Key Steps for 5S Accountability Success
Are you looking to improve organization and efficiency in your workplace? The 5S accountability method might be the solution you’ve been searching for.
By implementing these key steps, you can create a more structured and productive environment for your team. Each step plays a unique role in ensuring success, from sorting to standardizing.
In this article, we’ll explore the essential components of 5S accountability and how they can benefit your organization. Let’s dive in and discover the steps to achieving 5S success.
Understanding the 5S System
Key Principles Behind the 5S Methodology
The 5S methodology is based on five core principles. These are: Sort, Set in Order, Shine, Standardize, and Sustain. These principles help to make workspaces more efficient.
Each principle plays a role in making the workplace better. For example, Sort separates necessary items from unnecessary ones. Set in Order gives each item a specific place. Shine promotes cleanliness. Standardize sets clear procedures. And Sustain makes sure the changes become part of the company culture.
All of this has a big impact on manufacturing and organization. The 5S framework encourages efficiency, safety, and continuous improvement.
Implementing the 5S system has many advantages. It reduces waste and downtime, makes workspaces more productive, improves quality, and organizes the workplace visually.
This shows how important the 5S methodology is for reducing waste and creating a culture of ongoing improvement.
Translation and Significance of 5S Terms
The translation of 5S terms includes Sort, Set in Order, Shine, Standardize, and Sustain. These principles aim to create efficient work areas by separating necessary items from unnecessary ones. They help reduce waste, downtime, and encourage continuous improvement in the workplace.
Understanding the significance of 5S terms is crucial because they contribute to the overall effectiveness of the methodology. The Straighten principle ensures that every item has a specific home, reducing waste from excess motion and enabling employees to easily find what they need.
The Impact of 5S on Manufacturing and Organization
Implementing the 5S framework in manufacturing and organization provides five important advantages.
First, it reduces waste and downtime by sorting items and distinguishing between necessary and unnecessary ones, creating more productive workspaces.
Second, it ensures every item has a specific home, reducing waste through excess motion.
Third, the framework enhances workplace safety and organization by setting clear and easy-to-follow guidelines for item placement and designated areas.
Fourth, it standardizes procedures, reducing time spent looking for items and improving overall workflow.
Fifth, the 5S framework promotes continuous improvement by creating a culture of accountability and responsibility.
Crucial Advantages of Implementing the 5S Framework
The 5S framework has important benefits in a workplace. It reduces waste and downtime, creating a more productive workspace. This framework also impacts manufacturing and organizational efficiency. It helps with lean manufacturing processes, reduces waste, and encourages continuous improvement. The 5S steps reinforce workplace safety. They ensure every item has a specific home, reduce excess motion, and improve work area effectiveness and cleanliness.
Executing the First Pillar: Sort (Seiri)
Defining Sort Within the 5S Framework
Sorting within the 5S framework involves separating necessary items from unnecessary ones to create a more productive workspace.
According to the 5S methodology, Sort is necessary in the workplace to not only reduce waste and downtime but also to ensure that every item has a specific home, which ultimately reduces waste from excess motion.
Effective procedures for implementing Sort within the 5S Framework include:
- Developing a systematic and standardized approach to regularly discard unnecessary items.
- Setting clear criteria for what should stay and what should go.
- Establishing a structured system for organizing and storing necessary items to maximize productivity and efficiency in the workplace.
The Necessity of Sort in the Workplace
Sort (Seiri) is important in the workplace. It separates necessary items from unnecessary ones, creating a more productive workspace. It is essential for lean manufacturing processes and Total Productive Maintenance (TPM) since it reduces waste and downtime. To implement sort effectively, one should first identify necessary items and discard any unnecessary ones.
The principle of “a place for everything and everything in its place” should be followed to ensure that each item has a specific home, reducing excess motion and keeping the workspace organized. The 5S system enhances workplace safety and organization through the principles of sort by reducing the risk of accidents and injuries caused by clutter and disorganization. It also allows employees to easily locate tools and materials, promoting a safer work environment and ensuring smooth operations.
