Basics of Lean Management Principles
Lean management principles help organizations become more efficient and effective. They focus on minimizing waste and maximizing value to streamline processes and improve productivity. Understanding these principles can help business owners, managers, and employees contribute to a more successful organization. This article explains the basics of lean management and how they can be applied in different industries.
Understanding the Core Lean Management Principles
Principle One: Drive Efficiency by Optimizing as a Whole
Lean management principles focus on driving efficiency by optimizing the organization as a whole. This means clearly defining the organization’s main purpose to effectively meet customer needs at a low cost. It’s important to align everyone’s efforts towards serving the customer. Organizations achieve this by focusing on the process (value stream) used to achieve their main objectives.
They can do this by identifying someone responsible for each value stream to improve performance from its current state to a better future state. This approach creates a culture of continuous improvement within the organization, leading to competitiveness, increased customer value, decreased business costs, and higher profitability. By optimizing the organization as a whole, processes can be streamlined, waste can be eliminated, and productivity can be improved across the entire value stream, resulting in a more efficient and effective organization.
Principle Two: Eradication of Waste in Processes
Waste in processes can be found and removed by using value stream mapping, analyzing process flow, and examining non-value-adding activities. This can help organizations identify areas of waste like overproduction, waiting times, unnecessary transportation, excess inventory, unnecessary motion, and defects. Getting rid of these wasteful activities can improve efficiency and productivity, reduce lead times and costs, and enhance overall performance.
There are several strategies and tools that can help eliminate waste in processes and promote lean management principles. These include implementing the 5S methodology for workplace organization, standardizing processes, using error-proofing techniques, and embracing continuous improvement practices like kaizen events and daily management huddles. Visual management tools and techniques, such as kanban systems and andon lights, can also help identify problems and prevent waste.
Removing waste in processes leads to improvements in quality, delivery, and customer satisfaction by streamlining operations, reducing defects, and ensuring timely delivery of products and services. This results in increased customer satisfaction, decreased lead times, and ultimately, increased value for customers.
Principle Three: Embedding Quality into Product Development
It’s important to prioritize quality in product development to meet customer expectations. This includes implementing quality control checkpoints, using customer feedback for improvements, and ensuring all team members understand the importance of quality. To balance quality, efficiency, and speed, companies should optimize processes, reduce waste, and increase productivity.
Creating a culture that values quality, providing training and support, and establishing clear quality goals are also essential for aligning team members with this priority.
Principle Four: Acceleration of Delivery for Customer Satisfaction
Improving delivery speed is important for making customers happy in lean management. When the delivery process is faster, customers get their products or services quickly and efficiently. This makes them happier overall.
To speed up delivery, organizations can use strategies like making production and supply chain processes more efficient, simplifying logistics and distribution channels, and using better inventory management practices. These strategies can be integrated into lean management by focusing on getting rid of waste, always improving, and working together as a team to meet customer needs quickly.
In the end, making deliveries faster is a big part of lean management that directly affects customer satisfaction by giving them good products and services quickly.
Principle Five: Fostering a Knowledge-Driven Work Environment
Organizations can value and promote knowledge sharing by fostering a culture of continuous learning. This means encouraging employees to seek out and share knowledge, and implementing strategies for skill development. For instance, they can establish systems for attending workshops, training programs, and seminars. Leaders can also recognize and reward employees for their knowledge contributions, thus incentivizing them to share.
Creating platforms for sharing insights and lessons learned is another effective strategy. Lastly, leaders can emphasize the importance of sharing knowledge through their actions, actively participating in knowledge-sharing activities, and championing a culture of open communication and collaboration.
Principle Six: Encouraging Flexibility by Deferring Decisions
Encouraging flexibility is important in Lean management. It allows for adaptability and agility. By postponing decisions until the last responsible moment, teams can assess the situation and gather necessary information. This helps avoid premature choices that can lead to wasted resources or unfavorable outcomes. Keeping decision-making flexible allows for changes based on the most current data, leading to more informed and effective actions.
