Brainstorming Magic: Kaizen Style!
Welcome to the magic of brainstorming, Kaizen style! If you want to enhance your creativity and problem-solving skills, you’re in the right place.
Kaizen is a Japanese business philosophy that emphasizes continuous improvement. When applied to brainstorming, it can do wonders. In this article, we’ll look at how Kaizen-style brainstorming can help you generate new ideas, enhance team collaboration, and achieve better results.
Get ready to unleash your creative potential with this innovative approach to brainstorming!
Exploring the Essentials of Kaizen Events
Understanding the Kaizen Philosophy
The Kaizen philosophy is all about continuous improvement. It means making small, gradual changes to processes, products, or services to make them better. This philosophy encourages employees at all levels to suggest and make improvements, leading to a culture of continuous learning and innovation.
Kaizen focuses on getting rid of waste and making processes better. This helps achieve maximum productivity and efficiency. The key principles and values of Kaizen include involving all employees, promoting teamwork and collaboration, using data to make changes, and committing to ongoing training and education.
These principles are essential for creating an environment that supports continuous improvement and excellence in the organization.
Determining When to Implement Kaizen Events
Determining when to implement a Kaizen event involves identifying current pain points or areas of opportunity within the organization. These could include urgent problems, the need to hit target goals, or the opportunity for cross-functional collaboration. Implementing a Kaizen event aligns with the organization’s strategic goals by fostering a Kaizen culture focused on continuous process improvement.
To successfully execute a Kaizen event, it is important to ensure that the necessary resourcesand support are available, such as involving individuals, forming a Kaizen committee, providing organization, and engaging all team members.
Identifying the Key Players in Kaizen Events
The people involved in a Kaizen event are employees, managers, and owners. They work together to find issues, offer solutions, and make process improvements. This leads to the formation of a Kaizen committee and regular updates to keep everyone included.
Their roles involve preparation, organization, and communication. They form a committee, hold weekly meetings, and use visual tools to solve problems. They provide resources, involve the whole team, and focus on continuous improvement.
Having the right people in these roles is crucial for the event’s success. Their involvement leads to good communication, collaboration, continuous improvement, and engagement in the change process.
The Lifecycle of a Kaizen Event
Preparation: Setting the Stage for Success
In the preparation stage for a Kaizen event, there are important steps and actions to take. These include defining the problem, selecting the right team members, and providing necessary training and resources.
Identifying the key players means reaching out to those with the required knowledge and stake in the process. It’s important to ensure their availability and commitment to the event.
Bringing together the right team members, such as employees, managers, and owners, is crucial for successful preparation and implementation.
The important elements of setting the stage for success include organization, engaging team members, and documenting progress.
By focusing on effective communication, collaboration, and continuous improvement, these elements contribute to the overall success of the event.
This requires fostering a Kaizen culture, providing resources, and following specific steps for the implementation of the event.
Execution: Day-by-Day Breakdown
The recommended day-by-day breakdown for executing a Kaizen event involves several tasks and milestones:
- Day 1: Focus on preparation and training, assembling the right team, setting the event agenda, identifying the current and end-state process, educating the team on the specific issue, and ensuring everyone understands the objectives and expected outcomes.
- Days 2 and 3: Implementation is a key focus with the team finding and testing solutions to the identified issues. They should use a data-driven approach and capture relevant data on any changes made.
- Last Day: Dedicated to follow up and refining improvements, documenting changes, speaking with individual team members, and identifying areas needing further improvement.
To ensure successful implementation, the team should maintain effective communication and collaboration, focus on continuous improvement, and provide ample resources to support the team throughout the event.
Post-Event: Ensuring Continuous Improvement
After a Kaizen event, feedback can be gathered in several ways. This includes conducting interviews with team members, managers, and owners involved in the event. Surveys can also be used to collect quantitative data on the impact of the event and the effectiveness of the changes made. Regular meetings can then be scheduled to discuss progress and challenges after the event.
To measure the impact of changes, organizations can use key performance indicators (KPIs) related to quality, productivity, cost, and time management. Data on these KPIs can be collected before, during, and after the event to assess the effectiveness of the improvements. This data can then be analyzed to identify areas that need further attention and to ensure continuous improvement.