Procedures for Implementing Sort Effectively
To effectively implement the Sort pillar in the 5S framework, organizations should follow step-by-step procedures.
First, they need to identify all items in the workspace and categorize them according to their necessity. Unnecessary items should be removed from the workspace and stored in a different area, ensuring that only essential items remain.
This will help create a more focused and organized workspace. Additionally, it’s crucial to involve all employees in the Sort process to ensure full participation and allow them to contribute ideas on how to improve the organization of the workspace.
This not only maximizes efficiency but also fosters a sense of ownership and accountability among employees.
It’s also important for organizations to regularly revisit the Sort process to maintain its effectiveness and address any new changes in the workspace.
By aligning the Sort (Seiri) process with the overall goals of the 5S methodology, organizations can create a work environment that promotes productivity, waste reduction, and continuous improvement.
Actualizing the Second Pillar: Straighten (Seiton)
Understanding the Concept of Straighten
The 5S framework includes the concept of straightening. It’s about organizing the workplace so that everything has a specific place. This makes it easier for employees to find and return items during their work processes.
Understanding straightening is important for implementing 5S effectively. It promotes workplace organization and efficiency. When everything has a designated place, employees can quickly locate items and reduce wasted time searching for tools or materials.
Effective straightening involves labeling storage areas, creating visual management systems like floor marking for tool storage, and maintaining a clean and clutter-free workplace. These strategies ensure that items are easily accessible, simplify workflows, and contribute to the overall success of the 5S accountability framework.
Strategies for Effective Straightening
Straightening is about organizing items in a specific home. This reduces waste from excess motion and makes the workspace more productive. To make it successful, organizations can use visual cues like color-coding, labels, and shadow boards. These help in recognizing the correct tools and equipment location. It also promotes a sense of responsibility and makes missing items immediately apparent.
Effective straightening in the 5S methodology involves creating a system for proper item placement, organizing and labeling the workplace, and establishing clear responsibilities and expectations for maintaining cleanliness and orderliness. Periodic audits can also be used to observe whether the system is being followed and to identify areas for improvement or additional training.
Polishing the Third Pillar: Shine (Seisou)
Exploring the Role of Shine in Maintenance
Shine is important in the 5S framework. It focuses on keeping tools and the work environment clean and well-maintained. Clean equipment and work areas help employees spot problems easily and keep things organized.
For example, cleaning machinery regularly not only makes it last longer but also reduces breakdowns, leading to less downtime and higher productivity. A tidy workspace also has a psychological benefit, promoting a sense of order and dedication to quality.
To implement shine in the 5S process, it’s best to create a schedule for daily cleaning and regular inspections. This makes maintaining shine a regular part of the routine and keeps the workplace visually organized and efficient. Prioritizing shine in the 5S approach encourages a proactive problem-solving mindset and motivates employees to take responsibility for their work areas.
Best Practices for Shine Implementation
Effective implementation of the Shine (Seisou) pillar in the 5S framework emphasizes the importance of cleanliness and organization in the workplace.
Organizations can ensure this by:
- Developing strategic plans and procedures, like daily and weekly cleaning schedules
- Assigning responsibilities for cleanliness
- Conducting routine inspections and audits
- Using visual management tools, such as color-coding and shadow boards
- Providing adequate training and resources for employees
- Using supply replenishment tools like Kanban cards to guarantee availability of cleaning materials
Regular assessment and feedback can help identify areas for improvement, contributing to continuous improvement. These practices, along with sustained efforts, can lead to successful Shine implementation and maintenance, creating a standardized and efficient work environment.
Harmonizing with the Fourth Pillar: Standardize (Seiketsu)
Defining Standardization in the 5S Process
Standardization in the 5S process means having consistent protocols and practices for an organized and efficient workspace.
