Solving Workflow: 5S and Bottleneck Issues
In any workplace, making workflow as efficient as possible is important for getting things done. One way to do this is by using the 5S methodology, which is about keeping the workspace organized and tidy. It’s also important to find and fix any problems that slow things down, so work can keep moving smoothly.
In this article, we’ll look at how using the 5S methodology can help with these issues and make workflow better in different workplaces.
Understanding Workflow Bottlenecks
Defining Process Bottlenecks
Signs and symptoms of process bottlenecks:
- Uneven flows
- Bad planning
- Batch processing
Consequences:
- Waste
- Economic risks
- Decreased throughput
Impact on workflow efficiency:
- Delays
- Increased idle time
- Reduced overall throughput
Tools to identify bottlenecks:
- Cumulative flow diagrams
- Problem-solving techniques
Systematic approach:
- Theory of Constraints (TOC)
- Five Focusing Steps
Benefits:
- Continuous improvement
- Enhanced performance
Recognizing Production Variations as Bottleneck Triggers
Production variations can cause uneven flows, poor planning, and batch processing. Recognizing these variations as potential bottleneck triggers involves looking for fluctuations in output levels, delays in production, and inconsistent inventory levels. Strategies to address production variations as bottleneck triggers include using problem-solving techniques, implementing 5S methodologies to streamline workflow, and using Cumulative Flow diagrams to visualize variations.
By addressing these variations, organizations can improve productivity and reduce waste.
Identifying Production Capacity Constraints
There are some signs of production capacity constraints in the workflow. These include uneven flows, bad planning, and batch processing. Changes in production, like delays or long wait times, can lead to potential bottlenecks.
Effective ways to identify these constraints include problem-solving techniques, using 5S for workspace organization, and using a Cumulative Flow diagram to visualize work flow. The Theory of Constraints offers a systematic approach to improve workflow, with a method called the Five Focusing Steps. These steps involve identifying the bottleneck, exploiting it, subordinating other processes to it, elevating it, and rechecking for continuous improvement.
By combining practical problem-solving techniques with TOC methods, it’s possible to identify and fix production capacity constraints for better workflow efficiency.
Detecting Bottlenecks in Your Workflow
Common signs of a bottleneck in a workflow:
- Queues of work
- Congestion at specific workstations
- Delays in production output
Production variations can trigger potential bottlenecks:
- Inconsistent or uneven throughput in the production process
Methods to identify bottlenecks:
- Analyzing flow charts
- Using Cumulative Flow diagrams
- Conducting time and motion studies to pinpoint areas where work is piling up or moving slowly
Additional techniques:
- Value Stream Mapping
- Process observation
- Identifying areas where resources are overburdened or underutilized can also help detect bottlenecks within a workflow.
Resolving Workflow Bottlenecks
Step-by-Step Process for Addressing Bottlenecks
In the step-by-step process for addressing bottlenecks, the workflow constraint can be identified by analyzing throughput and identifying areas where work-in-progress or inventory piles up, causing slowdowns.
This can be visually represented using a Cumulative Flow Diagram to track inventory levels at different stages throughout a process, enabling identification of bottlenecks.
To maximize the bottleneck’s output in the resolution process, methods such as utilizing buffer management to manage work-in-process, increasing batch transfer sizes, or introducing additional shifts can be used.
Through thoughtful planning and problem-solving, these methods can help prevent idling at the bottleneck and maximize throughput.
The short-term effect of bottleneck resolution is an immediate increase in productivity at the bottleneck point, which can help to clear backlogs and prevent further inventory build-up.
Long-term effects include increased overall throughput, reduced lead times, and improved flow efficiency throughout a process.
By addressing bottlenecks, work-in-progress and inventory levels are reduced, leading to a more continuous workflow.
Identifying the Workflow Constraint
Production variations can cause bottlenecks in the workflow. These bottlenecks disrupt the smooth sequence of operations and create uneven flows.
Identifying and addressing workflow constraints involves a systematic approach, like the Theory of Constraints. This approach includes the Five Focusing Steps to identify and eliminate constraints in a cyclical process.
Resolving bottlenecks in the workflow has short-term effects. It leads to increased efficiency and reduced waste, resulting in improved productivity and cost savings.
In the long term, addressing bottlenecks can drive continuous improvement and performance. This ultimately leads to increased throughput and profitability.
Maximizing the Bottleneck’s Output
To maximize the bottleneck’s output within the workflow, it is important to first identify the bottleneck in the production process.