A system for regular review and reflection on the outcomes of the Kaizen event involves scheduling frequent follow-up meetings to assess the impact of the changes made. These meetings can provide an opportunity to review the successes and failures of the event, identify areas for ongoing improvement, and celebrate achievements.
Additionally, documenting the progress made and lessons learned from each event can serve as a valuable resource for future improvement initiatives.
Critical Steps for Leading a Kaizen Event
Training Team Members for Kaizen Initiatives
Training team members for Kaizen initiatives involves:
- Engaging all employees, managers, and owners
- Forming a Kaizen committee
- Providing resources
To ensure effective preparation, a leader should focus on the following:
- Organization, comfort, and communication
- Engaging team members
- Documenting progress
Best practices for implementing Kaizen event training include:
- Asking employees to identify problems and submit solutions
- Using visual tools and techniques like value stream mapping, 5-S, and pull systems
- Implementing Kaizen events through weekly committee meetings while retaining all team members.
Best Practices for Kaizen Event Implementation
To successfully execute a Kaizen event, businesses can:
- Form a Kaizen committee
- Provide resources
- Effectively communicate with team members
This means engaging all individuals, setting clear objectives, and reporting changes.
Training for Kaizen initiatives can maximize impact by using visual tools and techniques like:
- Value stream mapping
- 5-S
- Pull systems
These methods help team members understand and implement specific solutions for process improvements.
Best practices for implementing Kaizen events:
- Engage all team members
- Document progress
- Maintain continuous improvement through weekly committee meetings
Focusing on effective communication, collaboration, and providing resources are vital for the success of a Kaizen event.
Operating Within the Kaizen Culture
Avoiding the Eight Wastes of Lean with Kaizen
Kaizen Events help organizations find and remove waste in lean manufacturing. They target eight major areas of waste: transportation, inventory, motion, waiting, overproduction, overprocessing, defects, and skills underutilization. Value stream mapping is used during Kaizen events to identify and eliminate non-value adding activities.
Engaging employees and forming a Kaizen committee creates a culture of continuous improvement. This ensures processes are streamlined and resources are fully utilized. Integrating Kaizen principles also prevents waste by establishing a structured problem-solving approach and encouraging cross-functional collaboration. This addresses systemic issues surrounding the eight areas of waste holistically.
Transport
Transport is very important in Kaizen events. It can have a big impact on process improvement. In Lean principles, there are eight wastes of transport that can make things inefficient and costly. Some examples are unnecessary movement of materials, too much handling, and transport delays.
To reduce waste and make transportation better in a Kaizen event, businesses should focus on making the movement of goods and materials smoother, cutting out unnecessary handling, and making transport times shorter. Good ways to improve transportation in a Kaizen context are using visual tools like value stream mapping to find inefficiencies, using pull systems to control material movement, and involving all team members in the process to keep improving. Also, weekly meetings and regular communication are important to stay focused on transportation and reducing waste.
Inventory
Inventory management is a critical part of Kaizen events. It involves keeping the right amount of stock, reducing excess or old items, and improving processes to minimize waste and increase efficiency.
Using Kaizen principles, businesses can streamline inventory processes by identifying and eliminating unnecessary steps or materials.
Employees from different levels of the organization can contribute to regular brainstorming sessions to make incremental changes. This approach supports the Kaizen philosophy of continuous improvement.
Managing inventory reduces waste by ensuring the right materials and supplies are available when needed, minimizing excess and avoiding unnecessary accumulation.
This aligns with the Kaizen principle of eliminating waste and emphasizes the importance of continuous improvement to achieve greater efficiency and productivity.
Motion
Motion is very important in Kaizen events. It helps businesses make breakthroughs in process improvements. Analyzing and minimizing unnecessary motion can make processes more efficient. Strategies like value stream mapping, 5-S, and pull systems can help identify and reduce unnecessary motion. Involving employees in identifying problems and using visual tools for problem-solving can also help.
Holding weekly committee meetings and involving all team members in Kaizen events can reduce the impact of unnecessary motion. Addressing motion-related issues is essential for streamlining processes and getting better results in the short and long term.
