Ways to Get Lean in Your Work
Want to improve your work routine? You can do this by adding movement breaks and organizing your workspace. These changes can help you work more efficiently and reduce stress.
Whether you want to be more productive, lessen stress, or develop healthier habits, these strategies can assist you in achieving a better work-life balance.
Keep reading for practical tips on improving your work routine.
What Are the 7 Ways in Lean?
Identify Value
Value can be identified and prioritized within a process or system by using strategies such as the 7 Ways Idea Generation Form for brainstorming and problem-solving. This tool encourages people to stretch their creativity and generate innovative solutions to a problem.
Additionally, activity diagrams, benchmarking, infographics, rapid prototyping, and surveys can be used to assess and measure the value of a specific process or product.
These techniques allow businesses to identify areas of waste and inefficiency in their processes, leading to improved quality, reliability, and customer satisfaction.
Furthermore, value stream mapping is a useful method to visualize and analyze the steps required to deliver a product or service, enabling businesses to identify non-value-added activities and create a more efficient workflow.
By utilizing these methods and tools, organizations can gain a better understanding of their processes and products, ultimately leading to increased value and customer satisfaction.
Map the Value Stream
Mapping the value stream in a lean process involves documenting the current state of the process. It also includes identifying waste and designing a future state that eliminates that waste.
This process helps understand the sequence of steps in a process and identify value-added and non-value added activities.
Mapping the value stream also helps establish an understanding of demand, production capacity, and inventory levels, which contribute to creating flow and establishing pull in the lean process.
By clearly mapping out the process, the team can identify areas for improvement to reduce cycle times and unnecessary movement of materials or information.
Additionally, mapping the value stream ensures that value is being delivered to the customer and requirements are met at the lowest possible cost.
The benefits of mapping the value stream in a lean transformation are numerous. In addition to process improvement and waste reduction, it helps promote a culture of continuous improvement, increases customer satisfaction, and empowers teams to make data-driven decisions.
Create Flow
Creating flow in an organization’s processes is important for improving efficiency and reducing waste. One effective way to do this is by using the 7 Ways Idea Generation Form, a brainstorming tool that encourages creativity. This tool is often used in 3P events and problem-solving activities to inspire innovative solutions.
By using this form to push people beyond their comfort zones, an organization can generate unique ideas that can lead to smoother work flow in a lean environment. In a lean organizational structure, a common challenge is people quickly coming up with a few ideas but struggling to generate more. To address this, an organization can ask for more ideas, leading to the emergence of valuable solutions.
The key idea here is that pushing people beyond their comfort zones can bring significant benefits in creating flow within a lean organizational structure.
Establish Pull
Pull is an important concept in lean manufacturing. It can be achieved in various ways. One method is using a just-in-time (JIT) system, which reduces excess inventory by producing products only as needed. Another way is through kanban systems, which use visual cues to signal the need for more materials, ensuring a smooth flow of work. Focusing on customer demand as the primary driver for production is also key in establishing pull.
To integrate pull into the value stream, companies can use tools like value stream mapping to identify waste and optimize material and information flow. Creating flexible work cells and cross-training employees helps companies adapt quickly to changes in customer demand.
Establishing pull is important for pursuing perfection in lean principles. It helps reduce lead times, improve quality, and increase efficiency. Pull-based systems also drive continuous improvement and innovation, enabling companies to adapt quickly to market changes and stay competitive.
Pursue Perfection
The Idea Generation Form is one of the 7 Ways in lean. It’s a brainstorming tool that encourages creativity and innovative problem-solving. This form pushes people to come up with unique ideas. It’s particularly useful in 3P events and other problem-solving activities.
The basic premise is to encourage people to stretch their creativity, resulting in a wider array of ideas and potential solutions. This increases the likelihood of finding truly innovative approaches to solve the problem at hand.
Furthermore, the lack of leadership support and the difficulty in sustaining Lean practices can be addressed through these methods. Creativity and innovation play a key role in overcoming these obstacles. By promoting a culture of creativity and providing tools like the 7 Ways Idea Generation Form, organizations can achieve a sustainable Lean environment and overcome these challenges.
Seek Continuous Improvement
Lean thinking is all about continuous improvement. The 7 Ways Idea Generation Form is a helpful tool for brainstorming. It encourages thinking outside the box to find creative solutions. This technique can push people out of their comfort zones, leading to unique and innovative ideas. It’s especially useful in 3P events and problem-solving activities, helping teams consider new ideas. This method is important in the lean approach, where challenges in embracing continuous improvement can happen.
Using tools like the 7 Ways Idea Generation Form, organizations can promote a culture of change and creative problem-solving.
Empower the Team
One way to empower the team in lean is by using the 7 Ways Idea Generation Form. This tool encourages creativity and helps generate innovative solutions. It’s often used in problem-solving activities and 3P events to push individuals beyond their comfort zones and inspire exceptional ideas.
