Adopting the Kaizen Mindset for Success
Do you want to achieve more success in your personal or professional life? The Kaizen mindset could be the key. Kaizen comes from Japan and it’s about making continuous improvement through small, gradual changes. This article will show you how adopting the Kaizen mindset can lead to significant progress and success in different areas of your life.
Whether you want to advance in your career, develop personally, or grow your business, using Kaizen principles can make a real difference in your journey toward success.
Understanding the Kaizen Philosophy
The Origins of Kaizen: A Historical Perspective
Kaizen is a philosophy of continuous improvement. It originated from post-World War II Japanese quality circles and was later popularized in the West by Masaaki Imai in 1986.
Understanding the historical perspective of Kaizen helps shed light on its development and evolution. The historical origins have influenced the principles and techniques associated with it. This philosophy prioritizes small, ongoing positive changes over large-scale transformations, which remains central to the practice of Kaizen today.
Organizations that comprehend the historical roots of Kaizen can better integrate the philosophy into their culture and operations, promoting a continuous improvement mindset for personal and organizational success.
Additionally, familiarity with Kaizen’s historical background provides a solid foundation for its effective implementation in modern organizations. It emphasizes the importance of understanding problems and developing solutions at the real place where work is done. This ensures that organizations can utilize the principles and practices of Kaizen to improve processes, eliminate waste, and foster a culture of continuous improvement.
Defining Kaizen: The Core Principles
The core principles of Kaizen focus on continuous improvement through small positive changes. These include teamwork, personal discipline, improving morale, quality circles, suggestions for improvement, and quality control.
By fostering a culture of continuous innovation and improvement, Kaizen principles contribute to organizational improvement. This involves encouraging all employees to participate in the improvement process, identifying problems, suggesting solutions, and implementing changes systematically.
These principles also support ongoing improvement by promoting regular reflection and problem-solving, enhancing employee engagement, and reducing waste and inefficiencies.
Embracing these principles enables organizations to create an environment where everyone is committed to making small daily improvements, leading to sustainable growth and success.
Fundamentals of the Kaizen Cycle
The Kaizen Cycle focuses on continuous improvement. It involves making small, incremental changes that lead to significant improvements over time. Core principles include the 5 Whys Analysis, PDCA cycle, and 5S Program. These help identify and resolve issues while promoting workplace efficiency and organization.
Organizations can encourage employees to initiate change through the Kaizen Cycle. This is done by fostering a culture of open communication, feedback, and idea-sharing. By creating a safe space for employees to voice their suggestions and actively participate in problem-solving, organizations can harness collective knowledge and creativity to drive positive change.
Implementing the Kaizen Cycle in day-to-day operations has its advantages and challenges. Its strengths include increased productivity, cost savings, and improved quality. However, challenges may involve resistance to change and the need for sustained commitment from all levels of the organization.
Evolving into a Learning Organization Through Kaizen
Cultivating a Growth Mindset for Mastery
Cultivating a growth mindset through Kaizen philosophy means making small, ongoing positive changes for continuous improvement. Mastery is achieved by focusing on progress, embracing challenges for growth, and persisting through setbacks. Core principles like quality circles and the PDCA cycle support this mindset by encouraging improvement and learning from experiences. In organizations, Kaizen involves employees in decision-making, creating ownership and commitment to improvement.
Implementing Kaizen in Day-to-Day Operations
Commitment from Management: The Driving Force
Management plays a crucial role in the success of Kaizen. When leaders actively support and participate in the continuous improvement process, it sets the standard for the rest of the organization. This impacts the overall organizational culture by promoting a growth mindset and a focus on continuous improvement. It also instills confidence in the workforce.
Management can demonstrate their commitment to Kaizen by engaging in Gemba walks, participating in Kaizen events, and providing resources for ongoing training and education. By consistently showing dedication to Kaizen, management creates an environment that fosters innovation, problem-solving, and collaboration, ultimately driving the organization’s success.
Empowering Employees to Initiate Change
Employees can drive change within the organization through Kaizen principles. This involves fostering a culture of continuous improvement and innovation. It is achieved by encouraging open communication, providing learning and growth opportunities, and acknowledging employee contributions.
Establishing cross-functional teams and involving employees in decision-making processes also fosters a sense of ownership and shared responsibility. Holding regular brainstorming sessions, creating feedback mechanisms, and offering mentorship programs empower employees to initiate change by actively participating in problem-solving and generating new ideas.
Providing necessary training, resources, and recognizing successful change initiatives contributes to a culture that encourages the Kaizen mindset. This in turn empowers employees to take initiative in driving positive change within the organization.
The Gemba Walk Approach
“The Gemba Walk Approach” is a vital part of the Kaizen philosophy and continuous improvement. It focuses on understanding and identifying potential issues at the ground level where work is done. Managers and leaders are encouraged to visit the actual workplace, engage with employees, observe processes, and gather firsthand knowledge to develop effective solutions.
This approach empowers employees by highlighting their importance in continuous improvement and allows them to see real-time feedback, leading to positive changes in day-to-day operations.
Getting Organized with the 5S Program
The 5S Program is a method for organizing and improving efficiency in a work environment. It involves five key steps: Sort, Set in Order, Shine, Standardize, and Sustain.
By decluttering workspaces, defining storage locations, and establishing cleanliness and maintenance procedures, organizations can eliminate waste, reduce process time, and increase productivity.
Implementing the 5S Program leads to a safer and more enjoyable work environment and fosters a culture of continuous improvement and innovation.
This contributes to the overall success of the Kaizen philosophy, which emphasizes small, incremental changes for long-term improvement.
