Kaizen Implementation Made Simple
Kaizen is a Japanese business philosophy focused on continuous improvement. It’s gaining popularity in today’s corporate world. Implementing Kaizen doesn’t have to be daunting.
In this article, we’ll break down the process into simple, easy-to-follow steps. By the end, you’ll understand how to incorporate Kaizen into your business in a manageable and effective way. Let’s get started!
Understanding Kaizen and Continuous Improvement
Kaizen means continuous improvement. It focuses on making rational changes in organizational processes. The concept helps employees and managers achieve continuous improvement.
There are seven steps to applying Kaizen in any organization:
- Involving employees.
- Reviewing the workplace.
- Identifying problems.
- Developing solutions.
- Pilot testing.
- Implementing solutions.
- Standardizing processes
Kaizen aims for slow, gradual, and incremental change, leading to a culture focused on removing waste and enhancing processes for efficiency.
Adebayo, a thought leader in continuous process improvement and manufacturing excellence, emphasizes the importance and benefits of Kaizen.
Kaizen is a Japanese philosophy that constantly seeks ways to improve processes within an organization. Companies implementing Kaizen report positive results, such as improved quality, shorter delivery times, reduced costs, more effective management, increased safety, and improved morale.
The Kaizen process involves identifying opportunities for change, analyzing current processes, developing a solution, implementing the solution, analyzing results, standardizing the change, and planning future improvements. Successful implementation requires involving everyone, encouraging personal process checks by management, and prioritizing data tracking.
Kaizen is a culture, not just a process, and requires a cultural shift in the organization to support continuous improvement rather than maintaining the status quo.
Kaizen vs. Traditional Improvement Models
Kaizen focuses on slow, gradual, and incremental change, promoting a culture that removes waste and enhances processes for efficiency. This is different from traditional improvement models, which emphasize radical changes. Embracing Kaizen offers advantages like improved quality, shorter delivery times, reduced costs, more effective management, increased safety, and improved morale.
When implementing Kaizen, organizations should avoid pitfalls such as mismanagement of the cultural shift, failure to involve everyone, overlooking personal process checks by management, and neglecting data tracking to ensure that changes are having the desired impact. In comparison, traditional improvement models may not fully prioritize these aspects, leading to less successful outcomes.
Key Advantages of Embracing Kaizen
Embracing Kaizen in an organization has many advantages. It can lead to improved quality, shorter delivery times, reduced costs, more effective management, increased safety, and improved morale.
Implementing the philosophy of Kaizen allows companies to achieve continuous improvement and long-term success through a slow, gradual, and incremental change. This change leads to a culture focused on removing waste and enhancing processes for efficiency.
This approach offers a competitive advantage over traditional improvement models. It involves identifying opportunities for change, analyzing current processes, developing a solution, implementing the solution, analyzing results, standardizing the change, and planning future improvements.
Getting Started with Kaizen
Cultivating a Kaizen Mindset in Your Organization
An organization can form a diverse Kaizen team by:
- Encouraging personal process checks by management.
- Making interdepartmental collaboration a regular habit.
- Facilitating brainstorming conversations between members of different departments or at different management levels.
Recognizing opportunities for improvement involves:
- Questioning current practices.
- Measuring impacts.
- Thinking small.
These strategies can be implemented effectively by:
- Establishing employee feedback as a part of every process.
- Keeping a record of all employee input.
- Removing barriers that prevent collaboration or progress tracking.
To optimize Kaizen and maintain momentum, digital solutions can be used:
- Employing software for easy tracking of changes.
- Engaging employees in a digital feedback system.
- Ensuring that all departments have access to technological tools for continuous improvement.
Assembling a Diverse Kaizen Team
The organization can ensure the Kaizen team is diverse in skills, experience, and perspectives by involving employees at all levels. Facilitating brainstorming conversations between members of different departments and recognizing the success of team members is also important. Priority should be given to data tracking.
To attract and retain a diverse group of individuals for the Kaizen team, it’s crucial to support Kaizen from the top. Barriers that prevent collaboration should be removed, and employee feedback should be established as part of every process.
Diversity within the Kaizen team contributes to the overall success of continuous improvement efforts. It helps to get ideas flowing, remove barriers, recognize success, and measure impacts.
