What are Kaizen Beliefs? Your Quick Guide
Kaizen beliefs are an important concept in continuous improvement. They have been used by many successful organizations. In this guide, we will explore the basic principles behind Kaizen beliefs and how they can be applied to improve different areas of life.
Whether you are a business owner, student, or simply someone looking to make positive changes, understanding Kaizen beliefs can be helpful in today’s fast-paced world. Let’s dive in and discover what Kaizen beliefs are all about.
The Pillars of Kaizen Philosophy
Management’s Role in Fostering Kaizen
Management plays an important role in fostering a culture of continuous improvement through Kaizen. They empower employees to drive change by promoting open communication, encouraging employee involvement in decision-making, and providing opportunities for skill development and growth.
Additionally, management is responsible for implementing and sustaining the Kaizen 5S framework for order and efficiency. This involves creating a work environment where processes are standardized and organized to eliminate waste and maximize productivity.
However, management should be aware of potential challenges and resistance to change when fostering Kaizen in the organization. This could include employee pushback, fear of the unknown, and a reluctance to embrace new ways of working.
Therefore, it is essential for management to proactively address these challenges through effective communication, training, and leading by example.
Empowering Employees to Drive Change
To empower employees to lead change, management can:
Provide regular training and development opportunities to enhance skills and knowledge.
Offer leadership seminars, value stream analysis, and agile organization training for continuous improvement.
Encourage an open and inclusive workplace culture that supports and recognizes contributions.
Establish a Kaizen event process involving employees in small, ongoing positive changes to foster innovation.
Offer sector-specific training and mentoring to support and encourage employee contributions.
Create an environment that values employee feedback and input in all aspects of the business.
The Kaizen Path: A Continuous Improvement Cycle
Kaizen events involve various activities such as value stream analysis, office improvement, and project management, in a continuous improvement cycle.
The Kaizen 5S framework focuses on sorting, setting in order, shining, standardizing, and sustaining to promote order and efficiency in the workplace. This leads to a more organized and productive environment.
When assessing the impact of Kaizen on an organization, potential benefits include increased efficiency, improved quality, and higher employee morale. However, there may be tradeoffs like resistance to change, initial implementation costs, and the need for ongoing commitment and resources to sustain the improvements.
Familiarizing with Different Kaizen Event Types
Point kaizen: Small, Incremental Changes
Implementing small, incremental changes through point kaizen can greatly contribute to overall process or system improvement. By making small adjustments and improvements, organizations can achieve ongoing enhancement in efficiency, productivity, and quality.
This approach allows for continuous, sustainable improvement and creates long-lasting positive change within the organization. Additionally, point kaizen can lead to several potential benefits, such as increased employee engagement, better problem-solving capabilities, and a culture of continuous improvement.
Empowering employees to drive small, incremental changes through point kaizen can be achieved by providing training, creating a supportive work environment, and encouraging open communication and collaboration.
By involving employees in the improvement process, organizations can harness the collective knowledge and creativity of their workforce, leading to more impactful and sustainable changes.
System kaizen: Overhauling Entire Systems
System kaizen is a strategic approach that involves making regular, small improvements and implementing changes gradually.
To overhaul entire systems through system kaizen, an organization would apply an action plan that focuses on leveraging small, ongoing changes.
This process relies on carefully designed Kaizen events and a dedication to developing a continuous improvement culture.
Leading organizations use system kaizen to drive significant change by aligning it with Standardized Work and scientifically implementing changes within their manufacturing processes.
When undertaking system kaizen initiatives, important considerations and best practices include emphasizing the philosophy of continuous improvement, ensuring thorough communication and feedback, and using strategy & cultural change efforts.
These practices help overcome resistance to change and promote sustainable transformation initiatives within the organization.
Line kaizen: Enhancing Production Line Efficiency
Line Kaizen is a strategy to improve production line efficiency. It focuses on making small, continual improvements to the manufacturing process. Organizations can use strategies like value stream analysis and Standardized Work to identify and address inefficiencies.
By integrating Line Kaizen into the continuous improvement cycle, organizations ensure long-term efficiency gains. This approach develops a culture of ongoing improvement, aligning with the philosophy of Kaizen.