Waiting
Common sources of “waiting” within a process or project include:
- Long approval processes
- Waiting for feedback
- Delays due to dependencies on other teams or departments
These bottlenecks can slow down production and hinder progress, leading to a less efficient and effective workflow. Excessive waiting can result in:
- Missed deadlines
- Increased idle time
- Decreased motivation among team members
To minimize or eliminate waiting and improve productivity, strategies can be implemented such as:
- Streamlining approval processes
- Establishing clear communication channels
- Cross-training team members to handle multiple tasks
Additionally, identifying and addressing the root causes of waiting, setting realistic timelines, and leveraging technology to automate certain tasks can help eliminate unnecessary waiting, ultimately leading to a more efficient and effective workflow.
Overproduction
Overproduction means making more than what is needed. It can lead to too much inventory, higher storage costs, and products becoming outdated. This can harm a company’s finances.
Overproduction can also divert attention from real areas that need improvement. It can reduce the resources available for making actual process enhancements.
To stop overproduction in a company that follows Kaizen, they can:
- Use a system that makes products based on what customers need.
- Make work processes standard to avoid extra output.
- Include middle and lower management in planning production to match supply and demand.
Other ways to prevent overproduction are:
- Setting limits on production.
- Checking inventory regularly.
- Shortening the time between making different parts.
Overprocessing
Overprocessing in a Kaizen event can waste time, resources, and effort, leading to lower productivity and higher costs. This is particularly true during a short-term brainstorming session for process improvements, as it can distract the team from achieving breakthroughs.
Identifying and reducing overprocessing during a Kaizen event involves closely monitoring the workflow, analyzing resource usage, and getting feedback from team members. Visual tools like value stream mapping and 5-S can help pinpoint overprocessing areas, which can then be minimized by streamlining processes and eliminating unnecessary steps.
To prevent overprocessing in future Kaizen events, it’s important to set clear objectives, empower team members to make decisions, and emphasize continuous process improvement. Regular reviews and feedback sessions can also help catch and address overprocessing early on.
Defects
Defects in a process or system can include data entry errors, machine malfunctions, customer complaints, rework, and production delays.
During a Kaizen event, defects can be identified and tracked through careful observation, data collection, and analysis. For instance, visual tools and techniques like value stream mapping and 5-S can be used to find the root causes of defects and track their frequency and impact.
To minimize defects in a Kaizen culture, strategies such as involving all team members in continuous improvement, using pull systems to prevent overproduction, and implementing standard operating procedures can be employed. Also, regular committee meetings where employees share their solutions and maintaining a focus on continuous improvement are important for reducing defects in the long term.
Skills Underutilization
Organizations can identify skills underutilization by evaluating their employees and roles regularly. This helps to pinpoint areas where employees may not fully utilize their skills. Gathering feedback from employees about their skill sets and where they could contribute more is also important.
To address skills underutilization, organizations can implement strategies like cross-training, job rotations, and project-based work. Cross-training helps employees gain additional skills and knowledge that can be applied to their current role or other areas of the organization. Job rotations allow employees to develop new skills and gain experience in different business areas. Project-based work assignments provide opportunities for applying skills in new and challenging ways, reducing underutilization in the workforce.
Fifteen Golden Rules for Effective Kaizen Events
The fifteen golden rules for effective Kaizen events are:
- Thorough preparation.
- Team selection.
- Documentation.
- Data-driven decisions.
- Clear objectives.
- Prioritization
These rules focus on continuous process improvement, open communication, clear roles and responsibilities, resource allocation, milestone tracking, and regular follow-up.
They can be applied to ensure successful implementation of Kaizen events by providing a structured approach, fostering teamwork and accountability, and emphasizing the importance of data and communication.
Best practices for integrating the Kaizen philosophy into the culture of an organization involve:
- Promoting employee involvement.
- Establishing a Kaizen committee.
- Implementing visual tools and techniques for problem-solving
Furthermore, organizations should encourage regular committee meetings, team engagement, and maintaining a focus on continuous improvement to ensure the successful integration of the Kaizen philosophy.
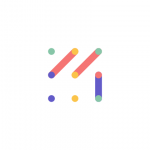
Vizologi is a revolutionary AI-generated business strategy tool that offers its users access to advanced features to create and refine start-up ideas quickly.
It generates limitless business ideas, gains insights on markets and competitors, and automates business plan creation.