Getting Your Product Testing Approved Easily
Are you a product developer seeking easier testing approval? Look no further! We’ll explore strategies and tips to streamline the process. Understanding the key steps and requirements will help you navigate confidently and efficiently.
Let’s dive in and make the product testing approval process a breeze!
Discover the Safety Standards for Your Item
Safety standards for your item include meeting fire, shock, radiation, and mechanical hazards requirements. There should not be any other safety risks to the user.
Testing requirements are important to ensure consumer safety. It’s crucial to update product certificates regularly to stay compliant with the latest standards and regulations. This helps minimize potential risks for the end user and the organization.
While supplier tests can be valuable, relying solely on them for safety standards is not advisable. A rigorous testing program performed by an accredited safety testing laboratory can help mitigate potential risks and ensure that products consistently meet safety standards.
Figuring Out What Safety Tests You Need
Identifying safety standards for specific items is crucial for compliance and consumer safety. Thorough research and understanding of federal consumer product safety rules are necessary. The product’s safety tests are determined by evaluating it to recognized standards and seeking expert guidance from accredited safety testing laboratories.
Each product batch’s certification should be updated when safety standards change, design modifications are made, or other factors impact safety and compliance. This helps ensure the product meets all required safety standards, minimizing user and organization risks.
Other Tasks You’ve Got to Do
Material change means a major adjustment in a product’s design, construction, or parts. When this happens, manufacturers and importers have to retest the product to ensure it still meets consumer safety rules.
It’s essential to regularly check and review a product’s safety, as standards can change over time. Also, if any part of the product is altered or replaced with a different component, thorough retesting is needed to confirm it’s safe for consumers.
Testing products regularly and ensuring they meet safety standards is crucial to keeping consumers safe.
What ‘Certifying’ Means for Common Items
Safety standards are essential to prevent everyday items from posing risks like fire, shock, radiation, or mechanical hazards. Products undergo rigorous testing to comply with these standards and obtain regulatory marks like CE or NRTL. Manufacturers and importers must ensure their products meet these standards to minimize risks to users and the organization. Certification papers should be updated regularly to ensure ongoing safety compliance.
While relying on supplier tests may work sometimes, rechecking products for certification is necessary, especially after modifications or regulation changes.
What Goes into the Certification
- A product needs safety testing to get certified. This ensures it meets government safety standards. Tests check for fire, shock, radiation, and mechanical hazards. After passing an evaluation, a product gets marks like CE or NRTL.
- Certification documents should be updated for each product batch. This is important to keep meeting safety standards. Every unit needs to meet safety criteria and be hazard-free.
- A product must be rechecked for certification after material changes or supplier tests. This includes changes in composition, design, or suppliers. These changes might affect safety and need retesting.
Setting Up Your Product’s Certification Papers
Product safety standards must be identified to determine the required certification papers. Different products have different requirements, and the appropriate certification documents must be obtained to show compliance with the regulations. Certification papers are necessary for each product batch and must be updated according to specific timelines outlined in consumer product safety rules.
If the product undergoes material changes or relies on supplier tests, it must be rechecked and recertified to ensure ongoing compliance. Relying on supplier tests and material changes can impact product safety, and rechecking and recertifying products in these situations affirms their uncompromised safety. These checks and certifications help maintain consumer safety standards and prevent potential risks associated with product use.
Digital vs. Paper: Which Certificate Works?
Do Certificates Need Updates for Every Batch?
Updating certificates for every new batch of products is essential to ensure its safety and compliance. Failing to do so can have serious consequences. It can increase risks for both users and the organization. The product may not meet safety standards, leading to fire, shock, radiation, or mechanical hazards. Therefore, updating certificates for every batch is critical.
It helps maintain safety and compliance by ensuring the product meets recognized standards. Regular testing by an accredited safety testing laboratory can help reduce these risks and ensure the end user’s safety. Manufacturers and importers must prioritize the regular updating of certificates for every new batch of product to guarantee ongoing safety and compliance.
Making Sure Certificates Follow Your Product
To ensure that the product’s certificates are always up to date, a company needs to establish a process to check and update the certificates as needed regularly. This involves identifying relevant federal consumer product safety rules and the necessary testing to confirm compliance. The product’s certification should also be periodically reviewed if there are material changes or supplier tests to ensure continued safety standards compliance.
Failing to keep certificates current could lead to penalties for non-compliance and increased risk for both users and the organization. Therefore, it’s crucial to have a thorough and standardized testing program conducted by a certified safety testing laboratory to reduce potential safety risks and maintain the product’s safety compliance.
How Often You Have to Check and Promise Your Product is Okay
Manufacturers and importers should regularly check and guarantee the safety of their products. This means making sure they meet the right safety standards. They should test and certify their products at specific times and for specific risks, such as fire, shock, radiation, and other safety risks.
After their products pass the right tests, they should receive regulatory marks, such as the CE mark or NRTL mark.
Regular and careful testing by certified safety testing labs can help reduce safety risks for the user and the company.
To maintain a high level of product quality over time, they should follow a good testing plan, use electronic certificates for each product, and give the right General Certificate of Conformity to follow safety rules for products.
What ‘Material Change’ Means and When to Recheck Your Product
Determining a ‘material change’ in a product is important. It can affect the product’s safety compliance. A material change can involve construction, components, or manufacturing alterations. Changes in the intended use, design, or performance can also be considered a material change. Manufacturers may need to reevaluate and retest their products to ensure they meet safety standards.
Several circumstances may require rechecking a product for safety after a material change. These include adjustments to the production process, changes in suppliers or materials, and modifications to the product’s design or purpose. If a new hazard is introduced or existing hazards are worsened due to the material change, retesting the product is necessary to confirm its safety compliance.
Organizations can determine if a material change has occurred by thoroughly assessing the product’s specifications, intended use, and risk factors. Reviewing technical documentation and industry standards and seeking expert advice can provide valuable insights into the impact of any changes. Depending on the nature and extent of the modifications, retesting the product with accredited safety testing laboratories may be needed to confirm its compliance with safety standards.
Relying on Supplier Tests: Is It Okay?
If You Change Part of the Product, Does It Need New Tests?
If a product undergoes a “material change,” like a different design, materials, or processing, it usually needs retesting for safety standards.
Deciding if new testing is needed is based on common sense and experience. Companies must consider if the changes impact safety or compliance.
This decision often follows industry standards and regulations, such as the General Certificate of Conformity (GCC) and the Consumer Product Safety Improvement Act (CPSIA).
These rules outline the process for identifying federal safety rules and the necessary testing after modifying a product.
Even though these regulations offer general guidance, organizations may need to refer to specific standards and involve experts for this determination.
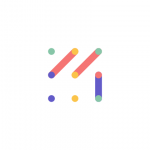
Vizologi is a revolutionary AI-generated business strategy tool that offers its users access to advanced features to create and refine start-up ideas quickly.
It generates limitless business ideas, gains insights on markets and competitors, and automates business plan creation.