Organize Better: 5S Bin Location Tricks
Keeping your workspace organized and efficient is important. 5S bin location tricks can help you with this. These strategies are simple but effective. They can streamline your workflow and make it easier to find and access items. Whether you’re in a warehouse, office, or any other work environment, these tricks can save you time and reduce frustration. We’ll explore five practical tips for optimizing your bin locations and improving your organization system in this article.
Explanation of the 5S Acronym
The 5S acronym stands for five key principles in workplace organization: Sort, Set in Order, Shine, Standardize, and Sustain. These principles can be applied in warehouse management to create an efficient and well-organized work environment.
For example, by sorting through materials and tools, warehouse staff can eliminate unnecessary items, reducing clutter and improving workflow. Additionally, organizing and identifying necessary materials for easy access can streamline processes and reduce time spent searching for items, increasing overall productivity.
Seiri: Sorting for Success
Elimination of Non-Essential Items
Evaluate the materials and tools in the workspace. Consider if they are necessary and relevant to the tasks at hand.
If you’re unsure if an item is non-essential, think about how often it’s used and if it helps with productivity. Also, check if it has a designated place in the work area.
Involving employees in identifying and removing non-essential items can significantly improve workplace efficiency.
Employees can help by sharing their insights on items that are rarely used, take up space, or cause clutter.
Eliminating non-essential items in the workspace can lead to enhanced organization, improved safety, and increased productivity.
With fewer unnecessary items, employees can better focus on essential tasks, find needed items quickly, and navigate their workspace easily.
This contributes to a more efficient and streamlined workflow, benefiting both the employees and the organization as a whole.
Seiton: Setting in Order
Effective Labeling Techniques
Effective labeling techniques are important for the “Seiton: Setting in Order” principle of the 5S methodology. Color-coding is one such technique, using different colors to distinguish items or locations. Visible signage with large, easy-to-read labels guides staff to the correct bin locations. Clear and descriptive labels for storage bins, shelves, and containers help in easily identifying and locating items, contributing to efficient workplace organization.
Proper labeling significantly contributes to process standardization in line with the “Seiketsu: Standardizing Processes” principle of 5S. Maintaining a consistent labeling system throughout the warehouse leads to improved efficiency and reduced errors, as employees can quickly and accurately locate items they need for their tasks.
Effective labeling is important for sustaining the practice of 5S, especially in warehouse management. Clear and standardized labeling ensures that gains made during the initial 5S event are maintained. This enables employees to adhere to established organizational processes, perpetuating a culture of cleanliness, order, and waste reduction in the workplace.
Seiso: Shining and Cleaning
Routine Cleaning Schedules
Routine cleaning schedules for 5S bin locations should cover work surfaces, tools, equipment, and storage areas in the warehouse. A daily cleaning schedule ensures a clean, organized, and safe work environment, promoting efficiency. It forms a habit of cleanliness and orderliness, aligning with the sustain pillar of 5S.
Additionally, deep cleaning tasks should be done weekly and monthly for a thorough workspace cleaning. Using a checklist helps track and maintain the cleaning schedule, ensuring no area or task is overlooked. Standardizing the process with clear guidelines and procedures helps maintain cleanliness and organization consistently, boosting productivity and morale.
Seiketsu: Standardizing Processes
Establishing Warehousing Standards
Establishing warehousing standards using the 5S methodology has many benefits. It helps improve efficiency, reduce costs, maintain consistency, and enhance safety.
By using effective labeling and regular cleaning, warehouses can stay organized and standardized. This makes operations smoother, reduces errors, and makes it easier to navigate through the facility.
When implementing 5S in warehouses, it’s important to prioritize optimizing layout and creating efficient storage solutions. Also, thorough training programs for employees are essential to ensure consistent adherence to the 5S methodology, leading to sustained cleanliness, order, and waste reduction efforts.
Establishing Guidelines for Employees
Specific guidelines should be established for employees to support the 5S principles in the workplace. These guidelines can include:
- Clearly marking bin locations for materials and tools.
- Implementing color-coded bin systems to differentiate between necessary and unnecessary items.
- Conducting regular audits to ensure compliance with the established standards.
Employees can be effectively trained and educated on the guidelines for maintaining the 5S standards in their work environment through:
- Hands-on training sessions.
- Visual aids such as posters and instructional videos.
- Regular communication and feedback from management.
Mechanisms that can be put in place to ensure employees consistently adhere to the established guidelines for 5S principles include:
- Assigning designated employees to oversee the implementation and maintenance of 5S practices.
- Implementing reward and recognition programs to incentivize compliance.
- Conducting regular assessments and inspections to monitor adherence to the established guidelines.
Shitsuke: Sustaining the Practice
Ongoing Commitment to 5S Principles
To keep following the 5S principles, the organization will:
- Have regular training sessions and workshops for employees.
- Continually highlight the importance and benefits of 5S in the workplace.
- Set clear expectations and guidelines for maintaining organized and clean work areas.
- Create designated 5S bin locations for easy tool and material access.
The organization will also:
- Integrate 5S principles into daily routines and processes.
- Encourage employees to make 5S a habit, not just a one-time event.
Safety is important to maintain the commitment to 5S principles by:
- Enhancing overall safety in the workplace.
- Reducing the risk of accidents.
- Improving visibility and access to emergency equipment.
- Minimizing potential hazards.
Ongoing safety training and adherence to safety protocols are essential for upholding the 5S principles in the workplace.
