5S Batch Processing: Speedy Work Tips!
Do you want to work more efficiently and get things done faster? You’ve come to the right place.
In this article, we’ll talk about 5S batch processing – a method that can help you streamline your work and increase productivity.
Whether you work in manufacturing, healthcare, or any other industry, these tips can make a big difference in your daily operations.
Let’s explore the benefits of 5S batch processing!
Understanding the 5S System: The Key to Efficient Workflows
The Origin of 5S: Its Japanese Roots and Meanings
The 5S system comes from traditional Japanese practices for workplace organization. It includes Sort, Set in Order, Shine, Standardize, and Sustain. These components have specific meanings and impact modern workplaces.
5S has been integrated into lean manufacturing and continuous improvement practices. It aims to improve safety, reduce downtime, and boost employee morale.
The roots of 5S are in Japanese history and culture, focusing on efficiency, cleanliness, and holistic organization. These influences shape the 5S framework for maintaining high productivity and work quality in global workplaces.
The Impact of 5S on Manufacturing and Business Efficiencies
Implementing the 5S system has a big impact on manufacturing and business. It creates an organized, standardized, and clean work environment. This helps to reduce waste, improve the overall work environment, and provide a stable platform for activities like Total Productive Maintenance and Kaizen. It also supports lean manufacturing and continuous improvement important for businesses today.
Incorporating the 5S framework into business operations brings several benefits. This includes reducing waste, minimizing downtime, improving safety, boosting employee morale, and enhancing customer satisfaction.
For instance, Toyota Production System saw improvements in operational efficiencies, waste reduction, and employee morale with the 5S system. Similarly, Boeing’s use of the 5S methodology led to better resource utilization, cost reduction, and operational effectiveness.
These examples show the significant impact of 5S implementation on manufacturing and business efficiencies, cementing its importance in today’s competitive business environment.
The Five Pillars of 5S Explained
Step 1: Sort (Seiri) – Decluttering the Workplace
The Sort (Seiri) step in the 5S framework is important for decluttering the workplace. It’s essential to create an efficient and effective work area. This step is crucial for lean manufacturing and continuous improvement in manufacturing companies. It promotes reducing waste and improving the work environment.
Practical ways of implementing the Sort step include categorizing and removing unnecessary items from the workspace. This ensures that only essential items remain in the area.
For example, a production floor can benefit from this practice by organizing tools and machinery, eliminating unused equipment, and separating defective items for repair or replacement.
Additionally, the Sort step helps in creating more space and streamlined processes. This ultimately increases productivity and reduces the time spent searching for items. This step is evident in industries such as automotive manufacturing, where workstations are often organized with necessary components, and unused tools are removed to maintain an efficient and safe workspace.
Understanding the Importance of Sort
The Sort step is important in the 5S system. It helps identify and separate necessary items from unnecessary ones. This clears the workspace of clutter, avoids hazards, and gives each item a designated location.
It leads to better workflow efficiency, improved accessibility, and less time spent searching for tools or materials. Sort also simplifies the workplace, making it easier to keep clean and reduces waste.
Best practices for implementing Sort in the 5S system include categorizing items, clearing out unneeded ones, and setting standard procedures for keeping only necessary materials to avoid future clutter.
Furthermore, Sort ensures that workplace areas only contain what is necessary for current tasks.
Best Practices for Implementing Sort
When implementing the Sort step of the 5S system, it’s important to consider some best practices.
First, declutter the work area by removing non-essential items. This creates more space and reduces the risk of errors and accidents.
Second, designate and clearly label storage spaces for the remaining items. This makes it easy for employees to find and return items, improving workflow.
These best practices are used in various industries. For example, in automotive manufacturing, components are sorted and organized based on their usage. Similarly, in healthcare, medical supplies and equipment are streamlined for optimal patient care and safety.
Regular audits and visual management systems help maintain the Sort (Seiri) process in these industries.
Real-life Examples of Sort in Action
Businesses in different industries have used the Seiri step of the 5S system to make their workspaces more organized and efficient.
For instance, an automobile manufacturing plant organized workstations, tools, and components, which reduced the time workers spent looking for tools and materials.
In a retail setting, implementing Seiri led to a more organized stock management system and faster responses to customer queries.
