Lean Management & Automation Tips
Lean management and automation are powerful tools for businesses. They help streamline operations and improve efficiency. Lean management focuses on eliminating waste and maximizing productivity. It helps companies achieve their goals with minimal resources. When combined with automation, productivity can be taken to the next level.
In this article, we’ll explore tips for effectively implementing lean management and automation in your organization. This can drive success and growth.
Key Objectives and Advantages of Lean Automation
Intensifying Employee Safety Measures
The company can make sure that all employees are actively involved in promoting and following strict safety measures at work. This can be done by involving them in safety planning and implementation, offering regular safety training, and encouraging open communication about safety concerns.
Implementing an anonymous safety reporting system and recognizing employees for their safety contributions are also helpful in promoting strict safety measures at work.
To enhance employee safety, it is important to integrate appropriate tools and technologies effectively. This includes assessing safety needs, involving relevant stakeholders in selecting and implementing safety tools, and providing comprehensive training on how to use new safety technologies. It’s also crucial to ensure that the safety tools are user-friendly and accessible to all employees.
The company can measure the return on investment for strict employee safety measures and ensure continuous improvement in this area by tracking safety incident reports, conducting regular safety audits, and gathering feedback from employees on safety measures. Analyzing safety-related costs and comparing them with productivity gains can help measure the return on investment for strict safety measures. Ongoing review and adjustments to safety programs based on performance data and input from employees and safety experts are key to ensuring continuous improvement in this area.
Shrinking Production Lead Times
To reduce production lead times, companies can use Lean automation. This approach combines Lean Six Sigma with business process automation.
First, focus on cutting waste in business processes before automating tasks. This leads to gradual improvements instead of big changes. By integrating automation and lean principles, companies can cut production lead times by removing waste, controlling costs, increasing safety, improving accuracy, and automating front- and back-office processes. The benefits of cutting production lead times include improved efficiency, productivity, quality, and accuracy, as well as reduced waste. Lean automation can also result in a 5X ROI, shorter development times, easier maintenance, and better data management and reporting.
Elevating Accuracy in Operations
Elevating accuracy in operations through lean automation involves refining processes to ensure the highest level of accuracy. This can be achieved by reducing waste, increasing safety, and improving overall quality. Implementing business process automation tools, such as cloud apps, can simplify maintenance, bridge the gap between people and machines, and improve data management and reporting.
These tools enable organizations to optimize their business processes before automating tasks, leadingto increased efficiency and productivity, while reducing waste and improving overall quality and operational costs.
Cutting Down Operational Costs
Lean automation helps reduce operational costs. It involves identifying and eliminating waste in front- and back-office operations. This can cut costs and improve productivity. Integrating tools and technologies streamlines processes and improves accuracy, reducing manual task costs. Leaders who reconfigure processes and teams before automation can see improvements in development times, maintenance, and data management.
By using these strategies and the right tools, businesses can achieve a substantial return on investment and pave the way for successful lean automation.
Identifying and Eliminating Waste Through Lean Principles
Lean principles help businesses identify waste in processes. This is done through small improvements rather than big changes. Common examples of waste include overproduction, waiting, unnecessary transportation, excess inventory, over-processing, defects, and underutilization of employees. By making process changes before automating, companies can reduce waste and improve efficiency.
Applying Lean thinking alongside automation reduces development times, simplifies maintenance, and improves datamanagement. Steps include redesigning processes, teams, and the organization, as well as evaluating automation tools based on their ability to execute and vision completeness. Companies can assess potential efficiency gains and cost savings using an ROI calculation before starting lean automation.
Deploying Automation in Front- and Back-office Operations
Deploying automation in front- and back-office operations has many benefits. These include reducing waste, controlling costs, increasing safety, improving accuracy, and streamlining processes.
Businesses can start by analyzing processes and workflows, identifying areas for improvement, and determining desired outcomes. Then, they can choose tools that align with these objectives.
To implement lean automation, businesses can redesign processes and teams, simplify maintenance, improve data management and reporting, and consider the ROI achievable through automation.
Following these steps can help ensure successful integration of lean automation into operations.
Selecting the Right Tools for Business Process Automation
When choosing tools for automating business processes, companies should consider two main elements: the ability to execute and the completeness of vision.
The ability to execute includes factors like functionality, usability, and design. Completeness of vision involves criteria such as market understanding, business model, and innovation.
Integrating suitable tools and technologies can improve the effectiveness of business process automation. It can also reduce development times, simplify maintenance, enhance data management, and bridge the gap between people and machines.
However, using inefficient tools for automating business processes can pose potential risks. If processes and the management team supporting them are not reconfigured before automation, the benefits are minimal or nonexistent.
Therefore, it’s crucial to consider how processes could be redesigned and how the organization could be reconfigured to maximize the benefits of automation.
