Must-Have Lean Management Tools
Lean management is important for businesses. It helps to streamline processes and improve efficiency. However, choosing the right tools can be overwhelming. There are many options, such as value stream mapping and 5S methodology. It’s important to find the tools that best fit your business needs.
In this article, we’ll look at some essential lean management tools that can benefit your organization. Whether you’re experienced in lean management or new to it, these tools can optimize your operations and boost productivity.
Essential Principles of Lean Management
The Focus on Value
Value is very important in Lean Management. It helps the organization focus on delivering what the customer truly values. Lean tools like Value Stream Mapping and Just-In-Time (JIT) can streamline processes and create more efficient workflows by identifying value and eliminating waste. By implementing Value Stream Mapping, companies can visualize their processes, identify value-adding steps, and remove non-value-adding activities, leading to a more focused approach on value.
Similarly, JIT ensures that products are produced only as needed, reducing excess inventory and aligning production with actual customer demand. This strategic alignment between the implementation of lean tools and the focus on value drives operational excellence, allowing businesses to optimize their operations and deliver increased value to their customers while staying efficient and competitive in the market.
Mapping the Value Stream
Value stream mapping is a part of Lean management. It focuses on visualizing the entire process from start to finish. It helps companies understand how to create value for their customers and where there is waste in the process by identifying all the steps involved in delivering a product or service, as well as the flow of information and materials.
For example, a manufacturing company might use value stream mapping to identify unnecessary movement of materials on the factory floor. A service company might use it to find steps in their process that do not add value for the customer.
Value stream mapping is useful in identifying and eliminating waste. It allows companies to see the entire process in one view, facilitating the identification of bottlenecks, overproduction, waiting time, and transportation waste. By making waste visible, companies can prioritize areas for improvement, leading to more efficient and streamlined processes that benefit both the company and the end customer.
The benefits of using value stream mapping in lean management are numerous. It helps to improve efficiency by identifying non-value-added activities that can be eliminated, reduces lead time, and improves communication and collaboration across different departments. Ultimately, value stream mapping enables companies to continuously improve their processes, reduce costs, and deliver higher quality products and services to their customers.
For example, a healthcare organization might use value stream mapping to improve patient care processes, while a software company might use it to streamline their development process.
Ensuring Continuous Workflow
Companies can use lean management tools to maintain a continuous workflow and maximize efficiency. These tools include 5S, Bottleneck Analysis, Just-In-Time, and Plan-Do-Check-Act (PDCA). They help streamline workflow processes by identifying waste, standardizing work procedures, and improving operations.
With these strategies, organizations can proactively address potential obstacles that may disrupt workflow. For instance, Bottleneck Analysis identifies areas of congestion, allowing for timely intervention to prevent delays. Just-In-Time and PDCA facilitate an agile and adaptive approach to implementing changes and improvements continuously.
By using these lean management tools, companies can achieve a consistent and efficient workflow, promoting continuous improvement and enhancing overall productivity.
Implementing a Pull System
Implementing a Pull System requires several steps for success.
First, a company needs to establish reliable demand forecasting to understand customer needs and variations in product demand.
Businesses can efficiently manage inventory levels and reduce waste by using tools such as JIT inventory management and Kanban.
Creating clear communication channels among different departments and suppliers is essential for the smooth flow of materials and information.
Continuous monitoring of production and customer demand is crucial. This involves tracking lead times, throughput times, and cycle times to optimize production processes and minimize inventory.
Developing a culture of continuous improvement and employee involvement is also important to ensure the sustained effectiveness of the Pull System.
Key considerations for implementing a Pull System involve aligning production with customer demand, reducing excess inventory and associated costs, and fostering a lean and responsive production environment.
The integration of the Pull System can lead to increased flexibility, minimized waste, and enhanced customer satisfaction.
Pursuing Continuous Improvement
Organizations can ensure consistent identification and implementation of improvement opportunities by using lean management tools. These tools include Kaizen, PDCA, and Value Stream Mapping. They help teams analyze processes, find inefficiencies, and create action plans for improvement.
By promoting a culture of continuous improvement, organizations can involve employees in problem-solving and innovation. This can be achieved through regular training on lean principles, empowering employees to suggest and implement improvements, and recognizing successful initiatives to maintain momentum.
The concept of Kaizen, which focuses on small, incremental changes, can be integrated into business operations. Frontline workers can identify and address issues in their daily work, and these principles can be applied at all levels of the organization. This can lead to improved productivity, efficient resource usage, and better business processes overall.
Core Lean Tools for Process Enhancement
Systematic Organization with 5S
The 5S method helps organize a workplace by promoting order, cleanliness, and standardization.
