Lean Concept Demystified: Making Work Smarter
Efficiency is crucial in today’s workplace. Companies are always looking for ways to streamline processes, cut costs, and boost productivity. One popular method for achieving these goals is “lean” thinking. Lean is a practical and effective approach to working smarter, not just a buzzword.
In this article, we’ll explore the key principles of lean thinking and how they can improve our work.
Understanding Lean Thinking: Creating Value Efficiently
Overview of Lean Philosophy
Lean Philosophy focuses on creating value with fewer resources and less waste. It does this by identifying what the customer values and continuously experimenting to achieve perfect value with zero waste.
Lean Thinking includes ongoing experimentation to improve quality, flow, time, effort, and cost. It also emphasizes a lean enterprise organized to understand the customer’s needs and provide value more effectively.
This philosophy centers on respect for the humanity of customers, employees, suppliers, and communities. It aims to continuously eliminate waste and improve value in specific situations.
The Synergy of Lean Thinking and Practice
Lean thinking and practice create value efficiently. They focus on identifying what the customer values and continuously experimenting to achieve perfect value with zero waste. By doing this, resources are used effectively, waste is minimized, and processes become more streamlined and efficient, delivering higher value to the customer.
In the workplace, applying lean thinking leads to ongoing experimentation to improve quality, flow, time, effort, and cost. Continuously eliminating waste and improving value elevates performance and creates a more efficient, collaborative, and high-quality work environment.
To implement lean thinking effectively, organizations should understand the customer’s needs and provide value more effectively. This involves aligning purpose, process, and people, and creating an environment for continual learning and problem-solving. Embracing Lean principles can help in the effective implementation of lean thinking in daily work.
Breaking Down the Core Components of Lean
Defining Value from the Customer’s Perspective
Customers value products and services based on their quality, cost, and usefulness. Factors like durability, performance, convenience, and customer service are also important. To meet customer expectations, businesses should seek feedback, conduct research, and analyze customer needs. Lean thinking can help identify what customers value and improve quality, flow, time, effort, and cost. It’s important to respect the humanity of customers and employees when aligning with customer value.
Identifying and Eliminating Process Waste
Common types of process waste in a workplace include:
- Overproduction
- Excess inventory
- Unnecessary motion
- Defects
- Waiting
- Overprocessing
- Unused employee creativity
To prioritize process waste elimination, organizations can:
- Conduct value stream mapping
- Visualize the current workflow
- Analyze value-added and non-value-added activities
- Engage employees in continuous improvement
Strategies for more efficient workflow:
- Implement standardized work processes
- Optimize inventory levels
- Use visual management techniques like Kanban
- Engage in continuous problem-solving (Kaizen approach)
Other ways to streamline workflow:
- Reduce unnecessary handoffs
- Cross-train employees
- Empower decision-making at their level
These strategies lead to:
- Improved quality
- Reduced lead times
- Cost savings
- Enhanced customer value
Implementing Kanban for Workflow Management
Kanban helps manage workflow by visualizing work, limiting tasks in progress, and focusing on improvement.
Teams can use Kanban boards to see tasks, set limits to avoid overload, and review processes regularly.
Strategies like training, clear guidelines, and buy-in from stakeholders ensure successful implementation.
Consider existing workflows, team dynamics, and organizational culture when integrating Kanban.
Understanding current bottlenecks and adapting Kanban to fit unique needs are important for successful integration.
Adopting the 5S System for Workplace Organization
Implementing the 5S system in a work environment can make the workplace more organized and efficient. The 5S system includes Sort, Set in Order, Shine, Standardize, and Sustain. It focuses on creating a clean and orderly work environment to improve productivity and safety. By sorting and organizing items, setting up designated areas, and regularly cleaning and maintaining the workspace, employees can easily find tools and materials, reduce waste, and minimize workplace hazards.
Successful adoption of the 5S system requires clear communication, training, and active participation from all employees for consistent practices and sustained improvement. The 5S system also aligns with lean thinking in the workplace by promoting continuous improvement, waste reduction, and value creation. It helps create an environment centered around respect for employees and customers, as well as the ongoing pursuit of delivering high-quality products and services.
Continuous Improvement with Kaizen
Organizations can use the principles of Kaizen to improve their processes and workflows through small, incremental changes. This helps create a culture of continuous improvement and involves all employees in identifying and implementing improvements. Practical strategies include empowering employees to suggest and test new ideas, providing regular training on Kaizen principles, and recognizing small improvements.
Kaizen aligns with Lean thinking and practice by focusing on customer value and waste reduction. It can be adapted to different industries by using specific Kaizen tools and techniques, like daily team huddles, visual management, and standardized work processes. Embracing Kaizen helps organizations improve quality, reduce waste, and enhance overall efficiency.