Defining Clear Objectives
Kaizen aims to achieve specific goals and targets. These include improving quality, reducing waste, increasing efficiency, and fostering a culture of continuous improvement. To define these objectives, teams can set SMART goals: specific, measurable, achievable, relevant, and time-bound. This helps ensure focus and direction in the Kaizen process.
Metrics like process cycle time, defect rates, customer satisfaction scores, and employee engagement levels can measure the success of the Kaizen initiative. Tracking these metrics provides insights into the impact of implemented changes.
Recognizing Opportunities for Improvement
The organization can find areas for improvement in its processes or systems through the Kaizen process. This involves involving everyone, gathering feedback and ideas, and facilitating conversations between departments.
Employees should question current practices and examine processes constantly. To recognize improvement opportunities, the organization can analyze current processes, measure impacts, and develop solutions. Pilot testing for potential solutions can help standardize and track results.
Encouraging employees and teams to actively seek improvement by supporting Kaizen, removing internal barriers, and keeping ideas flowing is important. Recognizing success and congratulating team members for their contributions is also essential in continuous improvement.
Kaizen Implementation Strategies
Initiating the Plan: The ‘Plan’ Phase in the PDCA Cycle
The ‘Plan’ phase of the PDCA cycle starts by setting goals and defining objectives. Organizations also look for areas where they can make things better. They assess current processes, analyze data, and figure out what needs to improve. Clear objectives help companies focus on specific areas like reducing waste, improving quality, or increasing efficiency. To find improvement opportunities, they ask for employee feedback, check customer satisfaction, and analyze performance.
It’s important for organizations to keep measuring and analyzing progress to make sure they’re hitting their improvement goals in the ‘Plan’ phase of the PDCA cycle.
Executing the Plan: The ‘Do’ Phase in the PDCA Cycle
During the ‘Do’ phase of the PDCA Cycle, there are some important steps and considerations to remember:
- Involve everyone in the organization.
- Prioritize personal process checks by management.
- Focus on data tracking to monitor progress.
To build a Kaizen mindset and assemble a diverse Kaizen team during this phase, encourage input and feedback from employees at all levels. Also, facilitate brainstorming conversations and recognize the successes of the team.
Some common pitfalls to avoid during the ‘Do’ phase are not chasing perfection, thinking small to avoid overwhelming start-up processes, and questioning current practices rather than maintaining the status quo.
Strategies for maintaining the momentum of Kaizen during this phase include providing ongoing training, removing barriers that hinder progress, and sustaining interdepartmental collaboration as a regular habit.
Evaluating Outcomes: The ‘Check’ Phase in the PDCA Cycle
The ‘Check’ phase is part of the PDCA cycle. It helps evaluate outcomes in the context of Kaizen and continuous improvement. This phase involves reviewing the results of implemented changes and comparing actual outcomes with expected ones. It also identifies any deviations and determines the effectiveness of the changes made.
During the ‘Check’ phase, organizations can use strategies like data tracking, performance measurement, and impact analysis. These help assess the progress and impact of Kaizen initiatives. Involving everyone in the evaluation process, prioritizing accurate and relevant data collection, and encouraging personal process checks by management are important for meaningful insights and actionable improvements.
Additionally, the ‘Check’ phase should prioritize continuous learning. This allows organizations to adapt and make further improvements based on the insights gained from the evaluation.
Refining Processes: The ‘Act’ Phase in the PDCA Cycle
Organizations can improve their processes during the ‘Act’ phase of the PDCA cycle. They can do this by using continuous improvement strategies, like the Kaizen philosophy. They can also involve employees and measure the impacts of changes.
During this phase, it’s important to standardize processes, recognize and celebrate successes, and keep track of changes over time. For example, involving all employees in gathering improvement ideas and establishing a clear reporting process can lead to successful implementation.
However, organizations often face challenges during this phase. These challenges include resistance to change, lack of management support, and difficulty in effectively tracking and measuring impacts.
Kaizen Methodologies and Tools
Root Cause Analysis with ‘The 5 Whys’
The 5 Whys is a powerful tool for root cause analysis in Kaizen. This method involves asking “why” at least 5 times to uncover underlying issues that need to be addressed. It can reveal inefficiencies, errors, or defects in processes, leading to more targeted solutions.
By continually asking “why,” organizations can pinpoint areas for improvement and make data-driven decisions. Addressing problems at their source prevents recurring issues and promotes sustainable change. This aligns with the essence of Kaizen, which focuses on making small, incremental improvements over time.
