Easy 5S Method for a Tidy Workspace
Do you spend too much time searching for tools and supplies in your workspace? A messy and disorganized area can make you feel frustrated and reduce your productivity.
The 5S method offers a simple and effective way to organize your workspace. It involves five easy steps that can help you create a more efficient and enjoyable work environment.
In this article, we’ll look at the 5S method and how it can help you achieve a tidy and organized workspace with minimal effort.
The Roots of 5S: A Brief History
The 5S methodology began in Japan. It uses five Japanese words: seiri (sort), seiton (set in order), seis? (shine), seiketsu (standardize), and shitsuke (sustain/self-discipline). These words explain how to organize a workplace for efficiency.
Over time, 5S principles were translated into English and added to manufacturing processes. It evolved from workplace organization to a full production management philosophy. The 5S system was important in improving manufacturing processes. It enhanced workflow, reduced waste, increased safety, and improved quality.
Now, 5S is used in industries beyond manufacturing, like healthcare and education. It’s a widely used method for workplace organization and visual control.
Demystifying the 5S Methodology
Explanation of the Japanese 5S Terms
The Japanese 5S terms are:
- Seiri
- Seiton (set in order)
- Seis?
- Seiketsu
- Shitsuke (sustain/self-discipline)
These terms outline the steps for organizing a workspace effectively. Understanding them is important as they form the foundation of the 5S methodology. Each term represents a crucial step in the organizational process, contributing to the overall efficiency and effectiveness of the workplace.
Without a clear understanding of these terms, the implementation of the 5S principles may be challenging. This could lead to potential inefficiencies and disorganization. The Japanese 5S terms provide a clear framework for organizing the workspace. For example, “seiri” (sort) guides employees in identifying necessary items, while “seiton” (set in order) establishes a system for arranging these items. Each term serves as a practical guideline for employees to follow, resulting in a well-organized, streamlined work environment that enhances productivity and safety.
The 5S Principles Translated into English
The 5S principles are a set of Japanese terms: seiri , seiton (set in order), seis? , seiketsu , and shitsuke (sustain/self-discipline). When translated into English, these terms describe the process of identifying and sorting items, maintaining the work area, and sustaining the new organizational system to ensure effectiveness and efficiency in the workplace.
In English, the 5S principles contribute to enhancing manufacturing processes by promoting organization, cleanliness, and visual management in the workplace.
For example, by sorting and organizing tools and equipment, employees can easily locate what they need. This reduces time wastage and promotes a safer work environment.
Sustaining improvements is a critical step in the 5S methodology when translated into English. It ensures that the changes made to the work area are maintained over time. This step involves instilling a culture of self-discipline and continuous improvement among employees. This is essential for the long-term success of the 5S principles.
Critical Role of 5S in Enhancing Manufacturing Processes
The 5S methodology improves manufacturing processes. It does this by organizing and cleaning the workplace in a systematic way. This approach consists of sorting, setting things in order, shining, standardizing, and sustaining. This improves efficiency, safety, and quality for manufacturers. When items and tools are organized and easily accessible, workers complete tasks faster. This reduces downtime and increases productivity.
Moreover, the methodology ensures clean, organized workspaces, reducing errors and accidents. Its real-world impact is seen in the automotive industry, streamlining assembly lines, and in the food and beverage industry, maintaining safety and quality.
Five Compelling Advantages of Implementing the 5S System
The 5S system has many advantages:
- It improves workplace safety by removing clutter and hazards, reducing the risk of accidents.
- It increases efficiency and productivity by organizing the workspace, making it easier for employees to find tools and materials.
- It enhances quality control by ensuring that tools are readily available and in good condition, reducing errors and defects.
- It boosts employee morale and engagement by creating a clean and organized work environment.
- It lays the groundwork for continuous improvement by establishing a disciplined and standardized approach to work.
The 5S system also enhances manufacturing processes by:
- Streamlining operations, reducing downtime, and minimizing waste.
- Eliminating unnecessary items and optimizing workflow to create a more efficient and reliable production environment.
- Leading to improved overall equipment effectiveness, higher production output, and lower manufacturing costs.
