The 3 Stages of Process Validation Explained
Have you ever wondered how the products you use every day are guaranteed to be safe and effective? The answer lies in the validation stages of the process.
This article will explain the three crucial stages of process validation:
- Design qualification.
- Installation qualification.
- Operational qualification
Understanding these stages is essential for ensuring the quality and reliability of products in industries such as pharmaceuticals, food and beverage, and manufacturing.
This article will provide a clear and comprehensive explanation, whether you’re a professional in the field or simply curious about the process.
What is Process Validation?
The Three Stages of Process Validation are:
1.Process Design:
- Involves defining a manufacturing process
- Collecting and evaluating data
- Maintaining comprehensive record keeping.
2.Process Validation or Process Qualification:
- Evaluates the designed process
- Ensures consistent and reliable quality
- Collects and evaluates data on all manufacturing stages.
3.Continued Process Verification:
- Involves ongoing validation during production
- Ensures consistent quality
- Requires product sampling, analysis, and verification
These stages ensure quality, efficiency, and safety at each manufacturing step.
They focus on building in quality rather than simply testing the finished product.
Challenges in process validation include:
- Meticulous and comprehensive record-keeping
- Developing contingency plans
- Resolving process drift through ongoing validation
Meeting these challenges is essential for ensuring consistently high-quality products.
What are the 3 stages of process validation?
Stage One: Process Design
The three stages of process validation are essential for pharmaceutical manufacturing and other production processes that aim to produce high-quality and reliable products. These stages must be followed in order.
Stage one is Process Design, which includes research and development to define the manufacturing process. It also involves meticulous record-keeping to meet regulatory requirements.
The second stage, Process Validation or Process Qualification, evaluates the designed process to ensure it can consistently produce quality products. This involves collecting and evaluating data at all manufacturing stages and developing contingency plans for potential issues.
The final stage, Continued Process Verification, involves ongoing validation during production to maintain consistent quality. This includes product sampling, analysis, verification at various points in the process, and logging any anomalies and product quality issues.
Define the Process
Process Validation is collecting and evaluating data from the process design stage through commercial production. This establishes scientific evidence that a process can consistently deliver quality products.
The Three Stages of Process Validation are:
- Process Design: Defined manufacturing process.
- Process Validation or Process Qualification: Evaluate the designed process for consistent quality.
- Continued Process Verification: Ongoing validation during production for consistent quality.
These stages ensure quality by collecting and evaluating data, developing contingency plans for when things go wrong, and detecting/resolving process drift. This process is essential for creating efficiencies and troubleshooting problems in manufacturing.
Identify Critical Quality Attributes
Quality attributes in the pharmaceutical process include physical, chemical, biological, and microbiological factors. These attributes, such as potency, purity, and stability, are vital for ensuring product safety and effectiveness. Identifying and monitoring these attributes helps manufacturers maintain required quality standards. Challenges in this process include comprehensive data collection, contingency planning, and the need for specialized expertise and collaboration.
Identifying these attributes is essential for validating the manufacturing process and consistently delivering high-quality products.
Stage Two: Process Qualification
Process Qualification is the second stage of the Three Stages of Process Validation. Its purpose is to evaluate the process designed in the first stage to ensure it can reproduce consistent and reliable levels of quality.
In this stage, the focus is on collecting and evaluating data on all aspects and stages of the manufacturing process. This includes equipment qualification, ensuring that all equipment used is suitable for its intended use, and contributing to the overall process qualification.
Performance qualification establishes evidence that the process can consistently produce a product meeting its specifications and quality attributes. Both of these components contribute to Process Qualification, ensuring that all aspects of the manufacturing process are thoroughly evaluated and capable of delivering high-quality, reliable products.
This stage also involves developing contingency plans for situations where issues arise, further enhancing the overall process qualification.
Equipment Qualification
Equipment qualification means ensuring a piece of equipment is suitable for its intended use. It’s essential to show that the equipment consistently meets specific standards and quality. This helps to reduce the risk of equipment failure, which could affect the quality of the product. The steps involved in equipment qualification are:
- Installation qualification (IQ): This ensures the equipment is installed correctly and all key parts are in place.
- Operational qualification (OQ): This verifies that the equipment works according to its specifications.
- Performance qualification (PQ): The equipment consistently works according to predetermined criteria and produces quality results.
For example, in pharmaceutical manufacturing, equipment qualification could involve testing and documenting a tablet press machine to ensure it consistently makes high-quality tablets.
Performance Qualification
Performance Qualification is an important part of process validation. It comes after the initial stages and aims to confirm that the production process can consistently produce high-quality products in real operating conditions. This phase helps ensure quality by checking that the whole production process meets set specifications. It involves testing individual processes, systems, and equipment.
During this stage, manufacturers ensure that the process output meets set specifications and the product quality suits its intended use. Challenges at this stage can include identifying consistent process control cycles and detecting variations that affect product quality. Another challenge is creating detailed documentation, as the FDA needs substantial proof of process validation. Also, it’s crucial to ensure that process equipment and utilities are ready for use.
