Growing Your 5S Business the Smart Way
Growing your 5S business can be smart and simple. Whether you’re starting or expanding, there are proven strategies to help. We’ll explore practical tips to streamline processes and maximize efficiency. Let’s discover how to take your 5S business to the next level.
Understanding the 5S Framework
The Origins of the 5S Methodology
The 5S methodology was developed by Toyota in the 1960s. It aims to enhance workplace productivity and organization. Over time, it has expanded to sectors like healthcare, education, and business management. Factors contributing to its development include the increasing emphasis on quality management, waste reduction, and continuous improvement.
Cultural and organizational factors such as the “Kaizen” philosophy in Japanese culture, the need for efficiency and productivity in businesses, and the desire for quality improvement have greatly influenced the origins and implementation of the 5S methodology. By standardizing workplace organization, reducing waste, and encouraging a culture of continuous improvement, the 5S methodology has become a fundamental tool for enhancing productivity and efficiency in numerous industries, contributing to long-term success and sustainability.
Definition and Purpose of 5S
The 5S methodology is a system to improve workplace organization and efficiency. It has five principles: Sort, Set in Order, Shine, Standardize, and Sustain.
The purpose of 5S is to reduce waste and downtime, create a stable platform for further improvement, and instill a culture of quality and productivity.
Implementing 5S reduces clutter and unnecessary items, making it easier for employees to find what they need. This leads to improvements in productivity, safety, and employee satisfaction.
5S can be applied across different industries like manufacturing, healthcare, and office environments. It can be adapted to suit the specific needs of any industry or process.
The Cornerstones of 5S: Seiri, Seiton, Seisou, Seiketsu, and Shitsuke
Seiri (Sort)
Sorting is an important part of the 5S methodology. It helps make the work environment more organized and efficient.
By getting rid of things that are not needed, employees can find the tools and materials they need more easily. This makes their work easier and faster.
Sorting things out also helps get rid of old or unused items. This makes room for things that are actually needed, making work more productive.
To sort things effectively, items can be grouped based on how often they are used. Duplicates can be thrown out, and everything should be clearly labeled.
For example, in a manufacturing company, tools can be sorted by how often they are used. This makes it easier to find the tools needed near the work areas.
In a warehouse, inventory can be sorted by expiration dates. This makes sure that the oldest products are used first, reducing waste.
These examples show how sorting can make a big difference in how well a workplace runs. It leads to more productivity and less time wasted.
The Significance of Sorting in Organizational Efficiency
Implementing the 5S methodology can bring important benefits to businesses. It helps reduce waste, minimize downtime, and creates a more stable platform for improvement activities. This method not only organizes the work environment but also encourages continuous improvement and instills a culture of quality and productivity.
Sorting contributes to streamlining operations and improving productivity within an organization by eliminating unnecessary items, reducing clutter, and creating a more efficient workspace for employees. Successful implementation of sorting methods can be seen in various types of businesses, such as manufacturing, healthcare, and retail.
For example, in manufacturing, implementing the 5S system has led to reduced downtime, increased safety, and higher quality products. In healthcare, sorting methods have improved patient care by creating organized and efficient workspaces. In the retail sector, sorting has enabled businesses to manage inventory more effectively, leading to improved customer service and overall efficiency.
Executing Sort Within Your Business
Effective execution of the concept of Seiri (Sort) can significantly improve organizational efficiency within a business. By removing unnecessary items, tools, and equipment from the production floor or workspace, it becomes easier for employees to find what they need quickly and without wasting time. This optimization can also reduce the risk of workplace accidents and injuries due to clutter or poorly organized spaces.
Organizing tools and materials in designated areas can also prevent any misplaced parts or error in product assembly in manufacturing environments.
For example, utilizing color-coded floor tape to indicate the correct placement of tools and equipment can ensure a tidy and orderly workspace. In a healthcare setting, sorting can involve sorting through patient records, supplies, and equipment, which ensures the efficiency of healthcare workers and contributes to patient safety. In an office environment, sorting documents can help improve productivity by reducing the time employees spend searching for important papers, thereby increasing time spent on productive tasks. By effectively executing sorting practices, businesses can significantly improve overall efficiency and organization, regardless of the industry.
Illustrations of Effective Sorting
Effective sorting helps make work easier. It eliminates clutter and unnecessary items, making the work environment more organized. This saves time and improves productivity.
