What Is Inventory Management and How to Achieve It
Inventory management refers to the process of ordering, storing, tracking, and controlling a company’s inventory of products, materials, or goods for sale. Effective inventory management is crucial for businesses to maximize profits, cut costs, and ensure high customer service levels.
This comprehensive guide will explain what inventory management entails, why it’s vital for small and medium businesses, and provide actionable strategies for successfully implementing asset inventory control practices.
What is Inventory Management?
Inventory management is the supervision of non-capitalized assets, or inventory, and stock items. A component of supply chain management, inventory and asset management supervises the flow of goods from manufacturers to warehouses and from these facilities to point of sale.
The goals of inventory management are to:
- Track inventory levels in real-time
- Maintain optimal inventory sizes
- Protect inventory investments
- Control inventory-related costs
- Ensure high customer service levels
Proper asset inventory management balances the cost of holding inventory with the company’s need to make products readily available to customers by utilizing inventory software development services.
Companies apply both asset and inventory management systems and processes to manage three inventory types:
- Raw materials – The basic materials from which finished goods are made.
- Work-in-progress – Goods currently being made that are not yet finished.
- Finished goods – Products ready for sale to customers.
Key Players in Effective Inventory Management
Inventory control is the coordination of several departments and corporate responsibilities:
- Purchasing or procurement: It gets necessary asset management inventory from vendors under fair terms and pricing.
- Warehousing/Logistics: They stock and manage inventory in warehouses and distribution centers.
- Operations: It is used for manufacturing and production purposes of inventory.
- Sales and marketing: It helps in sales process and customer demand drives.
- Finance: It tracks the costs associated with inventory investments.
- IT: Develops and maintains asset inventory management systems and databases.
These groups are interested in maintaining the inventory levels and accuracy at optimum levels, and also at reducing carrying cost.
Why is Inventory Management Important?
Maintaining control and visibility of inventory is vital for small and medium businesses for several reasons:
1. Avoid Stockouts and Shortages
When demand for a product exceeds what’s available in inventory, that’s a stockout. For customers who rely on product availability, they may take their business elsewhere.
Careful asset inventory tracking and planning prevent such losses in revenue and reputation damage. Parameters such as safety stock levels, effective demand forecast, and reduced lead time mitigate the risk of shortages.
2. Cut Excess and Obsolete Inventory
Carrying too much inventory strains a company’s finances due to storage, tracking and related costs. Excess items also run the risk of damage, spoilage and obsolescence – where inventory becomes outdated.
Keeping inventory levels lean ensures capital is not caught up unnecessarily. Setting stock to reorder points and monitoring product shelf life helps avoid overstocking.
3. Optimize Warehouse Space
The capacity to store inventory for warehouses and stores is finite. Balancing inventory sizes with the number of storage rooms available is what managing this space judiciously requires.
Layout optimization, efficient use of storage equipment and categorization of products by velocity and volume increase facility capacity.
4. Maintain Accuracy
Inventory records in the asset inventory system must match the physical stocks on hand. Errors in reorder points, sales processing and poor customer service are the result of inaccuracies.
Cycle counting policies and stocktakes mean discrepancies are found and fixed quickly. Investing in integrated technology like asset tracking and inventory management systems eliminates duplication and mistakes.
5. Reduce Operational Costs
Companies can reduce annual operating costs by up to 25% through inventory management vs asset management optimizations. Carrying and storing inventory is expensive – optimizing safety stocks and preventing wastage and pilferage is key.
Process improvements and technology investments also help organizations control inventory expenses.
Core Inventory Management Processes
Maintaining asset management and inventory control requires coordinating a sequence of integrated supply chain processes:
Inventory Planning
The inventory planning concerns the alignment of projected inventory needs with budget, storage capacity and demand forecasts. Key activities include:
- Demand forecasting: Estimate expected demand for each product using historical sales, market trends, promotions calendar, economic indicators etc.
- Set target service levels: You would use this to decide on target inventory sizes that balance customer service levels that you want with the budget available.
Procurement
The procurement process involves purchasing or producing the inventory required to meet planned levels:
- Source vendors: Find reliable suppliers that will meet business needs such as product quality and lead times.
- Create purchase orders: Vendors are release ordered with item SKUs quantities needed to arrive on set timelines.
Warehousing
Efficient warehousing activities ensure inventory is accurately received, stored, preserved and dispatched:
- Receive & inspect: Confirm incoming order quantities, verify product condition, quality standards documentation and proper labeling.
