Your Guide to Lean Methodology Application
Are you interested in making your business more efficient and cutting out unnecessary practices? Lean methodology could be the solution. It’s an effective approach that aims to maximize customer value and reduce waste.
In this guide, we’ll look at how lean principles can be used across different industries. We’ll also offer practical advice on implementing lean methodology in your organization. Whether you work in manufacturing, healthcare, or technology, this guide can help you make the most of lean methodology to boost efficiency and progress in your business.
Core Elements of Lean Methodology
Continuous Improvement Explained
Continuous Improvement is a core principle of Lean Methodology. It focuses on creating value and learning. The method highlights the importance of constantly improving processes, products, and services. This is crucial for creating value for the customer and building stronger organizations.
Frontline workers are empowered by being involved in identifying and solving problems to improve work processes. Continuous Improvement originated in manufacturing through the concept of Kaizen, promoting small, incremental changes over time. As Lean methodology expanded to software development and other industries, the same principles were adapted to foster a culture of ongoing learning and improvement.
Empowering Frontline Workers
Organizations can empower frontline workers by involving them in continuous improvement projects and decision-making. This allows them to use their knowledge and expertise to generate innovative solutions and improvements.
Additionally, training on Lean methodologies and tools such as value stream mapping, just-in-time (JIT) practices, and error-proofing can equip frontline workers to make valuable contributions to the organization. Leadership can promote a culture of empowerment and collaboration by actively listening to frontline workers’ ideas, recognizing their contributions, and providing a supportive environment. This inclusive approach fosters a sense of ownership and accountability among frontline workers, driving positive change and efficiency within the organization.
Origins in Manufacturing
Lean methodology has historical origins in the manufacturing industry, starting with the Toyota Production System in the 1950s. The system aimed to reduce waste and improve efficiency through continuous improvement and respect for people.
Over time, lean methodology has evolved and adapted in manufacturing by integrating various tools and principles. These include bottleneck analysis, just-in-time , value stream mapping, overall equipment effectiveness (OEE), plan-do-check-act (PDCA), and error proofing.
Manufacturing has shaped lean methodology by highlighting the importance of optimizing resources and efforts to create value for the customer. It has also extended into other sectors like software development, healthcare, and service industries, showing its versatility and effectiveness beyond traditional manufacturing processes.
Adapting Lean for Software Development
In software development, Lean principles focus on continuous improvement and respect for people. This helps teams optimize resources and efforts towards creating value for the customer and building healthier organizations.
Bottleneck analysis and value stream mapping can identify and eliminate inefficiencies in the software development process. Just-in-time methodologies can reduce waste in the development cycle.
Project management practices can be aligned with Lean principles by implementing plan-do-check-act cycles and error proofing techniques to improve efficiency and productivity.
This approach enables teams to deliver more value sustainably to their customers, regardless of the industry they operate in.
Lean Methodology Tools and Techniques
Bottleneck Analysis to Identify Process Blockers
Bottleneck analysis is an important part of Lean methodology. It helps organizations find and fix process blockers that slow down work. Finding these blockers shows where there are problems and helps decide what to improve first. Techniques like value stream mapping and overall equipment effectiveness can be used to find and study process blockers. This gives a clear idea of where to make improvements.
Including bottleneck analysis in Lean methodology focuses on making continuous improvement targeted. This means efforts can be focused on the most important areas to make processes more efficient and productive. Using bottleneck analysis with Lean principles like continuous improvement and respect for people helps organizations use their resources better. This way, they can give more value to their customers in a sustainable way, no matter what industry they’re in.
Implementing Just-in-Time (JIT) to Reduce Waste
Implementing Just-in-Time in manufacturing means coordinating production with demand. The goal is to minimize inventory and reduce waste.
For example, a company can use JIT to order only the materials needed at that time. This avoids stockpiling excess supplies, reducing the risk of obsolescence and freeing up storage space. However, there are considerations and challenges, such as potential supply chain disruptions and the need for reliable suppliers. To support successful JIT implementation for waste reduction, businesses can use Lean Methodology tools. These tools include value stream mapping to identify non-value-adding activities and eliminate them. In addition, overall equipment effectiveness can help measure equipment efficiency and reduce downtime, promoting better synchronization with JIT production. By applying Lean Methodology tools and techniques, businesses can optimize their operations to effectively implement JIT and reduce waste.
Mapping Value Streams to Enhance Flow
Mapping value streams is a way to visually represent the steps and information flow required to deliver a product or service. This helps identify opportunities to enhance flow within a process or system. By examining the process from beginning to end, inefficiencies, waste, and non-value-adding activities become evident, enabling organizations to make necessary improvements.
Key steps and considerations in mapping value streams include:
- Identifying critical processes
- Analyzing the flow of materials and information
- Distinguishing value-adding and non-value-adding activities
- Collaborating with teams from different departments to ensure a holistic view of the entire process
Pursuing Perfection through PDCA Cycle
The PDCA Cycle, also known as the Deming Cycle, is a foundational tool for continuous improvement. It has four main steps: Plan, Do, Check, Act.
By following this cycle, organizations can identify areas for improvement, make changes, assess the results, and then act on those results to drive further improvements.
This iterative process encourages teams to continuously strive for perfection by identifying and addressing inefficiencies, errors, and waste in their processes.
