Lean Methodology: Diverse Applications
Lean methodology is popular in many industries, such as manufacturing and healthcare. It aims to streamline processes and reduce waste, boosting efficiency and productivity. Its versatility and adaptability have led to diverse applications across different settings. This article will explore how lean methodology is used and its impact on today’s business world.
Understanding Lean Methodology
Lean methodology focuses on core principles such as waste elimination, customer-centric approach, and value stream mapping. All of these principles contribute to improving organizational processes. By eliminating waste, companies can optimize their resources and improve operational efficiency.
Tools such as 5S, Kaizen, and Value Stream Mapping help in this optimization by organizing workspaces, encouraging continuous improvement, and identifying areas of waste. These tools play a crucial role in reducing unnecessary steps and streamlining processes, ultimately leading to cost reduction and increased productivity.
Implementing lean practices offers several advantages, including improved quality, reduced lead times, and increased customer satisfaction. Lean training plays a key role in helping employees understand and effectively implement these practices, impacting organizational performance. By equipping employees with the necessary skills and knowledge, organizations can enhance their operational efficiency and create a culture of continuous improvement.
As a result, lean training contributes to overall business success and growth.
The Core Principles of Lean Management
Identifying Customer Value
Organizations have tools like value stream mapping and overall equipment effectiveness (OEE) to measure customer value. These methods find inefficiencies and waste in processes, which can be improved to increase customer value. Lean methodology, a customer-centric approach, and waste elimination help organizations determine what’s valuable to customers.
Aligning processes with customer needs and using tools like Just-In-Time, bottleneck analysis, and error proofing improves operational efficiency and customer satisfaction. By integrating customer value into processes, organizations deliver products and services that meet customer needs, driving customer loyalty and brand value.
Mapping the Value Stream
Value stream mapping helps organizations understand how materials and information flow from the supplier to the customer. It uses graphics to show the production process, which helps to see the current state and find ways to improve it.
The key steps are gathering process information, creating a visual map, and identifying non-value-added activities. Once the map is made, it helps create a smoother workflow and pull-based systems within the organization. It also highlights areas of waste and inefficiency for improvement.
This can reduce lead times and improve overall productivity. For instance, a manufacturing company could use value stream mapping to find production bottlenecks, and then make changes to respond to customer demand, ultimately becoming more efficient and saving costs.
Creating Seamless Workflow
Organizations can make their processes more efficient by using lean management principles. This means finding and getting rid of anything that doesn’t add value to the workflow. Strategies like value stream mapping, just-in-time production, and overall equipment effectiveness can help find and solve inefficiencies. Lean methodology is all about focusing on the customer and cutting out waste.
By using lean tools and principles, organizations can provide more value to customers while using fewer resources. Professionals can learn how to use lean principles through quality management certification courses and help their organization work more smoothly.
Establishing Pull-Based Systems
Transitioning from traditional push-based systems to pull-based systems in an organization is important. It involves understanding customer needs and preferences, which then guides production schedules and inventory levels.
By using a pull-based system, organizations can reduce overproduction, lower inventory costs, and respond better to changes in customer demand.
Moving to a pull-based system needs careful planning and a change in mindset. This includes streamlining production processes, implementing just-in-time inventory management, and improving communication with suppliers and customers. Continuous improvement and clear performance metrics are also crucial.
Pursuing Perpetual Improvement
Organizations can improve their processes and systems by using Lean methodology tools and principles. Techniques like Value Stream Mapping and Plan-Do-Check-Act (PDCA) help to identify and eliminate inefficiencies and waste. It’s important to foster adaptability and flexibility among the workforce to maintain a culture of continuous improvement. Leadership sets the tone for the organization’s commitment to continuous improvement.
Leaders need to provide resources, support, and encouragement to empower employees to make meaningful contributions. By embodying Lean principles and championing a culture of continuous improvement, leaders can motivate and inspire their teams to pursue improvement relentlessly.
Lean Tools for Optimizing Processes
Eliminating Waste with 5S
The 5S methodology is a great way to make workplaces more efficient. It has five steps: Sort, Set in Order, Shine, Standardize, and Sustain.
