Understanding Kaizen Methodology
Imagine a world where small, continuous improvements add up to significant change. This is the world of Kaizen methodology. Kaizen means “change for the better” in Japanese. It focuses on making small, incremental improvements in processes and systems. Companies worldwide use Kaizen to increase efficiency, reduce waste, and improve their bottom line.
Understanding the principles and practices of Kaizen is important for businesses aiming to stay competitive in today’s fast-paced, ever-changing global market.
Exploring the Core Concept of Kaizen
Implementing the core concept of Kaizen involves encouraging small, frequent improvements to work processes by all employees. This challenges the notion of “that’s just the way we do things” and aims for efficient and standardized processes.
The 10 guiding principles of Kaizen contribute to continuous improvement by emphasizing the importance of seeking improvement, making incremental changes, and encouraging active employee participation. They also focus on standardizing processes and fostering a culture of continual improvement.
Adopting Kaizen in different organizational settings has merits that include significant results and fostering employee engagement. Potential drawbacks may include resistance to change and the challenge of maintaining momentum for ongoing improvements.
Implementing Kaizen: The Fundamental Steps
To implement Kaizen, organizations should first establish a culture of continuous improvement. This means encouraging small, incremental changes in work processes and involving all employees at every level. It’s about challenging the status quo of “that’s just the way we do things” and aiming for standardized and efficient processes.
Practical steps include creating process and deployment flowcharts to identify areas of waste. Organizing Kaizen diagrams and value stream maps can help drive improvements. It’s also important to prioritize employee engagement and create a system for soliciting and implementing employee suggestions for process improvement.
The Kaizen Framework: A Guide for Continuous Improvement
The Kaizen Framework is about making small, continuous improvements in work processes. It involves eliminating waste, standardizing processes, and prioritizing quality.
All employees at every level of the organization are encouraged to challenge existing practices and work towards more efficient and standardized processes.
To implement Kaizen, organizations can start by visualizing current processes through process and deployment flowcharts. This helps in identifying areas for improvement and reducing waste.
Using Kaizen diagrams and value stream maps can further help in identifying areas for improvement and getting employees engaged.
Real-world success stories of organizations using the Kaizen Framework show significant improvements in productivity, product quality, and employee morale.
Companies have achieved success by continuously making small, positive changes to processes, leading to sustained success and improved customer satisfaction.
The 10 Guiding Principles of Kaizen
Principle 1: Eliminate Waste
The first principle of Kaizen is to identify and eliminate waste within an organization. This can be overproduction, excess inventory, unnecessary motion, waiting times, overprocessing, defects, and underutilized skills.
By getting rid of these wasteful activities, the organization can continuously improve and increase efficiency. Practical strategies and tools to achieve this include building process and deployment flowcharts to see current processes, detecting waste, using Kaizen diagrams, and involving all employees in frequent improvements.
These small, ongoing changes can lead to big improvements, engage employees, and make the operation more standardized and efficient.
Principle 2: Standardization
Standardization helps implement Kaizen principles. It makes work processes efficient and consistent. Organizations can cut waste, remove unnecessary steps, and boost productivity by standardizing processes. This is important for continuous improvement and Kaizen, as it sets a baseline for finding areas to improve and measuring progress. Standardizing processes also encourages a culture of continuous improvement by giving employees a clear framework to follow, promoting better teamwork.
Standardizing processes has big benefits for continuous improvement and Kaizen. It leads to better quality, fewer errors, and happier customers. With standardized processes, organizations can streamline operations and achieve more consistency in their products or services. This results in cost savings and better efficiency, leading to improved financial performance and competitiveness.
To make sure standardized processes stay effective in their Kaizen efforts, organizations need to involve employees. This can happen through training, clear guidelines, and regular check-ins to ensure adherence to standardized processes. Listening to employee feedback and making adjustments when needed helps keep standardized processes effective in the long run. By creating a culture where standardization is valued and continuously improved, organizations can ensure the sustainability of their Kaizen initiatives.
Principle 3: Quality First
The concept of Kaizen emphasizes “Quality First.” This means consistently delivering high-quality products and services to achieve continuous improvement. Organizations prioritize quality by standardizing processes, reducing waste, and addressing defects or inefficiencies. They use strategies like process flowcharts, value stream maps, and Kaizen events to detect and eliminate errors.
To maintain this focus on quality, organizations invest in training employees, setting clear quality standards,and implementing quality control measures. By integrating quality management into Kaizen, organizations can drive continuous improvement while delivering high-quality products and services.
Principle 4: The 5S Framework in Kaizen
The 5S Framework supports Kaizen goals. It organizes workplace, cleanliness, and standardization. The framework includes Sort, Set in Order, Shine, Standardize, and Sustain. It aims to reduce waste and maximize efficiency.
To implement the 5S Framework in Kaizen:
- Declutter and remove unnecessary items (Sort).
- Organize essential items for workflow (Set in Order).
- Clean and inspect the workplace (Shine).
- Establish standardized procedures (Standardize).
- Uphold 5S practices consistently (Sustain).
The 5S Framework fosters continuous improvement. It promotes discipline, teamwork, and employee involvement. This leads to increased productivity, safety, and morale. It contributes to ongoing process and procedure enhancement.
Sort (Seiri)
The Sort (Seiri) step in the 5S Framework of Kaizen helps create an organized and efficient workplace. It does this by getting rid of unnecessary items, tools, and materials. Getting rid of unnecessary items reduces clutter and cuts down the time spent looking for tools or materials. This makes the workplace more productive and safer.
