Your Simple 5S Action Plan Guide
Are you ready to improve your organization’s efficiency and productivity? If so, it’s time to implement the 5S Action Plan. This system is designed to streamline your workplace, reduce waste, and improve overall organization. In this guide, we’ll walk you through the five key steps of the 5S Action Plan and provide practical tips for implementation.
Whether you work in a factory, office, or any other environment, this guide will help you achieve greater effectiveness in your day-to-day operations.
Understanding the 5S Framework
Origins and Definition of 5S
The 5S framework started in Japan and was developed by Toyota. It’s used for organizing workplaces and has been adopted globally by various industries.
5S consists of Sort, Set in Order, Shine, Standardise, and Sustain principles.
- Sort phase: Remove unnecessary items.
- Set in Order phase: Organize necessary items.
- Shine phase: Emphasize cleanliness and regular maintenance.
- Standardise: Establish consistent practices.
- Sustain: Maintain discipline to sustain improvements.
Understanding 5S’ origins and definition before implementing it in a workplace is crucial. This ensures proper application and maximizes benefits like improved organization, efficiency, safety, and productivity.
Critical Importance of 5S in Boosting Productivity
Implementing a 5S program can enhance workplace productivity and efficiency. It involves organizing the workspace, keeping it clean, reducing waste, and preventing equipment breakdowns.
Benefits of the 5S framework include improved workplace organization, efficiency, safety, increased productivity, better resource utilization, and reduced employee frustration and stress.
Additionally, implementing 5S can lead to reduced waste and cost savings by minimizing operational costs, preventing equipment failures, and reducing work site accidents.
Exposition on the 5 Phases of 5S
First ‘S’: Sorting Out the Unnecessary (Seiri)
In the Sorting Out the Unnecessary (Seiri) phase of 5S, there are steps to effectively sort workplace items.
- Separate the necessary items from the unnecessary ones.
- Remove the unnecessary items from the work area.
- Clearly mark the location of the necessary items.
Real-world applications can illustrate this by organizing tools and materials in a manufacturing setting. This can streamline production processes and reduce time spent searching for items.
In the Shine phase, workplace cleanliness can be ensured by:
- Conducting regular cleaning activities.
- Inspecting the work environment for dirt and debris.
- Completing tasks like sweeping, dusting, and lubricating equipment.
Best practices include developing a cleaning schedule, setting cleanliness standards, and engaging employees in maintaining a clean and organized workspace. Reiterating the importance of cleanliness and demonstrating its impact on workplace safety, equipment efficiency, and employee morale also contribute to successful implementation of the Shine phase.
Steps to Effectively Sort Workplace Items
To effectively sort workplace items according to the 5S framework, there are essential steps to follow. These include decluttering, establishing a system of order for all necessary items, and ensuring each tool or equipment has a specific designated location. Additionally, it’s important to remove unnecessary items.
Real-world applications of sorting can help improve workplace organization and efficiency. This is done by reducing wasted time and effort spent searching for misplaced items, streamlining processes due to readily available tools and materials, and minimizing the risk of workplace accidents due to improperly stored or discarded items.
Some examples of effective sorting strategies in a work environment include using color-coded labels for item locations and categories, implementing shadow boards to outline tool placement, and establishing clear identification and disposal procedures for obsolete or redundant items.
Real-world Applications of Sorting
Sorting has improved workplace efficiency and productivity. It organizes the workspace, making tools and equipment easier to find. This has led to cost savings and waste minimization in various industries, as it reduces time spent searching for items and eliminates clutter. In real-world applications, sorting has contributed to enhanced workplace safety and reduced equipment maintenance.
It minimizes workplace hazards like tripping and prevents equipment breakdowns due to cleanliness and proactive upkeep.
Second ‘S’: Setting in Order (Seiton)
Strategies for efficient arrangement in the “Second ‘S’: Setting in Order (Seiton)” phase of the 5S framework include:
- Defining the optimal location for tools, equipment, and materials.
- Using labels and color-coding to clearly identify items.