Once the bottleneck is determined, strategies can be implemented. These include exploiting the bottleneck’s capacity, subordinating non-bottlenecks to the bottleneck, elevating the bottleneck’s capacity, and rechecking the bottleneck to ensure continued improvement.
Furthermore, problem-solving techniques and methods like the 5S and Cumulative Flow diagram can lead to significant improvements in the bottleneck’s performance.
Addressing uneven flows, bad planning, and batch processing can maximize the bottleneck’s output, leading to reduced waste and economic risks.
The Theory of Constraints provides a specific methodology for identifying and eliminating bottlenecks, driving continuous improvement and performance within the workflow.
Combining these strategies can significantly enhance the performance of the bottleneck in the production process.
Ensuring Other Processes Align with the Bottleneck
To make the most of the bottleneck and increase its output, it’s important to adjust lean processes without creating more constraints. Companies can use the 5S methodology, which focuses on organizing and standardizing the workplace. This ensures that the bottleneck’s efficiency isn’t hindered by workspace organization and cleanliness.
Moreover, by using problem-solving techniques like root cause analysis and ongoing process improvements, companies can find and address issues that impact the bottleneck and long-term performance. The Five Focusing Steps, involving identifying, exploiting, subordinating, elevating, and rechecking the bottleneck, help companies strategically manage the bottleneck’s performance and enhance overall productivity.
By implementing these strategies effectively, companies can ensure long-term management of the bottleneck, leading to improved performance and less waste.
Improving the Bottleneck’s Performance
One strategy for maximizing the bottleneck’s output and improving its performance is using the Theory of Constraints. TOC offers a systematic approach to identifying and resolving constraints in processes. The Five Focusing Steps of TOC provide a specific methodology for breaking through bottlenecks, and the Thinking Processes can be used to identify root causes of workflow issues.
Processes can also be re-evaluated and adjusted through tools like Lean Thinking. This involves identifying, exploiting, subordinating, and elevating the bottleneck. By having a more effective process in place, managing and resolving workflow constraints can lead to increased productivity and reduced waste in the short-term. In the long-term, it can contribute to improved economic performance and enhanced overall efficiency.
Addressing workflow bottlenecks provides immediate relief and lays the foundation for continuous improvement and sustained success.
Re-evaluating and Adjusting Processes
Workflow bottlenecks can be found by observing, collecting data, and analyzing process flows. This involves looking at production rates, inventory levels, cycle times, and resource use to find where delays and inefficiencies happen.
To fix these bottlenecks, organizations can use the Theory of Constraints’ Five Focusing Steps. This includes identifying the bottleneck, exploiting it, subordinating other processes to it, increasing the bottleneck’s capacity, and continually checking it. Problem-solving techniques like using 5S and Cumulative Flow diagrams can also help overcome bottlenecks and make operations smoother.
Managing and addressing workflow constraints can have short-term and long-term impacts. In the short term, it can improve productivity, reduce waste, and use resources better. In the long term, it can save costs, increase throughput, improve quality, and enhance overall performance, leading to continuous improvement and profitability.
Mitigating Bottlenecks with Lean Strategies
Integrating Lean Methodologies with Constraint Management
Integrating Lean methodologies with constraint management is important for identifying and prioritizing workflow bottlenecks. Lean principles like 5S help maintain a clean and organized workspace, revealing bottlenecks more easily. Creating standardized procedures and visual management tools through Lean can aid in ongoing bottleneck identification.
Addressing bottlenecks and maximizing their output, while aligning other processes with the bottleneck, can be achieved through adopting the Theory of Constraints methodology. The Five Focusing Steps provide a cyclical process for identifying and eliminating constraints. Understanding how to exploit and elevate the bottleneck, as well as subordinating other processes to it, ensures the efficient use of resources and improves overall productivity.
Managing workflow constraints in the short-term and long-term can have several impacts. In the short-term, companies may experience reduced lead times, improved delivery performance, and optimized resource utilization. Over the long-term, successful bottleneck management may lead to increased profitability, enhanced customer satisfaction, and a more competitive position in the market. The key outcomes of this approach include continuous improvement, streamlined processes, and a stronger focus on driving operational efficiency.
Applying 5S to Identify and Organize Bottlenecks
5S is a method used to spot and organize workflow issues. It focuses on Sort, Set in Order, Shine, Standardize, and Sustain.
Sort removes unnecessary items to streamline the workflow. Set in Order ensures essential items are organized efficiently, highlighting bottlenecks. Shine maintains cleanliness and reveals hidden issues. Standardization ensures consistency, and sustaining ensures continuous improvement.