For example, in a manufacturing plant, a well-organized tool storage system using the 5S principles can save time and reduce the chances of misplacing tools. Best practices involve creating clear criteria for deciding which items are necessary, organizing them logically, creating visual cues and labels, and establishing maintenance schedules. These practices not only help in the efficient use of resources but also contribute to a safe and productive work environment.
Seiton (Straighten)
Seiton, or Straighten, is a fundamental principle in the 5S business methodology. It aims to ensure systematic arrangement and efficiency in the workplace.
By organizing items and tools in a structured, intuitive manner, employees can easily locate what they need. This reduces the time spent searching and minimizes disruptions to workflow.
This systematic arrangement also promotes safety and minimizes the risk of accidents, as tools and materials are stored in designated locations.
For example, in a manufacturing plant, tools can be arranged according to frequency of use. The most often used tools are placed closest to the work area.
In an office setting, filing cabinets and shelves can be labeled and organized in a logical order for easy access.
By streamlining operations through Seiton, the workplace becomes more productive. Employees spend less time looking for items and more time on value-adding tasks.
An organized and tidy workspace also has direct implications on morale and motivation. Employees feel more in control of their environment, ultimately boosting productivity.
The Rationale Behind Systematic Arrangement
The 5S methodology aims to create an organized, efficient, and standardized work environment. It improves workplace organization and efficiency, making tools, materials, and processes easily accessible to employees. This approach reduces waste and minimizes downtime, streamlining operations. It also provides a stable platform for further improvement activities and instills a culture of quality and productivity.
Arranging workstations in a specific order reduces the time spent searching for tools and materials, increasing productivity. Systematically arranging tools and equipment minimizes errors and defects in the manufacturing process, improving overall quality. An organized and standardized work environment fosters a sense of pride and ownership among employees, encouraging them to maintain the workplace meticulously.
Streamlining Operations with Seiton
Seiton is part of the 5S methodology. It helps to organize and standardize the work environment, making operations more efficient. By arranging tools, materials, and equipment systematically, employees can find and use what they need easily, saving time and increasing productivity. Best practices for implementing Seiton include labeling and color-coding items, creating storage spaces, and setting guidelines for maintaining order.
Floor markings and visual cues can also enhance Seiton’s effectiveness. It’s not just for manufacturing – Seiton can be used in offices, healthcare facilities, and retail establishments. Whether it’s organizing paperwork, standardizing workspaces, or arranging products on shelves, Seiton can improve efficiency in various settings.
Seisou (Shine)
Cleanliness and order are important at Seisou (Shine) because they create a safe and efficient work environment. Regularly cleaning and maintaining tools and equipment helps prevent accidents and injuries, making the workplace more productive. Best practices for implementing Seisou include creating a cleaning schedule, assigning responsibilities, and providing necessary tools and supplies.
A workplace that effectively implements Seisou (Shine) is where employees are trained and motivated to maintain cleanliness and order, where cleaning supplies are readily available, and where regular audits are conducted to ensure compliance.
For example, in a manufacturing facility, implementing a regular cleaning schedule for machines and work areas can significantly improve productivity and reduce the risk of mechanical failures or defects.
Why Cleanliness and Order Matter
Cleanliness and order are important in the 5S methodology. They help create a well-organized and efficient work environment.
Implementing the Sort and Set in Order principles eliminates clutter and ensures easy access to necessary tools and materials. This reduces time spent searching and minimizes workplace accidents.
Cleanliness and tidiness also contribute to organizational efficiency by creating a workspace conducive to productivity.
This allows employees to focus on tasks without distractions and reduces the risk of errors or defects due to disorganization.
Prioritizing cleanliness and order in workplaces leads to reduced downtime, increased productivity, and enhanced employee morale.
In manufacturing settings, a clean and well-organized workspace allows for smoother production processes and better quality control.
Best Practices for Implementing Shine
To effectively implement Shine in the 5S methodology, organizations should focus on regular cleaning and maintenance of the work environment. This means creating a daily cleaning routine, assigning cleaning responsibilities to employees, and providing the necessary tools and resources for cleaning tasks.
For example, a manufacturing facility can set daily cleaning schedules for workstations, machinery, and tools to keep the workplace clean and orderly. Visual cues like color-coded cleaning supplies and floor markings can help guide employees on effective cleaning.