The Role of Safety in 5S
Safety is an important part of the 5S methodology in warehouse management. Integrating safety into 5S practices can improve workplace efficiency and quality. Prioritizing safety within the 5S framework has many benefits. It can enhance employee morale, reduce equipment downtime, and improve overall safety measures. For instance, organizing and clearly marking bin locations not only helps in finding items easily, but also prevents accidents and injuries.
Implementing safety measures within the 5S framework can create a workplace environment that is both efficient and safe, leading to higher productivity and employee satisfaction.
Impacts of 5S on Warehouse Management
Benefits of Decreased Waste and Costs
Reducing waste and costs in warehouse operations has many benefits. Implementing the “Sort” process of 5S helps eliminate unnecessary items, reducing excess inventory and storage costs. The “Set in Order” and “Standardize” pillars of 5S improve organization, streamline processes, and cut unnecessary movement and transportation, all reducing costs and waste. A cleaner, organized work environment boosts employee morale, leading to higher productivity and quality standards.
Implementing the 5S methodology not only cuts costs and waste but also creates a more efficient and quality-focused work culture.
Improvements in Efficiency and Quality
Implementing the 5S principles in warehouse management has brought significant improvements in efficiency and quality. By sorting through materials, organizing workspaces, and establishing daily cleaning processes, warehouse operations become more streamlined. This results in better time usage and reduced waste, contributing to enhanced efficiency and work quality. Decreased waste and costs are some of the benefits achieved through the application of the 5S method in warehouse settings.
With a clean and organized workspace, there is less equipment downtime, improved safety, and heightened employee morale. All of these contribute to better quality and reduced operational costs.
Additionally, the 5S model can optimize warehouse layout and improve workplace productivity. This is done by standardizing the organization of necessary materials and tools for ease of use and access, further enhancing efficiency and quality in the warehouse environment. This illustrates how the 5S method is a valuable tool for improving warehouse operations.
Positive Effects on Workplace Morale
Implementing the 5S method in the workplace helps create a clean, organized, and efficient work environment. This can boost employee satisfaction and motivation. By reducing clutter, distractions, and safety hazards, it leads to improved safety, reduced equipment downtime, and enhanced efficiency.
The 5S system also promotes teamwork and collaboration by standardizing processes and establishing daily routines. This fosters a sense of unity and shared responsibility among team members, ultimately enhancing workplace morale.
Implementation of 5S in Warehouses
How to Apply the 5S Method to Bin Locations
The 5S Method is used for organizing bin locations in a warehouse.
First, sort through items to separate necessary and unnecessary ones. Remove unnecessary items, then organize and identify the remaining materials for easy access. Cleaning the area is important too, following the “Shine” pillar of 5S. Standardizing the process and establishing a daily routine for maintaining organized bin locations is crucial for sustaining productivity and safety gains. Strategies for optimizing the layout of bin locations include clear labeling, color-coded systems, and ensuring easy access to frequently used items. Training programs can include hands-on workshops, visual management tools, and regular refresher courses for warehouse employees to apply the 5S Method effectively.
Optimizing the Warehouse Layout
When optimizing the warehouse layout for maximum efficiency and productivity, it’s important to consider factors such as the flow of materials, accessibility to items, and space utilization.
Implementing the principles of 5S into the warehouse layout can streamline processes and minimize waste. This involves ensuring that necessary items are easily accessible, removing unnecessary items, and keeping the workspace clean and organized.
An optimized warehouse layout has a significant impact on overall warehouse management and operations. It contributes to enhanced efficiency, reduced costs, improved safety, and heightened employee morale. Additionally, it allows for better time usage, consistency and quality, and less equipment downtime, ultimately leading to a more productive and well-managed warehouse environment.
5S Training Strategies
Workplace Productivity and 5S Training Programs
Implementing the 5S method can improve workplace productivity and efficiency. This method streamlines processes, eliminates waste, and creates a well-organized work environment.
For example, by applying the “Sort” and “Set in Order” principles, employees can easily locate tools and materials, reducing time spent searching and increasing overall productivity.
Effective training strategies for implementing the 5S methodology in warehouse settings include hands-on workshops, visual aids, and continuous reinforcement. For instance, hands-on workshops help employees understand the practical applications of the 5S principles in their daily work. Visual aids, like posters and signage, serve as constant reminders of the 5S practices.
The key components of a successful 5S training program for employees involve thorough education on the 5S principles, regular practice and reinforcement, and clear communication of the expected standards. For instance, incorporating daily routines to complete the “Standardize” and “Sustain” pillars can help employees establish a habit of maintaining cleanliness and organization, leading to sustained improvement in workplace productivity.
Applying the 5S Model in Warehouse Settings
Effective labeling in warehouses helps organize tools, materials, and bin locations. This makes it easier for employees to find items, reducing search times and confusion. When setting warehouse standards in the 5S Model, it’s important to create consistent labeling systems, uniform storage methods, and clear operational guidelines.
To optimize warehouse layout, design easy-to-navigate pathways, arrange storage based on usage frequency, and use visual management tools like floor markings and color-coded bins. These strategies improve workflow, minimize unnecessary movement, and enhance overall efficiency.
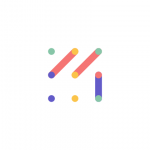
Vizologi is a revolutionary AI-generated business strategy tool that offers its users access to advanced features to create and refine start-up ideas quickly.
It generates limitless business ideas, gains insights on markets and competitors, and automates business plan creation.