Boost Workflow with 5S Automation
Do you want to make your workplace more efficient? 5S automation can help. By combining the 5S methodology with automation tools, businesses can streamline their processes, cut waste, and increase productivity.
In this article, we’ll discuss how 5S automation can transform your workplace and offer practical tips for getting started. If you’re ready to improve your workflow, keep reading to learn how 5S automation can benefit your business.
Understanding the 5S Methodology
Origins of 5S: Fundamental Japanese Terms
The 5S methodology is made up of five fundamental Japanese terms: Sort, Set in Order, Shine, Standardize, and Sustain. These terms represent the core principles of the methodology.
In English, these terms translate to the following actions:
- Eliminating unnecessary items.
- Arranging necessary items for easy access.
- Cleaning and inspecting the workplace.
- Creating standard procedures.
- Maintaining the discipline to sustain the improvements.
These actions are practical and straightforward, aligning with the simplicity and clarity of the methodology. Historically and culturally, these terms reflect the Japanese principles of order, cleanliness, and discipline, deeply rooted in the Japanese work culture.
The historical and cultural significance of these terms in the context of the 5S methodology lies in their ability to inspire a sense of ownership and pride in the workplace, promoting continuous improvement and efficiency.
Through the implementation of these fundamental Japanese terms, the 5S methodology drives workplace organization, visual management, and employee engagement, contributing to overall process improvement and performance.
Translating 5S: Meanings in English
The 5S methodology uses fundamental Japanese terms: Sort, Set in Order, Shine, Standardize, and Sustain. These terms are translated into English to convey their meanings clearly. “Sort” means distinguishing between necessary and unnecessary items. “Set in Order” means arranging necessary items for easy use. “Shine” means cleaning and inspecting the workplace. “Standardize” means maintaining and monitoring the first three S’s. And “Sustain” means ensuring the rules are followed daily.
Translating 5S from Japanese to English may face challenges due to cultural differences and the need for clear, concise language. Therefore, providing practical examples and explanations is important for successful implementation.
The Importance of 5S in Streamlining Manufacturing Processes
Implementing 5S in manufacturing helps streamline processes.
It creates organized and efficient work areas.
For instance, the “Sort” and “Set in Order” steps remove unnecessary items and organize necessary ones, reducing wasted time and movement.
Benefits include reducing waste, downtime, and creating a stable platform for improvement.
The “Shine” and “Standardize” steps involve regular cleaning and maintenance, reducing breakdowns and unplanned downtime.
To sustain 5S improvements, techniques like regular audits, training, visual management, and employee involvement can be used.
Visual tools like floor markings and labels remind employees of standards and engage them in maintaining them.
Top Benefits of Implementing a 5S System to Enhance Efficiency
Implementing a 5S system in the workplace offers several benefits for enhancing efficiency. This method helps to reduce waste, improve safety, and streamline processes by creating an organized and standardized work environment.
For example, by sorting and setting in order, employees can easily locate tools and materials, reducing downtime and increasing productivity. Additionally, the 5S system contributes to improving overall efficiency in manufacturing processes by creating a cleaner and more organized workspace.
By regularly shining and standardizing the workspace, employees are better able to maintain and sustain improvements, creating a culture of continuous improvement and quality. This methodology engages employees in taking ownership of their workspace and instills a culture of productivity and improvement.
Phase 1: Sort (Seiri) – Decluttering the Workspace
The Concept of Sort in 5S
The “Sort” concept in the 5S methodology means removing unnecessary items from the workspace. This helps create a more organized and efficient environment. It helps employees locate tools and materials easily, leading to improved productivity and safety.
Practical implementation techniques for Sort include:
- Creating designated storage spaces for essential items.
- Implementing a red-tagging system to identify unused items.
- Regularly reviewing and maintaining the organized workspace.
Real-world examples of successful Sort implementation:
- Automotive manufacturing facilities organizing tools and parts.
