Mastering Lean: Exploring the 5 Levels in Depth
Welcome to the exploration of the 5 levels of mastering Lean. Lean methodology aims to eliminate waste and improve efficiency. It’s popular in various industries.
In this article, we will cover each level of Lean. We’ll start with the foundational “Basic Stability” and end with the advanced “True Perfection”. You’ll gain a comprehensive understanding of Lean principles at every stage of your organization. Whether you’re new to Lean or refining your skills, this article will equip you with the knowledge to excel in Lean practices.
Core Principles Driving Lean Practices
The Lean Enterprise Institute defines 5 core principles driving Lean practices: value, value stream, flow, pull, and perfection.
These principles aim to contribute to continuous improvement. They focus on eliminating waste, improving efficiency, and delivering better value to customers.
By understanding customer needs, mapping the value stream, creating flow in work processes, establishing a pull-based system, and continuously pursuing perfection, lean strategies aim to elevate quality, efficiency, and customer satisfaction.
Lean management techniques include setting clear goals to motivate the team and eliminate roadblocks, adopting a lean mindset focused on removing waste and creating a culture of shared leadership, and finding a change agent to establish lean practices throughout the organization.
These techniques contribute to achieving lean excellence by fostering a culture of continuous improvement and maximizing customer value while minimizing waste.
The Importance of Lean for Continuous Improvement
Key Techniques in Lean Management
Value stream mapping is a helpful tool in Lean management. It allows organizations to examine their processes and find areas for improvement. By mapping the flow of materials and information, businesses can identify unnecessary steps and get rid of waste.
For example, a company might realize that products are moving back and forth between different production stages, which slows down the process. Using value stream mapping, the company can optimize the production line layout to reduce inefficiencies and speed up the workflow.
Implementing the 5S system can also improve organizational efficiency in Lean management. The 5S system includes sort, set in order, shine, standardize, and sustain. By decluttering the workspace and setting everything in order, employees can find tools and materials more easily, creating a more organized and productive work environment. This leads to faster turnaround times, easier navigation through materials, and overall improved efficiency, while reducing waste.
In lean operations, mistake-proofing methods like Poka-Yoke and root cause analysis are important in preventing errors and defects. Poka-Yoke involves designing products or components in a way that makes errors impossible or easily detectable. This ensures that mistakes are not made during production. Root cause analysis allows organizations to pinpoint the underlying reasons for a problem, helping them eliminate the source of defects and prevent future occurrences. These strategies are essential for ensuring high-quality outputs and minimizing waste in lean operations.
Value Stream Mapping
Value stream mapping is a helpful tool in Lean project management. It can identify the current state of the value stream in terms of flow, information, and materials.
By visually representing the steps in a process, it shows which steps add value to the product or service and which ones are waste. This helps identify opportunities for improvement, leading to higher efficiency and lower costs.
For example, a company using value stream mapping may identify instances of overproduction or excess inventory in the production process, which are considered waste. They can then make changes to eliminate these inefficiencies.
Similarly, mapping the information flow in a customer service system may reveal communication bottlenecks that can be resolved by reallocating responsibilities or adjusting procedures.
Using value stream mapping to comprehend and analyze processes, organizations can continuously make strategic improvements.
5S System Implementation
The 5S system has five key steps: sorting, setting in order, shining, standardizing, and sustaining.
Managers leading Scrum project management should prepare the team for change by setting clear goals, adopting a Lean mindset, and finding a change agent within the organization.
This system helps reduce waste and improve efficiency by encouraging a clean and organized workspace. It also makes it easier to identify items and tools, increases productivity, and reduces the time required to locate and retrieve items.
These changes can improve employee morale and satisfaction, reduce workplace injuries, and decrease work-related stress.
Integrating the 5S System into an organization’s processes can bring improved overall working conditions, increased safety and security, the ability to quickly identify and correct operational problems, and the establishment of a quality and safety-oriented culture.
Mistake Proofing with Poka-Yoke
Poka-Yoke can help prevent mistakes and errors in processes. It uses fail-safe mechanisms and error-proofing techniques to create foolproof processes.
For example, a digital camera that won’t turn on until an SD card has been inserted ensures no pictures are taken without storage capacity.
Mistake-proofing techniques can also involve color-coding, multiple signaling, parts that only fit together in the correct way, and clear instructions.
