Your Guide to Lean Management Tools
Welcome to your guide to lean management tools!
If you want to streamline your processes, increase efficiency, and eliminate waste in your organization, then you’re in the right place.
In this article, we’ll explore the most effective lean management tools you can implement today.
These tools include:
- Value stream mapping
- Kanban boards
These tools are designed to help you identify and eliminate non-value-added activities, ultimately improving productivity and higher-quality output.
Whether you’re new to lean management or looking to enhance your current practices, this guide covers you.
Core Principles of Lean Management
Determining Value from the Customer’s Perspective
Customers consider several factors when deciding whether a product or service is good: quality, price, reliability, and overall happiness. Companies can ask customers directly, use surveys, or interact with them on social media to understand what customers think.
Companies can use Lean management tools like Value Stream Mapping, Key Performance Indicators (KPIs), and Continuous Flow to ensure that their value matches customers’ expectations. These tools help find areas for improvement, measure progress, and ensure that everything runs smoothly for the customer.
Also, things like ensuring there are no mistakes and tracking productivity can improve the quality and consistency of the value for the customer.
Mapping the Value Stream to Identify Waste
Value stream mapping is a Lean management tool. It visually represents the materials and information needed to deliver a product or service to customers. Organizations can find waste and inefficiencies in their processes by analyzing the entire value stream.
This mapping helps identify non-value-added steps, wait times, excess inventory, overproduction, and other forms of waste. Excess inventory leads to carrying costs, storage space issues, and potential obsolescence.
Organizations can also find bottlenecks, delays, and defects by mapping the value stream. This allows them to prioritize improvements that will impact efficiency and quality most.
Establishing Continuous Workflow
Lean management uses 5S, Kaizen, Kanban, and Total Productive Maintenance (TPM) to organize the workplace, streamline processes, and maintain equipment. Value Stream Mapping (VSM) and Bottleneck Analysis help identify and eliminate waste, while Just-In-Time (JIT) and Plan-Do-Check-Act (PDCA) methods aid efficient production and process improvement.
These principles help eliminate waste and improve work processes. Tools like Heijunka, Andon, and Poka Yoke help level production, signal abnormalities, and prevent mistakes, ensuring a smooth workflow. Key Performance Indicators and Overall Equipment Effectiveness (OEE) help measure and manage performance to optimize work processes continuously.
Continuous improvement is crucial for maintaining a constant workflow. Organizations can constantly identify and address inefficiencies and defects using tools like Gemba, SMART Goals, and Root Cause Analysis, leading to ongoing enhancements and sustained continuous workflow.
Implementing a Pull System
Implementing a Pull System in a business or organization needs careful planning and execution.
First, identify value and map the value stream to understand the flow of activities. Create a continuous workflow and establish a pull system for a smooth and efficient process. Once implemented, maintain and optimize the Pull System with continuous improvement and adaptation based on customer demand. Monitor key performance indicators and apply lean tools like Andon, Heijunka, and Kaizen to address issues and ensure effectiveness. Focus on waste reduction and product quality to enhance production efficiency and customer satisfaction. Utilize Lean tools such as Kanban and Total Productive Maintenance to support maintenance and optimization, ensuring a streamlined and efficient production process.
Pursuing Perfection Through Continuous Improvement
Organizations can pursue perfection in their processes by embracing Lean management tools. These tools include Kaizen, Jidoka, Poka Yoke, Kanban, Continuous Flow, and Key Performance Indicators. They help reduce waste, increase efficiency, maintain product quality, and ensure customer satisfaction.
Practices such as mistake-proofing, level scheduling, visual management, and productivity measurement can continuously improve processes, creating a streamlined and efficient production process. Effectively utilizing tools like 5S, Andon, Bottleneck Analysis, and Plan-Do-Check-Act sustains this culture of continuous improvement in the workplace.
Lean tools and methodologies not only align with the core principles of lean management but also drive process improvement, eliminate waste, and achieve continuous improvement in organizations. Embracing these tools is essential in the pursuit of perfection through continuous improvement.