To ensure long-lasting benefits, it is crucial to sustain the improvements made through the 5S system. This can be achieved by:
- Establishing standard procedures, regular audits, and employee training.
- Maintaining improved workplace conditions and productivity levels.
- Preventing the workspace from reverting to its previous disorganized state.
- Upholding the gains made through 5S implementation.
Initial Step: Sort (Seiri)
Understanding ‘Sort’ in 5S
The ‘Sort’ step in the 5S methodology helps identify necessary and unnecessary items in a workspace. This creates a productive and efficient environment by removing obstacles and streamlining workflow.
In the healthcare industry, hospitals use the ‘Sort’ step to organize medical supplies and equipment, leading to quicker response times and more efficient patient care. In education, schools declutter classrooms and storage areas, creating a conducive learning environment for students and educators.
In manufacturing, the ‘Sort’ step improves safety, reduces downtime, and increases overall productivity by sorting through equipment and tools. This step ensures seamless workflow across industries and contributes to the successful implementation of the 5S methodology.
The Necessity of Sorting for Efficiency
Sorting is an important step in the 5S methodology. It helps workers find necessary items and get rid of unnecessary ones, making the workspace clean and organized.
By reducing clutter, it saves time spent searching for tools or materials. This leads to increased productivity and fewer errors. In manufacturing, sorting improves workflows, reduces downtime, and prevents accidents.
For instance, by clearly marking and sorting tools and materials, workers can easily find what they need, optimizing production and ensuring a safer work environment. Real-world applications in healthcare and education show the need for sorting for efficiency.
In healthcare, organizing medical supplies with the 5S methodology leads to quicker patient care and better inventory management. Similarly, in education, a well-organized classroom helps educators focus on teaching. This benefits students and teachers.
These examples demonstrate how sorting is important for creating efficient, productive, and safe work environments.
Executing the Sort Process
The sort process in the 5S methodology involves identifying and prioritizing necessary items in a workspace. Then, removing unnecessary items to create a more streamlined and efficient environment. This phase focuses on categorizing items based on frequency of use and necessity. It allows for easier access to essential tools and reduces clutter.
Executing the sort process optimizes the layout of a workspace, improves workflow, and enhances productivity. This contributes to overall efficiency by minimizing time spent searching for tools and materials and reducing the risk of workplace accidents.
Real-world examples of successful implementation of the sort process can be found in various industries. For instance, in healthcare facilities where the organization of medical supplies and equipment is critical, and in educational institutions where classroom materials and resources need to be easily accessible. In manufacturing, the sort process has been used to enhance inventory management and production line efficiency.
Sorting: Real-World Applications
The 5S methodology helps organize workspaces for efficiency and effectiveness. It’s used in manufacturing, healthcare, and education to streamline processes and reduce waste.
This approach involves identifying, sorting, maintaining, and sustaining the new organizational system. It ensures tools, materials, and information are easily accessible and stored in standardized locations. This reduces downtime and errors, ultimately improving productivity.
By creating well-organized and efficient work environments, the 5S methodology provides practical solutions across different industries.
Second Step: Set in Order (Seiton)
Grasping ‘Set in Order’ within 5S
The ‘Set in Order’ step of 5S is important. It ensures items are arranged logically. This leads to improved efficiency and less wasted time. Visual cues like floor markings, shelves, and labels help implement these guidelines in a workplace. They designate specific locations for tools and supplies.
Clear definitions for item storage help employees find what they need easily. This creates a more productive work environment. Various industries, like manufacturing, healthcare, and education, successfully implement ‘Set in Order’ within the 5S methodology.
For example, in manufacturing, color-coded floor tape and shadow boards guide employees on where to store tools. In healthcare, labeled storage areas ensure quick access and organization. Educational institutions use visual cues and designated areas for learning materials to create an organized learning environment.
Importance of an Ordered Setup
An ordered setup is important in the 5S methodology. It directly aligns with the “seiton” or “set in order” phase. This phase focuses on organizing a workspace, ensuring everything is in its proper place, and having a designated spot for all items, tools, and equipment.
The benefits of an ordered setup in the manufacturing process are significant. It helps reduce time spent searching for tools and materials, minimizes the risk of accidents or injuries caused by clutter, and improves overall workflow by eliminating obstacles and unnecessary movements.