These principles and techniques contribute to efficiency gains and quality improvement by reducing the possibility of defects and errors.
By incorporating Poka-Yoke methods, companies can save time, resources, and costs associated with errors.
It also creates a culture of continuous improvement and quality control, leading to more efficient operations and increased customer satisfaction.
Root Cause Analysis (RCA) Basics
Root cause analysis (RCA) helps identify the main reason for a problem or process failure in lean management. By finding the root cause, teams can prevent recurring issues, improve processes, and increase efficiency.
The steps in conducting root cause analysis include defining the problem, gathering and analyzing data, identifying possible causes, evaluating these causes, and implementing corrective actions.
RCA benefits lean practices by offering insights into areas for optimization and waste reduction, leading to continuous improvement.
Addressing root causes helps organizations streamline operations, reduce defects, and enhance performance, aligning with the objective of lean management to drive value and eliminate waste.
Benefits of Integrating Lean Strategies
Elevating Quality through Lean Application
Lean practices help businesses and organizations improve quality by using five principles: defining value, mapping value stream, creating flow, establishing pull, and pursuing perfection. This eliminates waste, streamlines processes, and boosts overall quality and efficiency.
Lean management techniques also play a key role in quality improvement. Understanding customer needs, creating flow in work processes, and continuously seeking perfection are vital. These techniques reduce waste, improve teamwork, manage inventory efficiently, and enhance the customer experience.
Lean methodologies aim to maximize customer value while minimizing waste, leading to improved customer satisfaction and quality. Focusing on efficiency and continuous improvement creates a culture of shared leadership and responsibility, ultimately enhancing the customer experience and overall quality.
Efficiency Gains from Streamlined Processes
Streamlined processes have made the organization more efficient. They have eliminated waste, reduced production times, and improved quality.
Lean strategies have also boosted efficiency by identifying and addressing bottlenecks. They focus on continuous improvement and empower employees to enhance processes.
Techniques like value stream mapping, creating flow in work processes, and establishing a pull-based system have contributed to efficiency gains.
Moreover, pursuing perfection, incorporating Lean thinking into the corporate culture, and maximizing customer value while minimizing waste have been crucial in achieving efficiency gains.
Cost Management via Waste Reduction
Waste reduction can help businesses manage costs. It does this by getting rid of unnecessary expenses and using resources more efficiently.
For example, a company can cut operational costs and improve profits by making processes more efficient and reducing excess inventory. By finding value, creating smooth workflows, using pull-based systems, and aiming for perfection, businesses can save money and use resources better. Integrating waste reduction into operations can lead to better profits, lower expenses, and improved productivity. This opens up opportunities for investment, growth, and other plans to make the business stronger for the long term.
Boosting Customer Satisfaction with Lean
Lean practices help make customers happy. They do this by concentrating on what customers find valuable and cutting down on waste. To boost customer satisfaction, businesses can use strategies like setting clear goals, embracing a Lean mindset, and finding a change agent in the company. Lean also helps create a culture of always getting better and working together, which results in better value for customers.
Cultural Transformation through Lean
Lean principles are important for organizations. They involve a Lean mindset, shared leadership, and clear goals.
Explaining Lean and its benefits to the team helps them embrace the change. Finding an influential change agent within the organization is also helpful.
Leadership is crucial for fostering a culture of continuous improvement and Lean practices. It helps set clear goals, demonstrates commitment, and drives cultural transformation.
Successful examples of using Lean methodologies include creating shared leadership, increasing efficiency, and eliminating waste. Organizations also improve teamwork, inventory management, and customer interactions by embracing Lean thinking.
Capturing a Competitive Edge
Lean management offers valuable tools to help organizations streamline processes, minimize waste, and focus on delivering maximum value to customers. The five essential principles of Lean are understanding customer needs, mapping the value stream, creating flow in work processes, establishing a pull-based system, and continuously pursuing perfection. These techniques emphasize continuous improvement, waste reduction, and efficiency enhancement.
Companies implementing these principles can optimize operations, reduce costs, and improve productivity to gain a competitive edge in the market.
