Automate with Toyota Production System
The Toyota Production System is an innovative methodology. It has revolutionized how companies approach automation in production processes. Implementing TPS can streamline operations, reduce waste, and improve efficiency. We will explore how TPS can automate different aspects of production, leading to significant improvements in productivity and quality. If you’re interested in learning about cutting-edge automation techniques, the Toyota Production System is worth your attention.
Historical Evolution of the Toyota Production System
The Toyota Production System (TPS) has evolved over time. It was developed based on the fundamental principles of Just-in-Time production and Jidoka, with the aim of eliminating waste and achieving smooth process value delivery.
The TPS has evolved through implementing philosophies such as “Daily Improvements” and “Good Thinking, Good Products,” which have driven continuous improvement and value addition.
Historical factors and events, such as Sakichi Toyoda’s automatic loom, influenced the TPS by automating work, making judgments into the machine, and eliminating wasteful practices. Furthermore, Kiichiro Toyoda’s vision led to the development of methodologies and techniques for eliminating waste between operations, culminating in the Just-in-Time method.
These key strategies and approaches, along with Taiichi Ohno’s Workplace Management outlining TPS implementation, have shaped the core objectives and fundamentals of the TPS.
Toyota has shared the TPS with other organizations and charities to improve their operations by adopting the principles of continuous improvement, respect for people, and adding value through problem-solving.
Core Objectives of the Toyota Production System
The Toyota Production System has several main objectives. These include:
- Eliminating waste
- Implementing a just-in-time production system
- Achieving consistent, high-quality results
The system focuses on continuous improvement in processes and outcomes. It emphasizes problem-solving and value-driven solutions. Additionally, it prioritizes employee engagement and a culture of respect by empowering the workforce to contribute to the improvement of their work environment and processes.
By fostering a culture of respect and empowerment, the Toyota Production System not only enhances employee morale but also builds a foundation for sustainable and long-term success within the organization.
The Fundamentals of Toyota’s Production System
Pursuing Excellence through Continuous Improvement
Creating a culture of continuous improvement and excellence in an organization involves adopting the Toyota Production System principles. This means focusing on lean manufacturing, just-in-time production, and jidoka to reduce waste and improve process value delivery.
The TPS also emphasizes continuous improvement, respect for people, and problem-solving as key principles of the Toyota Way. This promotes a positive work environment and encourages employees to embrace change and strive for excellence.
To encourage organizational learning, companies can implement strategies like regular training programs, knowledge sharing platforms, and cross-functional collaboration to address the root causes of issues.
Investing in people and partners is crucial for achieving organizational growth and continuous improvement. By empowering employees, providing them with necessary skills and knowledge, and building strong relationships with suppliers and stakeholders, organizations can drive innovation and improve operations, ultimately leading to sustainable growth and success.
Building a Culture of Respect for Employees
Leaders in the organization should actively involve employees in decision-making and give them a voice. Open communication and recognizing employee contributions are important. Employee feedback mechanisms such as surveys, suggestion boxes, and team meetings can help achieve this. Involving employees in decision-making fosters a culture of respect and shows their opinions are valued.
Leaders should also lead by example, treating all employees fairly and considerately, regardless of their position.
Additionally, clear policies and procedures for respectful conduct should be created. Training on these policies for employees and managers can help prevent disrespectful behavior. Channels for reporting inappropriate behavior, like harassment or discrimination, should be accessible to all employees. These measures help create a safe and respectful workplace where all employees feel valued.
Efficient Processes Lead to Superior Outcomes
Implementing efficient processes in an organization can lead to superior outcomes. It can eliminate waste, streamline workflows, and improve productivity. Prioritizing efficient processes helps reduce costs, enhance product and service quality, and meet customer demands effectively.
A focus on efficient processes can lead to improved organizational performance and results. This includes increased competitiveness, better workplace morale, and higher customer satisfaction.