The five key components – Sort, Set in Order, Shine, Standardize, and Sustain – contribute to lean management by eliminating waste and reducing the time needed to locate items.
This method creates a visual workplace that enhances efficiency and supports continuous improvement in a business.
5S fosters a sense of ownership and pride among employees, increasing their engagement in maintaining a well-organized and efficient work environment.
Enabling Flexible Processes through SMED
Implementing SMED (Single-Minute Exchange of Die) can greatly improve processes in an organization. It does this by reducing changeover time and making operations more efficient.
SMED focuses on identifying and separating internal and external setup tasks. This helps to significantly reduce set-up times, leading to increased equipment use and production flexibility. The key steps of SMED include converting internal setup tasks to external ones, simplifying and standardizing processes, and using parallel activities to reduce changeover time.
Visualizing Processes via Value Stream Mapping (VSM)
Value Stream Mapping (VSM) is a great way to understand processes in an organization. It helps create visual representations of all the steps involved in delivering a product or service. This tool is useful for identifying waste, inefficiencies, and potential problem areas, so targeted improvements can be made. VSM also provides insights into the flow of materials, information, and resources, helping companies understand their current operations better.
Using Value Stream Mapping (VSM) offers many benefits. It helps streamline processes, improve lead times, reduce inventory levels, and enhance productivity. VSM also helps identify bottlenecks and areas for improvement, which can lead to cost reductions and improved quality. By visualizing the entire value stream and processes, companies can make informed decisions and drive sustainable improvements.
Identifying Delays with Bottleneck Analysis
Bottleneck analysis is a helpful tool in lean management. It helps to find delays in a process. The method looks at how work flows. It finds areas where production may slow down or get crowded.
To do bottleneck analysis, you need to look at each step of the process. You also need to figure out how long each step takes. Lastly, you should find any steps where work piles up. This helps businesses find the specific points causing delays. Then they can fix them.
Addressing bottlenecks helps businesses improve their processes. This leads to better efficiency and a steady flow of work. Finding and fixing delays is important for businesses that want to streamline their operations, cut waste, and keep getting better.
Cyclic Methodology with Plan-Do-Check-Act (PDCA)
One of the important lean management tools is the Plan-Do-Check-Act cycle. This methodology contributes to the cyclic nature of lean management. The PDCA cycle involves four stages:
- Planning.
- Implementing the plan.
- Checking the results.
- Acting to make necessary adjustments
For example, in waste reduction, a company can identify areas for improvement, implement changes, assess the outcomes, and then make further adjustments to optimize the process.
The PDCA cycle can be effectively implemented by:
- Encouraging employees to actively participate in all stages
- Engaging in regular reviews to assess progress
- Fostering a culture of continuous improvement
The benefits of using the PDCA methodology within lean management include:
- Enhanced efficiency
- Reduced waste
- Improved quality
- Streamlined processes
By consistently following the PDCA cycle, organizations can ensure that they are constantly refining their operations and striving for ongoing advancement in their processes.
Mitigating Errors with Poka-Yoke Techniques
Poka-Yoke techniques help prevent errors in manufacturing processes and workflows. They incorporate mechanisms to make it impossible for mistakes to occur or make errors immediately noticeable for quick rectification.
For example, designing parts to only assemble in the correct orientation minimizes mistakes. Sensors or alarms can alert operators when errors are made, preventing defects from spreading down the production line. Using fixtures, jigs, and templates during assembly processes ensures correct component positioning and assembly.
Effective implementation involves closely observing and analyzing processes to identify potential error points and designing foolproof prevention methods, like incorporating physical barriers, color coding, or creating user-friendly software interfaces.
Providing operators with proper training and clear work instructions is essential for successful implementation.
In real-world applications, the automotive sector uses sensors and computerized systems to ensure manufacturing equipment operates within specified parameters. The food and beverage industry uses automated quality control systems to detect errors in packaging and labeling, preventing defective products from reaching consumers. These real-world examples highlight the effectiveness of Poka-Yoke in error prevention and quality improvement.
Analyzing Root Causes for Problem Solving
Root cause analysis is an important method in problem-solving. It helps companies dig deep into the underlying issues affecting their operations. Techniques like the 5 Whys and Fishbone Diagrams are commonly used to identify root causes. This helps organizations address the fundamental reasons for inefficiencies or errors. Understanding these root causes helps businesses implement targeted solutions that contribute to overall operational improvement.
For example, identifying a recurring bottleneck through root cause analysis can lead to workflow reorganization, reducing delays and increasing productivity. In the context of lean management, root cause analysis is key in continuous improvement efforts by providing a structured approach to problem-solving. It allows organizations to systematically address issues, optimize processes, and eliminate waste.