The 5 Whys contributes to the success of Kaizen methodology by providing a structured approach to problem-solving. It encourages organizations to delve deeper into the underlying causes of problems, promoting a culture of continuous improvement and learning. This can lead to enhanced productivity, efficiency, and quality, ensuring lasting change in various industries.
Visualizing Problems: Fishbone Diagram (Ishikawa)
A Fishbone Diagram, also known as an Ishikawa diagram, is a visual tool. It aims to categorize potential causes of a problem to identify its root causes. In the context of Kaizen and continuous improvement, this diagram is used to visualize problems. The goal is to understand their underlying causes and find effective solutions.
By creating a Fishbone Diagram, an organization can analyze different factors that may contribute to an issue. These factors include equipment, people, processes, materials, and the environment. This approach helps in identifying the key causes of problems, which is essential for implementing sustainable solutions.
The use of a Fishbone Diagram in Kaizen allows organizations to pinpoint the root causes of issues. This is done by visually organizing various factors that could potentially contribute to a problem. It enables teams to conduct a structured analysis of the problem, leading to a comprehensive understanding of the contributing factors. This, in turn, empowers organizations to address the actual causes of the issues rather than just treating the symptoms, resulting in more effective and lasting solutions.
The key benefits of utilizing a Fishbone Diagram as a tool for problem visualization in the context of Kaizen methodologies include improved problem-solving efficiency, enhanced team collaboration, and the ability to prioritize improvement efforts effectively. By visually representing the potential causes of a problem, teams can better focus their efforts in addressing the most critical underlying issues, leading to sustainable and measurable improvements.
Additionally, the collaborative nature of creating a Fishbone Diagram encourages the involvement of team members at various levels. This results in a more comprehensive analysis and solution development process.
Prioritizing with Pareto Analysis
Pareto Analysis is a helpful tool in Kaizen. It helps prioritize improvement opportunities by identifying and addressing the most impactful issues. The method involves focusing on the 20% of causes that result in 80% of the problems. This directs efforts where they will have the most significant impact.
The key steps in using Pareto Analysis are:
- Gathering relevant data.
- Categorizing and prioritizing problems.
- Identifying the vital few issues to address.
- Implementing solutions.
- Tracking the outcomes.
When integrated into the Kaizen methodology for continuous improvement, Pareto Analysis makes the issues easier to understand and guides organizations to make data-driven decisions. By incorporating Pareto Analysis into the Kaizen cycle, organizations can target critical areas for change and allocate resources effectively.
Observation in Action: The Gemba Walk
The Gemba Walk helps managers see the workplace firsthand, to understand daily operations. It aligns with Kaizen principles by involving all staff in continuous improvement. By being on the production floor, leaders can spot improvement opportunities and waste sources. Observation in the Gemba Walk gives key insights into production and processes. It helps identify areas for improvement. Understanding how work is done contributes to the continuous improvement process of Kaizen.
This allows management to implement small changes that boost productivity and efficiency.
Preventing Errors with Poka-Yoke
Poka-Yoke, also known as mistake proofing, focuses on preventing errors before they happen. It involves designing processes or equipment to stop mistakes from occurring.
To implement Poka-Yoke effectively, employees should concentrate on improving processes and preventing errors, rather than just finding and fixing them. By embedding Poka-Yoke principles in the organization’s culture, employees can pinpoint and remove errors at the source, leading to ongoing improvement and higher quality.
When implementing Poka-Yoke in a continuous improvement approach, it’s important to avoid some common pitfalls. These include overlooking the human element in processes, not involving employees in the mistake-proofing process, and failing to standardize processes to prevent errors across the organization.
Successful implementation of Poka-Yoke involves recognizing the need for a systematic approach to error prevention and involving employees at all levels in the continuous improvement process.
Kaizen Applications and Best Practices
Applying Kaizen in Healthcare
Kaizen can benefit healthcare by improving care quality, patient safety, and operational efficiency. To foster a Kaizen mindset, organizations can promote open communication, collaboration, and continuous improvement training. Building a diverse Kaizen team involves professionals from different departments. Effective strategies include regular process reviews, encouraging staff to spot improvement opportunities, testing small changes, and measuring their impact.
Prioritizing patient care and safety can establish a culture of continuous improvement through Kaizen.
