Boost Your Business with Toyota Production System
If you want to make your business run better, do more work, and waste less, consider the Toyota Production System (TPS). Originally used in car making, TPS is now known for making processes better and improving business overall. By using TPS ideas, different businesses have made big improvements in how well they work, the quality of what they do, and how much money they make.
In this article, we will look at how you can make your business better with TPS and the good things it can do for your company.
Objectives of Implementing the Toyota Production System
The Toyota Production System has two main goals: achieving high efficiency and eliminating waste in manufacturing and logistics processes. TPS uses Jidoka and Just-In-Time to produce products efficiently, meet customer demand, and maintain high-quality standards.
TPS also focuses on organizing interactions with suppliers and customers to design out overburden, inconsistency, and waste, aiming for continuous improvement and excellence in processes.
Another goal of TPS is to empower employees and develop a culture of respect for people within the organization by emphasizing the Toyota Way. This management philosophy focuses on continuous improvement, respect for people, and value creation through the development of people and partners.
Understanding the Toyota Production System
The Toyota Production System focuses on excellence and continuous improvement. It achieves this by eliminating waste and achieving high efficiency.
By using Jidoka and Just-In-Time concepts, TPS makes work easier for workers. This results in producing products efficiently and at the pace of customer demand. It ensures that every vehicle meets high-quality standards and individual customer requirements.
The core principles of TPS are just-in-time manufacturing and Jidoka, aimed at eliminating overburden, inconsistency, and waste.
These principles shape effective workplace management by emphasizing continuous improvement, respect for people, and adding value to the organization by developing people and partners.
To share TPS practices and encourage a culture of respect for people, strategies such as sharing TPS with suppliers, organizations, and charities have been implemented. TPS principles have also been implemented in disaster relief efforts.
Taiichi Ohno’s Workplace Management outlines how to implement the TPS and contains commonly used terminology associated with the system.
Historical Development of the Toyota Production System
The Toyota Production System has a history marked by important events and milestones, shaping its principles and practices. Initially, it focused on eliminating waste and achieving high efficiency. Over time, the system evolved to prioritize meaningful work and high-quality standards.
The concepts of Jidoka and Just-In-Time have been central to TPS, allowing efficient production at the pace of customer demand. Toyota’s commitment to continuous improvement, respect for people, and adding value to the organization has primarily driven the implementation and evolution of TPS. These forces have shaped the underlying principles of TPS, emphasizing the development of people and partners.
Furthermore, Toyota has shared TPS with its suppliers, other organizations, and charities to improve their operations and impact. The historical development of TPS has contributed to its current principles and practices by incorporating the values of continuous improvement and respect for people, in addition to prioritizing meaningful work and high-quality standards to meet customer requirements.
Core Principles of the Toyota Production System
Pursuing Excellence: Continuous Improvement
Creating a culture of continuous improvement and excellence in an organization means focusing on developing and supporting its employees. It involves using processes like just-in-time manufacturing and Jidoka to streamline operations, reduce waste, and maintain high efficiency. This helps meet customer demand and maintain product quality. Empowering and working with employees is crucial for problem-solving and fostering a commitment to excellence.
The Toyota Production System centers on continuous improvement and respects people while adding value to the organization. By developing and supporting employees, as well as extending these principles to partners and suppliers, organizations can establish a culture of excellence and continuous improvement.
Building a Culture of Respect for People
Leadership can promote a culture of respect by leading by example, actively listening to employees, and ensuring everyone feels valued. Regular training and development can empower employees. Open communication, collaboration, and recognizing achievements also contribute to a respectful workplace. Successful indicators include high employee satisfaction, low turnover, and a positive reputation.
Increased productivity, innovation, and business performance also demonstrate the effectiveness of a respectful workplace culture.
Processes That Lead to Desired Outcomes
The Toyota Production System has specific processes that lead to desired outcomes. These include Just-In-Time manufacturing and Jidoka.
These concepts help Toyota produce products efficiently and meet customer demand, resulting in high-quality standards.
Continuous improvement plays a role in achieving desired outcomes by making work easier for workers and eliminating waste.
It ensures high efficiency and meaningful work.
The development of people and a culture of respect for people are also important.
The Toyota Way emphasizes respect for people and continuous improvement, adding value to the organization.
Empowerment Through Developing People and Collaboration
Organizations can empower their employees in many ways. One approach is by embracing the principles of systems like the Toyota Production System. This involves providing opportunities for skill development, training, and involving employees in decision-making. This creates a culture of continuous learning and improvement.
Collaboration within the workplace also plays a key role. Prioritizing collaboration fosters teamwork, mutual support, and information sharing, all important in achieving common goals. The TPS principles, such as just-in-time manufacturing and Jidoka, optimize workflow and eliminate waste, leading to increased efficiency and cost-effectiveness.
By adopting these principles and promoting a collaborative and development-oriented culture, organizations can positively impact employee motivation, job satisfaction, and performance. This ultimately helps achieve higher levels of empowerment and success for the employees.
Learning from Problem-Solving
Learning from problem-solving in the Toyota Production System helps identify and fix issues in manufacturing and logistics. This leads to greater efficiency, less waste, and better quality. Problem-solving also promotes continuous improvement, encouraging employees to find solutions to challenges they face, fostering innovation and adaptability. It also values input and expertise of workers, creating an environment of empowerment and collaboration.
Strategies for Sharing Toyota Production System Practices
Effective strategies for sharing Toyota Production System practices involve organizing workshops and training sessions. These aim to educate employees on TPS principles like just-in-time manufacturing and jidoka. It’s important to have clear communication channels to share TPS tools and techniques, allowing all team members to contribute to process improvements.
Providing hands-on experience through gemba walks and Kaizen events helps employees engage with TPS practices directly, fostering a culture of continuous improvement. Organizations can promote cross-functional collaboration and knowledge sharing by holding regular meetings and forums. This promotes a collective understanding of TPS principles. Leadership plays a vital role in promoting and sustaining TPS practices by demonstrating commitment to the TPS philosophy, providing resources for TPS training and implementation, and empowering employees to drive change through TPS initiatives.
Effective Workplace Management Inspired by TPS
The Toyota Production System principles can help manage the workplace.
Focus on eliminating waste and achieving high efficiency are important.
Ideas like Jidoka and Just-In-Time can make production efficient and meet customer demand.
This streamlines operations and makes work easier for employees.
It also promotes a culture of continuous improvement and respect for people.
Empowering employees and promoting collaboration are essential.
Embracing TPS principles emphasizes continuous improvement, respect for people, and adding value.
Sharing TPS principles with suppliers, organizations, and charities can inspire a culture of collaboration and continuous improvement.
Key Terminology in the Toyota Production System
The Toyota Production System is focused on efficiency and reducing waste. Key terms like Just-In-Time and Jidoka are important to TPS. Just-In-Time means making goods based on customer demand, ensuring high quality and meeting specific customer needs. Jidoka involves stopping production to fix problems and prevent defects.
These terms show TPS’s main values: continuous improvement, respect for people, and adding value. Using these principles, Toyota organizes manufacturing and logistics to promote efficiency and quality. They also share TPS practices with suppliers, charities, and other organizations to improve operations. This broad application has impacted the terminology used in TPS, showing its wider influence.
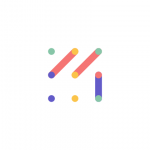
Vizologi is a revolutionary AI-generated business strategy tool that offers its users access to advanced features to create and refine start-up ideas quickly.
It generates limitless business ideas, gains insights on markets and competitors, and automates business plan creation.