- Healthcare facilities streamlining supply storage.
- Office spaces decluttering paperwork and files.
These examples show how Sort in the 5S process improves workflow and operational efficiency in various industries.
Practical Implementation Techniques for Sort
Practical implementation techniques for the Sort phase in the 5S methodology include:
- Identifying and removing unnecessary items from the work area, like unused tools, outdated paperwork, or defective products.
- This process helps evaluate necessary and unnecessary items, leading to a more organized and efficient work environment.
Real-world applications can be demonstrated in a workplace by:
- Using visual aids like color-coding systems, floor markings, or shadow boards to help employees easily identify where items belong.
- Implementing labeling systems and organizational structures to maintain designated item locations and ensure accountability.
Key strategies for the Set in Order phase of 5S involve:
- Positioning frequently used items within easy reach using ergonomic design principles.
- Implementing storage solutions such as shelving, bins, or containers.
- Standardizing the layout of work areas to promote efficiency and productivity.
Real-World Applications of Sort
The 5S method can help improve efficiency and streamline operations in real-world manufacturing processes. It involves organizing and decluttering work areas to create a more productive and visually organized environment.
Some practical examples of the Sort phase (Seiri) of the 5S methodology include removing unnecessary items from a workstation, identifying and eliminating waste in the production process, and organizing tools and materials for easy access.
The benefits of implementing a 5S system in a real-world setting include reducing waste, increasing efficiency, promoting safety, and creating a work culture of continuous improvement.
By implementing the 5S methodology, companies can significantly improve their manufacturing processes, enhance workplace organization, and reduce the time and resources wasted on non-value-added activities.
Phase 2: Set in Order (Seiton) – Organizing for Flow
Defining Set in Order in the 5S Process
Step 2 in the 5S process is Set in Order. It’s about organizing and arranging things so they’re easy to use and access, which helps to eliminate wasted time.
To effectively set items in order, consider how often they’re used and put frequently used items in easy-to-reach places. Using visual cues like labels, shadow boards, and floor markings can also help maintain organization.
“Set in Order” is used in manufacturing facilities and offices to keep tools, equipment, documents, and supplies organized. This can include labeled storage areas and clear systems for organization.
Strategies for Setting Items in Order
One effective strategy for organizing items in the 5S methodology is to assign a specific place for each item in the workspace. This makes tools and materials easy to find, reduces the risk of misplacing items, and boosts productivity. Visual management tools like color-coded labels, shadow boards, and floor marking tape also help with organization and identification. They assist employees in returning tools to their designated places and signal when items are missing.
“Set in Order” improves workplace efficiency by cutting down the time spent searching for tools and materials. This leads to smoother workflow and reduced production lead times. For instance, a manufacturing facility using labeled and color-coded bins for parts and materials can significantly speed up workers’ tasks and minimize errors and accidents.
Successful examples of implementing “Set in Order” within the 5S framework include organizing workbenches or assembly stations to keep only essential tools and materials close by. Visual cues indicate where items should be returned after use. Ergonomic and adjustable shelving units, with clear labels and signage, enhance the visual and physical order of a workspace, boosting productivity and reducing downtime.
Illustrative Examples of Set in Order
During the “Set in Order” phase of the 5S process, items are organized to optimize workflow. This means arranging them logically and systematically. It can involve organizing tools based on how often they’re used, creating specific storage spaces for each item, and using visual indicators like labels and color-coding for easy identification.
Strategically placing items within a workspace helps employees find tools quickly, reduces the risk of accidents, and improves productivity. This approach is used in manufacturing facilities, hospitals, and offices. In manufacturing, tools and materials are arranged along assembly lines to streamline production. Hospitals organize medical supplies for quick access, while offices arrange workstations and supplies for efficient work processes.
To effectively set items in order as part of the 5S methodology, strategies like creating visual management systems, establishing clear storage locations, and involving employees in the organization process can be used. Visual management systems, like shadow boards and floor markings, help clarify where items belong. Involving employees ensures the organization meets their specific needs.