- “Sort” helps remove unnecessary items, making processes smoother.
- “Set in Order” arranges necessary items efficiently, saving time and making processes clear.
- “Shine” ensures workspaces are clean and safe, enhancing the work environment.
- “Standardize” and “Sustain” establish best practices and maintain improvements, leading to ongoing efficiency.
Enhancing Efficiency through Kaizen
The principles of Kaizen focus on continuous improvement. They enhance efficiency within an organization by encouraging constant evaluation and evolution. Empowering employees to suggest small changes to their work processes leads to significant improvements in productivity over time. Strategies like daily meetings for discussing improvements and setting achievable goals for small process changes can integrate Kaizen into the workflow.
This fosters a culture of responsibility and innovation among staff, resulting in consistent process optimization. Kaizen leads to increased productivity and overall organizational performance by valuing employee input. It commits to frequent, small improvements over time, resulting in a work culture attentive to waste elimination, customer value, and long-term growth.
Accelerating Changeover with SMED
Single-Minute Exchange of Die (SMED) is a lean methodology. It aims to reduce or eliminate changeover time in a manufacturing process.
SMED focuses on converting changeover tasks into external activities. These activities can be performed while the equipment is still running. This greatly improves changeover time.
To accelerate changeover with SMED, some key strategies are:
- Categorizing internal and external setup tasks
- Converting internal tasks to external
- Simplifying or streamlining tasks
- Standardizing processes
Implementing SMED offers benefits to organizational performance and efficiency. It directly reduces downtime, increases machine utilization, and allows for smaller, more frequent production runs. It also positively impacts inventory reduction and flexibility in adjusting production quantities.
With a customer-centric approach, the value is added directly to the process. This lean principle emphasizes waste elimination, thus optimizing organizational performance.
Professional training in lean principles and tools is a crucial aspect for successful implementation.
Visualizing Processes via Value Stream Mapping
Value stream mapping is a useful tool in Lean methodology. It visually represents processes in an organization, showing the steps and data involved in turning raw materials into finished products or services.
By using symbols to depict information flow and inventories, this method makes it easy to visualize the process and identify activities that add value to the product.
It helps enhance efficiency, decrease lead times, and optimize resource utilization by identifying unnecessary steps and bottlenecks. This saves time and resources, leading to higher productivity and cost savings.
Value stream mapping also reveals areas for growth, helps teams recognize constraints in the workflow, and improves capacity and workflow integration.
Analyzing and Resolving Bottlenecks
Two commonly used methods to identify bottlenecks in a workflow or process are bottleneck analysis and value stream mapping. These tools help organizations visualize the flow of processes and pinpoint areas where work is piling up or slowing down, thereby identifying bottlenecks.
Once bottlenecks are identified, organizations can analyze the root causes. This can be done using techniques such as Six Sigma’s DMAIC (Define, Measure, Analyze, Improve, Control) process. This method helps to gather data, identify root causes of problems, and implement solutions to resolve bottlenecks effectively.
Additionally, other Lean management tools such as Just-In-Time (JIT) and Plan-Do-Check-Act can be used to streamline processes and eliminate bottlenecks. For instance, implementing JIT principles can reduce inventory levels and minimize overproduction, thereby improving workflow. Utilizing PDCA helps organizations continuously improve their processes and identify solutions to eliminate bottlenecks, ultimately enhancing overall efficiency and customer satisfaction in a Lean management approach.
PDCA: The Cycle for Quality Control
The PDCA cycle is a great framework for maintaining and improving quality control. It involves four key steps: Planning, Doing, Checking, and Acting.
- In the manufacturing industry, the Planning phase involves setting quality standards for a product.
- The Doing phase entails the actual production and adherence to these standards.
- Checking involves regular quality checks using tools like Value Stream Mapping or Overall Equipment Effectiveness.
- Acting means taking corrective action if any issues arise.
By following these steps, organizations can systematically improve their processes, identify areas for improvement, and maintain a continuous focus on quality.
Incorporating PDCA principles into an organization’s quality management system can lead to a reduction in defects, increased efficiency, and overall cost savings. For instance, a call center could use the PDCA cycle to streamline its customer service processes, resulting in improved customer satisfaction and reduced call handling times.
