Lean Simplified: The Three Key Methodologies
Lean methodologies are changing how businesses work. They streamline processes and reduce waste.
In this article, we’ll explain three important methodologies: Value Stream Mapping, 5S, and Kaizen. Whether you’re a business owner, manager, or employee, learning these principles can greatly impact your organization’s efficiency and success. Lean doesn’t have to be complicated—by understanding these three methodologies, you can start improving your business.
The Essence of Lean Simplified
Lean methodology focuses on continuous improvement and eliminating waste to provide the highest value to consumers. It compares with Agile and Kanban but can also combine methods for greater efficiency. There are synergies between Lean and Agile, for example, integrating Agile’s adaptive approach with Lean’s waste reduction.
Management plays a role in fostering Lean principles and implementing Lean methodologies by driving cultural change, supporting process improvements, and developing problem-solving skills in employees. Effective management ensures the successful implementation of Lean principles, leading to improvements in quality, efficiency, and profitability.
The Historical Evolution of Lean Methodology
The Lean Methodology has evolved historically through key events and influences. The development of the Toyota Production System in Japan and its global adoption and adaptation have played a major role.
Continuous improvement is crucial to Lean Methodology. It focuses on refining internal processes to maximize customer value. This principle has driven Lean Methodology’s historical evolution as a systemic approach to eliminating waste and creating value.
Furthermore, Lean Methodology highlights the importance of respecting people and workplace culture. It recognizes that individuals at all levels of the organization contribute to process improvement and innovation. This approach values employee management and talent development as essential components of Lean Methodology’s historical evolution.
The Foundational Elements of Lean
Continuous Improvement as a Lean Cornerstone
Continuous improvement is a big part of Lean methodology. It focuses on refining internal processes to deliver the most value to consumers. Anything that doesn’t add value to the product for the customer is seen as inefficient and should be removed. The continuous improvement cycle in Lean includes managing processes, understanding reality, and visual communication. Lean organizations aim to continually improve to deliver value to customers by optimizing internal processes.
This helps to cut waste, boost efficiency, and make sure the company meets customer needs, all of which are important for high-quality products and services.
The Continuous Improvement Cycle
The Continuous Improvement Cycle in lean methodology consists of three key components: improving processes, increasing efficiency, and ensuring customer alignment. The cycle aims to continuously refine and optimize internal processes to eliminate waste and provide customers with the highest value in a product or service.
By focusing on improving processes and increasing efficiency, the Continuous Improvement Cycle contributes to delivering value to customers in lean principles. This is achieved by streamlining operations, reducing costs, and minimizing lead times. In turn, this allows organizations to produce higher quality products and services that meet or exceed customer expectations.
The Continuous Improvement Cycle plays a crucial role in empowering employees and fostering a culture of continuous improvement in lean methodology. It encourages employees at every level of the business to identify and eliminate waste, thus contributing to the overall success of the organization. By involving employees in the improvement process, organizations can tap into the collective knowledge and expertise of their workforce to drive ongoing operational enhancements and increase organizational productivity.
Respect for People and Culture
A company can show respect for different cultures and backgrounds in its workforce by:
- Using diversity and inclusion programs
- Celebrating cultural holidays and traditions
- Providing language resources for employees who speak different languages
- Implementing mentorship programs and diversity training
- Creating affinity groups for people of different cultural backgrounds
- Promoting open and respectful communication
- Encouraging leadership opportunities for individuals from diverse backgrounds to ensure their voices are heard
Delivering Value to Customers
To deliver value to customers, organizations can use three Lean methodologies:
- Improve processes.
- Increase efficiency.
- Ensure customer alignment
This helps eliminate wasteful activities and focus on delivering high-value products or services.
By refining internal processes, organizations can meet customer needs and expectations. This includes waste reduction and optimizing production processes for better quality.
Measuring customer satisfaction through surveys and feedback forms supports continuous improvement. Analyzing customer feedback helps identify areas for improvement and make necessary adjustments to deliver better value.
Empowering Employees
Leadership is important. It supports and empowers employees, so they feel a sense of ownership and contribute meaningfully to the organization. Leaders can do this by providing clear expectations, setting achievable goals, and offering support and guidance. Recognizing and rewarding employee contributions can further empower them to excel in their roles.
To create a culture of empowerment, organizations can implement strategies such as open communication, transparent decision-making processes, and opportunities for employee involvement in decision-making. Valuing diverse perspectives fosters a sense of inclusion and innovation. Providing opportunities for professional growth and development enables employees to take on new challenges and contribute to continuous improvement.