Efficiency gains from streamlined processes play a crucial role in capturing a competitive edge. By eliminating waste, improving workflow, and maximizing customer value, companies can operate more effectively and stand out within the industry. Lean strategies aim to foster a culture of continuous improvement and shared leadership, promoting collaboration and innovation. Consequently, companies can meet customer expectations better, deliver higher quality products and services, and stay ahead of competitors.
Integrating lean strategies offers benefits for companies seeking a competitive edge, including improved teamwork, inventory management, and customer interactions. Lean principles enable organizations to have a more customer-centric and efficient operation.
Additionally, integrating lean thinking into a corporate culture can foster continuous improvement and collaboration, allowing businesses to adapt more swiftly to market changes and achieve sustained success in a competitive environment.
Diving Deep into Lean Six Sigma Phases
Define: The Starting Point of Lean Projects
Starting a lean project is important in the lean methodology. It sets the stage for successful implementation and continuous improvement. Identifying the starting point defines the value for the customer and establishes a clear direction for the project. It also aligns the organization’s efforts toward waste elimination and efficiency improvement.
Key considerations in identifying the starting point include:
- Understanding customer needs
- Mapping the value stream
- Creating flow in work processes
- Establishing a pull-based system
- Consistently pursuing perfection
Organizations can apply this by integrating lean principles into their culture, focusing on teamwork, inventory management, and customer interactions. By focusing on value and waste elimination, organizations can make sustainable improvements that benefit both the company and its customers.
Measure: Quantifying the Current State
In Lean management, we can measure the current state of a process by looking at specific data points like cycle time, lead time, defects, inventory levels, and overall process velocity.
These metrics show how efficient and valuable a process is, helping organizations find areas to improve and cut waste.
We can also use methods like process mapping and value stream analysis to visually show the current state, find bottlenecks, and see how value moves through a process.
Using tools like value stream maps and kanban boards can make it easier to see inefficiencies and ways to improve. This helps organizations measure the current state accurately and start a continuous improvement journey following Lean principles.
Analyze: Identifying the Root Problems
To conduct a thorough root cause analysis in Lean Management, organizations can use tools such as the 5 Whys technique, the cause and effect diagram (also known as the fishbone or Ishikawa diagram), or the Pareto chart. These methods can help them identify the underlying issues or problems that are hindering efficiency and quality in their processes.
By focusing on identifying the root problems, organizations can better understand the factors contributing to waste, defects, or delays in their operations. This is important as part of the Lean methodology because it allows organizations to make targeted improvements that address the fundamental causes of their challenges, rather than just treating the symptoms.
Identifying root problems helps organizations avoid inefficiencies and errors, leading to the delivery of better value to customers and the establishment of a culture of continuous improvement.
Improve: Implementing Effective Solutions
Implementing solutions through the Lean methodology involves several steps:
- Set clear goals and communicate them to the team to motivate and eliminate roadblocks.
- Adopt a Lean mindset within the team by explaining the concept and its benefits, fostering shared leadership and continuous improvement.
- Find a change agent to establish Lean practices and transform the organization.
- Create a pilot group with members from different teams and introduce them to the 5 principles of Lean.
- Incorporate Lean thinking into the corporate culture, emphasizing effort, vigilance, maximizing customer value, and minimizing waste.
- Evaluate the effectiveness of solutions by considering factors like customer value, waste reduction, teamwork improvement, and customer interactions.
Control: Maintaining and Monitoring
Lean management techniques are important for maintaining and monitoring processes. They include identifying waste, creating a culture of continuous improvement, value stream mapping, setting clear objectives, and using the “pull” principle. These techniques help organizations find inefficiencies, maintain production standards, and monitor performance against waste reduction goals.
Mistake-proofing with Poka-Yoke can be used to maintain and monitor lean practices by preventing defects in the production process. Poka-Yoke methods, like error-proofing devices or processes, help eliminate errors that can lead to waste.
Efficiency gains from streamlined processes in lean management can be maintained and monitored through regular monitoring, data collection, and analysis to identify areas for improvement. Continuous improvement and maintaining Lean thinking among team members also play a critical role in sustaining efficiency gains. This involves establishing clear performance metrics, involving employees in the improvement process, and making incremental changes to deliver better value to customers.
Distinguishing the Belt Levels in Lean Methodology
Understanding the Lean White Belt Tier
The Lean White Belt tier is guided by core principles. These include defining value, mapping the value stream, creating flow, establishing pull, and pursuing perfection. These principles help drive continuous improvement and contribute to the importance of Lean practices. They help organizations eliminate waste, improve efficiency, and deliver better value to customers.