Stage Three: Continued Process Verification
Stage Three: Continued Process Verification ensures that the commercial product’s production process maintains consistent quality. It involves ongoing validation to detect and resolve any process drift. This stage includes product sampling, analysis, and verification at different points in the manufacturing process to maintain quality over time. Employees with quality control training continuously monitor product quality.
Key steps in this stage include keeping detailed records of anomalies and product quality issues and developing contingency plans for unexpected events during production.
Monitor Operations
Process validation involves collecting and evaluating data from the process design stage through commercial production. It ensures that a process consistently delivers quality products.
There are three stages of process validation:
- Process Design: This stage involves defining a manufacturing process and maintaining detailed records. The collected data can be used to improve production processes and troubleshoot problems.
- Process Validation or Process Qualification: This stage evaluates the established process to ensure consistent and reliable quality. It includes collecting data on all aspects of the manufacturing process and developing contingency plans for potential issues.
- Continued Process Verification: This stage involves ongoing validation during production to ensure consistent quality through product sampling, analysis, and verification.
It aims to detect and resolve process drift and requires comprehensive record-keeping.
These stages ensure quality, efficiency, and safety throughout the product lifecycle, not just at the end. They also help detect and resolve process issues and create contingency plans for problems.
Review Data and Adjust
During the continued process verification stage, all aspects of the manufacturing process should be reviewed. This includes product sampling, analysis, and verification at different points in the process. Employees with quality control training are involved in this stage.
A critical part of this stage is detecting and resolving process drift. This means logging anomalies and product quality issues. Reviewing the data can help adjust the process to maintain consistent quality levels.
Analyzing the data helps identify areas where the process may need to be adjusted. Manufacturers can then take corrective actions. Challenges in this stage include manufacturing processes drifting over time, the need for comprehensive record-keeping and data analysis, and the requirement for employees with quality control training.
How Do These Stages Ensure Quality?
Stage One Explained
Stage One is called Process Design. It helps define a manufacturing process for a product during the research and development phase. This stage includes collecting and evaluating data and keeping detailed records. The goal is to set the requirements for a safe and efficient manufacturing process to ensure quality. The data collected can also improve production processes, make them more efficient, and solve problems.
Some challenges might arise in Stage One, such as ensuring that the defined process meets quality standards, identifying potential failure points, and creating backup plans for unexpected situations.
Build the Foundation for Quality
The process validation has three stages:
- Process Design.
- Process Validation or Process Qualification.
- Continued Process Verification
These stages help ensure quality by collecting and evaluating data throughout manufacturing.
It establishes scientific evidence that the process can consistently deliver quality products.
Common challenges in process validation are process drift, maintaining consistent quality, and developing contingency plans for potential issues during manufacturing.
Stage Two Explained
In Stage Two, we evaluate and qualify the process designed in Stage One, ensuring consistent and reliable quality. We collect and evaluate data on all aspects and stages of the manufacturing process, such as equipment, materials, and personnel. We also develop contingency plans for things that go wrong, such as equipment failure or material shortages. This process is essential for ensuring the reproducibility of the added quality.
The main aim is to develop and maintain a process that consistently meets quality standards. Challenges that may arise include equipment malfunction, material shortages, and personnel not following established protocols. Therefore, careful and thorough data collection is necessary to address these challenges and maintain the consistency and reliability of the manufacturing process.
Test and Confirm the Process
Process validation involves collecting and evaluating data. It occurs from the process design stage through commercial production and aims to show that a process can consistently produce quality products.
There are three stages: process design, process validation (or process qualification), and continued process verification. These stages ensure quality by collecting and evaluating data on all aspects of the manufacturing process. This helps verify consistency and reliability when producing high-quality products.
These stages also involve developing plans for potential problems, ongoing validation during production, and detecting and resolving process drift to maintain consistent quality.
Record-keeping is crucial. It includes logging anomalies and issues with product quality. This ensures that quality standards are consistently met throughout the product’s lifecycle.
Stage Three Explained
Stage Three of process validation is called Continued Process Verification. Its purpose is to ensure that the process designed and qualified in the previous stages continues to deliver consistent quality. This involves ongoing validation during commercial product production to detect and resolve process drift.
Stage Three involves product sampling, analysis, and verification at various points in the manufacturing process to maintain quality over time. It also requires employees to have quality control training and comprehensive record-keeping, including any anomalies and issues with product quality.
The key components of Continued Process Verification include product sampling, analysis, verification at various points in the manufacturing process, and the involvement of employees with quality control training. Hence, Stage Three is essential for maintaining consistency and reliability in manufacturing.
Maintain Quality Over Time
Process validation is vital for maintaining product quality. It ensures that a process consistently delivers high-quality products, which is crucial for pharmaceutical compliance.
