Lean Methodology: How to Analyze It
Lean methodology is a popular business approach. It focuses on efficiency and eliminating waste. Many companies use it to improve processes and deliver better results.
But how can you analyze lean methodology for your organization? This article explores the methods and tools to evaluate lean methodology. It helps determine if it’s the right approach for your business.
Whether you’re new to lean or refining existing processes, this guide will help you make informed decisions about integrating lean methodology into your organization.
Understanding the Core of Lean Methodology
Origins in Manufacturing and Evolution into Software Development
Lean methodology started in manufacturing, particularly the Toyota Production System. It focused on continuous improvement and respect for people. It has now expanded to software development and knowledge work. The transition was possible due to the focus on creating value for the customer and eliminating waste. Speedy delivery and feedback are also essential, relevant to both manufacturing and software development.
Both sectors use lean tools like Value Stream Mapping and Just-in-Time manufacturing to reduce waste. However, they differ in application due to their unique challenges. Software development requires adapting lean principles to fit the iterative and collaborative nature of the work.
Key Pillars: Continuous Improvement and Respect for People
Organizations can promote continuous improvement in Lean methodology by creating a culture of learning. This involves regular data analysis to identify areas of improvement. Encouraging innovation and idea generation from all employees is also important, as well as providing support for process optimization.
Businesses can demonstrate respect for people within Lean principles by empowering employees to make decisions and contribute to problem-solving. Facilitating transparent communication, recognizing diverse perspectives, and promoting a supportive work environment are essential components in showcasing respect for people within Lean principles.
Lean Tools and Techniques: Accelerating Efficiency
Comprehensive Overview of Value Stream Mapping
Value Stream Mapping (VSM) is a way to visualize and analyze how materials and information move to deliver a product or service to customers. It helps to understand the current state of the organization and find ways to reduce waste, processing times, and delays. By creating a clear picture of the value stream, companies can make plans to improve operations, lessen lead time, and make customers happier.
VSM supports continuous improvement and respect for people in Lean practices. It helps to find activities that don’t add value, so teams can focus on removing waste and making processes better. Also, involving employees from different levels of the organization in the mapping process promotes Lean’s respect for people principle. This includes frontline workers and gives them control to suggest ideas for improving processes, encouraging ongoing learning and getting better.
Just-In-Time (JIT): Optimizing Inventory Management
Just-In-Time (JIT) inventory management means companies get goods only when they need them for production. This reduces the need for warehouse storage. JIT lowers inventory levels, reducing carrying costs and the risk of inventory becoming obsolete or damaged. It also optimizes inventory control by streamlining operations, reducing waste, and increasing overall production efficiency.
Implementing JIT inventory management brings several benefits, like reduced inventory holding costs, shorter lead times, better product quality, and increased productivity. JIT also promotes employee involvement, collaboration with suppliers, and efficient use of machinery.
JIT inventory management contributes to overall efficiency and cost savings in the supply chain. It achieves this by reducing stock levels, lowering warehousing needs, and streamlining the production process. This leads to reduced waste and the ability to adapt quickly to changes in customer demand, saving time and resources in the supply chain.
Employing Bottleneck Analysis to Eliminate Delays
Bottleneck analysis helps identify and eliminate delays in a process. It focuses on the steps or stages where work-in-progress tends to accumulate, causing overall delays. Organizations prioritize efforts to optimize these specific areas for reducing delays and improving the flow of work.
Key steps and considerations when implementing bottleneck analysis:
- Map out the entire process
- Measure cycle times and work-in-progress at each stage
- Identify the stage with the highest cycle time or work-in-progress level as the bottleneck
Organizations can then make targeted improvements, like reallocating resources or improving equipment, to alleviate the bottleneck and enhance efficiency.
The data and insights gathered from bottleneck analysis inform decision-making, guide resource allocation, and help organizations adapt to changing needs and conditions. This analysis drives ongoing improvements, ensuring processes remain efficient and effective.
5S Methodology for Workplace Organization
The 5S principles make work environments more efficient and productive. They are:
- Sort.
- Set in Order.
- Shine.
- Standardize.