Successful examples of workplaces implementing Shine in their 5S initiatives include manufacturing plants, healthcare facilities, and offices. Regular cleaning and maintenance have led to improved safety, efficiency, and workplace morale.
Examples of Shining Workplaces
Workplaces across different industries like healthcare, education, and offices have successfully applied the Seisou aspect of the 5S framework. In healthcare, it involves regular cleaning and maintenance of medical facilities for a safe and hygienic environment. Organizations sustain these improvements through regular audits, identifying areas for improvement, and continuous improvement.
Educational institutions have used the methodology to organize classrooms and improve the learning environment. Office settings have also adopted 5S to streamline workflows, reduce clutter, and boost productivity.
Seiketsu (Standardize)
In the 5S business methodology, standardization is crucial to maintaining improvements. Clear standards for the Standardize phase ensure sustained progress. Companies can uphold earlier 5S stages by setting specific guidelines and protocols for maintaining an organized work environment.
For example, a manufacturing plant improved safety and productivity by standardizing equipment maintenance and storage. Another company reduced waste and improved efficiency through standardized inventory management. These success stories demonstrate the positive impact of standardization on organizational productivity and effectiveness in the 5S framework.
The Essential Role of Standardization
Standardization is important in the 5S methodology. It helps maintain the improvements in workplace organization and efficiency. By implementing standards, businesses can have consistent processes for organization, cleanliness, and maintenance. This includes clear guidelines and procedures for everyone to follow, leading to greater efficiency and fewer errors. Developing and implementing standards in the 5S framework involve visual cues, training, and clear expectations for all employees.
Successful standardization stories in the 5S methodology include businesses achieving significant improvements in productivity, waste reduction, and employee morale. This results in streamlined workflows, improved safety, and better overall work environment quality.
Developing and Implementing Standards
Standards can be developed and implemented within an organization by following the 5S framework. The 5S framework consists of Sort, Set in Order, Shine, Standardize, and Sustain. Each step focuses on a specific area of workplace organization and efficiency.
For example, the “Sort” step involves removing unnecessary items from the workspace. The “Standardize” step involves developing and implementing standard procedures for maintaining the organized environment.
These standards can be customized to fit the specific needs of different work environments. For instance, a manufacturing facility may implement the 5S principles to reduce waste and improve productivity, while an office setting may focus on creating a clean and organized workspace to enhance focus and efficiency.
Regularly auditing and monitoring the workplace, providing ongoing training to employees, and incorporating the 5S principles into the organizational culture are key to ensuring sustained discipline and long-term improvement in the implementation of standards.
Standardize: Success Stories
Organizations have found success with the 5S methodology. It has led to better workplace organization and efficiency. Standardization, as part of the 5S initiatives, has reduced waste and downtime while boosting productivity. Developing and implementing standards within the 5S framework includes defining guidelines for organization and cleanliness, involving all employees, and regularly reviewing and updating standards for improvement.
These best practices are essential for successfully implementing standardized processes, leading to positive long-term outcomes for businesses.
Shitsuke (Sustain)
The Sustain phase of the 5S methodology can be maintained by using strategies like regular audits and visual management.
Regular audits ensure that the 5S standards are consistently met. Visual management tools, such as floor markings and labels, provide clear visual cues for maintaining the organized and standardized work environment.
Discipline in the Sustain phase (Shitsuke) of 5S can be upheld by fostering a culture of accountability and continuous improvement within the organization.
This involves regular training and education for employees, as well as clear expectations and involvement of all team members in maintaining standards.
Real-world examples of sustained 5S initiatives and their impact can be seen in manufacturing plants. The implementation of 5S has led to reduced waste, improved productivity, and enhanced workplace safety.
Consistently upholding the principles of Sort, Set in Order, Shine, Standardize, and Sustain has helped companies achieve long-term improvement and a culture of continuous improvement.
Maintaining Discipline for Long-Term Improvement
The Sustain phase of the 5S methodology requires disciplined strategies for long-term improvement. One way to achieve this is through regular monitoring and audits. These hold employees accountable for maintaining the standards set during the previous phases.
Ongoing training and education about the importance of sustaining the 5S principles can reinforce the discipline needed for continuous improvement.
Organizations can ensure sustained success of their 5S initiatives by creating a culture that values organization and cleanliness. They can also incorporate 5S into performance evaluations and recognition programs. This helps to prevent regression into old habits and motivates employees to consistently adhere to 5S principles.