- Manage warehouse space: Optimize layouts, contain inventory to active locations, and efficiently use vertical space to maximize capacity.
Inventory Tracking
Recording inventory transactions and movements provides updated data to optimize ongoing decisions:
- Maintain inventory records: Inventory management system for log purchase receipts, inventory adjustments, order issues and product dispatches.
- Perform cycle counting: Maintain inventory accuracy by conducting regular spot checks on quantities on hand for a sample of items.
Inventory Management Strategies and Best Practices
It involves bringing together people, processes and technology in implementing comprehensive asset and inventory management. Keep these proven strategies in mind:
Integrate Inventory Operations
Help break down the business silos between procurement, production, warehouse and sales departments. Coordinated planning and integrated inventory management is leveraged through system wide data. Also, cross functional KPIs align the teams to optimize overall working capital and service levels.
Categorize Inventory
ABC analysis provides an annual consumption value based segmentation of stock keeping units (SKUs). “A” items contribute to 70-80% of inventory value while comprising only ~20% of total SKUs. Assigning tailored management policies per ABC class improves control.
Employ Unique Item Identification
Using identification technologies like barcodes, RFID, and serial numbers, unique SKUs can be identified for each item batch combination. It avoids errors, makes it easier to track through distribution chains, and helps maintain inventory records accurately.
Set Optimal Reorder Points
Determining when to replenish items is crucial to maintaining availability while minimizing excess stocks. While fixed reorder systems are simpler, dynamic parameterized reorder points based on demand variability, lead times, and stockout risks prove more cost-effective.
Invest In WMS Technology
A warehouse management system centralizes inventory tracking across facilities and business functions, all on the same platform. Cycle counting and stocktake efficiency is improved with the help of automation, and analytics-driven insights help optimize planning.
Inventory Management System Software
Technology plays a pivotal role in driving inventory management excellence with small and medium businesses:
Features
- Centralized inventory database visible across departments
- Dashboard displaying KPIs and analytics
- Mobile app allowing remote, real-time inventory tracking
- Barcode and serial number support for tracking unique items
- Bill of materials formatting for manufactured items
- Expiry management for monitoring shelf life
- Multiple warehouse management with inter-facility transfers
- Purchase order generation and vendor collaboration
- Sales order and invoice management
- Reorder point definition and inventory replenishment alerts
- Cycle counting templates for physical stock verification
Benefits
Inventory management systems lead to substantial operational efficiencies, including:
Improved demand planning:
- Statistical forecasting methods leveraging historical sales data
- Promotional event modeling capabilities
- Capability to define multiple demand plans with reordering impact
Greater inventory visibility:
- Real-time tracking of inventory transactions, orders and movements
- Unified view of stock levels across facilities
- Identification of excess, obsolete and slow-moving items
Faster cycle counts:
- System-directed counting based on item velocity
- Mobile devices for bedside cycle counting
- Automated variance analysis to fix discrepancies
Space optimization:
- Slotting analysis to optimize warehouse layout and storage plans
- Modeling expected capacity constraints
- Dynamic allocation policies based on inventory profiles
Lower stockouts:
- Parameter-based reorder point calculation
- Inventory replenishment alerts
- Monitoring of projected available inventory
Shipment accuracy:
- Direct picking and dispatching based on orders
- Barcode scanning and serialization to avoid errors
- Packaging rule definition
Reporting and analytics:
- Real-time inventory valuation tracking
- Identification of fast/slow-moving items
- Historical performance reporting
Key Takeaways
So, what is asset inventory and why you need it? Effective inventory asset management is vital for small and medium businesses targeting working capital optimization, operating cost reduction and profit maximization.
Creating an integrated inventory strategy requires detailed demand planning, intelligent warehouse and procurement management and continuous tracking for optimization.
Inventory is a large investment for companies, so accuracy checks, proper storage, and lean stocking levels are required in order to protect its value.
A feature-rich inventory management system brings data together and automates processes for efficiency. It generated analytics to spot improvement areas to align inventory plans with financial targets.
Through these concerted efforts, businesses are able to improve customer service levels while controlling inventory-related costs significantly.
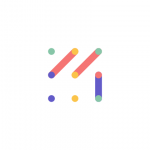
Vizologi is a revolutionary AI-generated business strategy tool that offers its users access to advanced features to create and refine start-up ideas quickly.
It generates limitless business ideas, gains insights on markets and competitors, and automates business plan creation.