It involves creating uniform procedures for labeling and storing items. Also, defining cleaning schedules and quality control checks is important.
For example, in a factory, color-coded bins and shadow boards can be used to ensure tools and materials are always in their designated locations, promoting a cleaner and more efficient work environment.
Standardized protocols can be developed and implemented through comprehensive training programs. These programs educate employees on specific procedures and expectations for maintaining an organized workspace.
Regular audits and performance reviews can ensure that standardization procedures are followed and identify areas for improvement.
The key principles and significance of standardization in the 5S methodology include reducing waste and downtime, promoting workplace safety, and fostering a culture of continuous improvement.
By standardizing work practices, companies can increase operational efficiency and productivity. Also, it can improve employee morale and job satisfaction.
Developing Standardize Protocols
Developing standardized protocols for the successful implementation of the 5S framework requires careful consideration of each pillar. It’s important to have protocols for Sort, Set in Order, Shine, and Straighten. These help companies maintain a clutter-free, organized, and clean workspace.
For example, creating standard protocols for the Sort pillar involves clearly defining necessary items and what can be discarded or moved. Protocols for Set in Order need to establish specific spaces for each item to prevent wasted time searching for tools or materials. Best practices for creating and implementing standardized protocols include involving employees in the process, providing clear instructions, and regularly reviewing and updating protocols. By focusing on standardizing protocols for each aspect of the 5S methodology, companies can better support the sustainability of 5S in the workplace and foster a culture of continuous improvement.
Maintaining the Fifth Pillar: Sustain (Shitsuke)
The Importance of Sustain in Continuous Improvement
The 5S methodology consists of Sort, Set in Order, Shine, and Standardize principles. Sustain is crucial in maintaining the progress achieved through these steps. It ensures that the work environment stays organized, clean, and efficient for long-term success. Employees’ sustained efforts in upholding 5S principles foster a culture of continuous improvement, leading to higher productivity and engagement.
Additionally, the 5S elements enhance workplace safety by reducing accidents and injuries. Sustain plays a critical role in reinforcing safety by consistently following safety protocols and addressing hazard areas. It ensures that safety standards remain high. Through its unwavering commitment to continuous improvement, Sustain ensures that the benefits of the 5S methodology are perpetually realized, leading to increased productivity, safety, and operational efficiency.
Ensuring Long-Term Success with Sustain
One way organizations can ensure long-term success with the sustain pillar of the 5S framework is by consistently enforcing the principles of Sort, Set in Order, and Shine.
This involves maintaining a clutter-free and organized workplace, which promotes safety, efficiency, and productivity.
Regular audits and inspections can be conducted to ensure that the standards set by the sustain pillar are being adhered to and that improvements are made over time.
Furthermore, providing ongoing training and education to employees about the importance of sustaining a clean and organized work environment can lead to greater buy-in and commitment to the principles of the sustain pillar.
Reinforcing Safety through the 5S Steps
How 5S Elements Enhance Workplace Safety
The 5S framework enhances workplace safety through specific elements.
- “Sort” involves removing unnecessary items, reducing clutter, and minimizing the risk of accidents.
- “Straighten” ensures each item has a designated place, preventing obstacles and reducing tripping incidents.
- “Shine” involves keeping the work area clean and organized, promoting a hazard-free environment.
Implementing 5S improves safety protocols by establishing standardized procedures and reducing hazards. This promotes a culture of safety and prevention, impacting the overall safety culture within an organization. Employees become more conscious of safety hazards and take ownership of maintaining a safe work environment, contributing to enhanced safety organization-wide.
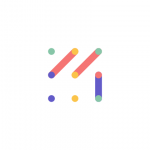
Vizologi is a revolutionary AI-generated business strategy tool that offers its users access to advanced features to create and refine start-up ideas quickly.
It generates limitless business ideas, gains insights on markets and competitors, and automates business plan creation.