For example, most people can quickly come up with a few ideas to solve a problem. However, the 7 Ways Idea Generation Form challenges them to think even further and come up with truly unique solutions. This technique helps overcome cultural barriers by fostering a culture of creativity and continuous improvement, which is important for sustaining lean efforts in the long term.
By using this form, teams can enhance their problem-solving capabilities and drive innovation, ultimately contributing to the success of lean initiatives.
Strategies to Implement Lean Principles
Develop a Lean Mindset
To develop a Lean mindset, individuals can start by identifying value and creating pull. This means focusing on delivering value to customers, minimizing waste, and continuously improving processes.
Techniques like value stream mapping, just-in-time production, and pull systems can help streamline operations and reduce inefficiencies. Implementing Lean principles involves setting clear objectives, involving employees in decision-making, and aligning business goals with Lean methodologies.
Organizations can support Lean by encouraging employee involvement through regular meetings, training sessions, and feedback opportunities. Continuous training is vital for maintaining a Lean culture and helping employees stay updated with the latest improvement tools.
By creating a supportive environment and investing in employee development, organizations can effectively promote Lean principles and drive sustainable improvements in their operations.
Adopt Lean Tools and Techniques
One of the 7 ways in lean manufacturing is overcoming cultural barriers. This involves pushing people beyond their comfort zones to encourage innovative thinking.
The 7 Ways Idea Generation Form is a brainstorming tool that is used to stretch people’s creativity and encourage them to come up with exceptionally unique ideas.
By asking individuals to come up with more ideas, even after they have already proposed a few, the form helps to challenge them and break cultural barriers that may be limiting their creativity.
This technique is used to generate new and breakthrough ideas in the continuous improvement process.
Another way to maintain momentum for continuous improvement is by using various techniques for product development and improvement, such as:
- Design review.
- Rapid prototyping.
- Storytelling.
These techniques can be used at different stages of the product development process to enhance quality, reliability, and customer satisfaction, maintaining the impetus for continuous improvement.
Align Lean Goals with Business Objectives
To align key business objectives in lean, organizations should focus on quality improvement, waste reduction, cost reduction, and process efficiency.
To integrate lean principles into the overall business strategy, organizations can take steps like having top executives actively support and participate in lean initiatives, provide adequate resources for lean training and implementation, and promote a culture of continuous improvement and problem-solving at all levels.
Measures that can be put in place to track the alignment of lean goals with business objectives include:
- Setting clear and measurable goals for lean initiatives.
- Regularly monitoring and evaluating progress using key performance indicators.
- Obtaining feedback from employees and stakeholders on the impact of lean efforts on business objectives.
- Conducting regular gemba walks and value stream mapping to identify opportunities for improvement.
Comparison of Lean Against Traditional Work Methods
Differences in Process Management
Lean process management is quite different from traditional work methods. In Lean, the focus is on identifying and eliminating waste, constantly improving processes, and prioritizing customer value. Unlike traditional work methods, which can be wasteful and inefficient, Lean aims to streamline and optimize processes. This approach often leads to greater efficiency and productivity in Lean environments.
The impact of Lean on workplace culture also differs greatly from traditional work methods. Lean promotes a culture of continuous improvement and respect for people, creating an environment where employees are empowered to identify and solve problems. This is in contrast to the more rigid and hierarchical culture often found in traditional work methods.
These differences make Lean a highly effective process management approach for organizations seeking to improve quality, reliability, and customer satisfaction.
Outcomes in Efficiency and Productivity
Implementing Lean principles can lead to more efficiency and productivity. It helps reduce waste, improve quality, shorten lead times, increase throughput, streamline processes, and enhance workplace safety. These improvements make the workforce more engaged and motivated, creating a positive impact on workplace culture.
The success of Lean transformations can be measured through key performance indicators like overall equipment effectiveness, cycle time, inventory turnover, and customer satisfaction. When comparing Lean to traditional work methods, the impact on workplace culture can be measured by employee satisfaction, turnover rates, and engagement levels. These measurements provide valuable insights into the effectiveness of Lean principles in transforming an organization’s productivity and efficiency.
Impact on Workplace Culture
Implementing Lean principles in the workplace can have a big impact on workplace culture. It encourages employees to think of new and innovative solutions to problems, creating a more creative and proactive work environment.
It also promotes increased collaboration and communication among employees, emphasizing the importance of teamwork and open communication to streamline processes and eliminate waste. This can improve employee engagement, as they feel empowered to take ownership of their work and contribute to the organization’s success.
However, there are challenges when integrating Lean methods into workplace culture. Resistance to change, lack of leadership support, and insufficient training are common pitfalls. It’s important for organizations to address these issues to successfully transform their workplace culture.
Practical Applications of Lean in Renowned Companies
Toyota’s Lean Manufacturing System
The 7 Ways Idea Generation Form is a brainstorming tool. It encourages creativity and is used in problem-solving activities like 3P events. It helps generate innovative solutions. The form’s basic premise is to push people out of their comfort zones, resulting in unique ideas.
It sets rules to stimulate unfamiliar ideas and guides participants through sorting the concepts. This technique is just one of many tools listed on the blog for the product development process.