Preventing Mistakes with Error Proofing
Error-proofing helps prevent mistakes in a process. One strategy is to use visual cues or markers to reduce the chance of errors. Standardizing work processes and providing thorough training also minimize errors. Designing products that can only be assembled in one way is another effective error-proofing technique. Regular audits and quality checks ensure these measures are followed. Cultivating a culture of continuous improvement and encouraging employees to report potential errors is crucial.
Regular training sessions reinforce the importance of error-proofing for process efficiency.
Determining Root Causes of Issues
One effective method for finding out why problems happen in an organization’s processes is using Lean tools. These tools include Value Stream Mapping, Just-in-Time , and Bottleneck Analysis. They help the business see how things are currently done, spot areas of waste, and figure out where they can make things better for the customers. Once the reasons for the problems are found, the organization can make targeted changes to fix them, making the work and efficiency better.
But there might be a problem when finding out why things go wrong: some employees might not want to change the way they do things. To deal with this, the organization can use good ways to manage change, talk clearly, and involve employees in making things better. Also, not having enough resources or know-how to use Lean tools might be another problem.
This can be fixed by giving the right training and getting Lean Six Sigma certification so the organization has the needed skills to do the problem analysis better.
Standardizing Work for Consistency
Standardizing work is important in lean management. It helps make processes and outcomes consistent. This means organizations can eliminate mistakes and get predictable results. In manufacturing, it makes sure each product meets the same standards, which reduces defects and rework.
Key components of standardizing work in lean management include clear work instructions, visual aids, and regular training. Visual aids like flow charts and checklists help employees reference standard procedures easily.
Implementing standard work practices may face challenges, like resistance to change and needing more resources for training. But the benefits, like better quality, increased productivity, and less waste, are worth it. In service industries, standardizing work can lead to quicker customer service and fewer errors, which makes customers happier.
Leveraging Six Sigma Techniques
Organizations can use Six Sigma techniques to improve process efficiency and reduce defects. This includes implementing tools like the DMAIC method (Define, Measure, Analyze, Improve, and Control) and the DMADV method (Define, Measure, Analyze, Design, and Verify). These tools help identify areas for improvement, analyze data to find the root cause of defects, and develop solutions to enhance process efficiency and reduce defects.
Six Sigma focuses on customer satisfaction, data-based decision making, and a systematic approach to problem-solving. By using these principles, organizations can streamline processes, reduce variability, and improve quality and performance, leading to increased customer satisfaction and profitability.
Implementing Six Sigma helps reduce waste and optimize processes by rigorously analyzing data and identifying areas of inefficiency. Tools such as process mapping, statistical analysis, and root cause analysis can help identify and eliminate waste, reduce defects, and optimize processes to improve operational efficiency and quality.
Advantages of Implementing Lean Practices
Organizations that use lean practices benefit in several ways:
- They reduce waste, improve quality, increase productivity, and enhance customer satisfaction.
- Lean tools like Just-In-Time and Value Stream Mapping help identify inefficiencies and make strategic improvements to eliminate waste.
- These improvements positively impact organizational performance by streamlining operations, reducing lead times, and enhancing product and service delivery.
- Lean training is essential for successful implementation, as it equips employees with skills and knowledge to identify and eliminate waste and fosters a customer-centric approach.
- This training helps create a culture of continuous improvement, empowering employees to proactively implement efficiencies in their work for sustained benefits.
Lean Training and its Impact on Organizational Performance
Lean training is really important for improving how a company works. It helps employees learn and use lean methods well. Using lean practices in a company has many benefits such as less waste, better quality, higher efficiency, and happier customers. Lean methods find and get rid of waste, make workflows better, and boost productivity. By putting customers first, lean principles help companies run better by making operations smoother and encouraging ongoing improvement.
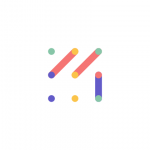
Vizologi is a revolutionary AI-generated business strategy tool that offers its users access to advanced features to create and refine start-up ideas quickly.
It generates limitless business ideas, gains insights on markets and competitors, and automates business plan creation.