- Establishing clear visual indicators, such as outlines, to show where items belong.
Effective straightening examples include:
- Using clear containers and storage cabinets to separate and organize items.
- Utilizing shadow boards to keep tools in their designated location.
- Arranging workstations in a user-friendly layout to minimize wasted motion and time.
The “Second ‘S’: Setting in Order (Seiton)” phase contributes to the overall efficiency and productivity of the workplace by:
- Reducing the time spent searching for tools and materials.
- Streamlining workflow and processes.
- Minimizing the risk of errors or accidents due to misplaced items.
Additionally, an organized workspace can improve employee morale and satisfaction, leading to increased productivity and quality of work.
Strategies for Efficient Arrangement
Efficient arrangement in the workplace, part of the “Set in Order” phase of the 5S framework, involves labeling and organizing tools, equipment, and materials in designated locations. Visual management tools like color-coded labels, shadow boards, and floor markings help employees identify and retrieve items quickly. Ergonomic storage solutions like bins, cabinets, and shelves optimize layout and item accessibility, reducing wasted time and movement.
To build a culture of consistency and commitment, companies can establish regular training programs and workshops to educate employees on 5S principles. Encouraging employee involvement in decision-making and process improvement fosters ownership and accountability. Recognizing and rewarding employees who demonstrate continuous improvement and adherence to 5S principles reinforces the value of efficient arrangement.
Real-world examples of successful implementation of efficient arrangement include streamlined assembly lines in manufacturing facilities, organized inventory and optimized storage space in warehouses, and improved patient safety and treatment accuracy in healthcare facilities. These examples demonstrate the practical benefits of implementing efficient arrangement within the 5S framework.
Examples of Effective Straightening
Straightening in the workplace involves organizing tools and materials for efficiency, reducing errors, and minimizing wasted time. For instance, arranging workstations logically can streamline workflow and improve productivity. Color-coding and labeling items can make it easier for employees to find what they need, reducing search time and mistakes.
Implementing shadow boards or tool cribs can further enhance organization by providing designated spots for each tool or item, promoting a tidy and systematic workspace.
This can contribute to the success of a 5S program by promoting a clean, organized, and efficient work environment. It reduces workplace accidents, minimizes equipment downtime, and enhances operational efficiency, leading to increased productivity, reduced frustration and stress among employees, and lower operational costs.
To ensure effective implementation, strategies such as regular training on 5S principles, clear communication, ongoing evaluation and improvement processes, and reinforcement of 5S standards can be utilized. Creating a culture of continuous improvement and employee involvement in the 5S program can help sustain the effectiveness of straightening efforts.
Third ‘S’: Shining the Work Area (Seiso)
One way to keep the workplace clean in the “Shining the Work Area (Seiso)” phase is to do regular inspections. These inspections help find and fix dirt, dust, and leaks. Cleaning tasks may include sweeping the floor, taking out the trash, and wiping down equipment. Employees should keep their workstations and tools clean, and managers should communicate and use visual aids to reinforce cleanliness standards.
In real workplaces, successful “Shine” phase examples involve regular inspections to find cleanliness and safety issues. Organizations can also create clear cleaning rules and involve all employees in keeping the workplace clean. By raising cleanliness standards, organizations can reduce safety risks, improve equipment efficiency, and boost employee morale.
Advantages of the “Shining the Work Area (Seiso)” phase of the 5S program include better equipment efficiency, lower safety risks, and higher employee morale. A clean work environment can also reduce employee frustration and stress, leading to higher productivity and overall workplace efficiency.
Best Practices for Ensuring Workplace Cleanliness
One of the best practices for workplace cleanliness in the “Shining the Work Area” phase of the 5S framework is to embrace 5S shine as more than just a quick sweep of the workplace. This phase involves a full clean, inspection, and lubrication of the entire plant. It’s important to take photographs to document the before and after, which reinforces the value of ongoing 5S efforts and identifies areas for improvement.