A well-organized and ordered setup makes workplace processes more efficient and effective. Employees can easily locate and access the tools they need, leading to a smoother and more streamlined production process.
Additionally, an ordered setup contributes to maintaining a clean and visually controlled workspace, promoting a work environment that is conducive to productivity and safety.
Guidelines for Setting in Order
Setting in order in the 5S methodology involves:
- Identifying and sorting items in the workspace.
- Ensuring everything has its rightful place.
- Maintaining orderliness by labeling and categorizing items and creating a system for easy access.
This contributes to efficiency and organization by reducing time spent searching for tools or materials, minimizing workplace accidents, and improving productivity. For example, in a manufacturing facility, floor tape and labeled pathways can guide employees and visitors safely. In an office, well-organized spaces can improve workflow and save time. Successful implementation also includes maintaining and sustaining the organized system over time, through regular cleaning, organizing sessions, and involving all employees.
Examples of Setting in Order in Practice
Setting in order is very important for manufacturing processes. It helps make tools, materials, and equipment organized and easily accessible.
For example, clear labeling and designated storage areas for tools and supplies can help workers quickly find what they need, reducing downtime and increasing productivity. This practice also reduces the risk of errors and accidents by maintaining a safe and organized work environment.
In real-world examples, setting in order is seen in industries like healthcare and education. In hospitals, it involves organizing medical supplies and equipment to streamline patient care and reduce errors. In education, it can mean arranging classroom materials to support teaching and learning.
Setting in order is a key part of the 5S methodology, which emphasizes workplace organization and visual control. The 5S methodology aims to create an efficient and visually organized work environment by defining specific locations for tools and supplies and standardizing the way items are stored. This not only improves productivity but also contributes to the overall success of lean product and process development.
Third Step: Shine (Seiso)
The Essence of ‘Shine’ in 5S
The “Shine” in the 5S methodology is about keeping the workplace clean and organized. This helps make everything run smoothly. Implementing “Shine” means cleaning and inspecting the work environment to make sure all tools and equipment are in good condition. Regular cleaning helps spot issues early and prevents delays and safety problems.
For example, you can set cleaning schedules, inspect equipment, and use visual cues like floor markings. Keeping the workplace clean is essential for maintaining the gains from the 5S framework. It boosts productivity, safety, and creates a positive work environment. Regular cleaning becomes a standard practice that supports the overall goals of 5S, promoting continuous improvement and operational excellence.
Justification for Shining Your Workspace
Maintaining a clean and organized workspace is important in the 5S methodology.
A shining workspace ensures that the workplace is free of clutter, dirt, and potential hazards. This helps create a safer environment for all employees and prevents costly accidents.
It also promotes a positive work culture and increases efficiency and productivity. Employees can easily find tools and materials needed for their tasks, reducing time spent searching for items and resulting in smoother workflow processes.
Additionally, a clean and organized workspace creates a positive first impression for potential clients and visitors. It supports a visual workplace environment where everything has its place and is easily identifiable.
Strategies for Implementing Shine
One effective strategy for implementing the ‘Shine’ step of the 5S methodology is to establish routine cleaning and maintenance schedules.
This ensures that work areas are well-maintained and free of clutter.
To achieve this, specific cleaning tasks can be assigned to employees, and the workspace can be regularly inspected to identify any areas that require attention.
Organizations can integrate the ‘Shine’ principle into their daily operations by providing training and clear guidelines on cleanliness and orderliness.
They can also encourage employees to take ownership of their workspaces.
Practical examples of successful implementation of the ‘Shine’ concept include using color-coded cleaning tools, visual cues such as floor markings, and regular audits to monitor cleanliness and identify areas for improvement.
These strategies help to create an organized and efficient work environment, contributing to increased productivity and employee satisfaction.
Shine Illustrated with Examples
The “Shine” step in the 5S methodology is about keeping your workspace clean and organized. This helps to make work more efficient and safe.
In manufacturing, “Shine” means regularly cleaning and checking equipment to prevent breakdowns and ensure a safe environment. In healthcare, it involves thorough cleaning and disinfecting of medical equipment and patient rooms to reduce infections and promote wellness.