One strategy for implementing this principle involves regular cross-functional collaboration and information-sharing among team members. This ensures decisions are made with the most complete and up-to-date information available. Another strategy is having a structured framework for revisiting decisions, enabling teams to adjust their course of action as needed.
Deferring decisions aligns with the goal of fostering a flexible and adaptive work environment in Lean management. This ultimately aims to minimize waste, increase efficiency, and enhance overall productivity by promoting continuous improvement and problem-solving.
Principle Seven: Advancing a Culture of Respect for Every Individual
Lean management principles focus on respecting every individual in the workplace. These principles identify and support the value that each person brings to the organization. By promoting inclusivity and respect through processes, Lean management principles encourage input from everyone. This includes assigning a value-stream manager to align the efforts of the entire team, recognizing each person’s contribution, and establishing support processes to address employee needs.
Emphasizing continuous improvement, Lean principles develop strategies that acknowledge and respect the unique strengths of each individual, creating an environment where all employees feel valued and appreciated.
Building and Nurturing Lean Teams
Assembling a Cross-Functional Team
Cross-functional teams bring together members from different departments and expertise. This allows them to work together, share insights, and align processes to improve efficiency.
To create a respectful culture, it’s important for all team members to feel valued and appreciated. Open communication and inclusive decision-making processes also play a crucial role.
Encouraging continuous improvement involves regular feedback sessions, skill development opportunities, and fostering innovation and creativity in the team.
Organizations can benefit from cross-functional teams by leveraging diverse skills and experiences to achieve common goals, ultimately boosting operational performance and driving innovation.
Promoting Continuous Improvement Among Team Members
The organization can encourage and incentivize team members to continually seek ways to improve their work processes and outcomes by establishing a culture that recognizes and rewards innovation and process improvements. This can be achieved by regularly acknowledging and showcasing successful improvements and providing tangible rewards or opportunities for further professional development.
Strategies that can be implemented to support and promote a culture of continuous improvement among team members include creating regular forums for sharing and discussing improvement ideas, providing access to resources and tools that facilitate experimentation and learning, and implementing regular training focused on lean principles and methodologies.
The organization can foster an environment where team members feel empowered to regularly contribute ideas and suggestions for improvement by encouraging open and transparent communication, involving employees in decision-making processes, and providing clear channels for submitting improvement ideas and feedback, as well as celebrating and recognizing employees who contribute valuable suggestions for improvement.
Lean Tools and Practices
Utilizing 5S for Workplace Organization
The Lean management principles can be used to make the workplace more organized and efficient by implementing 5S.
The steps for implementing 5S are:
- Sort.
- Set in Order.
- Shine.
- Standardize.
- Sustain
These steps involve organizing the workplace by sorting items and removing unnecessary clutter, setting items in order for easy access, maintaining cleanliness, establishing standardized procedures, and sustaining the practice through regular audits and continuous improvement.
The potential benefits of using 5S for workplace organization include improved safety, increased productivity, reduced waste, and enhanced employee satisfaction.
By following these 5S principles, organizations can create a more efficient and effective work environment, aligning with Lean management principles.
Applying Kanban to Optimize Workflow
Kanban is a visual scheduling system that helps teams manage work efficiently. It uses Kanban boards to show task status, identify bottlenecks, and prioritize work. To use Kanban effectively, teams need clear workflows, work in progress (WIP) limits, and continuous process improvement. This ensures maximum productivity and timely delivery of work. Challenges like resistance to change and differing team priorities may arise. Despite this, using Kanban has numerous benefits.
It provides transparency, flexibility, improved communication, increased productivity, and an efficient work environment. Kanban plays a significant role in optimizing workflow and driving lean thinking in various work environments as organizations seek continuous improvement.
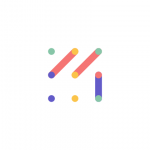
Vizologi is a revolutionary AI-generated business strategy tool that offers its users access to advanced features to create and refine start-up ideas quickly.
It generates limitless business ideas, gains insights on markets and competitors, and automates business plan creation.