For instance, a manufacturing facility using root cause analysis might uncover equipment downtime as a chronic issue, prompting the implementation of preventive maintenance schedules to enhance overall equipment effectiveness.
Creating Uniformity with Standardized Work
Standardized work creates uniformity in processes and operations. It sets clear and consistent procedures for tasks like cycle times, work sequence, and methods. This ensures that all employees perform their duties in the same way, leading to uniformity and consistency.
By eliminating variations in output, standardized work guarantees that every product or service meets quality standards. It includes clear work instructions, visual aids, standardized tools and equipment, and regular training and feedback.
Standardized work reduces errors, waste, and potential production or service delivery issues. It also contributes to continuous improvement and operational excellence. By capturing best practices and implementing them as standard work, organizations achieve greater efficiency, reduced defects, and enhanced productivity. It also promotes a culture of continuous improvement by encouraging employees to suggest and implement improvements.
Advanced Lean Tools for Operational Excellence
Minimizing Waste through Just-in-Time (JIT)
One way to minimize waste in production or service is by using Just-In-Time principles. JIT synchronizes production with customer demand, reducing excess inventory and overproduction. This makes operations leaner and more efficient.
The Kanban system is a key part of JIT. It ensures that components are only delivered as needed, preventing excessive stockpiling. Additionally, JIT encourages continuous improvement and waste reduction through techniques like Kaizen, fostering an environment of efficiency and innovation.
Continuous Improvement with Kaizen
Continuous improvement is important for organizations. They can achieve this by using Kaizen as a core principle. Kaizen encourages small, gradual changes in processes, systems, and employee behaviors, leading to ongoing improvement and efficiency.
For example, a manufacturing company can use Kaizen to review and improve its production line regularly. This can reduce waste and increase productivity over time.
To pursue continuous improvement with Kaizen in lean management, key strategies include fostering a participative and collaborative culture among employees, empowering them to identify and implement improvements, and using visual management techniques to track progress and highlight areas for improvement.
Integrating Kaizen into the business strategy can lead to benefits such as increased employee engagement and motivation, improved customer satisfaction, and reduced costs through waste elimination.
Balancing Workload via Heijunka (Level Scheduling)
Heijunka, also known as Level Scheduling, is a helpful tool for lean manufacturing. It helps to balance the workload and keep the production flowing smoothly.
By using Heijunka, organizations can manage their production processes effectively. This ensures a consistent level of output, without the peaks and valleys that can cause problems.
This method involves smoothing out production schedules by sequencing orders. This keeps the production mix constant and ensures resources are used evenly, promoting stability.
The key principles and techniques for using Heijunka focus on evaluating customer demand. It also involves creating production sequences that match this demand, and deciding on appropriate production quantities.
By doing this, organizations can standardize processes and reduce waste by only producing what is needed when it’s needed. This strategy helps companies balance workloads, minimize inventory, and adjust to changes in production demands.
Heijunka also helps to reduce waste by cutting excess inventory, overproduction, and waiting times. These are often linked to uneven production schedules. Smoothing production helps organizations align their resources with demand, leading to better overall efficiency and resource use.
Automating Quality with Jidoka (Autonomation)
Jidoka (Autonomation) is a concept in lean management. It focuses on automating quality by giving machines the ability to detect and prevent defects in the production process.
Jidoka enables machines to stop themselves when an abnormality occurs, preventing defective products from being produced. This ensures higher-quality output and reduces the need for constant human intervention in the production line.
Businesses can adopt Jidoka by implementing automatic inspection and stopping mechanisms in their manufacturing processes. Additionally, they can train employees to identify and address abnormalities promptly.
By doing so, businesses can improve operational excellence, achieve higher product quality, reduce waste, and enable continuous improvement. This promotes a culture of problem-solving and quality-driven operations, leading to improved efficiency and customer satisfaction.
Using KPIs to Track Performance
KPIs are helpful in lean management. They provide measurable metrics to assess performance and find areas for improvement.
For example, tracking cycle time, inventory turnover, and customer lead time can show process efficiency and reduce waste.
These KPIs help organizations pinpoint bottlenecks, streamline workflows, and boost productivity. They also allow organizations to set specific targets and track progress.
Analyzing KPI data over time helps identify trends and implement measures for improvement.
Using KPIs in a lean framework promotes data-driven decision-making and encourages teams to make informed choices.
Focusing on clear and measurable performance indicators helps lean organizations make systematic and sustainable improvements.