The FDA and EMA outline a process focusing on built-in quality, efficiency, and safety measures at every manufacturing stage. This approach ensures that quality is measured at the end and maintained throughout.
Challenges like meeting regulatory requirements and planning for unexpected errors can affect quality. To address this, organizations can use collected data to optimize production, create efficiencies, identify areas for improvement, and troubleshoot problems. Comprehensive data records are required for each stage to ensure sustained quality over time.
Challenges in Process Validation
Common Issues in Stage One
Issues that can arise in Stage One of process validation include inadequate record-keeping and failure to optimize the production process.
Research and development in Stage One require meticulous and comprehensive record-keeping from a regulatory point of view. Setting realistic parameters for manufacturing the product is vital, although challenging.
The data collected in this first stage can be used to optimize the production process and create efficiencies.
In Stage Three of process validation, maintaining quality over time becomes challenging. Ongoing validation during production is required to ensure consistent quality and detect and resolve process drift.
Comprehensive record-keeping is necessary, and ongoing product sampling, analysis, and verification are vital to ensure consistent reliability.
Setting Realistic Parameters
Setting realistic parameters in process validation is essential. It ensures that the manufacturing process consistently produces high-quality pharmaceutical products.
Companies can establish the boundaries within which their processes should operate. This helps them detect and address any deviations that might impact product quality.
Realistic parameters during the process design stage can help companies identify and mitigate potential bottlenecks, which could affect the efficiency and safety of the manufacturing process.
However, setting realistic parameters can present challenges. This includes balancing the need for stringent control with the flexibility to innovate and improve existing processes.
Companies need to strike the right balance. This is crucial to ensuring that the validation process effectively delivers high-quality pharmaceutical products.
Common Issues in Stage Two
Common issues often relate to ensuring consistent and reliable quality during the Process Qualification stage of Process Validation. This includes collecting and evaluating data on all aspects and stages of the manufacturing process, including raw materials, equipment, personnel, and environmental conditions. It’s also useful to develop contingency plans for unexpected situations.
Organizations typically adjust to test results and challenges encountered during this stage by using the data collected to optimize their production process, create efficiencies, and troubleshoot problems. This may involve adjusting various elements of the manufacturing process and developing new strategies to ensure consistent and reliable quality in their products.
In Stage Three of process validation, challenges often relate to ensuring continuous improvement and detecting and resolving process drift. One strategy for ensuring continuous improvement is ongoing validation during commercial product production to ensure the process delivers consistent quality. This involves product sampling, analysis, and verification at various points in the manufacturing process, as well as keeping comprehensive records and logging anomalies and issues with product quality.
Adjusting to Test Results
Effective adjustment to test results in the stages of process validation involves thorough data collection and comprehensive evaluation. The first stage, Process Design, allows for developing a product manufacturing process, thus providing the opportunity to adjust to test results early on.
For example, through meticulous record-keeping, any deviations or issues can be identified and promptly addressed, ensuring the quality and reliability of the process. The second stage, Process Validation or Process Qualification, presents challenges such as identifying potential problems and developing contingency plans. These challenges provide opportunities for continuous improvement, leading to more reliable and effective adjustments to test results. Lastly, the third stage, Continued Process Verification, plays an essential role in the ongoing validation during production, ensuring that necessary adjustments are made to maintain consistent quality.
Through these stages, the process validation ensures quality by continually adjusting to test results, thus delivering high-quality, reliable products.
Common Issues in Stage Three
Common issues in Stage Three of process validation:
- Continuous monitoring is needed to ensure consistent quality over time.
- Thorough collection and evaluation of data is essential.
- Product sampling, analysis, and verification of various manufacturing processes.
- Employees with quality control training are required to monitor operations and review data.
- Detecting and resolving process drift is essential for maintaining quality over time.
- Comprehensive record-keeping is needed to log anomalies and product quality issues.
- Contingency plans for possible deviations in the manufacturing process should be developed.
- Continued process verification is crucial in pharmaceutical manufacturing and other production processes.
Continuous Improvement
The stages of process validation are essential for continuous improvement. They help ensure that the production process consistently delivers quality products. By collecting and evaluating data on all aspects of the manufacturing process, the company can identify areas for improvement, optimize production processes, create efficiencies, and troubleshoot problems.
One of the main aims of Continuous Process Verification, the last stage, is to detect and resolve process drift. Challenges encountered in process validation include variations in raw materials, equipment, environmental conditions, or human error. These can be addressed by developing contingency plans, using comprehensive record-keeping, providing quality control training to employees, and analyzing and verifying the process at various points in the manufacturing process.
The process can work smoothly and consistently by addressing these challenges, leading to continuous improvement.
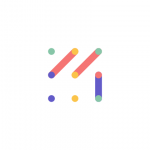
Vizologi is a revolutionary AI-generated business strategy tool that offers its users access to advanced features to create and refine start-up ideas quickly.
It generates limitless business ideas, gains insights on markets and competitors, and automates business plan creation.