Investing in People and Partners for Organizational Growth
Organizations can improve by implementing the Toyota Production System. This system focuses on just-in-time production, jidoka, continuous improvement, and problem-solving. It aims to eliminate waste, overburden, and inconsistency, achieving smooth process value delivery.
Implementing the TPS can develop a culture of respect and empowerment for employees. Effective partnerships and collaborations are vital for overall growth and success. Sharing the TPS with other organizations and charities to improve their operations and impact shows the value of strong collaborations.
This approach fosters continuous improvement and adds value by solving problems, ultimately leading to sustained growth and development. By following the principles of the Toyota Way and embracing the TPS, organizations can invest in their people and partners to achieve sustainable growth and development.
Fostering Organizational Learning by Addressing Root Causes of Issues
Issues within an organization can be addressed by identifying and prioritizing root causes. These may include excess inventory, extraneous processing steps, and defective products, which create more waste and impact management. Implementing methodologies and techniques for eliminating waste, such as the Toyota Way, is vital.
Strategies to ensure addressing root causes becomes part of the organization’s culture include adopting TPS, sharing the system, and creating a supportive workplace environment. This fosters organizational learning and adds value through problem-solving, promoting a culture of continuous improvement and respect for people.
Strategies for Implementing Toyota’s Production System in Your Organization
An organization can create a culture of continuous improvement and respect for employees in a few ways.
- Promote open communication.
- Involve the workforce in decision-making processes.
- Demonstrate appreciation for their contributions.
This approach encourages employees to strive for excellence and engage in ongoing improvement efforts.
To achieve efficient processes and superior outcomes through the Toyota Production System , organizations can implement strategies such as visual management, standardization of work, and error-proofing methods.
These strategies help in identifying and addressing inefficiencies, reducing waste, and ensuring high-quality results.
Additionally, empowering the workforce and effective workplace management can be achieved by providing necessary skills and training, delegating decision-making authority, and creating a supportive work environment that encourages autonomy, creativity, and problem-solving.
This enables employees to take ownership of their work, contribute to the continuous improvement culture, and drive the successful implementation of Toyota’s Production System.
Workforce Empowerment and Effective Workplace Management
The Toyota Production System is an example of how organizations can create a culture of respect for their employees.
It empowers the workforce and effectively manages workplace operations. TPS emphasizes respect for people, fostering an environment of empowerment and continuous improvement.
Investing in its people and partners, Toyota pursues excellence through continuous improvement, enabling organizational growth and success.
The principles and terminology associated with TPS, such as Just-in-time production and Jidoka, aid in workforce empowerment and effective workplace management.
These principles promote the elimination of waste, design out overburden and inconsistency, achieve smooth process value delivery, and respect for people.
The systems and knowledge shared by Toyota provide practical examples of how a company can maintain a pragmatic approach to workplace management, ensuring a conducive and efficient work environment.
Key Terminology Associated with the Toyota Production System
Kaizen – The Practice of Continuous Improvement
Kaizen, The Practice of Continuous Improvement, focuses on eliminating waste, designing out overburden and inconsistency, and achieving smooth process value delivery. Organizations can foster this culture by incorporating principles from the Toyota Production System , like Just-in-time production and Jidoka. These aim to eliminate waste, streamline processes, and provide better value to customers.
Additionally, they can encourage employee engagement in problem-solving, support a willingness to experiment and innovate, and promote respect for everyone’s contributions. The benefits of implementing Kaizen include increased productivity and efficiency, reduced waste, improved employee morale, better quality products and services, enhanced customer satisfaction, and a competitive edge in the market. By practicing continuous improvement, organizations can adapt to changes, meet customer needs, and remain sustainable.
Jidoka – Automation with a Human Touch
Jidoka is a concept in the Toyota Production System. It’s about automating processes while keeping a human touch. The goal is to help employees work efficiently, using automation as a tool, not a replacement.
Empowering employees to stop production for quality issues or abnormalities is a key part of Jidoka. This builds a culture of respect and trust.
