Why Toyota’s Way of Making Cars Wins
Toyota is known for its unique approach to making cars, which sets it apart in the competitive automotive industry. The company focuses on efficiency, innovation, and attention to detail, making it a leader in the market. Its method has proven successful repeatedly. Let’s see why Toyota’s way of making cars is winning.
The Beginnings of the Toyota Production System
The Toyota Production System (TPS) was created after World War II in Japan to make production more efficient. Japan’s culture and history, which focused on consistency and attention to detail, greatly influenced the development of TPS. TPS stood out from traditional manufacturing by focusing on reducing waste, using space effectively, and having no extra inventory. These differences led to better efficiency, quality, and customer satisfaction compared to other manufacturing systems.
TPS’s benefits like sustainability, improved customer satisfaction, and higher profits helped Toyota outperform rivals during supply chain disruptions, making TPS a key manufacturing system.
Core Principles of the Toyota Production System
Jidoka: Automation with a Human Touch
Jidoka is a key part of the Toyota Production System. It allows machines to stop automatically when defects are found, so human workers can fix the issues. This combination of automation and human intervention boosts equipment effectiveness and production quality.
Integrating Jidoka brings many benefits, like less work waste, efficient space use, and zero inventories. This improves production efficiency by cutting hidden losses, optimizing workspace layout, and reducing inventory costs.
Moreover, Jidoka enhances production quality and efficiency by making better use of workspaces, resulting in higher product quality and overall productivity. It also boosts customer satisfaction by reducing work waste, increasing effectiveness, and ultimately improving financial returns and customer loyalty.
Just-In-Time: The Right Parts at the Right Time
“Just-In-Time” aims to produce or procure the exact quantity of parts needed precisely when they are needed. This approach results in zero inventories, eliminates inventory handling costs, and reduces the risk of outdated or excess stock. It also improves efficiency and reduces waste by establishing standardized work and eliminating seven types of work waste, unevenness, and overburden within the processes.
Implementing a “Just-In-Time” system in manufacturing operations offers several benefits, including proper utilization of physical spaces, improved quality, zero inventories, enhanced customer satisfaction, increased profits, and sustainability. It also leads to better financial profits by focusing on customer suggestions to reduce work waste and increase effectiveness, thus delivering improved customer service and better quality products.
Lastly, “Just-In-Time” contributes to increased efficiency and reduced waste by eliminating work waste, standardizing work, and utilizing available workplace space effectively. This brings about improved business operations efficiency, a clean and organized workplace, reduced waiting and transportation times, and better sustainability in the market.
Kaizen: Continuous Improvement
Kaizen is a part of the Toyota Production System. It focuses on continuously improving manufacturing processes. This means getting rid of work wastes, using physical spaces efficiently, having zero inventories, improving the quality, making customers happier, and ultimately making more profits.
This concept promotes small, constant improvements in processes to make them more efficient and effective. TPS and Kaizen work together to find and get rid of inefficiencies, make the work environment safer, and enhance it.
There are key principles and practices. They include getting rid of the seven types of work waste (Muda), promoting standardized work, making things just-in-time, and prioritizing customer satisfaction.
Kaizen has had a big influence on lean manufacturing and operational excellence. It has done this by setting up a culture of continuous improvement, getting employees to help with innovation and problem-solving, and making a customer-centered approach.
Toyota’s success, even during supply chain disruptions, shows that TPS and the principles of Kaizen are still good strategies for operational excellence and staying competitive in the manufacturing world.
Toyota Production System Advantages in Action
Increase in Efficiency and Productivity
- A company can measure the increase in efficiency and productivity by implementing Toyota Production System principles. This includes eliminating work wastes, creating standardized work and processes, and using physical spaces and inventories properly. These measures improve business operations and processes, leading to visible improvements in the organization’s productivity.
- To continually improve and sustain efficiency and productivity, strategies like the zero inventories principle and proper utilization of available workplace can be implemented within a manufacturing process. The ‘Just-in-time’ approach of the Toyota Production System reduces the cost of inventory handling and waiting time, continually improving efficiency and productivity.
- The Toyota Production System reduces waste and improves sustainability in manufacturing through the zero wastes, zero safety issues, and zero inventories approach. This fosters better sustainability in the market. The system also targets customer suggestions to reduce work wastes, improve effectiveness, and increase customer service, all of which reduce waste and contribute to improved sustainability.
Reduction of Waste and Improved Sustainability
Implementing Toyota Production System and lean manufacturing helps organizations reduce waste in manufacturing processes. This improves sustainability by minimizing environmental impact. These strategies eliminate work wastes, establish standardized work, and efficiently utilize physical spaces. TPS and lean manufacturing also support sustainable practices like recycling and renewable energy.