In the “Sustaining the Discipline” phase of the 5S framework, a culture of consistency and commitment can be built by reviewing and resolving any outstanding action items from previous phases, and by encouraging continuous improvement. It’s crucial to regularly take an inventory of what went well and areas of improvement for the next round of 5S Days. Instilling the understanding that the process should be a never-ending cycle is also important.
When developing uniform standards in the “Standardizing Processes” phase of the 5S framework, guidelines to follow include implementing tools like Kanban Systems and Visual Management Boards to sustain the 5S methodology.
Additionally, integrating 5S into the organization’s culture and routine processes is essential for promoting teamwork, shared dedication, and improved organizational performance.
Examples Demonstrating the Shine Phase
Organizations can demonstrate the shine phase by ensuring cleanliness and order in the workplace with a 5S program. They can achieve this by conducting regular deep cleaning and inspection activities to address potential safety hazards like oil spills and debris accumulation.
Best practices for maintaining workplace cleanliness include daily cleaning routines, visual management tools to ensure cleanliness standards, and providing training to employees on proper cleaning procedures.
Real-world examples of successful implementation of the shine phase include automotive manufacturing plants implementing daily cleaning schedules and food processing facilities conducting regular equipment lubrication and maintenance.
The shine phase of the 5S framework is essential for creating a clean, safe, and efficient workplace.
Fourth ‘S’: Standardizing Processes (Seiketsu)
To establish consistent standards for the Fourth ‘S’, it’s important to set best practices for maintaining cleanliness and organization in the workplace.
Standardizing Processes (Seiketsu) involves creating written guidelines and checklists for routine tasks. It also includes regular audits to ensure adherence to standards and providing consistent training to employees on cleaning and organizing processes.
Employees should be encouraged to suggest improvements to current procedures and provide regular updates to ensure that the current methods and tools are being used effectively.
For the Fifth ‘S’ phase, Sustaining the Discipline (Shitsuke), it’s important to cultivate a culture of consistency and commitment.
This can be achieved by creating a sense of accountability through regular performance evaluations and recognition of employees who consistently adhere to 5S principles.
Leadership should encourage open communication and feedback mechanisms to address any challenges to sustaining the 5S methodology.
Integrating 5S principles into everyday work routines and processes will ensure that employees understand it’s a long-term commitment towards continuous improvement and efficiency. Regular training sessions and performance reviews will provide continuous support and reinforcement of the 5S culture.
Guidelines to Develop Uniform Standards
Organizations should prioritize:
- Proper labeling and identification practices
- Consistent storage and tool placements
- Cleaning and inspection schedules
- Visual controls that signal when standards are not met
Consistency and commitment in adhering to uniform standards are ensured through:
- Regular audits
- Employee training
- Ongoing engagement to instill the importance of maintaining established standards
Additionally, creating a system to manage and share best practices, success stories, and problem-solving techniques establishes a culture of continuous improvement and encourages overall commitment to standardizing processes.
Fifth ‘S’: Sustaining the Discipline (Shitsuke)
The best practices for cultivating a culture of consistency and commitment in the Fifth ‘S’ phase, Sustaining the Discipline , include:
- Conducting regular audits to monitor progress.
- Providing ongoing training and education to employees.
- Establishing clear expectations and accountability measures.
Success stories demonstrating the effectiveness of sustaining the discipline in the workplace can be found in companies that have experienced:
- Decreased equipment failures.
- Improved operational efficiency.
- Reduced workplace accidents as a result of implementing a 5S program.
To ensure that the Fifth ‘S’, Sustaining the Discipline (Shitsuke), is integrated into the overall 5S program, a company can:
- Establish standard operating procedures.
- Create visual management tools such as daily checklists and performance boards.
- Regularly communicate the importance of sustaining the program to all employees.
Cultivating a Culture of Consistency and Commitment
A company can create a consistent and committed workplace culture by using a 5S program. This program includes sorting, setting things in order, shining, standardizing, and sustaining cleanliness and organization.
To make this work, the company needs to do regular training, clearly communicate expectations, and provide resources for standardized processes.
Successful companies in the manufacturing industry have used the 5S program. They have focused on cleanliness, safety, and efficiency, leading to better productivity and morale.
