Top Advantages of Lean Methodology
Lean methodology is becoming popular in many industries because it helps to simplify processes and boost efficiency. This approach, used in manufacturing and software development, offers clear benefits. By cutting out waste and maximizing value, businesses can achieve higher productivity, enhanced customer satisfaction, and lower costs.
In this article, we’ll look at the key advantages of lean methodology and how it can help organizations of any size. Whether you’re a small startup or a big corporation, knowing the benefits of lean methodology is important for staying competitive in today’s fast-paced market.
Understanding Lean Methodology
Five Pillars of Lean Thinking
The Five Pillars of Lean Thinking focus on boosting efficiency and reducing costs. They emphasize identifying and eliminating waste. Lean Thinking helps organizations streamline processes, minimize unnecessary steps, and improve productivity.
For example, by removing non-value-adding activities in a manufacturing process, a company can improve efficiency and reduce costs.
To build strong customer relationships and improve transparency, organizations can use strategies like value stream mapping and visual management. Value stream mapping helps businesses understand the entire process from customer order to delivery, leading to better responsiveness to customer demand. Visual management tools, such as Kanban boards, make work visible, allowing for better communication and collaboration with stakeholders. This can help build trust and foster stronger relationships.
Lean Thinking can promote a continuous improvement culture and increase team engagement by encouraging a focus on learning and experimentation. By seeking ways to eliminate waste and improve processes, employees are engaged in making meaningful contributions. It also promotes a collaborative environment where employees can contribute ideas for improvement, leading to increased team engagement and a culture of continuous learning and growth.
Eliminating the Eight Wastes of Lean
The elimination of the eight wastes of lean can greatly improve efficiency and reduce costs in an organization. These wastes are defects, overproduction, waiting time, non-utilized talent, transportation, inventory, motion, and extra processing. Companies can streamline their processes and resources by identifying and removing these wastes.
For instance, reducing unnecessary inventory and minimizing extra processing in manufacturing can lead to cost savings and increased productivity. In a continuous improvement culture, strategies like value stream mapping, just-in-time production, and employee empowerment can be used to identify and eliminate the eight wastes of lean.
Empowering employees to identify and address defects in real-time can lead to continuous improvement and waste reduction. The elimination of these wastes contributes to strong customer relationships and enhances stakeholder transparency by focusing on value and reducing waste.
Minimizing waiting time and overproduction can result in faster delivery and improved customer satisfaction. Additionally, increasing transparency in the value stream allows stakeholders to better understand the process and contribute to its improvement.
Boosting Efficiency
To improve efficiency in the workplace, you can:
- Implement standardized work procedures
- Optimize work layouts
- Cross-train employees
- Use advanced planning and scheduling tools for better coordination
- Minimize waste and improve supply chain management
- Invest in technology and automation
- Implement continuous improvement processes
- Foster a culture of innovation for long-term efficiency gains
Minimizing Bottlenecks
The organization can find and prioritize bottlenecks in its processes. It can do this by analyzing the workflow using techniques like value stream mapping and process observation. This helps them figure out where work is getting stuck or delayed. They can then find the root causes of these bottlenecks.
Once they know the bottlenecks, they can use strategies and tools like workload balancing, cross-training, and standardizing work processes to reduce or eliminate them. They can also use technology and automation to make repetitive tasks easier and improve the flow of work.
The organization can track key performance indicators like cycle time, lead time, and throughput to see if their efforts are working. These metrics show how the strategies and tools are affecting the organization. This helps them make changes for continuous improvement.
Reducing Costs
One effective strategy to identify and eliminate unnecessary expenses in the organization is through the implementation of Lean methodology. Lean methodology focuses on minimizing waste and optimizing processes to help pinpoint areas where costs can be reduced without sacrificing quality.
Streamlining processes and operations is another way to reduce production and operational costs. This can be achieved by identifying bottlenecks and inefficiencies and finding creative solutions to improve workflow and resource allocation, ultimately leading to cost savings.
Additionally, organizations can explore opportunities to renegotiate contracts or seek alternative suppliers to minimize expenses and reduce costs. Engaging in strategic partnerships and leveraging market competition can potentially lower production and operational costs while maintaining the quality of products or services.
