How to Adopt Lean Methodology at Work
Lean methodology has changed how many companies work. It focuses on efficiency and cutting waste, making a big impact in business. If you want to use lean methodology at work, you’re in the right spot. This article will cover the basics and how to apply it to boost productivity and streamline operations. Let’s dive in and elevate your work with lean methodology.
Understanding the Core Philosophies of Lean
Vizologi
A generative AI business strategy tool to create business plans in 1 minute
FREE 7 days trial ‐ Get started in seconds
Try it freeLean methodology focuses on core philosophies that shape organizational culture and processes. It emphasizes understanding value from the customer’s perspective, eliminating waste, and empowering employees for continuous improvement. By adopting these philosophies, organizations create a culture of efficiency, innovation, and customer-centricity while reducing costs.
To encourage Lean adoption, organizations can communicate the benefits of Lean principles in addressing current challenges like inefficiencies, quality issues, or customer complaints. They can also share success stories and highlight the competitive advantage gained through Lean practices. Setting clear objectives and metrics for improvement can reinforce the importance of immediate action.
Sustaining Lean methodology requires strategies like regular training for employees, collecting and analyzing performance data, fostering problem-solving and collaboration, and engaging employees in decision-making. Implementing feedback loops and encouraging innovation and learning are essential for long-term success.
Setting the Foundation for Change
Igniting a Sense of Urgency for Lean Adoption
Effective communication is important for encouraging the use of lean principles. Leaders can do this by sharing real examples of how lean methods improve efficiency, productivity, and quality. They can also use data to show how lean adoption increases customer satisfaction and boosts overall organizational performance. Engaging employees in continuous improvement and giving them ownership of their work processes is also key.
To get everyone on board with lean methodologies, leaders should have open discussions about the benefits of lean, gather feedback from employees, and make sure lean goals align with the organization’s mission and vision.
Defining Objectives and Key Performance Indicators
Defining objectives and key performance indicators (KPIs) in Lean methodology is important. It helps measure progress and provide clear direction for continuous improvement. This involves setting specific objectives and KPIs to focus on eliminating waste and creating value. It aligns efforts with Lean principles like improving efficiency, productivity, and customer satisfaction.
Organizations can communicate objectives and KPIs effectively by engaging employees at all levels. This includes providing training and resources for understanding and integrating them into daily operations. This creates a shared sense of purpose and empowers employees to identify and address issues in real-time, leading to sustained improvements.
Mapping the Lean Journey
Identifying Crucial Value Streams
The organization has important processes that help deliver value to customers. Identifying these value streams can help prioritize and improve them to align with business objectives.
Tools like value stream mapping and process analysis can help recognize areas for efficiency improvements and waste elimination.
Engaging employees and implementing continuous improvement practices can refine and optimize value streams to meet customer needs, increase productivity, and enhance overall customer satisfaction.
Process Mapping: Visualization for Efficiency
Process mapping helps organizations become more efficient. It visualizes workflows and identifies bottlenecks. This gives organizations a clear understanding of their processes. It leads to improved productivity, reduced lead times, and minimized waste.
Process mapping also helps identify and eliminate waste in value streams. Examples of waste include overproduction, excess inventory, and unnecessary transportation. It provides a visual representation of the entire process.
Visualization techniques like flow charts, swimlane diagrams, and value stream maps promote continuous improvement. They help employees understand processes better. This empowers them to identify areas for improvement and make changes that drive efficiency.
For example, by mapping a process and highlighting waste areas visually, employees can work together to streamline the workflow. This ultimately improves overall efficiency. Process mapping and visualization lead to significant improvements in operations and foster a culture of continuous improvement.
Cultivating a Lean Culture
Fostering Employee Engagement in Lean Practices
Organizations can foster employee engagement in lean practices and cultivate a lean culture in several ways.
They can involve employees in decision-making processes, encourage open communication, and provide opportunities for skill development and training.
This can be achieved through regular feedback sessions, recognition of employee contributions, and creating a culture of collaboration and accountability.
Strategies for empowering the workforce for continuous improvement in lean methodology include providing necessary resources and support, setting clear expectations, and promoting a problem-solving mindset among employees.
Organizations can measure success in fostering employee engagement in lean practices by tracking performance metrics such as cycle time reduction, defect rates, and employee satisfaction surveys.
Recognizing achievements in lean adoption can be done through employee recognition programs, celebrating milestones, and sharing success stories within the organization.
Empowering the Workforce for Continuous Improvement
Organizations can foster employee empowerment in Lean practices. They can do this by engaging employees in decision-making, encouraging open communication, and providing training opportunities.
Involving employees in problem-solving and decision-making instills a sense of ownership and commitment to continuous improvement. Recognizing and rewarding their contributions can also motivate the workforce to sustain a Lean culture.
Recognizing and rewarding employee contributions includes acknowledging their efforts publicly, offering performance incentives, and providing career development opportunities. These strategies help cultivate a Lean culture that encourages employee involvement in continuous improvement.
Sustaining Lean Methodology
Implementing Continuous Improvement Techniques
To implement continuous improvement and sustain lean methodology, an organization can start by fostering a culture of ongoing improvement and learning. This keeps employees engaged and makes continuous improvement a natural part of their routine. Encouraging small improvement projects and empowering employees to identify and address inefficiencies creates a sense of accomplishment and motivation.
Additionally, regularly measuring and analyzing key performance indicators like cycle time reduction, defect rate, and work in progress is essential for evaluating the success of continuous improvement techniques.
Lastly, organizations can promote employee engagement by involving them in the value stream mapping process, providing learning and skill development opportunities, and recognizing and rewarding employee-driven improvements.
By taking these steps, businesses can successfully embed continuous improvement practices within their organizational culture and realize the long-term benefits of lean methodology adoption.
Measuring Success and Recognizing Achievements
Measuring success in lean implementation means tracking key performance indicators. These include improved efficiency, reduced waste, increased productivity, and higher customer satisfaction. The organization uses metrics like cycle time, lead time, defect rate, and on-time delivery to monitor progress.
To recognize achievements, the organization celebrates milestones in the adoption of lean principles. This includes successful value stream mapping, waste elimination, and continuous improvement practices.
Furthermore, the organization ensures sustainability by embedding lean thinking into the company culture. It empowers employees to identify and address process inefficiencies. The organization encourages a continuous improvement mindset, establishes regular review cycles, and fosters a culture of learning and knowledge sharing to build upon successful lean initiatives for ongoing improvement.
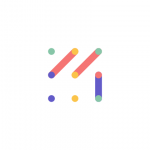
Vizologi is a revolutionary AI-generated business strategy tool that offers its users access to advanced features to create and refine start-up ideas quickly.
It generates limitless business ideas, gains insights on markets and competitors, and automates business plan creation.