By using these methods, businesses can move towards zero waste, zero safety issues, and zero inventories for better overall sustainability. Toyota’s success during supply chain disruptions shows the effectiveness of TPS in reducing waste and improving sustainability in manufacturing.
Flexibility and Adaptability in Manufacturing
Flexibility and adaptability in the manufacturing process improve efficiency and productivity. They do this by eliminating work waste and establishing standardized work in the workplace.
Proper utilization of physical spaces also plays a role. This leads to easier, safer, cleaner, and more organized workplaces.
Additionally, zero inventories, improved quality, and improved customer satisfaction are achieved through the implementation of flexibility and adaptability in manufacturing processes.
Manufacturers can successfully implement flexibility and adaptability in their production systems by focusing on zero work waste, proper utilization of physical spaces, zero inventories, improved quality, improved customer satisfaction, improved profits, and sustainability.
Flexibility and adaptability in manufacturing contribute to high quality and customer satisfaction. They do this by improving product quality, delivering better quality products to customers, and retaining loyal customers.
High Quality and Customer Satisfaction
The Toyota Production System contributes to high quality in manufacturing by focusing on the proper utilization of physical space within the workplace. By implementing TPS and lean manufacturing, companies see improved efficiency of business operations and processes, allowing employees to use their potential for increased productivity and effectiveness. This, combined with a focus on research and innovation, leads to improved overall product quality.
Additionally, the elimination of work wastes and establishment of standardized work within the processes further ensures high-quality manufacturing.
The Toyota Production System prioritizes customer satisfaction by targeting customer suggestions to reduce work wastes and increase effectiveness. This approach not only leads to improved customer service and better quality products but also fosters customer loyalty and retention of good customer relationship, leading to increased customer satisfaction. Toyota’s focus on customer feedback and using it to inspire research and innovation for products further reinforces its commitment to customer satisfaction and loyalty.
Lean Manufacturing: Toyota’s Approach to Operational Excellence
The Lean Methodology: Minimizing Waste, Maximizing Value
The Lean Methodology maximizes value in manufacturing processes. It does this by:
- Eliminating work wastes
- Implementing standardized work
- Ensuring proper utilization of physical spaces
As a result, this leads to:
- Improved efficiency
- Workplace safety
- Reduced waiting and transportation times
- Zero inventories
- Increased product quality
Employees play an important role in this. They utilize their potential for:
- Research
- Innovation
- Creating more productive and effective things in the workplace
Toyota’s manufacturing strategy has evolved. It now incorporates innovations and advancements in production.
It continues to maintain the principles of the Toyota Production System. Despite supply chain disruptions, TPS continues to be a key reason for Toyota’s outperformance of rivals. This proves that it is alive and well.
Additionally, it focuses on sustainability in the market.
The Role of Employees in Lean Manufacturing
Employees in Lean Manufacturing make a big impact on the principles of Jidoka, Just-In-Time, and Kaizen. They find and fix defects with Jidoka, keep production smooth with Just-In-Time, and always look for ways to improve with Kaizen. This is important for making Lean Manufacturing successful.
Employees also help make Lean Manufacturing more efficient, reduce waste, and improve sustainability. They do this by following work procedures, keeping workspaces clean, and making sure materials flow well.
Employees also affect the flexibility, adaptability, quality, and customer satisfaction goals of Lean Manufacturing. They use their skills to create a safe and clean workplace, which leads to better product quality and customer satisfaction.
So, employees really drive the benefits of Lean Manufacturing in the organization.
Toyota’s Kentucky Plant: A Model of Efficiency
The Toyota Production System has core principles. These include the elimination of work waste, proper use of physical spaces, zero inventories, improved quality, customer satisfaction, and sustainability.
At the Kentucky Plant, the implementation of Jidoka, Just-In-Time, and Kaizen contributes to efficiency. This is done by ensuring proper pathways and material flow paths, reducing waiting and transportation time, and improving the work environment.
The TPS gives the Kentucky Plant advantages in efficiency and productivity over competitors. It focuses on customer suggestions, reducing work waste, delivering better quality products, and gaining better financial profits.
This has allowed Toyota to outperform rivals and withstand supply chain disruptions. This demonstrates that the era of the Toyota Production System is not over.
