Rules of Lean Management Explained
Lean management is a powerful approach. It focuses on maximizing value while minimizing waste. Continuous improvement and streamlined processes are its core principles. Lean management has revolutionized how organizations operate.
In this article, we will explore the fundamental rules of lean management. It explains how they can help businesses achieve greater efficiency, profitability, and customer satisfaction. Whether you’re new to lean management or refining your existing practices, understanding these rules is the first step to unlocking the full potential of this transformative management philosophy.
Understanding Lean Management: An Overview
The Essence of Lean Management
Lean management focuses on delivering customer value. It does this by defining value, mapping the value stream, and creating flow. This streamlines the production process and eliminates waste, focusing on delivering what the customer truly values. Pull is established to prevent overproduction and unnecessary inventory, ensuring work is done only when there is demand.
Lean management also sustains continuous improvement through the principle of Kaizen, constantly seeking ways to improve processes and enhance efficiency. By integrating Lean thinking into corporate culture, organizations can continuously strive for improvement, leading to better value for the customer and reduced waste.
The Fundamental Principles of Lean Management
Identifying Customer Value
Businesses need to prioritize what is valuable to customers. They can do this by defining value, a key principle of Lean management. This means understanding the specific needs and preferences of customers and aligning products or services accordingly. To gather feedback and insights, methods such as surveys, interviews, and social media monitoring can be used to understand the customer’s perception of value.
Companies can also identify and measure the value their products or services deliver by analyzing sales data, customer reviews, and return rates. Applying lean principles helps businesses continuously improve their offerings to better meet customer needs and deliver greater value.
Mapping the Value Stream
The value stream mapping process involves:
- Identifying and visually representing every step in the production process.
- Analyzing information and material flow to find areas of waste and improvement opportunities.
- Identifying customer value and waste by distinguishing value-added and non-value-added activities.
- Eliminating non-value-added activities to use resources more efficiently, leading to a streamlined production process and higher customer value.
To ensure a seamless workflow:
- Steps are taken to encourage open communication and collaboration between different departments.
- This helps to identify and address bottlenecks and inefficiencies in the production process, leading to improved overall workflow and productivity.
Ensuring a Seamless Workflow
To ensure a seamless workflow, it’s important to map each step in the process and remove any unnecessary steps. Understanding the flow of materials and information helps identify waste and areas for improvement.
Implementing strategies like kanban boards and real-time dashboards can visually signal when work should start and finish based on customer demand. This prevents overproduction and reduces inventory, making the workflow more efficient and responsive.
Continuous improvement can be achieved by promoting a culture of Kaizen, encouraging all employees to make small, regular changes to the workflow. This leads to ongoing improvements in productivity, quality, and customer satisfaction, contributing to the goal of a seamless workflow.
Implementing a Pull System
To successfully implement a Pull System in a work environment, follow these steps:
- Analyze the existing workflow to find areas for improvement and Pull System implementation.
- Understand product or service demand and adjust production or delivery accordingly.
- Communicate and collaborate between departments for a smooth transition to a Pull System.
- Train and educate employees on Pull System principles and just-in-time production.
- Structure the work environment to support Pull System, focusing on flow and waste reduction.
- Align production or service delivery with customer demand, minimize inventory holding, and continuously improve processes.
Successful implementation requires careful planning, collaboration, and commitment to continuous improvement.
Pursuing Continuous Improvement
Organizations can encourage continuous improvement in processes by integrating lean management principles. This includes defining customer value, mapping the value stream to identify waste, creating flow to streamline processes, establishing pull based on customer demand, and pursuing perfection through ongoing Kaizen efforts.
Strategies for identifying areas in need of improvement and implementing changes include using tools like project brief templates, Gantt charts, and project dashboards. Project management software with features like kanban boards and task automation can also facilitate lean project management.
The concept of “Kaizen,” or continuous improvement, can drive ongoing improvements and waste reduction by empowering employees to identify and address inefficiencies in their daily work, contributing to the organization’s lean management goals.
Applying Lean Management in Engineering
Adapting Lean Principles in Engineering Projects
Lean principles can help improve efficiency and minimize waste in engineering projects. This is achieved by focusing on defining value, mapping the value stream, creating flow, establishing pull, and continuous improvement (Kaizen).
For example, integrating lean management tools and templates like the project brief template, Gantt chart template, and project dashboard template can guide project teams in aligning their work with customer value and streamlining workflow processes. This approach also ensures a seamless workflow by identifying and eliminating non-value adding activities while enhancing customer value.