In food production, refining raw materials inventory management reduced waste and improved ingredient storage.
Step 2: Set in Order (Seiton) – Organizing for Efficiency
Organizing a work area for efficiency is a key part of the 5S system. This step, called Set in Order (Seiton), involves arranging and labeling tools, materials, and equipment so that they are easy to find and use.
It’s important because it helps workers find what they need quickly, reduces unnecessary movement, and saves time. This makes the workflow smoother and increases productivity.
Setting in Order also helps to keep the workplace organized, ensures that the right tools are always available, simplifies processes, and saves time. For example, in manufacturing, organizing tools and equipment helps workers quickly access what they need, reducing downtime and preventing delays.
This practice also enhances safety by reducing accidents and injuries caused by disorganized work areas.
The Rationale Behind Set in Order
The “Set in Order” step in the 5S system is about making the workplace more organized and efficient. It means arranging items logically and accessibly to reduce wasted time and movement. This, in turn, reduces waste and improves the work environment.
“Set in Order” helps employees find tools and resources quickly, reducing accidents and workflow disruptions. It involves labeling, color-coding, clear storage areas, and ergonomic workstations. Regular maintenance and inspections are important to remove unnecessary items and ensure workers have all the tools they need.
Guidelines for Effective Setting in Order
The 5S Batch processing system has guidelines for effective setting in order. This includes defining and arranging basic items for a specific work area, minimizing time spent locating tools, and increasing the ease of work processes.
To ensure efficient organization and workflow through the 5S Set in Order pillar, organizations must store tools and equipment close to the point of use. They should also use visual controls to enhance the workplace and communicate its operational status. Additionally, each item should have its own dedicated place.
Best practices for implementing Set in Order in the workplace include using clear labeling and signage, and designing efficient layouts to maintain the greatest amount of available space. Regular audits and immediate correction of disorganization issues are crucial for success.
Step 3: Shine (Seiso) – Ensuring a Spotless Environment
Shine (Seiso) is an important part of the 5S Batch system. During the Shine phase, businesses keep their working areas clean to support efficiency and safety. Successful Shine initiatives include daily cleaning, deep cleaning, proper storage, and regular maintenance. A clean and organized workspace not only helps maintain tools and equipment but also boosts employee morale. It creates a positive atmosphere, showing that the business cares about employee safety and comfort.
This leads to a greater sense of pride and responsibility among the workforce and reduces the risk of accidents, ultimately improving overall business productivity and success.
Shine’s Role in Maintenance and Morale
Shine is a key part of the 5S system. It focuses on keeping the workplace clean and organized. Employees regularly clean and inspect all areas to catch and fix potential problems. This helps prevent equipment defects and breakdowns, maintaining a smooth workflow. A clean and organized workplace creates a safer and more efficient environment, making employees feel more comfortable and motivated.
This boost in morale and job satisfaction comes from the happier and more genuinely confidentfeeling employees have in a neat and clean workspace. Regular cleaning and maintenance also positively impact employee morale and satisfaction.
Techniques for a Successful Shine Initiative
Shine is an important part of the 5S system for keeping a manufacturing environment clean and safe. Some techniques for a successful Shine initiative include scheduling daily cleanings or inspections, using cleaning as a team-building exercise, and promoting employee-driven initiatives.
Shine contributes to enhanced employee morale by promoting workplace cleanliness and reducing accidents due to improved workplace visibility. Some best practices for ensuring a spotless environment as part of a Shine initiative in the 5S system include clearly outlining cleaning responsibilities for employees, providing adequate training on the proper use of cleaning materials, and setting clear cleanliness standards for all work areas.
These proactive measures help ensure a consistently organized and clean work environment that supports the well-being and satisfaction of all employees.
Step 4: Standardize (Seiketsu) – Creating Uniformity
Standardization is an important part of the 5S system. It helps make processes consistent and efficient. By setting standards, materials and tools are stored in the right places. This also helps everyone understand the proper processes and ensures they are done in a predictable way. To maintain consistency, it’s helpful to create cleaning schedules, define roles and responsibilities, and prepare written procedures or diagrams.
Peer audits can also be used to check how well the 5S principles arefollowed and to keep the plan on track. This adds accountability to maintain the standards.