Leveraging Internet of Things (IoT) in Lean Automation
IoT technology can improve accuracy and efficiency in lean automation processes. Smart sensors can collect real-time data on machinery performance and product quality. This data is then analyzed to identify areas for improvement and monitor overall equipment effectiveness, reducing waste and increasing productivity.
The advantages of using IoT in lean automation include streamlined processes, reduced human error, and improved decision-making through real-time data access. However, challenges such as cybersecurity risks, data overload, and integrating IoT systems with existing IT infrastructure must be carefully addressed for successful implementation.
Lean automation initiatives using IoT can be measured by tracking key performance indicators like improved lead times, reduced downtime, and increased employee satisfaction. Quantifying these improvements through data analytics can demonstrate the initiative’s business value and foster a culture of continuous improvement.
Unveiling Potential Risks in Automating Inefficient Processes
Automating inefficient processes has potential risks. One risk is limited benefits if processes and systems aren’t reconfigured before automation. This can lead to minimal improvements. Organizations should consider redesigning processes, teams, and even the organization itself to prepare for automation. Lean thinking can help reduce development times, simplify maintenance, bridge the gap between people and machines, and improve data management and reporting.
To mitigate risks, organizations should select business process automation tools based on their ability to execute and completeness of vision. Using a lean automation ROI guide, companies can calculate the return on investment by considering manual task time, task frequency, and associated costs. Making informed decisions and considering potential risks can help companies implement lean automation more effectively.
Mapping the Route to Implement Lean Automation
Analyzing Processes and Workflows
Lean automation is a combination of Lean six sigma and business process automation. It focuses on reducing waste in business processes before automating tasks. Lean Automation uses iterative improvements to adopt business technology, unlike traditional software delivery. The match between Business Process Automation and Lean isn’t perfect if the goal is to redesign the process rather than just automate it. Automation should always accompany changes in the business process.
Companies need to understand their existing and new processes before implementing any technology. Leaders are often tempted to dive straight into execution, but this can lead to automating inefficient processes. Lean thinking can reduce development times, simplify maintenance, bridge the gap between people and machines, and enhance data management and reporting.
Evaluating Workforce Engagement with Lean Principles
Lean automation improves operational efficiency. It also positively impacts workforce engagement with Lean principles. Lean automation tools help evaluate how effectively the workforce engages with Lean principles in their day-to-day operations.
For example, in the manufacturing industry, Lean automation enables tracking of productivity and waste reduction. This ensures that employees actively engage with Lean principles to drive value. Businesses can measure the impact of workforce engagement through Lean automation. This includes tracking improvements in worker safety, reduced lead times, enhanced accuracy, and cost savings.
These strategies emphasize the importance of evaluating and improving workforce engagement with Lean principles in a measurable and iterative manner. This is essential for sustained success in implementing Lean automation.
Integrating Appropriate Tools and Technologies
Lean automation uses tools and technologies to make work safer and more accurate. This means fewer mistakes and smoother processes for employees.
When choosing tools for automating business processes and using the Internet of Things (IoT) in lean automation, it’s important to consider how well the tools can perform and if they meet the organization’s needs.
To start lean automation, it’s essential to improve processes before automating, think about how processes can be changed for automation, and calculate the cost of manual tasks to see if automation makes financial sense.
By following these steps, companies can integrate the right tools and technologies in lean automation, saving money and making operations better.
Calculating Return on Investment for Lean Automation Initiatives
When organizations implement lean automation initiatives, they may have to pay for scope, design, and training at the start. They might also have to invest in business process automation tools.
But, they can measure the potential savings and efficiencies achieved from lean automation by looking at the time spent on manual tasks, how often these tasks are done, and the related costs.
To figure out the financial benefits of lean automation, organizations can use a basic ROI calculation. For example, they can assess the yearly costs of manual tasks.
When evaluating the return on investment for lean automation, organizations should consider key performance indicators. These include improvements in efficiency, reduced lead times, lower operational costs, and better accuracy.
By analyzing these factors, organizations can understand the impact and effectiveness of their lean automation initiatives more clearly.
Kickstarting Lean Automation: A Practical Guideline
Lean automation can improve employee safety and reduce production lead times by eliminating waste in business processes. This approach combines Lean six sigma with business process automation to make iterative improvements and systematic changes, resulting in a safer and more efficient work environment with shorter production lead times.
When choosing tools for business process automation in line with lean principles, companies should consider factors like ease of use, scalability, adaptability, and completeness of vision. Complete vision includes usability, integration capabilities, and continuous improvement.
The return on investment for lean automation initiatives can be calculated by considering time spent on manual tasks, frequency of task execution per month, and cost per hour. Evaluating these factors gives companies a clear understanding of potential yearly costs of manual tasks and the efficiency benefits they could achieve with lean automation.
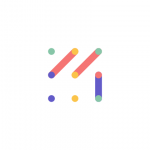
Vizologi is a revolutionary AI-generated business strategy tool that offers its users access to advanced features to create and refine start-up ideas quickly.
It generates limitless business ideas, gains insights on markets and competitors, and automates business plan creation.