Kaizen in Office Settings
Implementing Kaizen in office settings for continuous improvement is achieved by involving all employees. This includes full support and participation from leadership and management. One effective strategy is to start with training with outside trainers, to gain an objective view of the organization’s needs. It’s important to think small and not chase perfection to support Kaizen from the top.
Questioning current practices, fostering idea generation, removing barriers, recognizing success, and measuring impacts are all essential. Embracing the Kaizen mindset brings improved quality, reduced costs, more effective management, increased safety, and improved morale in an office environment. Kaizen fosters a culture of slow, gradual, and incremental change for efficiency and removing waste.
Service Industry and Kaizen: A Symbiotic Relationship
Embracing Kaizen in the service industry has many advantages. It can improve quality, shorten delivery times, reduce costs, manage more effectively, increase safety, and boost morale. This can lead to increased customer satisfaction and loyalty, which are important in the service industry.
To cultivate a Kaizen mindset, organizations can assemble a diverse Kaizen team made up of employees from all levels and departments. It’s important to encourage a mix of perspectives, experiences, and talents to understand organizational processes and engage all team members actively.
Maintaining Kaizen momentum involves involving everyone in the improvement process, prioritizing data tracking, encouraging personal process checks by management, and implementing changes through a structured process. Recognizing and celebrating small wins is also crucial for sustaining motivation and engagement.
Avoiding Common Pitfalls in Kaizen
The Importance of Leadership Commitment
Leadership plays a significant role in making Kaizen successful in an organization. When leaders actively support and participate in the Kaizen process, it shows employees that continuous improvement is important. This commitment motivates employees to get involved and encourages a culture of improvement. On the flip side, if leaders aren’t committed to Kaizen, it can result in disengagement and doubt among employees, which hampers the process.
To show commitment, leaders can join training programs, engage in improvement discussions, and provide resources for employee-led initiatives. Recognizing and praising employees’ efforts in implementing Kaizen also reinforces leadership commitment and encourages more participation.
Beyond Immediate Results: Long-term Focus
To cultivate a long-term focus beyond immediate results when implementing Kaizen and continuous improvement, organizations must:
- Involve everyone in the process
- Encourage personal process checks by management
- Prioritize data tracking
It’s important to prioritize employee involvement, as each member of the organization can contribute unique perspectives and ideas for improvement. Personal process checks by management can ensure that all levels are engaged and committed to the continuous improvement process. Additionally, data tracking allows organizations to measure the impact of their changes over time, providing insight into which processes are working and where further improvement is needed.
Maintaining momentum and optimizing Kaizen through digital solutions in the long-term involves involving everyone from leadership to frontline workers and ensuring that the process of continuous improvement is supported at all levels of the organization.
To maintain a long-term focus on improvement and success, organizations should avoid common pitfalls such as:
- Not chasing perfection
- Fostering a culture of open communication and idea sharing
- Recognizing success
It’s essential to embrace the concept that perfection can be the enemy of progress, and that fostering open communication and recognizing success can contribute to maintaining momentum and long-term focus on improvement and success.
Maintaining the Momentum of Kaizen
Implementing Kaizen in an organization requires ongoing training, encouraging employee input, and promoting collaboration between departments.
Leadership can sustain Kaizen by acknowledging achievements, promoting teamwork, and tracking data for measurement. While technology can enhance progress, it’s clear that Kaizen is about gradual change and cultural shift, not just technology.
Optimizing Kaizen through Digital Solutions
Using digital tools like project management software, workflow automation, and real-time data analytics can greatly improve Kaizen in an organization. These tools help track progress, manage tasks, gather feedback, and provide insights for process improvement.
Digital solutions also make data collection and analysis easier by automating collection and offering advanced analytics. They help with communication and collaboration among Kaizen teams through digital dashboards, online forums, and collaborative platforms, allowing employees from different departments to share ideas, provide feedback, and work together.
Moreover, digital solutions enable remote access and real-time updates to ensure all team members have the most up-to-date information and can contribute effectively to the improvement process.
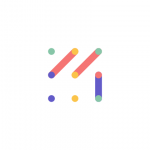
Vizologi is a revolutionary AI-generated business strategy tool that offers its users access to advanced features to create and refine start-up ideas quickly.
It generates limitless business ideas, gains insights on markets and competitors, and automates business plan creation.