Implementing Jidoka has many benefits. It improves efficiency by preventing defective products from moving forward, reducing waste and costs. This ensures high-quality products.
It also encourages continuous improvement and problem-solving among employees, leading to better productivity and customer satisfaction.
Just-in-Time – Timely Production and Inventory Control
Just-in-Time is about timely production and inventory control. It helps reduce excess inventory, minimize waiting times, and shorten lead times between production and customer delivery. When production is synchronized with customer demand, companies can avoid overproduction, prevent excess inventory, and maintain a highly efficient process that reduces costs and streamlines the supply chain.
The key principles and strategies of Just-in-Time include continuous improvement, waste reduction, increased flexibility, and just-in-time production scheduling. By empowering employees to identify and solve problems, organizations can create a culture of continuous improvement that promotes efficient operations. Small, frequent deliveries and flexible production capabilities enable organizations to adapt quickly to changing customer needs and product demand while minimizing inventory costs and storage space.
Organizations can apply Just-in-Time by implementing Kanban systems, creating cross-trained and flexible workforces, and fostering strong supplier partnerships. By establishing pull-based production systems driven by customer demand, companies can reduce waste, lower operational costs, and respond more quickly to changes in customer demand and market trends. Close collaboration with suppliers, quality control initiatives, and regular Kaizen events can create a culture of continuous improvement that further supports the principles of Just-in-Time production and waste minimization.
Heijunka – Production Leveling for Efficiency
Heijunka is a production leveling approach. It aims to balance workloads and smooth the flow of materials and products in production. By spreading production evenly over time, Heijunka helps to minimize inventory variations. It also makes it easier to identify and resolve issues that could disrupt the workflow.
Implementing Heijunka can reduce overproduction, lead times, and unnecessary fluctuations. This allows for a consistent, more efficient workflow.
One effective strategy for integrating Heijunka involves standardizing production and scheduling methods. This allows for greater flexibility and responsiveness to changes in demand.
Additionally, implementing visual management tools, such as kanban cards or scheduling boards, can enable workers to quickly identify and act on changes in the production schedule. This ensures a more seamless and efficient process.
Kanban – Visual Scheduling System
The Kanban visual scheduling system is a method of managing workflow. It originated at Toyota and aims to create a more efficient and streamlined production process. It does this by providing a visual representation of work items that need to be completed.
Kanban uses a card system to help manage tasks. The cards move through different stages of the production process, from inception to completion. This simple and practical system allows everyone to know what to do and when to do it.
By providing a clear visual representation of tasks and their status, Kanban helps to eliminate waste, improve time management, optimize inventory levels, and reduce backlog or overproduction. It encourages companies to make only what the customer needs when they need it, as part of the Just-in-Time production philosophy.
This system can be applied in various industries, from manufacturing to service-oriented organizations, as an efficient method for managing workflow and improving productivity. Its simplicity and focus on reducing waste and improving efficiency make it a valuable approach for modern business operations.
Muda, Mura, Muri – The Three M’s of Waste
Muda, Mura, and Muri are the three waste categories in the Toyota Production System.
Muda refers to activities that use resources without adding value, like overproduction, waiting, or unnecessary transportation.
Mura is the unevenness in operations, while Muri involves overburden on machines or employees due to unrealistic workloads.
These factors lead to inefficiencies in production, like excessive inventory, longer lead times, and reduced productivity.
The Toyota Production System offers strategies like Just-in-Time production to reduce overproduction and standardized work to eliminate inconsistency.
It also emphasizes creating a work environment that addresses equipment or human-related problems, seen in the Jidoka principle.
By tackling these types of waste, organizations can optimize their operations and achieve higher efficiency.
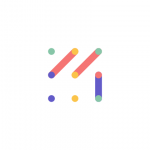
Vizologi is a revolutionary AI-generated business strategy tool that offers its users access to advanced features to create and refine start-up ideas quickly.
It generates limitless business ideas, gains insights on markets and competitors, and automates business plan creation.