Enhancing Process Transparency with Andon
Andon systems improve process transparency in a Lean environment. They provide real-time visibility into operations and alert team members to any issues. This empowers workers to address problems immediately, preventing disruptions. Benefits of using Andon include promoting collaboration, fostering continuous improvement, and increasing productivity. Andon facilitates open communication and swift problem-solving, contributing to creating value efficiently in Lean thinking.
It helps teams identify and resolve inefficiencies, minimize waste, and enhance output quality, aligning with delivering customer value and continuous improvement in a Lean enterprise.
Prioritizing People in Lean Transformation
Lean transformation focuses on respecting people. This means giving employees, customers, and other stakeholders a voice. It also involves creating a culture of open communication and prioritizing the well-being of employees.
Prioritizing the health, safety, and professional development of employees is at the heart of embracing respect for people in lean transformation. Leadership is essential in promoting a culture of continuous improvement by showing commitment to employee well-being, supporting innovation, and encouraging ongoing learning and problem-solving.
Leaders can also encourage a collaborative work environment that values every team member’s input and fosters a sense of ownership and accountability.
Embracing Respect for People as a Core Principle
Embracing respect for people is essential for the success of lean thinking. Prioritizing the well-being and empowerment of employees creates a culture of trust and collaboration. Practical ways to embrace respect for people in lean transformation include involving employees in decision-making, providing skill development opportunities, and fostering open communication.
Respecting people not only enhances lean thinking but also increases employee engagement, productivity, and satisfaction. When employees feel respected and valued, they actively participate in continuous improvement efforts and contribute to the organization’s success. Therefore, embracing respect for people is integral to creating a work environment that supports lean thinking and practice.
The Practical Benefits of Lean Thinking in the Workplace
Lean thinking has been used by organizations to bring practical benefits. It increases efficiency, reduces waste, and improves customer value. For instance, some companies have cut unnecessary steps in their production processes. This has saved costs and boosted product quality. Employees work together more effectively, concentrating on valuable tasks and minimizing non-essential ones. This improves job satisfaction and reduces stress. Leadership is vital for implementing lean initiatives.
It requires a cultural shift and a mindset of continuous improvement. By coaching, training, and setting clear expectations, leaders can empower their teams to embrace lean principles and create positive change. This ultimately leads to a more effective and high-quality work environment.
Real-World Applications: How Organizations Implement Lean
Industry-specific Lean Strategies
Lean strategies have been successfully used in the [industry name] industry. They involve identifying customer value, continuous improvement through experimentation, and reducing waste. Implementation of these strategies varies by industry, based on their specific needs. When implementing industry-specific lean strategies, it’s important to understand customer needs and ensure alignment of purpose, process, and people.
Challenges include resistance to change and lack of employee buy-in, while opportunities include increased efficiency and cost reduction. To overcome challenges, organizations can provide coaching, offer problem-solving techniques, and prioritize employee well-being and empowerment.
Getting Started with Lean Thinking: First Steps
Starting with Lean Thinking at work involves understanding customer value and constantly experimenting to achieve perfect value with no waste. Leadership is important for starting and maintaining Lean initiatives by aligning purpose, process, and people, and creating an environment for continual learning and problem-solving.
Establishing a culture of continuous improvement with Lean Thinking involves prioritizing people, using the 5S method, practicing Kaizen, and respecting others, regardless of their job description.
Implementing Lean in Your Daily Work
The Role of Leadership in Lean Initiatives
Leadership is important for driving and maintaining Lean initiatives in an organization. Leaders establish a clear vision for Lean implementation and provide resources for employees to embrace Lean principles. They communicate Lean thinking to all levels of the organization, integrate Lean concepts into daily operations, and provide training and coaching.
To foster a culture of continuous improvement and employee engagement in Lean initiatives, leaders involve employees in problem-solving, recognize and reward contributions to Lean practices, and create an environment that encourages experimentation and innovation.
Effective leadership is essential for creating a sustainable Lean culture that prioritizes delivering value to customers, eliminating waste, and promoting employee well-being and empowerment.
Building a Culture of Continuous Improvement
Building a culture of continuous improvement requires prioritizing people and embracing respect. This means focusing on the well-being and empowerment of employees to boost productivity and collaboration.
Implementing Lean thinking in the workplace is crucial for promoting continuous improvement. This involves strategies like understanding value, eliminating process waste, using Kanban, applying the 5S method and Kaizen, implementing the Andon principle, and respecting others.
Leadership also plays a vital role in fostering a culture of continuous improvement. By providing coaching and problem-solving techniques, leaders can guide employees to identify and eliminate waste, improve value, and elevate performance.
By concentrating on delivering value to customers and continuously improving processes, organizations can create a culture of continuous improvement rooted in Lean principles.
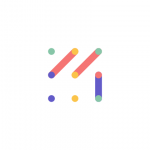
Vizologi is a revolutionary AI-generated business strategy tool that offers its users access to advanced features to create and refine start-up ideas quickly.
It generates limitless business ideas, gains insights on markets and competitors, and automates business plan creation.