Technology also plays a crucial role in integrating lean principles. Tools like kanban boards, real-time dashboards, and task automation in project management software enable greater transparency and efficiency. These technologies improve visualization, tracking, and progress monitoring, leading to greater efficiency and waste reduction in engineering projects.
Tools to Effectively Implement Lean Management
Lean Project Brief: Structure and Benefits
The Lean Project Brief includes defining value, mapping the value stream, creating flow, establishing pull, and continuous improvement.
By using these components, project managers can create a plan focused on adding value for the customer and eliminating waste.
It provides a clear structure and direction for the project, benefiting project management and efficiency.
Defining value and mapping the value stream ensures that resources are allocated to tasks contributing to the customer’s needs.
Creating flow and establishing pull reduces unnecessary steps and ensures work is pulled through the system only when needed.
The emphasis on continuous improvement allows for ongoing optimization and adaptability throughout the project lifecycle.
Implementing a Lean Project Brief fosters a culture of efficiency and continuous improvement in engineering projects.
It aligns project activities with customer value, streamlines processes, and delivers better value to customers.
This approach also reduces waste, whether in the form of excess inventory, overproduction, or defects, for a more sustainable and effective project outcome.
The Role of Gantt Charts in Lean Management
Gantt charts help visualize and manage workflow in Lean Management. They show a clear timeline of tasks and activities, allowing teams to monitor progress and track performance. This helps identify any bottlenecks or delays in the process.
Visualizing workflow is crucial in Lean Management. It enables teams to make data-driven decisions to optimize processes and improve efficiency. Gantt charts also help identify and eliminate waste, highlighting non-value-adding activities and unnecessary wait times. This helps streamline processes and reduce waste, leading to cost savings and improved performance.
Using Gantt charts contributes to the pursuit of continuous improvement in Lean Management. They provide a visual representation of the workflow, allowing for real-time adjustments and enabling teams to implement Kaizen, the principle of continuous improvement, through incremental changes for better results.
Dashboard Utilization for Project Tracking
Real-time dashboards can track project progress and identify areas for improvement in lean management practices. They provide a visual representation of key metrics such as cycle time, lead time, and work in progress.
Including these metrics in a project tracking dashboard is essential for effectively monitoring lean management principles and ensuring continuous improvement.
Technology, such as automated task management and integration of Kanban, enhances the efficiency of project tracking in lean management strategies. This streamlines workflow, reduces waste, and increases transparency.
Teams can achieve better visibility into their work processes and make data-driven decisions by utilizing project management software with features like kanban boards and task automation. This supports the overall goal of lean management, which is to deliver better value to customers and continuously improve operational effectiveness.
Leveraging Technology for Lean Efficiency
Integrating Kanban for Visual Workflow Management
Kanban is a helpful tool for visual workflow management. It shows work items and their status, helping teams spot issues and enhance workflow. Teams can track tasks and use resources better with Kanban boards, leading to increased efficiency. Benefits of Kanban in a lean system include more transparency, less waste, and smoother work flow. It also helps teams limit work in progress, prioritize tasks, and improve processes continuously.
Combining Kanban with real-time dashboards streamlines and monitors workflow. It gives current info on task statuses, resources, and project progress, aiding quick decision-making and proactive problem-solving, ultimately enhancing lean management.
Utilizing Real-Time Dashboards for Monitoring
Real-time dashboards are a useful tool for monitoring progress in lean management. They provide quick access to real-time data and metrics, allowing managers to stay informed about ongoing projects. This visibility helps in identifying issues or delays promptly for continuous improvement and smooth workflow. Real-time dashboards enable proactive decision-making by offering up-to-date insights into performance and productivity.
They give a comprehensive overview of operations, facilitating data-driven decisions to enhance efficiency and reduce waste.
Automating Tasks to Reduce Waste
Automation is an important part of lean management. It helps to find and get rid of waste in processes. Using technology to automate tasks, like data entry and report making, can make a big difference in how well a business works. Project management software can have features, like kanban boards and dashboards, that help with lean project management. Automating tasks can make things run smoother and with fewer mistakes. It also helps projects to do better and gives more value to customers.
To find tasks to automate, it’s important to think about how standardized the processes are, how often the tasks are done, and if there’s a way to make the tasks better. By thinking about these things, businesses can use automation in a better way to reduce waste and follow the basic ideas of lean management.
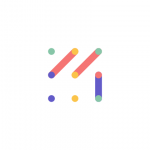
Vizologi is a revolutionary AI-generated business strategy tool that offers its users access to advanced features to create and refine start-up ideas quickly.
It generates limitless business ideas, gains insights on markets and competitors, and automates business plan creation.