The key principles of the PDCA Cycle include data-driven decision-making, iterative problem-solving, and a focus on sustainable change.
In the context of lean methodology, the PDCA Cycle supports the pursuit of perfection by providing a structured approach to problem-solving and improvement.
By leveraging the PDCA Cycle, organizations can streamline workflows, reduce defects, and enhance overall value delivery to customers, in line with the principles of lean methodology.
Enhancing Quality with Error Proofing
Implementing error proofing in Lean methodology involves important strategies. These include design for manufacturability, mistake-proofing processes, and training employees to recognize and respond to errors. Through integrating error proofing into the value stream mapping process, organizations can identify areas where errors occur and implement solutions to enhance flow and reduce defects.
Calculating Overall Equipment Effectiveness is important in error proofing. It helps organizations measure the efficiency of their equipment, identify improvement opportunities, and reduce unplanned downtime. By using error proofing techniques and tools like mistake-proofing devices, visual management, and standardized work, organizations can minimize errors, enhance product quality, and deliver sustainable value to their customers.
Calculating Overall Equipment Effectiveness (OEE)
Overall Equipment Effectiveness is important because it looks at three things: availability, performance, and quality.
Availability is about comparing how long equipment is actually working to how long it should work.
Performance is about how fast the equipment works compared to its design speed.
Quality is about how many good parts are made compared to the total parts.
To find OEE, you multiply these three factors together: OEE = Availability x Performance x Quality.
Calculating OEE can help find areas of inefficiency, reduce waste, improve equipment performance, and boost productivity. This can lead to continual improvement, which is a key goal of Lean methodology, by using data to make decisions and create value for customers.
Applying Lean in Project Management
Lean Portfolio Management Practices
Lean Portfolio Management Practices can help improve the flow of value streams in a project portfolio. This is done through continuous improvement and respect for people.
The goal is to optimize resources and efforts to create value for the customer and build healthier, more resilient organizations. In terms of leadership, Lean methodology focuses on empowering frontline workers and promoting value creation and learning.
Lean training programs offer many benefits, including improved efficiency, reduced waste, and increased customer satisfaction. Online Lean Six Sigma certifications can also help with the adoption of Lean methodologies in project management.
These certifications provide comprehensive training on Lean tools and principles such as bottleneck analysis, just-in-time , value stream mapping, overall equipment effectiveness , plan-do-check-act , and error proofing. They also equip professionals with the necessary skills to implement Lean principles effectively across various industries.
Adopting Lightweight Leadership Styles
Adopting lightweight leadership styles can greatly contribute to the implementation of lean methodology in project management. It promotes collaborative decision-making and empowers frontline workers. Lightweight leadership decentralizes authority and encourages team members to take ownership of their work. This fosters an environment of continuous improvement and adaptability, aligning with lean methodology’s core principles.
This approach allows teams to identify and address inefficiencies in real-time, leading to more effective problem-solving and resource utilization. Empowering frontline workers presents benefits such as increased employee engagement and motivation, improved quality and efficiency, and a greater sense of accountability and responsibility. Employees feel valued and trusted to make decisions, strengthening their commitment to the organization’s goals and values, resulting in enhanced productivity and overall job satisfaction.
This approach also contributes to a more inclusive and diverse workplace culture. Lean training programs and online certifications are valuable resources for individuals looking to develop and integrate lightweight leadership styles into their approach to lean methodology. These programs provide comprehensive education and practical tools for mastering lean principles and cultivating effective leadership skills.
By equipping individuals with the knowledge and competencies necessary to lead lean initiatives and promote a culture of continuous improvement, these certifications play a critical role in driving organizational success and sustainability.
Educational Pathways in Lean Methodology
Advantages of Lean Training Programs
Lean training programs have several advantages for organizations. They promote efficiency and productivity by giving employees tools and methods to identify and eliminate waste in their processes. This includes using Lean principles like value stream mapping and just-in-time production to streamline operations and reduce lead times, boosting overall productivity.
Additionally, Lean methodology encourages a culture of continuous improvement within an organization. Employees in Lean training programs are empowered to constantly seek ways to optimize processes, reduce defects, and improve quality. This creates a work environment that focuses on learning, adaptation, and innovation.
Exploring Online Lean Six Sigma Certifications
Online Lean Six Sigma certifications offer many benefits. They provide flexibility, cost-effectiveness, and the ability to learn at your own pace. These certifications deepen understanding of core Lean Methodology tools and principles. These include bottleneck analysis, JIT, value stream mapping, OEE, PDCA, and error proofing.
The programs also cover how Lean methodology benefits various industries, such as manufacturing, software development, and project management. By using case studies from diverse sectors, online Lean Six Sigma certifications show how Lean principles can adapt to different fields.
For example, in software development, Lean principles can reduce waste and streamline processes, leading to higher-quality products and faster delivery. Project management professionals can also benefit by learning to improve processes and minimize delays.
These certifications highlight the versatility of Lean Six Sigma, making it a valuable asset for professionals looking to enhance their skills and make a meaningful impact in their industries.
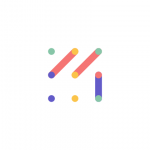
Vizologi is a revolutionary AI-generated business strategy tool that offers its users access to advanced features to create and refine start-up ideas quickly.
It generates limitless business ideas, gains insights on markets and competitors, and automates business plan creation.