Integrating 5S with constraint management involves identifying, exploiting, subordinating, elevating, and rechecking the bottleneck. This cycle allows continuous problem-solving and bottleneck resolution. Problem-solving techniques and methods like the 5S and Cumulative Flow diagram can effectively manage constraints.
Resolving workflow constraints leads to immediate productivity and efficiency increases. Long-term, it enhances profitability and achieves organizational goals through continuous improvement.
Utilizing Lean Tools for Bottleneck Exploitation
Lean tools can help find and fix workflow problems. One way is the 5S method. It focuses on organizing the workplace for efficiency and cutting waste. It involves sorting, setting in order, systematic cleaning, standardizing, and keeping workplace arrangements.
Also, the Cumulative Flow Diagram can show where workflow problems happen.
The steps for using Lean methods to handle workflow problems are: identify, fix, prioritize, improve, and check again. By finding the problem, fixing it, making other tasks follow the fix, improving the fix’s performance, and checking for new problems, organizations can manage workflow problems well.
Using Lean strategies to handle workflow problems can cut waste, boost productivity, and increase output. This can lower financial risks and keep production running well. It can also lead to more profits and growth for organizations.
Ensuring Lean Processes Are Subordinate to Bottlenecks
Lean processes can be better controlled in a workflow by using practical strategies like the Theory of Constraints methodology. One important way to do this is by recognizing and addressing the most critical limiting factor or bottleneck that hinders the workflow’s best performance. TOC focuses on achieving this by using the Five Focusing Steps, which involve identifying, exploiting, subordinating, elevating, and rechecking the bottleneck.
By following these steps to fix the bottleneck, organizations can ensure that lean techniques prioritize managing bottlenecks in a production environment, leading to improved productivity and less waste. The potential impacts of effectively addressing workflow constraints and ensuring lean processes are controlled by bottlenecks include reduced economic risks, getting rid of traditional accounting distortions, and a methodical approach to driving continuous improvement and performance.
Leveraging Lean Techniques to Enhance Bottleneck Performance
Lean methodologies can help improve manufacturing processes by reducing bottlenecks. The 5S principles – sorting, set in order, shine, standardize, and sustain – can enhance workspace organization and cleanliness, leading to less waste and improved efficiency. Visual tools like Cumulative Flow diagrams can identify bottlenecks and areas for improvement.
Short-term benefits of addressing bottlenecks and using Lean techniques include better flow, reduced lead time, and higher employee morale. Long-term benefits include sustained productivity improvements, less inventory, and increased customer satisfaction.
To optimize bottleneck output and align other processes, organizations can follow the five focusing steps: identifying, exploiting, subordinating, elevating, and rechecking the bottleneck. Problem-solving techniques and the Theory of Constraints can identify root causes and guide the process of eliminating constraints, driving continuous improvement in manufacturing processes.
Impacts of Addressing Workflow Constraints
Short-term and Long-term Effects of Bottleneck Resolution
Resolving bottlenecks in a workflow has short-term effects. These include:
- Increased production speed
- Reduced wait times
- Improved workflow balance
For example, by addressing bottlenecks in manufacturing using the 5S method, companies can decrease idle time, improve material flow, and reduce production line downtime.
Long-term solutions for bottleneck resolution lead to:
- Increased production efficiency and effectiveness
- Sustainable production improvement through the Theory of Constraints
This sustained improvement results in:
- Enhanced output
- Higher throughput
- Overall increased profitability
Effective bottleneck management brings key outcomes such as:
- Cost reduction
- Increased customer satisfaction
- Improved employee morale
Implementing TOC principles can lead to:
- Waste reduction
- Enhanced quality
- A more streamlined and efficient workflow
Addressing bottlenecks yields both immediate and long-lasting positive effects on a company’s operations.
Key Outcomes of Effective Bottleneck Management
Resolving workflow bottlenecks has short-term and long-term effects. In the short term, fixing bottlenecks can immediately improve productivity, efficiency, and reduce waste and risks. In the long term, it leads to sustained improvements in processes, higher throughput, and increased profitability.
Effective bottleneck management results in smoother workflows, reduced waste, higher productivity, and improved economic performance. The impacts can be evaluated through key performance indicators like cycle time reduction, increased throughput, improved on-time delivery, and reduced inventory levels. Tracking financial metrics such as cost reduction and increased profitability provides insight into its effectiveness.
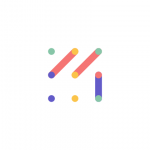
Vizologi is a revolutionary AI-generated business strategy tool that offers its users access to advanced features to create and refine start-up ideas quickly.
It generates limitless business ideas, gains insights on markets and competitors, and automates business plan creation.