Embarking on Your Kaizen Journey
Starting with Small Steps: A Practical Guide
Starting with small steps is an effective way to put the Kaizen philosophy into practice. By recognizing and addressing smaller issues within larger processes over time, both individuals and organizations can embrace continuous improvement. A practical guide for those starting their Kaizen journey includes understanding the 5 Whys Analysis, using the Plan-Do-Check-Act (PDCA) cycle, and implementing the 5S Program to organize the workplace.
By adopting these tools and techniques, individuals andorganizations can establish a culture of continuous improvement that leads to long-term success.
Additionally, having a growth mindset and fostering a learning organization is essential for maintaining the Kaizen approach. Personal and organizational success comes from making small, consistent positive changes, continually improving processes, and striving for excellence. Examples from various industries, such as healthcare and individual levels, show the practicality and success of the Kaizen mindset.
Designing Your Initial Kaizen Event
To design an effective initial Kaizen event, the team should:
- First, identify a specific area for improvement and set clear objectives.
- Assemble a multi-disciplinary team to participate in the event, ensuring diverse perspectives and skills are available.
- Create a process map to visualize the current state and identify areas of waste and inefficiency.
- Develop a customized Kaizen checklist by incorporating standard tools like the 5 Whys Analysis, PDCA cycle, and 5S program tailored to the specific needs of the project and organization.
- Explore various types of Kaizen events, including large-scale events, focused events, and rapid improvement workshops, each suited for different levels of organizational change.
- Select the most suitable type of event to align with the strategic improvement goals.
The event can be further enriched with:
- Benchmarking
- Brainstorming sessions
- Gemba walks, targeting practical solutions based on real-world observation rather than assumptions.
This approach ensures that the Kaizen event generates sustainable improvements in both processes and workplace culture.
Developing a Customized Kaizen Checklist
Organizations interested in Kaizen should pinpoint areas or processes needing improvement. This could be production, supply chain, inventory, or customer service. Understanding existing inefficiencies helps tailor the Kaizen checklist to fit operational and cultural needs. Customization may involve addressing specific pain points or aligning with the organization’s values and goals. To ensure effective continuous improvement, clear goals and adequate training and resources are crucial.
Ongoing monitoring and feedback mechanisms help track progress and identify areas for further improvement. Developing a customized Kaizen checklist can make continuous improvement a part of the organizational culture.
Exploring Types of Kaizen Events
There are various types of Kaizen events that organizations can explore for continuous improvement. Some of these include Value Stream Analysis, Six Sigma, Lean Six Sigma, Strategy & Cultural Change, and Supply Chain & Manufacturing. Each type offers specific tools and methodologies to address different areas of the organization’s processes and operations.
These different types of Kaizen events contribute to process improvement and organizational development by allowing teams to focus on specific areas that need enhancement. For instance, Six Sigma helps reduce defects and variations in processes, while Lean Six Sigma focuses on waste reduction. The Strategy & Cultural Change event assists in creating a culture of continuous improvement and innovation within the organization, leading to sustainable organizational development.
Organizations can identify and prioritize the types of Kaizen events that would be most beneficial for their specific needs and goals by conducting thorough assessments of their current processes and understanding the areas that require improvement. Analyzing key performance indicators and involving employees at all levels in the decision-making process can also help prioritize which types of Kaizen events would be most beneficial to the organization.
Real-world Kaizen: Illustrative Success Cases
Highlighting Key Business Transformation Examples
One example of successful business transformation through Kaizen is the reduction of waste in manufacturing processes. This has led to lower costs and increased productivity. Another example is the use of Kaizen principles in healthcare, resulting in improved patient care and reduced waiting times. These real-world examples show how organizations have used Kaizen to drive significant business transformation and achieve sustainable improvement.
It’s important to note that while Kaizen has been successful in many industries, some organizations have faced challenges during initial implementation due to resistance to change and lack of employee engagement. The pros of implementing Kaizen include increased employee morale, better customer satisfaction, and reduced operational costs, while the need for continuous commitment and culture change within the organization are considered cons.
Pros and Cons of Implementing Kaizen
Exploring the Advantages of Kaizen
Implementing Kaizen in an organization offers several potential benefits. It can lead to a more streamlined and efficient operation. This, in turn, reduces waste and increases overall productivity.
Continuous improvement through Kaizen creates a culture of always seeking ways to enhance processes and methodologies. This contributes to the organizational growth by fostering an environment of innovation and adaptation.
Employees also benefit from Kaizen, as it positively impacts their engagement and job satisfaction. By engaging employees in the process and showing that their ideas are valued, Kaizen can enhance morale and lead to an increase in productivity.
All these advantages demonstrate how implementing Kaizen in an organization can result in significant benefits and a positive impact.
Confronting the Challenges of Kaizen
Implementing Kaizen in organizations can face common challenges. These include resistance to change, lack of employee engagement, and the need for a significant cultural shift.
Leaders can confront and overcome these challenges by creating a supportive environment. This environment should encourage open communication, participation, and collaboration. It should involve employees in the decision-making process and provide training and resources to enhance their skills.
Additionally, celebrating small victories can maintain motivation.
To mitigate potential drawbacks, organizations can employ various strategies. These include setting clear goals and expectations, establishing regular check-ins and feedback loops, and recognizing and rewarding continuous improvement efforts. Creating a culture of recognition and appreciation, fostering an environment of trust, and allowing for experimentation and learning from failures can also help. These actions can build resilience and adaptability within the organization, allowing for greater long-term success and sustained improvement efforts.
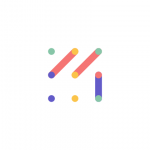
Vizologi is a revolutionary AI-generated business strategy tool that offers its users access to advanced features to create and refine start-up ideas quickly.
It generates limitless business ideas, gains insights on markets and competitors, and automates business plan creation.