Adaptive and Flexible Systems
Companies can use adaptive and flexible systems to improve how they work and save money.
They can do this by making their processes more efficient and cutting out unnecessary steps.
By using lean methods, companies can find and get rid of activities that don’t add value, reduce delays, and use their resources better.
Encouraging employees to find ways to do things better, working together to share ideas, and teaching lean principles can help create a culture of always getting better.
Tools for planning and scheduling can be used to make the most of adaptive systems, keeping everyone involved and informed, and helping teams work better together.
These tools can also show where things can be improved and make it easier to make those improvements.
Enhancing Stakeholder Transparency
Establishing Strong Customer Relationships
Businesses can effectively communicate and engage with their customers. This helps to establish strong relationships. They can prioritize customer feedback and actively listen to their needs and concerns. Strategies like conducting surveys, seeking input on product development, and responding promptly to customer inquiries and issues are important.
Additionally, businesses can ensure customer satisfaction and loyalty for long-term relationships. This can be achieved by providing personalized experiences, offering exclusive promotions or rewards, and maintaining consistent communication through various channels.
Personalizing interactions and experiences with customers is crucial. This can be done through targeted marketing efforts, keeping track of past interactions and preferences, and addressing individual customer needs and preferences.
By focusing on these strategies, businesses can cultivate trust and loyalty. This will lead to strong and lasting relationships with their customers.
Cultivating a Continuous Improvement Culture
Organizations can encourage continuous improvement among their employees. They can do this by promoting collaboration, idea sharing, and a focus on ongoing efficiency. This includes creating regular opportunities for team members to share feedback, ideas, and best practices through meetings, forums, and digital platforms.
Employees can take an active role in the continuous improvement process. They should be empowered to identify areas for improvement, experiment with new approaches, and provide constructive feedback to their colleagues.
Senior leadership also plays a role in cultivating and sustaining a culture of continuous improvement. They should set an example, provide resources and support for improvement initiatives, and recognize and reward innovation and positive change efforts.
By integrating these strategies and engaging employees at all levels, organizations can create a workplace culture where continuous improvement is valued, supported, and championed.
Increasing Team Engagement
Organizations can create a work environment that fosters increased collaboration and communication among team members by encouraging open dialogue, providing clear channels for feedback, and promoting a culture of transparency. Team-building activities, regular check-ins, and cross-functional team projects can also enhance collaboration and communication among team members.
Additionally, providing opportunities for team members to share their ideas and suggestions for process improvement can empower them and increase their engagement and commitment to the team’s goals.
Recognizing and acknowledging the efforts and contributions of team members can boost their morale and overall engagement. This can be achieved through various methods such as public recognition, appreciation emails, shout-outs in team meetings, and reward programs. Celebrating team milestones, achievements, and personal accomplishments can also contribute to fostering a positive and engaging work environment. By involving team members in decision-making processes and recognizing their valuable contributions, organizations can create a sense of ownership and empowerment that ultimately leads to increased team engagement.
Using Advanced Planning and Scheduling Tools
Advanced planning and scheduling tools help minimize bottlenecks and boost efficiency in manufacturing and production. They streamline the production schedule, identify potential issues, and optimize resource allocation, leading to smoother workflow and increased productivity.
These tools also reduce costs and improve stakeholder transparency. They offer benefits like better resource management, reduced lead times, and improved visibility into the production process. This results in cost savings, accurate forecasting, and enhanced collaboration among stakeholders.
Furthermore, these tools cultivate a culture of continuous improvement and increase team engagement within an organization. By providing real-time data on performance and progress, they empower teams to identify areas for improvement, implement changes, and measure the impact. This fosters a continuous improvement mindset and enhances team engagement in driving operational enhancements.
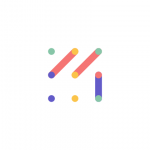
Vizologi is a revolutionary AI-generated business strategy tool that offers its users access to advanced features to create and refine start-up ideas quickly.
It generates limitless business ideas, gains insights on markets and competitors, and automates business plan creation.