- Sustain
These principles help organizations eliminate clutter, reduce waste, and create safer workspaces. For example, the “Sort” step removes unnecessary items, improving space utilization and workflows. The “Shine” step involves regular cleaning, maintaining equipment and work areas for increased efficiency.
The 5S methodology also creates standardized processes and procedures, leading to better organization and workflow management. “Standardize” involves documenting and communicating work processes, reducing errors and inconsistencies. This improves productivity and operational efficiency.
The key steps for implementing 5S are:
- Remove unnecessary items properly.
- Organize and label necessary items.
- Regularly clean work areas and equipment.
- Document and communicate work processes.
- Implement practices for continuous improvement.
Kaizen: The Power of Incremental Improvements
Kaizen, the Japanese term for continuous improvement, is important for making small, ongoing improvements in an organization’s processes. It encourages refining internal processes to provide the best value for consumers. This approach aligns with Lean Management, promoting waste elimination and efficiency.
Kaizen contributes to Lean Management by focusing on identifying and eliminating eight types of waste: defects, overproduction, waiting, non-utilized talent, transportation, inventory, motion, and extra-processing. Implementing Kaizen involves strategies like promoting employee involvement, setting achievable goals, empowering frontline workers to identify areas for improvement, and creating a culture that supports continuous learning. By integrating Kaizen, a business can streamline processes, increase productivity, and drive sustainable growth.
Fundamentals of Lean Leadership and Meta-Lean Approaches
Significance of Lightweight Leadership in Lean Practices
Lightweight leadership is important for lean practices. It empowers frontline workers and allows them to make decisions. This helps in quick problem-solving and process improvement. It also promotes a culture of continuous improvement by giving employees the power to address waste and inefficiencies. This leadership style boosts employee engagement and morale by showing trust in their capabilities.
Lean Portfolio Management: Realizing Enterprise Value
Lean Portfolio Management (LPM) helps businesses create value by aligning strategy, funding, and execution. This approach provides a more holistic view of development and delivery.
It enables organizations to make strategic and investment decisions in line with Lean principles, resulting in streamlined value delivery.
Lean management principles impact businesses by creating continuous workflow and delivering high value to the customer. Strategies include creating a pull system and continuous improvement through Lean tools such as Just-in-Time manufacturing, Plan-Do-Check-Act (PDCA), and Value Stream Mapping.
By focusing on optimizing workflows and eliminating waste, organizations can build a culture of continuous improvement and resilience. This allows for sustainable delivery of value to customers.
Respecting Frontline Workers’ Contribution to Lean Success
Frontline workers play a big part in Lean success. They use their experiences to give important input. This helps make Lean principles work in real life. Organizations can listen to them and make sure they feel respected. Communication should be open so they can share ideas and issues. Also, recognizing and rewarding their contributions can encourage them to be more engaged. When organizations value frontline workers, it helps Lean initiatives succeed.
When frontline workers feel valued, they are more likely to join in efforts to make continuous improvements. This makes Lean processes more efficient and long-lasting.
The Principles of Lean Management and Their Impact on Business
The Process of Identifying and Delivering Value
Lean methodology is all about making things better all the time. It’s about finding out what customers want, delivering it fast, and getting feedback to make things even better. By cutting out waste and inefficiency, organizations can make sure they give customers and stakeholders the best value.
Lean also uses things like Bottleneck Analysis, Just-in-Time manufacturing, Value Stream Mapping, Overall Equipment Effectiveness (OEE), Plan-Do-Check-Act , and Error Proofing tools to keep improving. These methods help organizations run better, make customers happy, and build stronger businesses in different industries.
Strategies for Creating Continuous Workflow
One strategy for creating continuous workflow within an organization using lean methodology involves the implementation of a pull system. This system focuses on producing goods only when there is demand. It helps minimize inventory, reduce waste, and ensure that resources are used efficiently.
Incorporating the principles of lean management such as just-in-time manufacturing, value stream mapping, and overall equipment effectiveness can cultivate and maintain a continuous workflow. By continuously improving internal processes, optimizing the value stream, and eliminating waste, organizations can ensure that tasks and resources are utilized effectively to create the highest value possible for the customer.
Additionally, Lean tools such as bottleneck analysis and error proofing help identify and address areas of inefficiency, leading to a streamlined workflow.