No matter the workplace, implementing “Shine” means setting cleaning schedules, using visual aids like floor markings, and training employees on cleanliness. Organizations can use tools like checklists and audits to monitor how well “Shine” is being done. This ensures a consistently clean and organized workspace.
Fourth Step: Standardize (Seiketsu)
Decoding ‘Standardize’ in the 5S Framework
Standardization is an important part of the 5S Framework. It focuses on creating a consistent and uniform work environment. This involves establishing and maintaining uniform procedures and practices throughout the workplace. It covers everything from the way tools are arranged to the way tasks are performed.
Standardization is crucial in the 5S methodology because it ensures that the improvements made in sorting, setting in order, and shining are maintained. Without standardization, there is a risk of reverting to the original disorganized state.
To achieve standardization in the 5S framework, organizations need to:
- Create clear and detailed guidelines for daily tasks
- Regularly monitor and audit the workplace
- Provide sufficient training to all employees
- Continuously reinforce the importance of following the established procedures
By doing this, organizations can sustain the gains made in the previous 5S steps, resulting in a more efficient and organized work environment.
The Critical Need for Standardization
Standardization is important in the 5S methodology. It ensures consistency and uniformity in workplace processes. This leads to efficient and effective task performance, boosting productivity and quality. Standardization also promotes safety by reducing errors and accidents from inconsistent work methods.
Within the 5S framework, standardized procedures create an organized workplace, minimizing waste and downtime. Employees can easily locate items, fostering a visually controlled environment. Clear expectations and guidelines benefit employees, ensuring understanding and compliance. This also supports continuous improvement efforts by providing a performance baseline.
For long-term sustainability, organizations can integrate training programs on 5S principles and standardized processes. Regular audits and reviews are important for compliance monitoring and adjustments. Leadership support and employee involvement are crucial for embedding standardized procedures into the organizational culture.
The Path to Standardizing Procedures
The 5S methodology has five key components:
- Sort.
- Set in order.
- Shine.
- Standardize.
- Sustain/self-discipline
These components involve organizing the workspace, maintaining the area, and establishing a new organizational system.
Standardizing procedures in the 5S framework contributes to the overall effectiveness and efficiency of manufacturing processes by ensuring that workflows are streamlined and consistent.
Challenges in implementing and sustaining standardized procedures in the 5S framework may include resistance to change, lack of clear guidelines, and inadequate training.
To address these challenges, organizations can:
- Implement comprehensive training programs
- Develop visual cues to reinforce standardization
- Involve employees in the process to foster a sense of ownership and accountability
Fifth Step: Sustain (Shitsuke)
Unpacking ‘Sustain’ in 5S Philosophy
The “Sustain” stage is important in keeping the newly organized workplace. After sorting, setting in order, shining, and standardizing the workspace, the “Sustain” phase focuses on long-term maintenance. This involves creating routines, conducting regular audits, and ensuring that the organized state is consistently upheld. Without the “Sustain” phase, the benefits achieved through the first four stages of 5S may be lost over time, leading to a return to the previous disorganized state.
By integrating “Sustain” into the 5S philosophy, organizations establish a culture of continuous improvement. This contributes to the long-term success and effectiveness of the 5S system by embedding self-discipline and ongoing improvement into the organization’s culture.
The Significance of Sustaining Improvements
Sustaining improvements is important in the 5S methodology. It ensures that the initial efforts to organize the workspace are continuously maintained. Without proper sustainment, the workplace may become disorganized again, negating the earlier improvements. To ensure ongoing commitment to sustaining improvements, companies can use visual management tools, regular audits, and employee training.
They can also establish a culture of self-discipline to encourage employees to take ownership of their workspaces.
For example, using floor tape and labels to designate storage areas can remind employees to return items to their designated locations. Other visual tools like shadow boards and color-coded labels can also help maintain 5S standards over time.
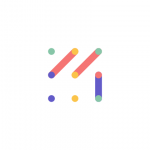
Vizologi is a revolutionary AI-generated business strategy tool that offers its users access to advanced features to create and refine start-up ideas quickly.
It generates limitless business ideas, gains insights on markets and competitors, and automates business plan creation.