The Need for Standardization in Processes
Standardization is important in the 5S framework. It helps maintain consistent processes for workplace organization.
Following standardized practices helps minimize errors and variation, leading to increased productivity and efficiency.
Incorporating standardization in processes within the 5S framework creates a structured environment that enhances workflow, fosters effective communication, reduces waste, and promotes safety.
Not using standardization can lead to disorganization, inconsistent quality, and higher operational costs. It may also cause confusion, inefficiency, and disorder, hindering business and manufacturing workflows.
Standardize: Methods for Maintaining Consistency
During the Standardize step of the 5S system, it’s important to:
- Create clear and simple guidelines for business processes.
- Conduct regular audits to ensure compliance.
- Map out standardized work instructions.
These methods help businesses maintain consistent processes and workflows. Visual aids, thorough training, and clear expectations of employee responsibilities are also essential for uniformity and consistency within the 5S framework. These practices support an organized and efficient work environment, allowing employees to perform tasks accurately and consistently.
Step 5: Sustain (Shitsuke) – Cultivating Discipline
To maintain the success of the 5S system in the long term, businesses can:
- Provide ongoing training and support to all employees.
- Create accountability measures and conduct regular peer reviews.
- Building habits to sustain the system’s success is important.
- Discipline promotes adherence to the system’s principles and standards.
- Fostering discipline within the workplace promotes continuous improvement and organizational excellence.
Sustain: Building Habits for Long-term Success
Building habits for long-term success within the 5S system involves maintaining organization and efficiency in the workplace. Integrating the concept of “Sustain” into company culture is crucial for long-term success. This can be achieved by fostering discipline and accountability among employees.
Businesses can also implement regular check-ins, audits, and training programs to reinforce the importance of the 5S system. Creating a workplace environment that promotes ongoing learning and improvement is essential for building lasting habits.
Providing ongoing education and support ensures that the 5S framework becomes ingrained as a long-term habit, leading to sustained efficiency and organization in the workplace.
Constructing Your 5S Implementation Strategy
Preparing Your Business for 5S Integration
Preparing a business for 5S integration involves:
- Identifying current workplace errors and issues.
- Educating staff about the system.
- Creating an action plan for implementation.
The action plan includes:
- Providing training on the 5S system.
- Conducting one-day sessions with each employee or team.
- Ensuring safety by defining ways to standardize processes and organizing cleaning schedules.
- Preparing written procedures or diagrams to help employees remember safety measures.
- Conducting peer audits to evaluate compliance with safety standards.
Developing an Action Plan for 5S Procedures
Businesses often find areas that need to be decluttered and organized in the workplace. This is part of the Sort and Set in Order steps of the 5S system. Effective and consistent labeling and color-coding of work areas and supplies are used.
Consultants or employees analyze the workflow and identify where unneeded items accumulate. Employers provide regular employee training on what items need to be stored and where, and ensure compliance.
The Visual Workplace solution in the 5S system is important for this process.
For the Shine, Standardize, and Sustain steps, businesses ensure consistent module meetings are in place. They also perform daily inspections of work environments.
In the long term, businesses take advantage of SMART technology (specific, measurable, achievable, relevant, timely) to keep the systems in place and merge these systems into the present.
Organizations have also incorporated Kaizen into the 5S system to ensure sustainable long-term success.
The Critical Role of Safety in the 5S Framework
Safety is important in the 5S framework. It helps create a secure work environment where employees feel empowered to identify and address potential hazards without fear of repercussions.
Maintaining a safe work environment helps employees concentrate on their work, leading to fewer accidents and improved safety.
By fostering a culture of safety, where employees are encouraged to speak up about potential issues, organizations can successfully implement and sustain the 5S principles.
Integrating safety measures impacts the success of the 5S methodology by reducing the risk of workplace hazards and accidents, allowing employees to focus on refining processes and workflows.
Addressing safety within the 5S framework not only protects the well-being of the employees but also has a direct impact on the overall success of the 5S system in delivering improved productivity and operational excellence.
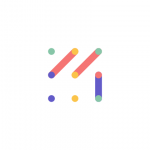
Vizologi is a revolutionary AI-generated business strategy tool that offers its users access to advanced features to create and refine start-up ideas quickly.
It generates limitless business ideas, gains insights on markets and competitors, and automates business plan creation.