The Tsutsumi Plant: Implementing Solar Power and Sustainable Practices
The Tsutsumi Plant has made changes to use solar power. They installed solar panels to make clean and renewable energy. The plant also works to reduce waste, use energy better, and encourage recycling. These changes have improved how well the plant works, how much it makes, and how long it can keep going. Using solar power has helped the plant need less traditional energy, which saves money and is better for the environment.
Also, using sustainable practices has helped the plant do its work better, make less waste, and be more responsible for the environment. This matches Toyota’s plan for making things and the Toyota Production System. They focus on making less waste, getting better at their work, and making things that last a long time. The Tsutsumi Plant’s changes not only help the environment but also make the plant more likely to do well and keep going strong in the market.
Toyota Production System Advantages Over Competitors
Benchmarking: Toyota vs. Other Automotive Giants
The Toyota Production System has helped Toyota to outperform its competitors in efficiency and productivity. It focuses on minimizing work wastes, which increases operational efficiency. TPS also highlights the proper use of physical space, leading to safer, cleaner, and neater workplaces while reducing inventory handling costs.
Toyota’s production system sets the standard for quality, customer satisfaction, innovation, and financial profits in the automotive industry. TPS’s emphasis on sustainability has also enabled Toyota to weather supply chain disruptions, outperforming other automotive giants.
Risk Management and Problem Solving
The Toyota Production System manages risks and solves problems in manufacturing processes by focusing on eliminating work wastes, unevenness, and overburden. TPS also emphasizes using physical spaces efficiently to reduce safety risks, waiting and transportation times, and create an organized workplace.
Toyota implements a “just-in-time” strategy to maintain zero inventories, reducing handling costs and minimizing risks from overstocking or shortages.
Furthermore, TPS prioritizes customer satisfaction and delivering better quality products, leading to loyal customers who provide valuable feedback. This contributes to continuous improvement through research and innovation, enhancing product quality.
Toyota’s Global Impact
Adoption of TPS Principles by Other Industries
Other industries have found success by adopting TPS principles. These principles help eliminate work wastes, make better use of physical spaces, maintain zero inventories, improve quality, satisfy customers, boost profits, and promote sustainability.
The adoption of TPS principles has significantly enhanced efficiency, productivity, and sustainability in other industries. By cutting work wastes and utilizing physical spaces effectively, businesses have become more efficient. Meanwhile, maintaining zero inventories has reduced inventory handling costs and improved quality, resulting in better products and financial returns.
Additionally, improved customer satisfaction has strengthened customer service and loyalty.
Brand Loyalty and Market Leadership
Brand loyalty matters a lot in the car industry. It helps a brand sell more cars and make more money. Toyota has done well in this area by using something called the Toyota Production System, which gets rid of waste and makes better cars. This makes customers happy and keeps them coming back. It also helps Toyota save money and be more eco-friendly, which makes their brand stronger. Their success with this has made other car companies notice and has helped Toyota become a leader in the market.
This shows how important brand loyalty is, especially when other companies are having a hard time.
The Future of Toyota’s Manufacturing Strategy
Innovations and Advancements in Production
The Toyota Production System is built on core principles: elimination of work wastes, proper use of physical spaces, zero inventories, improved quality, customer satisfaction, and profits. These principles drive innovation and advancement in production. Toyota focuses on these principles to enhance business efficiency, reduce waiting and transportation time, and create a positive work environment in manufacturing areas.
TPS enables Toyota to produce or procure the exact quantity at the exact time, reducing inventory handling costs and enhancing product quality. As Toyota evolves its manufacturing strategy and TPS principles, we can expect new innovations like better sustainability, improved customer satisfaction, and increased profits. Toyota’s lean manufacturing excellence has established it as a benchmark in the market, even amidst recent supply chain disruptions.
TPS and the Next Generation of Lean Manufacturing
The Toyota Production System is the foundation for lean manufacturing. It highlights seven types of work wastes, unevenness, and overburden in every process. By eliminating these wastes, TPS and lean manufacturing establish standardized work, improving efficiency.
TPS also focuses on proper use of physical spaces, creating a safe and clean workplace, and implementing ‘Just-in-time’ practices to eliminate excess inventories. These principles maximize employee potential, enhance product quality, and drive improved customer satisfaction.
As a result, TPS helps organizations become market benchmarks and achieve better financial profits. Additionally, the zero wastes and zero inventories approach contributes to better sustainability, setting TPS apart from other manufacturing systems.
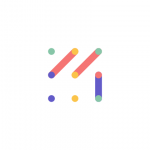
Vizologi is a revolutionary AI-generated business strategy tool that offers its users access to advanced features to create and refine start-up ideas quickly.
It generates limitless business ideas, gains insights on markets and competitors, and automates business plan creation.