Organizations should provide necessary resources and training to empower employees. This includes access to technology, tools, and support, as well as ongoing training programs. Encouraging a growth mindset and providing a platform for sharing ideas and knowledge can further empower employees to drive positive change and contribute to organizational success.
Team Dynamics and Process Focus
Focusing on team dynamics in Lean methodologies can improve effectiveness. It promotes collaboration, communication, and synergy among team members. This encourages open dialogue and knowledge sharing, fostering a work environment conducive to problem-solving and innovation.
Strategies like regular team meetings, workshops, and brainstorming sessions can align team dynamics and process focus with Lean principles. Assigning specific roles and responsibilities within the Lean process ensures clarity and accountability, contributing to more efficient implementation.
Emphasizing team dynamics can contribute to the successful implementation of Lean methodologies. It fosters a sense of ownership, motivation, and commitment among team members. This leads to increased engagement and productivity, as well as a higher likelihood of sustaining continuous improvement efforts.
By investing in team dynamics, organizations can create a culture supportive of Lean principles, ultimately leading to improved quality, efficiency, and customer satisfaction.
Comparing Lean With Other Improvement Methodologies
The Synergy of Lean, Agile, and Kanban
The synergy of Lean, Agile, and Kanban enhances organizational efficiency and productivity. They focus on waste reduction, continuous improvement, and customer value.
Lean emphasizes continuous improvement by refining internal processes to deliver the highest customer value. Agile promotes iterative development, adaptive planning, and customer collaboration. This allows organizations to respond quickly to changing market demands.
Kanban facilitates visual management and workflow optimization, ensuring smooth and efficient task execution.
Key principles and practices that facilitate the integration of Lean, Agile, and Kanban include regular process reviews, cross-functional collaboration, and feedback-driven improvement cycles.
Management can support the adoption of these methodologies by fostering a culture of continuous improvement, providing resources for training and implementation, and leading by example through their active participation in Lean, Agile, and Kanban initiatives within the organization.
Implementing Lean Methodologies for Enhanced Results
Embarking on the Kanban Journey: Initial Steps
The initial steps an organization should take when starting with Kanban involve:
- Understanding Lean management principles
- Identifying areas of waste
- Committing to continuous improvement.
By analyzing existing processes, inefficiencies can be determined and processes can be streamlined to eliminate waste and increase efficiency.
Empowering teams and employees to embrace Kanban and Lean methodologies involves:
- Providing necessary training, tools, and resources
- Implementing visual management systems, like Kanban boards, to make workflows transparent and accessible.
To ensure successful adoption of Kanban and Lean principles, organizations can:
- Set clear goals
- Provide ongoing training and support
- Foster a culture of continuous improvement.
Utilizing software solutions like ProcessMaker for business process management and workflow automation can streamline processes and ensure consistent application of Lean principles throughout the organization.
Lean Solutions and Strategies
Lean methodology focuses on continuous improvement rather than just eliminating waste. It was introduced to the West by James Womack and Daniel Jones, who outlined five core principles. The goal is to optimize internal processes to provide the highest value to customers. Lean methodology identifies eight types of waste and encourages continuous improvement at all levels of the business.
To enhance results, organizations can implement lean solutions by reducing waste and refining internal processes to deliver greater value to customers.
Effective management is crucial for fostering lean principles within an organization. Management plays a key role in implementing lean principles and achieving improvements in quality, efficiency, and profitability. Leadership and support from management are essential for promoting a culture of continuous improvement and waste reduction.
Management’s Role in Fostering Lean Principles
Management is important for fostering lean principles in an organization. They can do this by encouraging open communication, collaboration, and a willingness to embrace change.
Management can empower employees by setting clear expectations, providing resources, and encouraging ideas for improvement. By offering training opportunities, management helps employees enhance their skills in lean methodologies.
They can also align the organization’s goals by setting KPIs related to quality, speed, and customer satisfaction.
Additionally, management can promote a customer-centric mindset throughout the organization. This includes emphasizing the importance of customer alignment and value delivery in all aspects of the business.
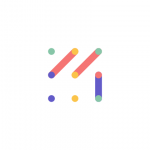
Vizologi is a revolutionary AI-generated business strategy tool that offers its users access to advanced features to create and refine start-up ideas quickly.
It generates limitless business ideas, gains insights on markets and competitors, and automates business plan creation.