Organizations can achieve regular incremental improvements by using this approach and develop a scientific approach to making changes, ultimately achieving a more efficient production line.
The strategy not only emphasizes action but also serves as a philosophy. This creates a workplace culture that welcomes continuous improvement and supports the methodical improvement of processes, driving long-term success and adaptability within the organization.
Plane kaizen: Cross-Departmental Improvements
Cross-departmental improvements can be implemented through plane kaizen by fostering a culture of collaboration and shared responsibility. By encouraging employees from different departments to work together on identifying and solving problems, companies can achieve comprehensive and sustainable improvements in their processes.
The benefits of implementing plane kaizen for cross-departmental improvements include increased efficiency, reduced waste, improved communication, and a greater sense ofteamwork and ownership. However, potential challenges and resistance to change may arise when implementing plane kaizen for cross-departmental improvements, such as conflicts of interest between departments, lack of buy-in from employees, and the need for significant time and resource investment. Overcoming these challenges will require strong leadership, effective communication, and a commitment to developing a culture of continuous improvement throughout the organization.
Cube kaizen: Organizational-Wide Initiatives
Cube Kaizen is about making small, ongoing improvements across the whole organization. It’s all about creating a culture of constant improvement and making sure it lines up with Standardized Work and a scientific approach. One way to make this happen is by using the Kaizen 5S framework, which involves sorting, setting things in order, systematic cleaning, standardizing, and sustaining.
But there can be challenges, like resistance to change, employees not getting involved, and not enough supportfrom leaders.
Implementing the Kaizen 5S Framework for Order and Efficiency
Sorting: Eliminating Unnecessary Items
Sorting is very important in the Kaizen 5S framework. It helps to eliminate unnecessary items in the workplace. Techniques like red-tagging are used to identify and remove unnecessary items during sorting. This leads to a clean and organized workspace, improving efficiency, safety, and productivity. It also encourages a culture of continuous improvement and employee engagement.
This waste removal is a key part of the Kaizen methodology, supporting the goal of making small, ongoing positive changes within an organization.
Set in Order: Organizing the Workplace
The “Set in Order: Organizing the Workplace” is an important part of the Kaizen philosophy. It focuses on creating an organized, clutter-free environment that helps with efficiency and continuous improvement.
Organizing the workplace makes it easy for employees to find tools, materials, and information, which leads to a smoother workflow. The key principles include sorting and removing unnecessary items, setting locations for tools and materials, and using clear visual indicators to maintain order.
This phase of the Kaizen 5S framework improves efficiency and productivity by reducing time wasted searching for tools, minimizing errors, and creating a safer work environment. It also helps standardize work practices and ensures consistent application of Kaizen principles throughout the organization.
Shine: Cleaning and Inspecting Work Areas
Employees can easily clean and inspect work areas as part of the Kaizen philosophy by adding these tasks to their daily routines. They can:
- Create a standard checklist for cleaning and inspection activities.
- Set aside time at the beginning or end of each shift for these tasks.
- Hold regular training sessions to emphasize the importance of maintaining a clean and organized work environment.
Integrating “Shine: Cleaning and Inspecting Work Areas” into the Kaizen framework can result in improved safety, increased efficiency, and a higher level of overall workplace organization. To ensure that work areas are consistently clean and well-maintained in line with Kaizen principles, strategies may include conducting regular audits, using visual management techniques (like color-coding and labeling), and empowering employees to take ownership of their workspaces through individual and team-based initiatives.
Standardize: Creating Consistency in Practices
Implementing the standardization process in the Kaizen philosophy involves some key strategies:
- Define and document standardized work procedures.
- Create visual aids and checklists.
- Provide thorough training to employees.
These strategies ensure that all team members understand and follow the same set of practices, contributing to consistency.
The Standardize phase of the Kaizen 5S Framework is critical for fostering a culture of continuous improvement and efficiency. By establishing clear, uniform work processes, this phase sets standard operating procedures, eliminates variations, and streamlines workflows, ultimately boosting productivity and reducing waste.
While standardizing practices is essential for improvement, it may face resistance from employees used to existing workflows. Challenges like lack of buy-in from management, fear of change, and limited resources for training and implementation can hinder the standardization process. Overcoming these hurdles requires effective communication, employee involvement, and strong leadership support.