Implementing Sort (Seiri) as part of the Kaizen process has many benefits, like improved workflow and process efficiency, cost reduction, and increased employee satisfaction. A decluttered workspace from Sort (Seiri) makes it easier to spot issues and areas for improvement, which fits with Kaizen’s philosophy of continuous improvement. Lastly, Sort (Seiri) also leads to a visually organized workplace, boosting employee morale and promoting high standards.
Set in Order (Seiton)
“Set in Order (Seiton)” is an important part of the 5S Framework of Kaizen.
Its purpose is to organize the work environment by arranging tools, equipment, and materials in a way that makes them easily accessible, reducing wasted time and effort.
By assigning specific locations for items and clearly labeling them, “Set in Order (Seiton)” helps to reduce clutter and improve workplace organization, thus enhancing safety.
Practical strategies for applying “Set in Order (Seiton)” include decluttering work areas, creating visual cues like shadow boards for tools, and using color-coding systems.
These strategies help employees find what they need quickly, maintain a clean workspace, and contribute to the overall efficiency and productivity of the organization.
Shine (Seiso)
“Shine (Seiso)” is part of the 5S Framework in Kaizen. It focuses on cleanliness and orderliness in the workplace. This concept is important for maintaining a high standard work environment and supports the principle of quality first in Kaizen.
“Shine (Seiso)” also helps in implementing Kaizen by promoting a clean and organized workspace. This is essential for identifying waste and inefficiency. It allows visualization of processes and detection of irregularities.
Incorporating “Shine (Seiso)” ensures that work areas are conducive to continuous improvement and efficiency in organizations.
Standardize (Seiketsu)
One way to standardize processes within an organization is by developing clear and concise work standards. These standards outline precise steps and expectations for each task or process. Visual aids, such as diagrams or flowcharts, can be used to ensure consistency in how tasks are performed.
Implementing training programs to educate employees on the standard procedures and regularly updating these standards as new improvements are identified can help maintain consistency and sustainability in the workplace.
By doing so, employees can better understand and adhere to the established guidelines, leading to improved productivity and quality.
The potential benefits of implementing the Standardize (Seiketsu) principle in Kaizen include reducing errors, enhancing efficiency, and creating a culture of continuous improvement where everyone is actively involved in maintaining and improving standardized processes.
This approach contributes to a more organized and systematic work environment that supports the overall goal of continuous improvement.
Sustain (Shitsuke)
The concept of “Sustain (Shitsuke)” can be integrated into the organization’s daily operations by:
- Creating standardized work procedures.
- Providing regular training and reinforcement.
- Developing a system for monitoring and maintaining the changes.
Strategies such as visual management, regular communication, and accountability can ensure that the improvements made through Kaizen are sustained over time.
Engaging and motivating employees to sustain the changes can be achieved by:
- Involving them in the improvement process.
- Recognizing and rewarding their contributions.
- Fostering a culture of continuous improvement and innovation.
By implementing these strategies, organizations can successfully embed the principle of “Sustain (Shitsuke)” into their daily operations and achieve long-term, sustainable improvements through Kaizen methodology.
Understanding Different Types of Kaizen Events
Kaizen events come in different types: rapid improvement events (RIEs), focused improvement events, and process improvement events. RIEs are short-term initiatives for tackling specific issues, while focused improvement events target particular aspects like reducing setup times. On the other hand, process improvement events have a wider scope, focusing on improving entire processes.
The Continuous Cycle of Kaizen
Kaizen is a continuous cycle involving small, ongoing positive changes leading to significant improvements in work processes. It includes identifying areas for improvement, brainstorming solutions, implementing changes, and evaluating the results.
Encouraging all employees at all levels to contribute fosters a culture of efficiency and standardized processes. This approach challenges accepting inefficiencies as “the way we do things” and promotes continuous improvement.
Challenges include the need for ongoing dedication and commitment, resistance to change, and potential complacency after initial improvements. However, Kaizen drives employee engagement, reduces waste, and achieves significant results through frequent improvements.
The Merits and Drawbacks of Adopting Kaizen
Implementing Kaizen in an organization has potential benefits. This includes increased efficiency, streamlined processes, and a culture of continuous improvement. It also fosters employee engagement and empowers staff to make positive changes, resulting in higher productivity and reduced waste.
However, some challenges associated with adopting Kaizen may include resistance to change, initial time investment, and the need for sustained commitment. Organizations can address these challenges by providing comprehensive training and support for employees, promoting open communication channels for feedback, and establishing a clear roadmap for the implementation process.
By maximizing the merits of Kaizen through effective leadership and strategic planning, organizations can overcome these challenges and create a culture of continuous improvement that drives long-term success.
Real-World Kaizen: Success Stories and Examples
Many companies have used Kaizen principles to make big improvements.
For example, a manufacturing company used Kaizen to cut waste and work better, leading to a 20% increase in productivity. A healthcare organization also used Kaizen to make patient care smoother, cutting wait times by 30% and making patients happier. These real-life examples show how Kaizen has a positive impact on different industries. Companies have used Kaizen to get better over time and be successful in the long run by encouraging innovation and involving employees. By making small, steady changes, companies have made lasting improvements in their work and business results. For instance, an automotive company used Kaizen principles in their production, leading to a 15% drop in mistakes and a 25% rise in efficiency. These case studies show the real benefits of using Kaizen across industries, emphasizing how effective it is in being excellent and giving customers great value.
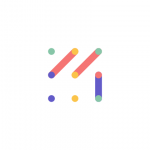
Vizologi is a revolutionary AI-generated business strategy tool that offers its users access to advanced features to create and refine start-up ideas quickly.
It generates limitless business ideas, gains insights on markets and competitors, and automates business plan creation.