Top Lean Management Tools & Techniques
Implementing the 5S Methodology for Workplace Organization
The 5S methodology is a systematic approach to improving workplace organization and efficiency. It involves sorting, setting in order, shining, standardizing, and sustaining.
This means removing unnecessary items, organizing the remaining ones logically, cleaning the workspace, establishing standard procedures, and ensuring sustained organization.
Successful implementation requires clear communication, employee involvement, regular training, and continuous monitoring and improvement.
Potential benefits include increased productivity, improved safety, enhanced quality, and a more organized work environment. However, challenges may arise in resistance to change, maintaining consistency, and sustaining efforts.
The Andon System for Real-Time Alerts
The Andon System for Real-Time Alerts in Lean management provides immediate notification of any production issues or abnormalities on the production line. It helps identify and address issues in real-time by alerting the necessary personnel, such as supervisors or maintenance staff, to the specific location and nature of the problem. This allows for quick resolution and prevents the issue from affecting the workflow.
Implementing The AndonSystem for Real-Time Alerts in a workflow can improve production efficiency, reduce downtime, and increase quality control. It also promotes a culture of continuous improvement and empowers employees to take ownership of the production process by encouraging them to participate in problem-solving actively.
Using Bottleneck Analysis to Identify Process Delays
Bottleneck analysis helps organizations in Lean management. It finds process delays in value streams by examining workflow. This pinpoints specific steps or workstations causing delays. Then, organizations can focus on improving these areas and allocate resources efficiently. The next step is implementing continuous improvement practices. This may involve reorganizing work processes or adjusting production schedules.
Through lean management practices, organizations can achieve better productivity and deliver greater value to customers by driving continuous improvement.
Continuous Flow to Reduce Waiting Time
One important Lean management tool for reducing waiting time is continuous flow. This means organizing workstations to minimize movement and material transportation. It helps reduce idle time and waiting between production stages.
Strategies can be used to maintain continuous workflow and minimize delays, such as standardizing work processes, implementing just-in-time systems, and using Kanban for visual inventory management.
Identifying and addressing bottlenecks in the process is also crucial. This includes conducting bottleneck analysis to pinpoint areas of congestion, implementing Andon systems for real-time issue recognition, and using Overall Equipment Effectiveness as a key performance indicator to track equipment downtime and speed loss.
Continuous flow enhances productivity by minimizing waiting times and streamlining transitions between production stages. Leveraging tools to track equipment downtime helps identify inefficiencies, schedule maintenance proactively, and prevent delays, ensuring a smoother and more efficient workflow.
When applied effectively, these measures contribute to a more efficient production process.
Employing Gemba Walks for Direct Observation
Gemba walks are a valuable tool for direct observation in the workplace. Managers and leaders physically go to where work is being done to understand processes, identify inefficiencies, and engage with employees at the front lines.
The benefits of employing Gemba walks to observe processes and identify opportunities for improvement are numerous. By being present in the work environment, leaders can witness firsthand how tasks are performed, spot areas for improvement, and engage with employees to gather insights and feedback.
Gemba walks contribute to continuous improvement and problem-solving efforts within an organization by fostering a culture of open communication, problem-solving, and continuous learning. This direct observation allows for immediate feedback, identifying root causes of issues, and implementing sustainable solutions.
Gemba walks also demonstrate leadership’s commitment to process improvement and the development of a collaborative and empowered workforce.
Heijunka: Achieving Level Scheduling
Heijunka helps achieve level scheduling in Lean management by smoothing out the production process and ensuring a consistent workflow. This is done by allocating production over a specified period based on customer demand, which helps avoid sudden spikes and drops in production levels.
The key principles of Heijunka that support level scheduling include maintaining a consistent workload, balancing production sequences, and synchronizing processes to match demand. Implementing Heijunka can reduce waste as it allows for a more efficient use of resources, minimizes overproduction, and prevents excess inventory.
Hoshin Kanri for Strategic Policy Deployment
Hoshin Kanri is a strategic tool used in Lean management to drive organizational policy deployment. It aims to align an organization’s objectives and resources to ensure effective strategy execution.
For example, Hoshin Kanri helps set clear, measurable goals and establish a continuous improvement cycle. This tool ensures that every level of the company is working towards the same strategic objectives, thus helping to align priorities and allocate resources effectively.
