Best Practices in Lean Management
Lean management is a method for improving efficiency and reducing waste in business operations. It focuses on continuous improvement and eliminating non-value-added activities.
Organizations can achieve cost savings and enhanced productivity by implementing lean principles. Whether a small business owner or a corporate executive, understanding and implementing lean principles can bring your organization tangible benefits.
Fundamental Lean Practice: Removing Non-Value-Adding Steps
You can find and eliminate non-value-adding steps in lean practice using the 5S methodology. Tracking metrics helps review all areas and processes in the organization. Prioritizing safety is also essential.
Challenges in removing non-value-adding steps include resistance to change and needing buy-in from all workforce members. Overcoming these challenges requires proper training and empowering each member to apply lean principles.
Removing non-value-adding steps contributes to overall process improvement in a lean environment by reducing waste and boosting efficiency. This leads to shorter production cycles, reduced lead times, and increased profitability.
Fostering Continuous Improvement
An organization can create a culture that promotes and supports continuous improvement in lean practices. This can be done by emphasizing the three common-sense principles of lean manufacturing. These principles should be ingrained into the company culture.
Additionally, workforce members should be empowered to apply lean principles anytime and anywhere in the organization.
Strategies such as training and gaining buy-in will help overcome resistance to change. Furthermore, to encourage employees to participate in identifying and implementing improvements, they can focus on identifying and eliminating the 7 types of waste in manufacturing. This can lead to reducing production cycle and lead times.
Leadership can demonstrate commitment to fostering continuous improvement in lean management by leading by example. An example is the president of Fastcap, a lean manufacturing company. His dedication and passion for lean principles demonstrate how leadership can drive improvements in the organization and foster a culture of continuous improvement.
Strengthening Lean Practice Through 5S Methodology
The 5S methodology helps remove non-value-adding steps in Lean practice. It promotes organization, cleanliness, and standardization.
Creating a visual workplace with organized and labeled tools and materials reduces unnecessary movement, searching, and inventory errors. This increases efficiency and minimizes waste.
5S methodology supports continuous improvement in Lean environments by evaluating and optimizing workspaces and workflows. It helps identify and address inefficiencies and safety hazards, enabling evidence-based decisions to enhance processes, productivity, and quality.
Companies can invest in organizational training to strengthen Lean practice through the 5S methodology to ensure all employees understand and implement the 5S principles. Regular audits and assessments help maintain and enhance 5S practices, fostering a culture of continuous improvement and waste reduction.
Enhancing Safety in Lean Environments
Improving safety in lean environments involves removing unnecessary steps. This reduces the risk of human error and accidents. In manufacturing, continuous improvement efforts can minimize equipment malfunctions and operator errors. The 5S methodology focuses on workplace organization and cleanliness, strengthening safety measures. It helps identify and mitigate potential hazards and risks. Empowering employees to address safety concerns proactively can enhance overall workplace safety.
Implementing innovative safety measures alongside lean initiatives creates a safer and more efficient work environment.
Measuring Success: Key Metrics in Lean Management
Lean management uses key metrics such as cycle time, percent complete and accurate, and overall equipment effectiveness (OEE) to measure success. These metrics help identify areas for improvement, remove non-value-adding steps, and foster continuous process improvement.
The 5S methodology involves sorting, setting in order, shining, standardizing, and sustaining, is crucial in maintaining organized and efficient workspaces, leading to improved productivity and reduced waste.
Employee empowerment is essential in Lean management, as it encourages staff to contribute ideas and take ownership of their work areas, thereby contributing directly to the success metrics.
Lean Training: Employee Empowerment and Buy-in
Implementing strategies to empower and gain buy-in from employees during lean training can involve:
- Promoting a culture of continuous improvement.
- Providing adequate training and support.
- Fostering open communication and collaboration within the organization.
- These strategies can help employees feel valued and entrusted with contributing to the organization’s success through lean methodologies.
- The principles of lean management can be effectively communicated and ingrained within the workforce by:
- Leading from the top.
- Engaging in open dialogue about the benefits of lean practices.
- Actively involving employees in the decision-making process.
- An example of successful implementation of lean training that has led to employee empowerment and buy-in involves Fastcap, a lean manufacturing company based in Bellingham, WA.
- The company’s president and owner, Paul Akers, is renowned for his dedication to continuous improvement and daily efforts to encourage employee engagement in lean practices, resulting in an empowered and motivated workforce.
- These examples demonstrate how empowering employees through lean training can lead to a culture of continuous improvement and enhanced organizational performance.
Quotes from Lean Thinkers
Renowned Lean Thinkers stress the significance of removing non-value-adding steps in fundamental Lean practice. They highlight the insights gained from this practice. For instance, they emphasize eliminating the seven types of waste: transportation, inventory, motion, waiting, overproduction, overprocessing, and defects. These are essential in Lean Manufacturing.
When implemented effectively in an organization, these practical principles result in reduced production cycle times and lead times. Furthermore, Lean Thinkers emphasize the significance of fostering continuous improvement within Lean organizations. This is done by promoting a culture of empowerment and motivation.
An example of this is Paul Akers, the president of Fastcap, a lean fanatic who works relentlessly to improve everything every day. Quotes from Lean Thinkers also shed light on the benefits and impact of utilizing the 5S methodology to strengthen Lean practice. This methodology enhances workplace organization, cleanliness, and standardization. In turn, this contributes to increased efficiency and productivity within Lean organizations.
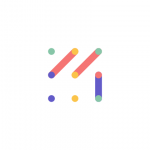
Vizologi is a revolutionary AI-generated business strategy tool that offers its users access to advanced features to create and refine start-up ideas quickly.
It generates limitless business ideas, gains insights on markets and competitors, and automates business plan creation.