Sustain: Maintaining and Improving Standards
Organizations can maintain Kaizen standards by making regular, small improvements to the manufacturing process. This involves creating a culture of continuous improvement within the organization, following standardized work, and embracing the scientific approach of Kaizen.
Improving standards in the Kaizen philosophy can be achieved by using a Kaizen action plan in the context of a Kaizen event process. This approach fosters a culture of continuous improvement and provides a structured way to enhance standards.
Continuous improvement in the Kaizen philosophy is essential for maintaining and enhancing standards by fostering ongoing positive changes. This supports the idea of a continuous improvement cycle and demonstrates a commitment to improving the organization over time.
Evaluating Kaizen’s Impact: Benefits Versus Tradeoffs
Enhanced Productivity and Efficiency
The principles of Kaizen philosophy can be used to enhance productivity and efficiency in the workplace. This is done by promoting continuous improvement through small, incremental changes.
Encouraging all employees to seek out and suggest improvements in their work processes fosters a culture of collaboration and innovation.
Management is essential in fostering Kaizen. They empower employees to drive change by providing the necessary resources, support, and training to execute their ideas.
In addition, management must be open to feedback and actively participate in the improvement process to set an example for others.
Implementing Kaizen for improved productivity and efficiency can lead to reduced waste, increased employee engagement, and improved quality.
However, some tradeoffs and challenges may arise, such as resistance to change, and the need for ongoing commitment and investment in training and empowerment.
Cultural Shifts Towards Better Quality
Cultural shifts towards better quality can be encouraged by implementing strategies like Kaizen. Kaizen promotes continuous improvement in the manufacturing process. Management plays a key role in driving these shifts by providing support and resources for employees to embrace the Kaizen philosophy. Effective leadership and communication are essential in cultivating a culture of continuous improvement and empowering employees.
Engaging employees, encouraging their input, and recognizing their efforts can create a motivating environment. This leads to a more efficient manufacturing process and better-quality products and services.
Potential Challenges and Resistance to Change
Implementing change through the Kaizen philosophy can have challenges. These may include employee resistance, lack of top management commitment, and difficulty sustaining momentum.
Employee resistance can show as decreased productivity, increased absenteeism, or negative attitudes toward the new process. To address this, organizations can:
- Create open communication channels
- Provide training and support
- Involve employees in decision-making
Top management commitment can be improved by:
- Ensuring leaders are actively engaged
- Setting clear goals
- Providing necessary resources
Sustaining momentum can be challenging, but organizations can:
- Employ regular monitoring
- Provide feedback
- Recognize employee contributions
Real-World Applications: Kaizen Success Stories
Real-world applications of the Kaizen philosophy have proven successful in various industries. Companies have seen improvements through regular, incremental changes in their manufacturing processes.
Empowered employees drive change by implementing Kaizen initiatives. This has led to benefits such as increased employee engagement, improved teamwork, and a strong sense of ownership in the continuous improvement process.
Organizations who have adopted Kaizen have experienced increased productivity, reduced waste, improved quality, and better customer satisfaction.
However, there are also tradeoffs, such as the need for significant time investment, potential resistance to change, and the necessity of thorough training in the Kaizen principles.
Starting the Kaizen Journey: A Quick Start Guide
Developing a Kaizen Checklist for Implementation
A Kaizen checklist for implementation should include:
- Clear goals and objectives
- Identification of improvement areas
- Involvement of all team members
- Regular review and monitoring
- Feedback system for continuous improvement.
The checklist should be structured with specific action items, deadlines, responsible team members, and regular progress tracking.
To evaluate the effectiveness of the Kaizen checklist, consider:
- Achievement of set objectives
- Level of team engagement
- Number of successful improvement initiatives
- Overall impact on the manufacturing process.
This evaluation will identify areas for further improvement and refine the checklist for future implementation cycles.
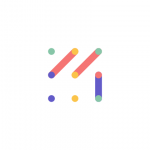
Vizologi is a revolutionary AI-generated business strategy tool that offers its users access to advanced features to create and refine start-up ideas quickly.
It generates limitless business ideas, gains insights on markets and competitors, and automates business plan creation.