Jidoka: Enhancing Autonomation
Jidoka is a concept in Lean Management that aims to combine automation with human involvement to enhance autonomation. When a problem is found, the process stops automatically. This prevents defective products from continuing down the line, making the production process more efficient. It also minimizes the risk of producing defective items and reduces waste.
Jidoka can improve workflow and reduce waste in manufacturing or production. It allows workers to spot and fix issues quickly, leading to smoother operations and higher product quality. Implementing Jidoka in Lean Management can improve product quality, increase efficiency, reduce waste, and create a safer work environment.
Adopting Just-In-Time (JIT) to Reduce Inventory
Adopting just-in-time can help reduce inventory levels. It enables organizations to produce and deliver products only as needed. This eliminates the need for excess inventory storage and helps minimize waste while reducing carrying costs.
The key steps in implementing Just-In-Time (JIT) for inventory reduction include:
- Establishing reliable and efficient supply chain management
- Implementing efficient production processes
- Establishing strong relationships with suppliers for timely material delivery
Organizations must also focus on quality control and continuous improvement to meet customer demand without excess inventory. However, transitioning to a Just-In-Time (JIT) system may pose challenges such as accurate demand forecasting, external supplier reliance, and supply chain disruptions. It also requires a cultural shift within the organization to prioritize efficiency, flexibility, and responsiveness to customer demand.
Facilitating Improvement with Lean Strategies
Kaizen for Encouraging Continuous Improvement
Kaizen is a fundamental tool in Lean management. It encourages continuous organizational improvement by promoting a culture of minor, ongoing enhancements. Employees at all levels are empowered to identify and address inefficiencies in their work processes. By embracing Kaizen, organizations instill a continuous improvement mindset, implementing manageable changes regularly. This approach drives overall progress and efficiency.
Kaizen also fosters open communication and collaboration, driving a culture of continuous improvement and innovation. Employees are encouraged to contribute their ideas to enhance workflows and processes. By systematically applying Kaizen principles, organizations can promote ongoing improvement and efficiency, resulting in streamlined operations and increased productivity. Recognizing and celebrating minor improvements ensures a more agile and adaptable work environment.
Kanban: The Pull System to Control Inventory
Kanban is used to control inventory in lean management. It ensures inventory is replenished only when necessary, based on customer demand. This helps prevent overproduction, reduce excess inventory, and minimize waste. Kanban also helps establish continuous workflow and reduce waste by visualizing workflow and materials. It enables smooth production and identifies bottlenecks or inefficiencies.
The benefits of using Kanban in lean manufacturing include improved production efficiency, reduced lead times, better coordination between production stages, and enhanced quality control. Kanban also allows for just-in-time inventory management, helping companies quickly respond to changes in customer demand and market conditions, leading to cost savings and improved customer satisfaction.
The Role of KPIs in Performance Measurement
Key Performance Indicators are essential for measuring performance in lean management. They track specific metrics like production lead times, on-time delivery, and defect rates. This data is essential for evaluating the efficiency and effectiveness of lean processes. KPIs help identify areas for improvement and measure progress toward lean management goals.
For example, monitoring KPIs related to inventory turnover or equipment downtime can pinpoint bottlenecks and areas of waste, enabling targeted improvement efforts. KPIs also help evaluate the effectiveness of lean management strategies by providing measurable outcomes. Tracking KPIs related to customer satisfaction or production output can gauge the impact of lean initiatives.
OEE for Equipment Effectiveness Analysis
Overall, Equipment Effectiveness is a helpful tool in Lean management. It measures and analyzes equipment effectiveness in manufacturing. OEE considers three components: availability, performance, and quality. This gives a full view of equipment productivity.
OEE analysis tracks metrics like downtime, speed loss, and defective products. This helps identify inefficiencies in equipment utilization. The results can be used to address issues and improve productivity and quality. For instance, if OEE analysis shows frequent downtime for a machine, a root cause analysis can be done to minimize future disruptions.
Similarly, OEE analysis can help identify and fix performance and quality issues, improving equipment utilization and process efficiency.
