Fun Lean Management Activities for Your Team
If you want to make lean management more engaging and enjoyable for your team, you’re in the right place! Fun activities like interactive games and team-building exercises can help your team understand lean management and improve collaboration. These activities make learning fun while promoting team bonding and creativity. Whether new to lean management or looking for fresh ideas, these activities can bring new energy and enthusiasm to your team.
Understanding Lean Management
Lean management is based on five essential principles for improving processes. These principles include identifying value, mapping workflow, creating a continuous workflow, using a pull system, and facilitating continuous improvement.
Value stream mapping techniques find and remove waste within processes, helping to create a more efficient workflow.
Having a continuous improvement mindset in Lean Management brings many benefits. It increases flexibility and responsiveness to consumer demands. It also makes companies more open to new ideas and experimentation, improving overall performance.
When these principles are implemented, organizations can significantly improve operational excellence and customer satisfaction.
Origins and Evolution of Lean Management
Lean management has a history rooted in the Toyota Production System. It started in the automotive industry and has expanded to healthcare, construction, and software development. It’s evolved from just waste reduction to focusing on continuous improvement and respect for people. The fundamental principles include identifying value, mapping the value chain, continuous workflows, creating a pull system, and promoting continuous improvement.
These principles have been adjusted to fit market demands and technological advancements, keeping lean management valuable to organizations in various industries.
Key Principles of Lean Management
Identifying Value in Processes
Businesses can find value in their processes by looking at each step. They can see which steps help the customer and which don’t. This lets them make operations better and cut down on waste. They focus only on things that help the customer.
One way to do this is using value stream mapping. This helps to see where processes can be improved by showing how materials and information move.
Another way is to use a pull system. Work is only done when needed, which helps to find and optimize processes. It also reduces extra stock and only makes what’s needed at the right time. This stops making too much and having too much stock, giving the customer more value.
These ways are essential for businesses that want to follow lean management. Lean management helps improve processes for efficiency and quality.
Value Stream Mapping Techniques
Value stream mapping is a technique for helping organizations identify and eliminate waste in processes. It involves analyzing the process flow, identifying redundancies, and eliminating non-value-adding steps. This helps businesses enhance their operational efficiency.
The technique includes creating a continuous workflow by implementing pull systems and continuous improvement. It also helps companies identify where customers add value by ensuring that products or services are developed most efficiently.
Establishing a Continuous Workflow
Establishing a continuous workflow in lean management activities involves making processes efficient and minimizing waste. Here are the key steps:
- Identify value.
- Map the value chain.
- Create a continuous workflow with a pull system for steady production.
Integrating continuous improvement optimizes workflow efficiency and productivity. Learning and experimentation solutions help companies be flexible and responsive to consumer demands, improving overall performance.
Implementing a Pull System
When a company wants to switch from a push system to a pull system, it needs to:
- Restructure its production or service delivery processes to match customer demand and real-time sales data.
- Eliminate overproduction and create flexible systems to respond to changing demands quickly.
Implementing a pull system involves:
- Rearranging the workflow.
- Setting up visual indicators for production.
- Using a Kanban system to control inventory levels.
The company must also consider workload balancing, equipment maintenance, and workforce training for a smooth transition.
To sustain and improve the pull system, the company should:
- Regularly collect and review performance data.
- Involve employees in problem-solving.
- Foster a culture of continuous improvement and innovation.
Regular management reviews and audits can help analyze the system’s effectiveness and identify improvement opportunities.
Embracing Continuous Improvement
Continuous improvement in an organization involves creating a culture that encourages innovation and evolution. Providing employees with tools and resources to identify areas for improvement and experiment with new ideas is key. This can be achieved through regular training, workshops, and open communication channels. Implementing a system to track and measure the success of these efforts is crucial. It can be done through key performance indicators (KPIs) and regular performance reviews.
Interactive Lean Management Training Activities
Interactive lean management training activities help people understand and apply lean management principles.
These activities include hands-on simulations and group exercises. They show how reducing waste, optimizing processes, and continuous improvement work in real life.
For example, participants can participate in virtual factory simulations, value stream mapping workshops, and Kaizen events. These activities help them understand key lean concepts and tools, such as identifying value, mapping workflow, and implementing pull systems.
Real-world examples in industries like healthcare, manufacturing, and service are also important. They demonstrate the benefits of lean principles. Case studies and success stories show increased efficiency, cost reduction, and improved quality from lean practices. This reinforces the relevance and usefulness of lean management in different organizations.
Lean Management Tools Exploration
Lean management tools, such as value stream mapping, Kanban boards, and 5S, help improve processes in various industries. These tools offer adaptable strategies for different company challenges. They help identify and eliminate inefficiencies, reduce waste, and optimize workflow, improving productivity, quality, and customer satisfaction. Benefits include increased transparency, streamlined processes, and cost savings.
These tools foster a culture of improvement, employee empowerment, and innovation, leading to sustainable market growth and competitiveness.
Real-world Examples of Lean Management
Lean management principles have helped real-world companies become more efficient and reduce waste. They achieve this by streamlining processes, removing unnecessary steps, and establishing clear work procedures.
For instance, a manufacturing company improved lead times and decreased inventory levels by rearranging its production floor layout. Another company enhanced communication and collaboration among employees by implementing visual management techniques.
These examples show that integrating lean management into day-to-day operations leads to lower costs, higher productivity, and improved customer satisfaction. Specifically, companies have observed fewer defects, shorter production cycle times, and improved on-time deliveries.
By continuously addressing inefficiencies, businesses optimize their operations and overall performance.
Benefiting from Lean Management
Lean Management principles and practices have a big impact on companies. They improve performance by making processes more efficient and eliminating tasks that don’t add value. Many organizations have seen better results after using Lean Management. For instance, they have streamlined operations, cut lead times, and increased output.
Also, Lean Management helps reduce costs and minimize waste by eliminating unnecessary processes and inventory, better-using resources, and improving product quality. These changes make customers happier and boost the company’s competitiveness.
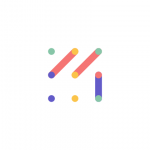
Vizologi is a revolutionary AI-generated business strategy tool that offers its users access to advanced features to create and refine start-up ideas quickly.
It generates limitless business ideas, gains insights on markets and competitors, and automates business plan creation.