By integrating 5S principles into daily operations and encouraging continuous improvement, these companies have built a culture of consistency and commitment. This has helped them achieve long-term success and sustainable growth.
Sustain: Best Practices and Success Stories
Here are some best practices for a successful 5S program:
- Organize the workspace
- Maintain cleanliness
- Reduce waste
- Integrate safety as the 6th “S” in Lean
Successful organizations have benefited from the 5S framework by:
- Improving workplace organization and efficiency
- Increasing productivity
- Utilizing resources better
Implementing 5S has:
- Reduced operational costs
- Minimized work site accidents
- Prevented equipment failures
- Decreased employee frustration and stress
Top Advantages of Implementing a 5S Program
Raised Efficiency and Improved Productivity
Implementing a 5S program can make a workplace more efficient and productive. It does this by organizing the workspace, keeping it clean, and reducing waste. This helps prevent equipment breakdowns, reduces accidents, and minimizes employee frustration and stress. The 5S framework also promotes teamwork, dedication, and organizational performance. Together, these factors improve efficiency and productivity in the workplace.
Minimization of Waste and Cost Savings
Implementing a 5S program helps minimize waste and save costs. It does this by promoting workplace organization, cleanliness, and waste reduction. The program operates on the principles of Sort, Set in Order, Shine, Standardize, and Sustain, leading to improved operational efficiency, reduced downtime, and prevention of equipment failures.
Visual management boards and Kanban Systems aid in maintaining the 5S framework and ensuring effective resource utilization, ultimately reducing waste and improving productivity.
Incorporating a 5S program brings several benefits, including reduced operational costs, prevention of equipment failures, minimized work site accidents, improved efficiency, and increased productivity. Employees also experience reduced stress and frustration, creating a positive work environment. The implementation costs are minimal, mainly involving employee training and periodic audits, making it a cost-effective approach to minimizing waste and achieving cost savings in the workplace.
Enhanced Safety and Reduction of Workplace Accidents
Implementing a 5S program can make the workplace safer. It promotes a clean, organized, and efficient work environment. This helps reduce the risk of accidents and equipment breakdowns. It also minimizes employee frustration and stress. Here are some of the benefits of a 5S program: minimal implementation costs, improved efficiency and productivity, and prevention of equipment breakdowns.
The 5S framework establishes standardized workspaces and processes, makes necessary items easily accessible, and promotes a culture of cleanliness. This helps in maintaining a safe workplace.
Lower Equipment Maintenance and Fewer Breakdowns
Implementing a 5S program can help lower equipment maintenance and reduce breakdowns. It promotes a cleaner and more organized work environment. By following the principles of Shine and Standardise, companies can ensure that workspaces are regularly cleaned, inspected, and maintained. This helps prevent equipment failures caused by dirt, dust, or leaked fluids. The 5S program also encourages employees to take ownership of their work areas, leading to improved equipment care and reduced wear and tear. Best practices within the 5S framework for minimizing equipment maintenance and reducing breakdowns include:
- Regular cleaning and inspection of equipment
- Using visual management tools to monitor equipment condition
- Establishing standardized maintenance procedures
- Ongoing employee training
- Periodic audits to ensure consistent adherence to 5S practices
These efforts ultimately contribute to lower equipment maintenance and fewer breakdowns.
Lessened Employee Frustration Through Streamlined Operations
Implementing a 5S program can help make work easier for employees and reduce frustration. It does this by organizing the workspace, maintaining cleanliness, and reducing waste. This makes it easier for employees to find items and complete their tasks, leading to improved efficiency and productivity.
Additionally, it prevents equipment breakdowns and work site accidents, reducing operational costs with minimal implementation costs.
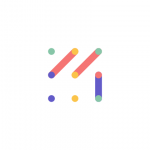
Vizologi is a revolutionary AI-generated business strategy tool that offers its users access to advanced features to create and refine start-up ideas quickly.
It generates limitless business ideas, gains insights on markets and competitors, and automates business plan creation.