Understanding Lean: The 5 Core Principles Explained
Lean principles are changing how companies operate. They lead to better efficiency and overall success. Understanding these principles is important for anyone using this approach in their business.
In this article, we will look at the 5 key principles of Lean and how they can bring big improvements in productivity, quality, and customer satisfaction. Whether you’re a business owner, manager, or employee, knowing these principles will help you streamline processes and keep making things better.
The Essence of Value from the Customer’s Perspective
Customers decide what is valuable to them based on their needs and preferences. This can include things like quality, price, convenience, and the overall experience. Understanding what customers value involves identifying all the steps in the process that directly contribute to meeting their needs. By doing this, organizations can get rid of any wasteful activities and focus on delivering value more efficiently.
Continuous improvement in providing value to the customer can be achieved by streamlining processes, gathering and analyzing customer feedback, and empowering employees to identify and address areas of improvement. These strategies ensure that the organization consistently meets and exceeds customer expectations, ultimately enhancing the overall value provided to the customer.
Identifying Each Step in the Value Stream
Each step in the value stream can be understood by analyzing the sequence of activities involved in producing a product or delivering a service. Techniques like value stream mapping can visually represent the flow of material and information, highlighting each step. This provides a comprehensive view of the entire value stream, including non-value added activities and improvement opportunities.
Understanding each step is crucial when implementing lean principles as it helps identify bottlenecks, waste, and inefficiencies. With insight into each step, companies can focus on eliminating waste and delivering better value to customers, a core principle of lean methodology.
Creating Flow by Eliminating Waste
Waste in a value stream can be found and removed by analyzing the process. This means finding activities that don’t add value, like overproduction, waiting, or unnecessary movement, and getting rid of them to make the value flow smoother.
Methods like 5S and visual management can help organize the workspace and reduce waste, leading to better flow. Using pull-based systems, where work is only done when needed, can also improve the value stream. This reduces extra inventory and wait times, making the process more efficient and valuable for the customer.
Strategies for Establishing Pull-Based Systems
To establish pull-based systems in a lean environment, organizations can employ some key strategies. They can implement a kanban system for inventory control, where items are only restocked when needed. They can also set up production cells that produce small, customer-specific batches in response to pull signals.
Organizations can effectively harness the power of pull to drive efficiency and value creation by using just-in-time (JIT) manufacturing. JIT manufacturing focuses on producing goods only as needed, reducing excess inventory and waste.
Additionally, transitioning from a push-based to a pull-based system involves techniques such as analyzing customer demand patterns, establishing collaboration between different departments, and implementing visual management tools like Andon systems to detect production issues in real time.
Challenges during this transition may include resistance to change from employees, initial disruptions to production flow, and the need for accurate demand forecasting to avoid under or overproduction.
Aiming for Perfection Through Constant Improvement
Continuous improvement is very important for reaching perfection in a lean organization. Organizations achieve this by identifying and eliminating waste, inefficiencies, and non-value-added activities. Lean principles guide this process by providing a structured approach to continuous improvement.
For example, creating flow encourages streamlining processes and minimizing interruptions, which promotes a culture of constant refinement. Using a pull system ensures that products are only made based on customer demand, reducing inventory waste and emphasizing quality. To promote this culture, lean organizations can implement strategies like regular employee training and involvement in improvement initiatives, creating an environment where all members contribute to continuous improvement. This fosters a workplace where continuous improvement is embraced and embedded in the organization’s DNA, ultimately leading to perfection in operations and processes.
Lean Principle Applications in Engineering
Value and Its Importance in Lean
Understanding and mapping the value stream in lean processes can help organizations improve and reduce waste. This is done by visualizing the entire process from start to finish.
This allows for the identification of non-value adding activities and areas of waste, such as overproduction, waiting times, and excess inventory.
Eliminating waste and enhancing flow in lean operations can be achieved through techniques such as 5S, standard work, and visual management. These techniques create a more efficient and streamlined process, reduce lead times, and improve overall productivity.
Using pull-based systems in a lean environment delivers value more efficiently and effectively to customers by producing products or services in response to actual customer demand.
Understanding and Mapping the Value Stream
Understanding and mapping the value stream allows organizations to identify each step in the process and recognize the value added at each step. This helps them pinpoint areas of waste and inefficiency, leading to opportunities for improvement.
Techniques such as visual management, standard work, and 5S can be used to eliminate waste and enhance flow within the value stream.
Establishing a pull-based system allows organizations to respond directly to customer demand rather than overproducing. This helps in striving for perfection through continuous improvement. Practices like kaizen events, root cause analysis, and error-proofing ensure that high-quality products or services are consistently delivered.
Implementing these strategies helps organizations create a culture of continuous improvement and respect for people, ultimately delivering better value to customers and eliminating waste in their processes.
Techniques to Eliminate Waste and Enhance Flow
In Lean methodology, there are techniques to eliminate waste and enhance flow.
For example:
- Identify and reduce unnecessary inventory and overproduction. This can lead to a more efficient flow of work.
- Implement visual management tools, such as kanban boards, to help teams visualize their work and monitor value flow.
- Establish pull-based systems, where work is initiated in response to customer demand. This can reduce waste in the value stream.
- Pursue constant improvement through practices like Kaizen events and daily stand-up meetings. This helps teams continuously address inefficiencies for a more valuable customer experience.
Harnessing the Power of Pull
Pull-based systems are part of lean principles. They involve using techniques like kanban systems and Just-In-Time inventory management. These methods help organizations meet customer demand in real time. They ensure that products are made only when needed, improving flow and reducing waste.
By using a pull-based approach, organizations can be more flexible and reduce lead times. This ultimately boosts efficiency and customer satisfaction. To implement pull-based systems, organizations need a cultural shift emphasizing employee empowerment to spot and solve problems. This fosters continuous improvement and striving for perfection in lean principles by constantly optimizing processes and reducing waste.
Striving for Perfection: Continuous Improvement
To improve continuously, organizations can use pull-based systems. They can do this by implementing strategies like Kanban boards. These help visualize work and control workflow. Just-in-time scheduling can also be used to avoid overproduction and unnecessary inventory.
In engineering, Lean principles focus on constant improvement. This is done by implementing practices like value stream mapping. This helps identify and eliminate non-value-added processes. Kaizen events are also used to foster a culture of continuous improvement and employee involvement.
To improve flow and eliminate waste, techniques like the 5S methodology can be used. This helps organize the workplace and standardize processes. Visual management tools are also implemented to track performance and identify abnormalities.
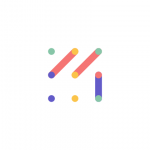
Vizologi is a revolutionary AI-generated business strategy tool that offers its users access to advanced features to create and refine start-up ideas quickly.
It generates limitless business ideas, gains insights on markets and competitors, and automates business plan creation.