Get Smart with 5S Awareness!
Do you struggle to find things in your workspace? Waste time looking for tools or supplies? It may be time to consider implementing the 5S method. 5S is a simple way to organize and maintain a clean, efficient, and safe work environment.
In this article, we will explore the 5S principles and how they can help you streamline your work processes. Let’s find out how it can make a difference in your daily work life.
Embrace Efficiency with 5S: Your Comprehensive Guide
Assessing Your Current Business Efficiency
Business processes should be organized and streamlined for efficient production and minimal waste. Performance can be measured using indicators like production output, revenue, and customer satisfaction. Identifying and addressing bottlenecks and inefficiencies in areas like inventory management, production cycles, and supply chain operations is important. Implementing 5S principles helps streamline and organize processes, making workspaces safer and more productive.
Unveiling the 5S Framework: A Detailed Overview
Definition and Origin of 5S
5S is a workplace organization method that originated in Japan. It’s derived from five Japanese words, all beginning with “S.” It has been integrated into Toyota’s manufacturing framework and has since become part of operational and process excellence across various industries.
The 5S methodology consists of five key principles:
- Sort.
- Set in Order.
- Shine.
- Standardize.
- Sustain
These principles focus on efficiency, waste reduction, and workplace safety.
Common misconceptions about 5S include its comparison to traditional organizational methods. However, 5S emphasizes ongoing housekeeping to maintain organization and order, and it’s not a one-time effort. Additionally, 5S goes beyond physical organization to encompass standardization and sustained efforts, making it different from traditional methods.
Developing a 5S Action Plan for Your Business
Establishing Standards: The Fourth Pillar
Establishing standards in the 5S framework is important for keeping a structured and efficient workplace. This step helps businesses set guidelines for organizing and sustaining improvements. By defining clear protocols and expectations, companies can ensure consistency and reliability in their processes. Implementing and maintaining these standards involves providing training to employees, peer audits, and defining schedules for assessing improvements.
Key considerations for businesses includedefining roles, organizing cleaning schedules, and developing written procedures. Prioritizing standardization and sustainability can enhance productivity, reduce waste, and create a safer work environment.
Maintaining Improvements: The Fifth Pillar of 5S
The strategies and techniques for maintaining improvements in the 5S framework involve creating a culture of continuous improvement. This includes:
- Establishing regular audits to monitor adherence to 5S principles.
- Defining clear roles and responsibilities.
- Developing written procedures to support long-term sustainability.
Organizations can ensure that maintaining improvements becomes an integral part of their daily operations by:
- Conducting regular peer reviews.
- Verifying that defined schedules are being met.
- Ensuring that everyone follows the established procedures.
Common challenges and obstacles that companies face when trying to sustain improvements after implementing the 5S methodology include resistance to change, lack of employee buy-in, and inconsistent management support.
However, by providing comprehensive training and ongoing support, companies can overcome these challenges and successfully embed the 5S principles into their organizational culture.
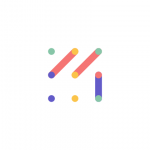
Vizologi is a revolutionary AI-generated business strategy tool that offers its users access to advanced features to create and refine start-up ideas quickly.
It generates limitless business ideas, gains insights on markets and competitors, and automates business plan creation.