Incorporating PDCA (Plan, Do, Check, Act) into Lean Cycles
Incorporating PDCA into Lean Cycles is essential for continuous improvement in Lean management. By following this cycle, organizations can plan improvement initiatives, make changes, check the outcomes, and take action to enhance their processes.
For example, a company using Lean principles can use PDCA to find areas of waste, make changes, check the impact, and adjust processes for ongoing improvement. This requires clear communication, employee involvement, data-driven decision-making, and a learning culture, all fundamental to Lean management. By using PDCA within Lean cycles, organizations can continuously find improvement opportunities, address them effectively, and enhance operational performance.
Applying Poka-Yoke for Mistake-Proofing
Poka-Yoke can help prevent mistakes in production by creating fail-safe mechanisms to eliminate errors before they happen.
The process involves designing systems that make it impossible for mistakes to occur, ensuring that quality is built into production from the start.
To implement Poka-Yoke, you need to identify potential errors, analyze their root causes, and then implement simple, practical solutions to prevent them. This can include automatic sensors, warning devices, and physical barriers to minimize potential errors.
By integrating these error-proofing mechanisms into the production line, Poka-Yoke ensures manufactured products’ highest quality and reliability.
Identifying Primary Causes with Root Cause Analysis
Root cause analysis is an integral part of identifying the leading causes of issues in lean management. It involves thoroughly investigating the underlying factors contributing to waste and inefficiency in a value stream. Techniques like the “5 Whys” or fishbone diagrams can help uncover the root causes of problems, allowing organizations to implement targeted solutions. Creating a culture of continuous improvement is key to practical root cause analysis.
This encourages employees to identify and address issues at their core. With this approach, organizations can make sustainable process improvements and work towards a more efficient production process.
Optimization Techniques in Lean Management
SMED for Quick Changeovers
SMED, or Single-Minute Exchange of Die, helps reduce changeover times in production processes. It focuses on identifying and separating internal and external setup activities, converting internal to external setup tasks, and streamlining the remaining steps.
This tool optimizes changeover times by standardizing work procedures, eliminating unnecessary adjustments, and using parallel activities when possible.
Implementing SMED involves analyzing the current changeover process, categorizing setup activities, identifying improvement opportunities, making changes to streamline the process, and continuously monitoring and refining the new setup procedures.
By applying SMED principles, organizations can significantly reduce changeover times, minimize production downtime, and improve operational efficiency.
Addressing the Six Big Losses in Manufacturing
Lean management principles are essential for addressing the six significant losses in manufacturing. By focusing on value, streamlining workflow, establishing a pull system, and promoting continuous improvement, organizations can effectively tackle issues related to downtime, inefficiencies, and defects.
Implementing top lean management tools and techniques such as 5S, Kaizen, Value Stream Mapping, Andon, and Total Productive Maintenance can minimize the six significant losses by ensuring workplace organization, continuous improvement, visual management, and efficient equipment maintenance.
Lean strategies and optimization techniques are essential in facilitating improvement and addressing the six big losses in manufacturing by promoting waste reduction, productivity measurement, mistake-proofing, and level scheduling.
Through the systematic application of these tools and strategies, organizations can strive towards a more efficient and effective production process, which will ultimately lead to improved quality, reduced costs, and increased customer satisfaction.
Setting SMART Goals for Clear Objectives
Setting clear goals in lean management is essential for driving improvement. One way to do this is using SMART criteria, which stands for Specific, Measurable, Achievable, Relevant, and Time-bound. These criteria help align lean management principles with effective goal-setting. For instance, an organization looking to reduce waste and enhance efficiency can set a SMART goal of implementing 5S in a specific production area.
This goal can include a measurable target to reduce waste by a certain percentage within a set timeframe. By using Key Performance Indicators, such as overall equipment effectiveness or cycle time, progress toward lean management goals can be tracked, providing measurable evidence of improvement.
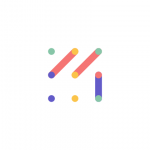
Vizologi is a revolutionary AI-generated business strategy tool that offers its users access to advanced features to create and refine start-up ideas quickly.
It generates limitless business ideas, gains insights on markets and competitors, and automates business plan creation.