Strengthening Equipment Efficiency with OEE
Overall Equipment Effectiveness (OEE) is a great tool for boosting equipment efficiency. It gives a complete view of equipment performance by measuring factors like availability, performance, and quality. OEE helps find areas for improvement and waste reduction.
For example, tracking downtime can help solve underlying issues and set up preventive maintenance, leading to better equipment use and productivity. Using Lean tools like 5S and Kaizen with OEE can also enhance equipment efficiency. For instance, applying 5S principles can make the work environment more organized and efficient, reducing the time to set up and use equipment. Similarly, continuous improvement through Kaizen can remove non-value-added activities, making equipment more efficient. These strategies match the principles of Total Productive Maintenance (TPM), which aims for proactive and preventive maintenance to achieve optimal equipment performance.
By using these approaches together, organizations can boost equipment efficiency and attain operational excellence.
Optimizing Maintenance with Total Productive Maintenance (TPM)
Total Productive Maintenance can help organizations optimize their maintenance processes. It focuses on preventative and predictive maintenance to reduce downtime and improve equipment effectiveness.
TPM involves machine operators in maintenance tasks, giving them a sense of ownership and responsibility. For instance, operators perform routine upkeep on their machines through autonomous maintenance.
TPM also emphasizes early equipment management to prevent potential breakdowns and continuous improvement in maintenance through clear performance metrics.
By integrating TPM into their strategies, organizations can proactively address equipment maintenance and foster a culture of continuous improvement.
Key Benefits of Utilizing Lean Management Tools
Incorporating lean management tools into an organization’s processes has several primary benefits.
- It eliminates waste, like overproduction, excess inventory, and unnecessary motion.
- Tools like 5S, Kaizen, and Value Stream Mapping help identify and address inefficiencies, leading to streamlined operations, improved productivity, and reduced costs.
- These tools also promote continuous improvement and standardize work processes, contributing to operational efficiency and cost reduction.
- Resource utilization is optimized, lead times and delays are minimized, ultimately enhancing the organization’s bottom line.
Moreover, the use of lean management tools impacts employee engagement and organizational performance.
- It instills a culture of accountability, problem-solving, and collaboration.
- Employees feel empowered to contribute to the company’s success, leading to increased satisfaction, motivation, and overall performance.
- Active engagement in continuous improvement efforts fosters a culture of excellence and drives sustainable results for the organization.
Integrating Lean Tools into Your Business Strategy
The Role of Employee Empowerment
Employee empowerment is important. It gives employees the freedom to make decisions and take ownership of their work. This helps create a culture of continuous improvement and efficiency within organizations. By empowering employees, individuals can find and fix process inefficiencies, which can lead to successful implementation of lean projects. For instance, when employees can suggest improvements using tools like Kaizen, organizations can become more efficient and reduce waste.
Setting SMART(Specific, Measurable, Achievable, Relevant, Time-Bound) goals for lean projects also enhances employee empowerment. It gives employees clear objectives to work towards, promoting accountability and engagement. This approach allows employees to take ownership of their work and align with the business strategy, leading to continuous improvement and success.
Establishing SMART Goals for Lean Projects
When creating SMART goals for lean projects, it’s important to consider specific criteria. The goals should be:
- Specific
- Measurable
- Achievable
- Relevant
- Time-bound
For instance, a manufacturing company aiming to reduce lead times could set a SMART goal of reducing lead times in the machining process by 15% within six months. This example meets all the SMART criteria.
Using the SMART goal framework can help ensure the success of lean projects. It provides clarity and focus on what needs to be achieved, as well as clear metrics for measuring progress. Additionally, it allows for better alignment of goals with the organization’s overall objectives, promoting efficiency and effectiveness.
However, there are potential challenges when establishing SMART goals for lean projects. These include setting overly ambitious targets, lack of clear metrics for measurement, and failure to involve relevant stakeholders in the goal-setting process.
To address these challenges, thorough data analysis, involving cross-functional teams in goal-setting exercises, and ensuring that the goals are realistic and aligned with the organization’s strategic priorities can be beneficial.
Why Invest in Lean Training and Certification?
Investing in lean training and certification has many benefits for an organization. It helps employees gain skills and knowledge, improving efficiency, reducing waste, and encouraging continuous improvement. This can lead to lower production costs, better quality control, and smoother processes. It also boosts employee morale and engagement, making staff feel more connected to the company’s success.
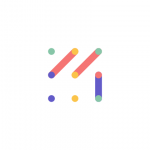
Vizologi is a revolutionary AI-generated business strategy tool that offers its users access to advanced features to create and refine start-up ideas quickly.
It generates limitless business ideas, gains insights on markets and competitors, and automates business plan creation.