Kaizen Benchmarking: Measure and Grow!
Do you want to improve your business processes and make continuous improvements? Then you should learn about Kaizen benchmarking! This powerful tool helps you measure your performance against the best in the industry and find areas for growth.
In this article, we’ll explore what Kaizen benchmarking is and how it works. We’ll also show you how to use it to take your business to the next level. If you’re ready to unlock your organization’s potential, keep reading to discover Kaizen benchmarking!
Fundamentals of Kaizen Methodology
Kaizen methodology focuses on continuous improvement and efficient problem-solving. It believes that small, consistent changes can lead to significant improvements in the workplace.
It encourages active employee involvement and emphasizes problem-solving abilities to reduce waste and streamline processes. The Kaizen improvement cycle involves planning, execution, analysis, and standardization.
Key principles include standardizing tasks, maintaining cleanliness, establishing order, and practicing discipline to create a more organized and productive work environment.
The 5S framework, a fundamental part of Kaizen, brings advantages like improved safety, workspace organization, and increased efficiency. It does, however, require dedicated maintenance efforts and regular monitoring to sustain its benefits.
Central Tenets of Kaizen Philosophy
The Kaizen philosophy encourages continuous improvement through principles like standardization, teamwork, and waste elimination.
Standardizing processes helps organizations find inefficiencies and keep working to improve them. Teamwork leads to collaborative problem-solving, bringing continuous improvements across different areas of work.
This philosophy focuses on “change for the better,” and believes small, incremental changes can lead to significant long-term improvements.
Kaizen emphasizes manageable and ongoing change for sustained improvements in processes and outcomes. It applies to work processes and all aspects of life, promoting small, incremental improvements in personal and professional growth, relationships, and overall well-being.
Understanding the Kaizen Approach to Enhancement
The Kaizen approach is about always getting better. It’s based on making small changes over time to achieve big improvements.
This philosophy emphasizes constant innovation and efficiency in an organization. It’s all about making small, gradual changes to foster a culture of continuous improvement and productivity.
The Kaizen improvement cycle involves:
- Identifying opportunities for improvement
- Making changes
- Measuring results
- Standardizing best practices
By using methods like Kaizen events, Gemba walks, and Quality Control Circles, organizations can address challenges and improve processes.
This approach taps into the collective knowledge, skills, and experience of employees to enhance productivity and efficiency.
The Kaizen Improvement Cycle Explained
The Kaizen Improvement Cycle has seven key components:
- Identifying an area for improvement.
- Analyzing the current state.
- Developing an optimal solution.
- Implementing the solution.
- Observing the impact of the change.
- Standardizing the process.
- Planning for the next improvement cycle
This approach ensures a continuous flow of improvements within the organization by focusing on small, incremental changes rather than large-scale overhauls.
The Kaizen Improvement Cycle contributes to continuous improvement in the workplace by creating a culture that encourages employees to seek out ways to optimize processes, eliminate waste, and boost productivity.
By using the PDCA (Plan-Do-Check-Act) cycle, employees are empowered to experiment with new ideas, learn from the outcomes, and refine their approaches over time. This iterative process allows for ongoing learning and development, leading to a more efficient and effective work environment.
Practical examples of the Kaizen Improvement Cycle in action can be found in manufacturing. Employees regularly suggest and implement small changes to production processes to enhance quality and reduce defect rates. In the service industry, the cycle can be seen in customer service practices, where continuous feedback is used to refine procedures and deliver better service to clients. Additionally, in healthcare, the Kaizen Improvement Cycle is used to streamline patient care processes and improve overall health outcomes.
Variations of Kaizen Events at the Workplace
Kaizen events are an important part of continuous improvement. They come in different forms, tailored to meet the specific needs and goals of different departments or teams. Common variations include value stream mapping, quality improvement, process optimization, and waste reduction initiatives.
These initiatives are used in various industries like manufacturing, healthcare, and service organizations. In manufacturing, teams may have daily production meetings to identify and eliminate waste. In healthcare, the focus could be on improving patient flow or reducing medication errors. And in the service industry, Kaizen methodologies could be used to streamline administrative processes, improve customer service, or enhance overall efficiency.
These examples show how versatile and effective Kaizen events can be in driving continuous improvement across different organizations.
Implementation of the Kaizen 5S Framework
Implementing the Kaizen 5S Framework in an organization involves several important steps and strategies.
Firstly, companies should ensure that employees understand the framework and its goals. This includes training them to recognize and eliminate waste, standardize work practices, and keep the workplace clean and organized.
Next, organizations need to assign a dedicated team to lead the implementation process. This team should create an action plan, set clear benchmarks, and continuously monitor progress.
Lastly, challenges may occur during the process, such as resistance to change or limited resources. These challenges can be addressed through effective communication, training, and leadership support.
Additionally, companies may need to adapt the framework to suit their specific needs. By successfully implementing the Kaizen 5S Framework, organizations can enhance efficiency, reduce waste, and establish a more organized and productive work environment.
Dissecting the Kaizen Model: Pros and Cons
The Upsides of Leveraging Kaizen
Kaizen offers businesses and organizations several benefits and advantages:
- Improved productivity
- Waste reduction
- Cost savings
- Enhanced quality
These help in continuous improvement and sustainable growth.
Kaizen encourages employees to take ownership of their work processes and think about how to improve them.
It also positively impacts employee engagement and fosters a culture of continuous improvement. This gives employees a sense of purpose and increases job satisfaction.
Additionally, Kaizen helps boost operational efficiency by identifying and eliminating inefficiencies and bottlenecks. This ensures smoother operations and a more streamlined workflow, contributing to overall operational excellence and long-term success.
The Downsides of Implementing Kaizen
Implementing Kaizen in a workplace may have challenges. It could cause employee burnout and fatigue due to increased work stress. This can lower morale, job satisfaction, productivity, and motivation. Also, it may create resistance to change among employees, impacting the organization’s culture and work environment. So, it’s important for organizations to assess and address these downsides for successful integration and sustainability.
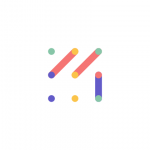
Vizologi is a revolutionary AI-generated business strategy tool that offers its users access to advanced features to create and refine start-up ideas quickly.
It generates limitless business ideas, gains insights on markets and competitors, and automates business plan creation.