Techniques like interviews, surveys, and rapid prototyping can enhance product quality and customer satisfaction. Therefore, the 7 Ways Idea Generation Form is an important part of Toyota’s Lean Manufacturing System. It helps improve their products and processes through creativity.
General Electric’s Adaptation of Six Sigma
One of the 7 ways in lean is “Lack of Leadership Support.” Many organizations struggle with this when trying to implement lean practices. If leadership doesn’t fully back lean initiatives, it’s hard to make changes across the organization. Employees may not see the value in lean principles and resist change. To overcome this, companies should ensure leaders actively support lean methods.
Leading by example, providing resources, and explaining the benefits of lean to the whole organization are important to get leadership on board. Showing the positive impact of lean practices through results can also help gain leadership support and maintain lean initiatives long-term. Without this support, implementing lean practices can affect the organization’s efficiency and productivity.
Ways to Foster a Supportive Environment for Lean
Foster Open Communication
Open communication is important for Lean implementation. Organizations can promote open communication by encouraging brainstorming sessions. These sessions, like the 7 Ways Idea Generation Form, help in innovative thinking and problem-solving. They create an environment where employees feel comfortable sharing their ideas. Implementing techniques like affinity diagrams can further encourage open communication by sorting and organizing ideas.
Actively involving employees in decision-making increases the success of Lean principles. Open communication also maintains a supportive environment for Lean implementation by ensuring everyone has a voice in the continuous improvement process. This taps into diverse perspectives and knowledge, leading to more effective problem-solving and greater buy-in from employees.
Encourage Employee Involvement
To encourage employee involvement, organizations can use the 7 Ways Idea Generation Form. It’s a brainstorming tool often used in 3P events and problem-solving activities to promote creativity.
Leaders should push employees beyond their comfort zones when using this form. This helps elicit unique and innovative ideas.
The tool helps overcome cultural barriers and manage employee buy-in by allowing diverse perspectives and ideas to surface. This promotes a collaborative and inclusive work environment.
Provide Continuous Training
Continuous training in Lean principles offers many benefits. It helps employees stay updated with the latest industry trends, best practices, and tools. This enhances their problem-solving skills and encourages innovative thinking.
The training also promotes a culture of continuous improvement. Employees are always looking to optimize processes and eliminate waste.
Additionally, continuous training ensures that everyone is aligned with the Lean philosophy. This creates a common language and understanding within the organization.
Effective methods for providing continuous training in Lean principles include:
- Workshops
- Gemba walks
- Kaizen events
- 3P events
- Regular coaching and mentoring
These methods enable hands-on learning and practical application of Lean tools and techniques. They reinforce the concepts and create lasting behavioral change.
Measuring Success in Lean Transformations
Key Performance Indicators in Lean
Performance metrics in Lean cover a wide range of areas. They are used to measure success in Lean transformations. Some common performance indicators in Lean include:
- Customer satisfaction
- Defect rates
- Cycle time
- Process efficiency
- Inventory levels
- Employee engagement
These indicators help organizations track and assess their progress in implementing Lean principles. By analyzing these metrics, organizations can identify areas for improvement and optimization. For example, by monitoring defect rates, organizations can find opportunities to reduce waste and improve product quality. Similarly, tracking inventory levels can help identify opportunities to streamline processes and reduce lead times.
Realizing Return on Investment
Realizing return on investment in lean transformations requires tracking key performance indicators. These include productivity, cycle time, and customer satisfaction.
Setting measurable goals and regularly assessing progress helps companies measure the impact of lean principles on their bottom line.
However, it’s important to recognize the challenges and pitfalls associated with this process. Overly focusing on financial metrics can undervalue the long-term benefits of lean transformations, like improved employee morale and organizational culture.
The intangible nature of these qualitative changes can make it difficult to capture their full impact. Therefore, it’s crucial for companies to take a holistic approach and consider both quantitative and qualitative aspects when evaluating the return on their lean investment.
Addressing these challenges ensures that companies accurately realize the return on investment from their lean transformations.
Challenges and Pitfalls in Adopting Lean Methods
Resistance to Change
Resistance to change is a common challenge when organizations implement Lean principles. People may resist change due to fear of the unknown, concern about job security, and a desire to stick to familiar processes. Change can also be disruptive and require extra effort to adapt to new ways of working. To overcome this resistance, organizations can use transparent communication to explain the benefits of Lean methods and involve employees in the change process.
Providing training, support, and recognition for those embracing the changes can also help. Creating a culture that encourages innovation, teamwork, and continuous improvement can make the transition smoother. By addressing these common reasons for resistance, organizations can increase the chances of successful Lean implementation.
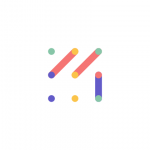
Vizologi is a revolutionary AI-generated business strategy tool that offers its users access to advanced features to create and refine start-up ideas quickly.
It generates limitless business ideas, gains insights on markets and competitors, and automates business plan creation.