Implementing these principles and strategies not only reduces waste but also enhances productivity, quality, and customer satisfaction, making it an advantageous approach for organizations seeking to achieve efficiency and sustainable growth.
Advantages of Developing a Pull System
Implementing a pull system in a business or organization has several advantages.
- It reduces lead times and inventory levels by producing based on customer demand, not estimates.
- This method ensures that products are made as needed, reducing excess inventory and costs.
- A pull system makes workflow more efficient by streamlining processes, saving storage space, and responding to customer demands quickly.
- It encourages continuous improvement and waste reduction by focusing on delivering value and eliminating waste in the production process.
- By refining internal processes to enhance customer value, it helps identify and eliminate waste, making production more efficient.
Cultivating Continuous Improvement Within an Organization
Creating a culture of continuous improvement within an organization involves:
- Establishing clear and measurable goals.
- Encouraging open and honest communication.
- Promoting a mindset of experimentation and learning from failures.
Lean principles can help by:
- Emphasizing the identification and elimination of waste in processes.
- Promoting standardized work.
- Encouraging the use of visual management tools to track progress and identify areas for improvement.
Lean leadership is crucial in:
- Providing support and resources for improvement efforts.
- Promoting a collaborative and participatory decision-making process.
- Setting an example through continuous learning and improvement.
Utilizing Lean Tools for Advanced Process Improvement
Single-Minute Exchange of Die (SMED) for Reduced Downtime
Single-Minute Exchange of Die (SMED) is a technique in lean manufacturing. It aims to reduce downtime during the changeover process. By simplifying and speeding up the changeover process, SMED helps organizations minimize downtime and maintain efficient production.
This is achieved by dividing changeover tasks into internal and external setup tasks. Whenever possible, internal tasks are converted to external tasks. The remaining tasks are streamlined to reduce changeover time.
Integrating SMED into lean management practices offers several benefits:
- Improved overall equipment effectiveness
- Reduced setup times
- Increased equipment utilization
- Greater production flexibility
This allows organizations to respond more quickly to customer demands, reduce costs, and increase competitiveness in the market.
Implementing Error Proofing Techniques in Operations
Error proofing helps make operations more efficient and reduce mistakes. Techniques like mistake proofing, visual controls, and automation can minimize human error, streamline processes, and reduce waste.
For example, in an automotive assembly line, poka-yoke sensors are used to prevent incorrect parts from being used during the manufacturing process, which ensures higher accuracy.
Incorporating error proofing techniques aligns with the goal of continuous improvement within an organization by systematically identifying and addressing areas for improvement, ultimately leading to increased quality and productivity.
However, challenges can arise in implementing error proofing techniques, such as resistance to change and lack of awareness. These challenges can be overcome through leadership support, training programs for employees, and creating a culture of continuous improvement that values error prevention through collaboration and feedback loops.
Enhancing Efficiency Through Standardized Work
Standardized work is important for making operations more efficient. It sets a standard for how tasks should be done, making sure they’re consistent and reducing wasted time. By documenting specific procedures, it helps to improve quality, increase productivity, and reduce lead times. This approach also helps to find inefficiencies and provides a foundation for making things better. Using standardized work can save money, make customers happier, and empower employees.
It’s also a key part of Lean management, creating a culture of improvement and excellence.
Incorporating Six Sigma Methods for Quality Control
Six Sigma methods focus on achieving operational excellence by reducing defects and improving customer satisfaction. The key principles include defining, measuring, analyzing, improving, and controlling processes.
Organizations can incorporate these principles by setting clear objectives, analyzing relevant data, and implementing solutions to improve product and service quality.
Using Six Sigma methods helps in reducing process variations, identifying defects, and streamlining operational processes, leading to better customer satisfaction and loyalty.
Specific tools and techniques, such as Six Sigma DMAIC methodology, statistical process control, root cause analysis, control charts, and value stream mapping, can be used to improve quality control processes in a business setting.
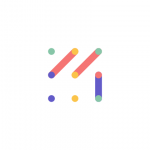
Vizologi is a revolutionary AI-generated business strategy tool that offers its users access to advanced features to create and refine start-up ideas quickly.
It generates limitless business ideas, gains insights on markets and competitors, and automates business plan creation.