Numerous companies and workplaces have effectively implemented and sustained 5S initiatives for long-term improvement. For example, Toyota has integrated the 5S methodology into its production system, resulting in greater efficiency, reduced waste, and improved workplace safety. Similarly, Boeing has successfully utilized 5S to streamline its manufacturing processes and improve overall productivity.
These real-world examples demonstrate the effectiveness of a disciplined approach to long-term improvement through 5S initiatives.
Strategies to Uphold the Sustain Phase
To maintain the Sustain Phase of the 5S methodology in an organization, specific strategies can be used. These include regular audits and visual management.
Regular audits involve periodic checks to ensure that the organization’s standards of cleanliness and organization, set by the 5S system, are being maintained. This can be done by designated team members or through 5S audit software.
Visual management involves using visual cues like floor markings and labels to sustain the practices established in the earlier stages of the 5S system.
These strategies help reinforce the importance of the Sustain Phase and maintain the gains made in workplace organization and efficiency.
Real-world examples of sustained 5S initiatives can provide practical insights into how the principles can be effectively incorporated and maintained in diverse applications. Studying successful examples can help businesses learn best practices and understand common challenges when implementing 5S principles.
Incorporating 5S into lean product and process development requires a focus on maintaining a clean and organized work environment while continuously improving processes. Strategies such as employee training, clear communication of 5S expectations, and creating a culture of accountability are necessary to ensure the Sustain Phase is upheld in these contexts. These strategies help embed 5S principles into the core values of the organization, ensuring long-term success in lean product and process development.
Real-World Examples of Sustained 5S Initiatives
Several companies have been able to sustain their 5S initiatives over the long term. This has led to better organization, efficiency, and productivity. They accomplished this by integrating 5S into their daily operations and making it part of their culture.
These companies provided extensive employee training, set clear expectations and benchmarks for maintaining 5S standards and implemented regular monitoring and auditing processes.
To ensure long-term success, they utilized strategies such as establishing cross-functional teams, conducting regular 5S events, rewarding best practices, and using visual management tools.
As a result, they created a work environment that promotes safety, quality, and efficiency, leading to increased employee satisfaction and higher overall performance.
Leveraging 5S Across Diverse Applications
Broadening 5S Beyond Manufacturing
5S principles can be used in non-manufacturing fields like healthcare, finance, and service industries. This involves focusing on organization, cleanliness, and process improvement. Strategies for implementing 5S in these areas include removing unnecessary items, creating a visual workplace, standardizing procedures, and fostering continuous improvement.
Examples of 5S in non-manufacturing settings include using color-coded labels and floor markings in healthcare for patient safety, applying 5Sin offices to boost productivity, and using 5S in the hospitality industry to enhance customer experience. Extending 5S to non-traditional industries and processes can result in improved safety, reduced waste, and increased efficiency.
Incorporating 5S into Lean Product and Process Development
The 5S methodology is a systematic approach to organizing the work environment and eliminating waste.
For example, the “Sort” principle involves removing unnecessary items from the workspace, preventing overproduction and excess inventory in lean manufacturing. “Set in Order” focuses on arranging tools and equipment in an ergonomic and efficient manner, leading to improved process flow and reduced motion waste. “Shine” ensures that work areas are clean and well-maintained, aligning with the goal of maintaining high-quality standards in lean production.
Specific strategies for implementing each of the 5S principles include creating visual management systems through floor markings and labels to facilitate easy identification and access to tools and materials.
Additionally, establishing clear maintenance schedules and checklists for equipment and workspaces supports the “Shine” and “Standardize” principles, contributing to overall equipment effectiveness (OEE) and equipment reliability in lean manufacturing environments.
Successful incorporation of 5S into lean product and process development initiatives across diverse industries is evident in cases where companies have implemented standardized workstations, optimized inventory control systems, and improved workplace safety through the application of 5S principles. Furthermore, utilizing 5S in product and process development has resulted in enhanced process efficiency, reduced lead times, and improvements in product quality across various industries, including automotive, pharmaceuticals, and consumer goods manufacturing.
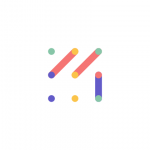
Vizologi is a revolutionary AI-generated business strategy tool that offers its users access to advanced features to create and refine start-up ideas quickly.
It generates limitless business ideas, gains insights on markets and competitors, and automates business plan creation.