Phase 3: Shine (Seisou) – Cleaning and Inspecting
The Essence of Shine within 5S
The Shine phase is important in the 5S methodology. It focuses on keeping the workplace clean and organized. This helps prevent equipment issues, find defects, and ensure safety.
Regular cleaning prevents dust buildup, which can cause machinery breakdowns. To execute the Shine step effectively, organizations need to create cleaning schedules, set cleanliness standards, and provide tools for employees.
This promotes a culture of cleanliness and discipline, leading to improved productivity and morale. Shine creates a visually appealing, safe workspace, promoting efficiency and pride among employees.
Executing the Shine Step Effectively
The Shine step in the 5S methodology is about thorough cleaning and inspection. This can be done in a manufacturing environment by using cleaning checklists, investing in good cleaning tools, and training employees on the importance of a clean workspace.
Clear expectations and standards for cleanliness can enhance efficiency and productivity. It reduces the risk of equipment malfunctions, minimizes time spent searching for tools and materials, and creates a safer workplace.
Effective execution of the Shine step is essential for maintaining a well-organized and productive manufacturing environment.
Phase 4: Standardize (Seiketsu) – Creating Consistency
Defining Standardization in the 5S Framework
Standardization is very important in the 5S framework. It helps to keep things consistent and orderly in the workplace. By setting up the same processes and procedures for everyone, standardization makes sure that everything is organized in the same way. This makes things more efficient and reduces the chance of mistakes. Visual cues, clear work instructions, and using the same tools and equipment are some ways to bring standardization into the 5S framework.
These methods help employees follow the standards, making the workplace organized, safe, and good for getting work done.
Methodology for Standardizing Workflow
Workflow standardization in the 5S methodology involves following key steps: Sort, Set in Order, Shine, Standardize, and Sustain. These steps help create efficient work areas and promote continuous improvement. Techniques like visual management tools and color coding ensure consistency.
Sort removes unnecessary items, Set in Order organizes remaining items, and Shine emphasizes cleanliness.
Standardize lays out guidelines for maintaining order, and Sustain ensures practices become ingrained in workplace culture.
Following these steps helps businesses establish and maintain a standardized workflow within the 5S framework, leading to productivity and a culture of quality and improvement.
Phase 5: Sustain (Shitsuke) – Maintaining Discipline
Fundamentals of Sustain in 5S
The 5S methodology consists of Sort, Set in Order, Shine, Standardize, and Sustain. These activities help create and maintain efficient work areas, promoting continuous improvement. Engaging operators in owning their workspace and fostering a culture of quality and productivity are crucial for long-term success. Ongoing training and education on the 5S methodology and its benefits reinforce the importance of a clean and organized workplace.
Sustaining the benefits involves reducing waste, minimizing downtime, and establishing a stable platform for improvement activities. This fosters an environment conducive to continuous improvement, enhancing workplace efficiency and effectiveness.
Approaches to Sustaining Improvements
To make sure that improvements made through the 5S methodology last, organizations can use these strategies:
- Engage all levels of the workforce in continuous improvement to create a culture of ownership and accountability.
- Provide regular training and education on the 5S principles to build awareness and commitment to maintaining standards.
- Establish clear visual controls and audits to monitor the effectiveness of Sort, Set in Order, Shine, Standardize, and Sustain practices.
- Maintain discipline and uphold 5S standards by implementing these approaches.
- Support and recognize employees who actively contribute to the sustained success of 5S practices.
This approach encourages employees to embrace the methodology and play an active role in sustaining improvements in the workplace.
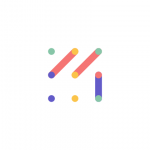
Vizologi is a revolutionary AI-generated business strategy tool that offers its users access to advanced features to create and refine start-up ideas quickly.
It generates limitless business ideas, gains insights on markets and competitors, and automates business plan creation.