, a company facing a sales decline can use the Five Whys to explore the reasons and implement solutions.
The Five Whys method supports the Kaizen philosophy of continuous improvement. It does this by encouraging thorough investigation into the reasons behind problems. It promotes open communication and problem-solving, aligning with Kaizen principles. Toyota and Ford Motor Company use the Five Whys to drive improvements and create a successful work environment.
Tool 2: Kanban Boards
Kanban boards are a visual management tool in Kaizen. They provide a clear view of the workflow. Team members can track stages, identify bottlenecks, and monitor progress. This visual representation fosters better communication and collaboration, leading to improved efficiency and productivity.
Using Kanban boards in Kaizen processes offers many benefits. They help streamline production, manage inventory, and reduce waste. Organizations can achieve a just-in-time inventory strategy, minimizing overproduction and excess inventory. This saves costs and improves product and service quality.
Kanban boards align with continuous improvement and good process in Kaizen. They foster transparency, waste elimination, and standardization. The visual representation encourages teams to identify areas for improvement, make necessary adjustments, and strive for excellence. This aligns with Kaizen’s focus on eliminating waste, improving quality, and maintaining a standard workflow.
Tool 3: Root Cause Analysis
Root Cause Analysis is a process used in Kaizen. It helps identify underlying issues in a business process. The process involves systematically investigating and diagnosing the root cause of a problem. This is done to prevent it from happening again.
Tools such as the five whys and value stream mapping are used in this process. They help uncover the fundamental reasons behind inefficiencies, errors, or defects in a process. This is instead of just addressing the symptoms.
For example, a manufacturing company experiencing frequent production delays may use root cause analysis to discover that the delays are due to suboptimal equipment maintenance procedures or inefficient material flow. This leads to excess inventory and process bottlenecks.
Root Cause Analysis is important in continuous improvement in Kaizen. It provides a structured method for identifying and resolving core issues. This approach aligns with Kaizen’s principle of waste elimination and standardization. It also promotes employee empowerment and transparency.
By addressing the root cause of problems, businesses can achieve sustainable improvements in quality, productivity, and customer satisfaction. This is in line with the overall goals of Kaizen.
Advantages of Kaizen in Today’s Businesses
Increase in Productivity
Implementing Kaizen contributes to increasing productivity. It creates an environment focusing on continuous improvement. By engaging all employees and striving for efficiency, Kaizen leads to streamlined processes. It also results in waste elimination and standardized work.
The advantages of Kaizen in driving continued improvement and productivity are evident. It focuses on waste elimination, good housekeeping, and standardization. Kaizen fosters employee engagement and teamwork to create a successful work environment, enhancing productivity further.
Compared to other improvement frameworks, Kaizen stands out. It drives productivity and process enhancement by incorporating principles such as knowing the customer, empowering people, and transparency. It also utilizes tools like 5S, JIT, Kanban, the five whys, and value stream mapping to sustain improvements and minimize waste. This approach sets Kaizen apart. It is effective in driving productivity and process enhancement.
Enhanced Employee Engagement
Empower employees and enhance engagement by creating a culture of transparency and open communication. Encourage them to voice ideas and concerns to foster ownership and participation in the improvement process. Provide skill development and recognize contributions to motivate engagement.
Implement strategies like regular training and coaching sessions, encouraging collaboration and teamwork, setting clear goals, and providing performance feedback. These approaches promote continuous improvement and development among employees.
Use visual management techniques like Kanban boards, process flow maps, and performance scorecards to engage employees in the Kaizen process. These tools provide real-time information and feedback, helping employees understand their roles and identify improvement opportunities.
Continuous Process Improvement
Continuous process improvement, like the Kaizen method, can boost productivity and employee engagement. It focuses on efficiency and empowering employees. Practices like just-in-time delivery, waste elimination, and standardized work help organizations streamline processes. This creates an environment where employees actively make improvements, leading to higher productivity and improved morale.
Toyota and Ford Motor Company are practical examples of implementing continuous process improvement. They’ve used the Kaizen method to streamline production processes, reduce waste, and increase efficiency. Tools like 5S, JIT, Kanban, and value stream mapping sustain these improvements and foster a culture of continuous improvement.
Compared to other improvement frameworks like agile, lean IT, and Six Sigma, Kaizen stands out in effectiveness and practicality. Its emphasis on employee engagement and teamwork sets it apart. The focus on waste elimination, standardization, and continuous feedback makes it a powerful method for driving positive change within organizations.
Practical Examples of Kaizen in Industry
Kaizen has made big improvements in different industries.
For example, the automotive industry has seen better production processes with kaizen. Employees are more involved in making things better by using principles like just-in-time delivery and standardized work. This has led to better teamwork and engagement, bringing good results. Visual management techniques, like value stream mapping and follow-up events, have helped with problem-solving at work. These techniques have made work more efficient and reduced waste. In all, applying Kaizen principles has really changed how things work, bringing real improvements in many industries.
Tying Kaizen to Just-in-Time Inventory Strategies
Kaizen principles, when integrated into Just-in-Time inventory strategies, can improve efficiency and reduce waste. This is achieved by focusing on continuous improvement and waste reduction.
Kaizen principles align with the goals of a Just-in-Time inventory system, as they strive for improvement in productivity and a more efficient work environment. This can be done through tools like value stream mapping to identify and eliminate waste, 5S for a clean and organized work environment, and follow-up events to sustain improvements.
By implementing Kaizen, employees are empowered, transparency is encouraged, and mistakes are seen as opportunities for growth. This promotes employee engagement and teamwork, resulting in a successful and efficient work environment.
Real-World Kaizen: Aligning Theory with Practice
Organizations can align Kaizen principles with practical applications by fostering a workplace culture focused on continuous improvement. This involves engaging all employees in identifying and implementing small, incremental changes to streamline processes, eliminate waste, and enhance productivity.
For example, Toyota’s “kaizen blitz” process encourages rapid problem-solving and idea implementation, enabling the company to apply Kaizen principles to real-world challenges in production and operations.
Implementing Kaizen’s tactical tools in today’s businesses presents both challenges and opportunities. One challenge is ensuring that employees understand and embrace the concept of continuous improvement, as it requires a shift in mindset and daily practices. However, the opportunity lies in leveraging tools such as 5S, JIT, Kanban, and value stream mapping to optimize workflows and minimize waste, leading to increased efficiency and cost savings.
Compared to other improvement frameworks, Kaizen’s practicality and effectiveness in real-world scenarios shine through its focus on employee engagement and teamwork. While Lean IT, Six Sigma, and Agile also aim for process improvement, Kaizen’s emphasis on incremental changes and employee empowerment sets it apart. This makes it a highly adaptable framework for organizations seeking sustainable growth and efficiency.
Comparing Kaizen to Other Improvement Frameworks
Kaizen is different from other improvement frameworks. It focuses on employee engagement, waste elimination, just-in-time inventory, and knowing the customer. Its PDCA cycle emphasizes continuous improvement through planning, doing, checking, and acting. This systematic approach allows for ongoing adjustments. Kaizen uses tools like 5S, JIT, Kanban, the five whys, value stream mapping, and follow-up events to sustain improvements.
This sets it apart with a comprehensive set of strategies focused on efficiency, waste reduction, and employee empowerment.
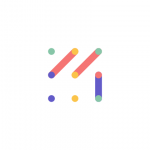
Vizologi is a revolutionary AI-generated business strategy tool that offers its users access to advanced features to create and refine start-up ideas quickly.
It generates limitless business ideas, gains insights on markets and competitors, and automates business plan creation.