At this tier, key techniques are crucial for Lean management. These techniques include understanding customer needs, mapping the value stream, creating flow in work processes, establishing a pull-based system, and continuously pursuing perfection. They provide a strong foundation for implementing Lean practices and fostering a culture of shared leadership and continuous improvement within organizations.
Lean Yellow Belt: Foundations and Application
The main principles of lean practices are value, value stream, flow, pull, and perfection. Lean methodology focuses on continuous improvement by emphasizing customer value and reducing waste. This encourages organizations to always look for ways to improve. Continuous improvement is crucial for organizations to stay competitive and sustainable in the long run.
In lean management, key techniques include value stream mapping, implementing the 5S system for workplace organization, using Poka-Yoke to prevent mistakes, and basics of root cause analysis to address problems at the root. These techniques help businesses streamline processes, minimize waste, boost productivity, and improve customer satisfaction.
Green Belt: Collaborative Efficiency Expertise
- Green Belt professionals follow five key principles central to Lean practices.
- The first principle is defining value. This involves identifying the activities that add value to the end customer.
- The second principle involves mapping the value stream, which means visualizing the steps required to deliver a product or service.
- Creating flow in work processes is the third principle, about minimizing interruptions and delays.
- The fourth principle is establishing pull, focusing on producing only what is needed when it is needed.
- Finally, the pursuit of perfection is the fifth principle, emphasizing continuous improvement.
- Green Belt experts collaborate to improve efficiency by creating a culture of shared leadership and involving team members in decision-making processes.
- Through open communication and shared responsibility, Green Belt experts seek continuous improvement and actively pursue waste reduction to deliver greater value to customers.
- To drive collaborative efficiency in Lean management, Green Belt professionals implement the concepts of Lean thinking, shared leadership, and continuous improvement.
- They work to eliminate waste, improve teamwork, and enhance customer interactions to deliver better value.
Black Belt: Mastery of Lean Tools and Leadership
The core principles of lean manufacturing practices are:
- Defining value
- Mapping the value stream
- Creating flow
- Establishing pull
- Pursuing perfection
These principles help in mastering lean tools by:
- Eliminating waste
- Improving efficiency
- Creating a culture of Lean thinking
The integration of lean strategies benefits by:
- Continuous improvement
- Quality elevation
- Efficiency gains
- Waste reduction
This, in turn, enhances:
- Customer satisfaction
- Cultural transformation
Lean strategies help in:
- Understanding customer needs
- Establishing flow in work processes
- Creating a pull-based system
The Black Belt level in lean methodology reflects a deep understanding and successful application of Lean principles. It signifies mastery of lean tools and leadership. Professionals achieving the Black Belt level can optimize processes and systems, improve teamwork, inventory management, and customer interactions, leading to a significant advancement in operational and leadership effectiveness.
Achieving Lean Excellence: The Master Black Belt
The core principles of Lean manufacturing are: defining value, mapping the value stream, creating flow, establishing pull, and pursuing perfection.
These principles work together to:
- Eliminate waste
- Improve efficiency
- Deliver better value to customers
By creating a culture of Lean thinking and continuous improvement, a Master Black Belt can guide an organization toward achieving Lean excellence.
The integration of Lean strategies can significantly benefit an organization by:
- Maximizing customer value
- Minimizing waste
- Improving teamwork, inventory management, and customer interactions
Additionally, Lean strategies can enhance:
- Quality
- Efficiency
- Cost management
- Customer satisfaction
- Ultimately give the organization a competitive edge
To achieve Lean excellence, a Master Black Belt should be proficient in:
- Value stream mapping
- Establishing pull-based systems
- Creating flow in work processes
- Understanding customer needs
- Continuously pursuing perfection
These key techniques and phases in Lean management are essential to achieving Lean excellence and delivering significant value to the organization.
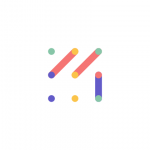
Vizologi is a revolutionary AI-generated business strategy tool that offers its users access to advanced features to create and refine start-up ideas quickly.
It generates limitless business ideas, gains insights on markets and competitors, and automates business plan creation.